LE SOL INDUSTRIEL DOIT REPONDRE A DE NOMBREUSES EXIGENCES
Un sol industriel doit répondre aux strictes exigences de l'environnement industriel. Il faut effectuer une bonne analyse de ce qui est nécessaire. Heureusement, il y a divers types de sol, adaptés à chaque souhait et à chaque besoin.
APPLICATION
Presque tous les environnements industriels ont intérêt à avoir un bon sol. Cela fait donc une multitude d'applications, chacune s'accompagnant d'exigences spécifiques.
Construction de machines
Les constructeurs de machine ont besoin d'un sol qui résiste à une charge mécanique et à l'usure. En effet, il accueillera de lourdes machines, certaines ayant des composants vibrants ou mobiles.
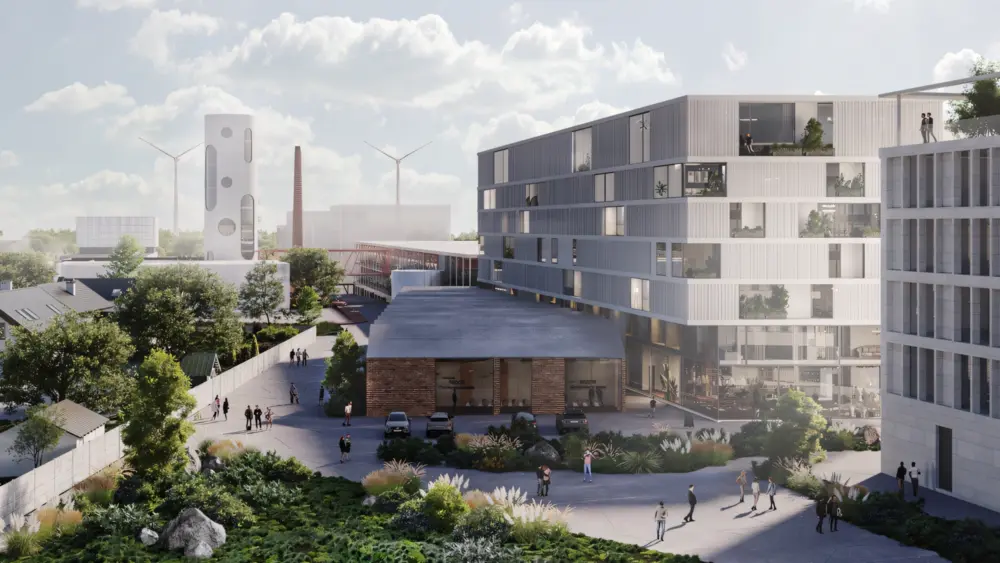
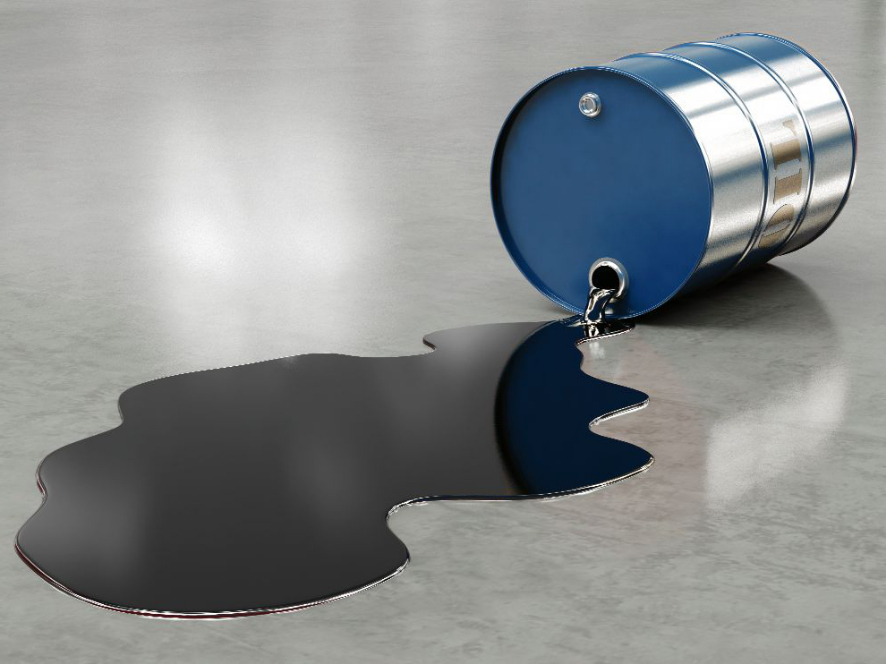
Industrie électronique
Dans cet environnement, la principale exigence pour le sol est la suivante: il faut qu'il empêche l'électricité statique. Il doit donc être conducteur dans un certain sens tout en offrant une sécurité en matière de décharge électrostatique.
Industrie chimique
Un sol dans l'industrie chimique ne doit pas être affecté par les produits chimiques avec lesquels il entre en contact. De plus, il est important que ce sol soit hermétique aux liquides.
Le sol adéquat
Pour chaque application, il convient d'effectuer une analyse pour déterminer le sol adéquat.
SUPPORTS
Béton
Le béton lié au ciment sert de base pour un sol industriel. Souvent, on pose dessus un sol de finition en fonction des exigences, mais ce n'est pas toujours nécessaire. Dans ce cas, on parle d'un sol en béton avec une finition monolithe.
Chape en ciment
Ce sol est à base de ciment. Il permet de répondre à des exigences liées à la construction comme la planéité ou l'application d'une inclinaison compliquée.
Sol blindé
Ce sol comprend généralement un sol en ciment gris avec des additifs comme du corindon ou du carbure de silicium. L'épaisse couche inférieure (25 mm) se compose généralement de gravier et de sable, et est recouverte d’une couche blindée de 4 à 15 mm.
Sol anhydrite
Ce sol blanc doit sa couleur à son liant: le sulfate de calcium, mieux connu sous le nom de plâtre. Sa particularité est que le plâtre ainsi formé se dissout dans l'eau. C'est pourquoi les sols anhydrites qui sont en contact avec la terre, sont toujours traités avec des revêtements laissant passer la vapeur.
Sol en pierre/bois
Ce sol se distingue par sa surface blanc crème à la structure lisse. Il est utilisé dans la construction résidentielle, mais aussi dans la construction industrielle. Il est lié avec du chlorure de magnésium ou de l’hydroxyde, qui assurent la cohésion des matières de charge telles que gravier fin, farine de bois et copeaux de bois. En fonction de la quantité de charge, le taux d'humidité résiduelle peut être de 12%. Par conséquent, les revêtements appliqués doivent être très perméables à la vapeur.
Chape à base de magnésium
Ce sol se compose d'un mélange d'oxyde de magnésium, d'une solution aqueuse de chlorure de magnésium et d'additifs comme de la sciure de bois. A cause de ça, entre autres, le revêtement appliqué doit présenter une forte perméabilité à la vapeur.
Asphalte coulé
Un sol en asphalte coulé est souvent utilisé comme matériau de support pour ses propriétés hydrofuges. Ce sol se compose de poudre de roche, de sable, de pierraille et de gravier liés avec du bitume (d'où la couleur noire). Directement après le refroidissement, on peut appliquer un revêtement polyuréthane sur l'asphalte coulé saupoudré de sable de quartz, ce qui offre un avantage au niveau du temps de traitement.
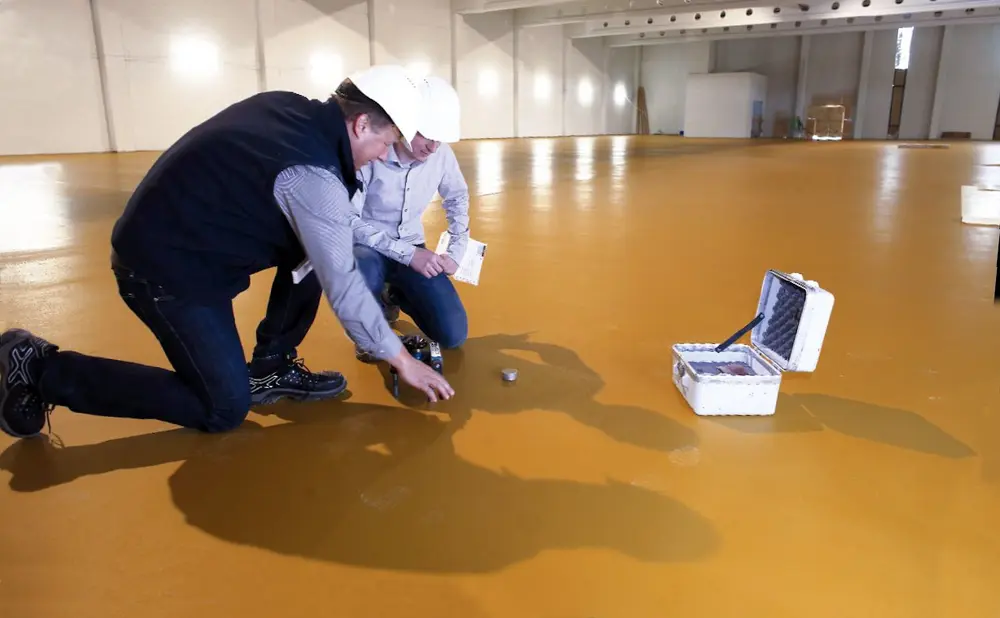
Chape avec émulsion de bitume
Ce sol repose sur la combinaison d'une émulsion de bitume avec du ciment. Comme garniture, on choisit du sable, de la pierraille, du quartz ou de la pierre de roche. Les caractéristiques de la finition de compression liée au ciment sont déterminées par le bitume.
Résine synthétique – chape truellée
Ce sol peut avoir différents liants: résine époxy, mais également polyuréthane, polyméthacrylate ou résine de polyester insaturé. Comme charge, on utilise du sable de quartz, du corindon ou du carbure de silicium.
Test du support
Il existe diverses méthodes pour tester le support. En effet, celui-ci doit être suffisamment solide pour supporter le sol industriel.
- Résistance à la pression: la durabilité du revêtement dépend en grande mesure de l'usage ainsi que de la résistance à la pression du support. Celle-ci est mesurée de manière non destructive avec un marteau antirebond. Idéalement, cette résistance à la pression doit être supérieure à 25 N/mm². Sinon, il faut appliquer un produit d'imprégnation renforçateur pour que le sol puisse supporter la charge mécanique.
- Résistance d'adhérence: c'est le nombre qui indique la puissance à la surface. On le mesure avec un mesureur de résistance d'adhérence. Celle-ci doit être d'au moins 1,5 N/ mm² pour une bonne adhérence du système de revêtement de sol au support.
- Examen des dégâts: le support à traiter doit évidemment être en excellent état, si l'on veut installer un sol industriel correctement. Une charge mécanique causée, par exemple, par la circulation d'un chariot élévateur peut abîmer les sols non traités, surtout au niveau des joints et dans les zones de passage.
- Mesure de l'humidité: l'adéquation d'un revêtement dépend du taux d'humidité du support. Si l'on veut éviter les dégâts sous la forme de craquellement ou de bulles, il faut pouvoir détecter l'humidité négative de la chape. La méthode idéale pour mesurer le taux d'humidité est une mesure CM.
- Fissures: il est important que les fissures soient réparées ou pontées. Pour ce faire, il faut observer la forme et/ou la taille de la fissure, qui peuvent varier: fissures fines, morcellement, fissures de joint, fissures dynamiques, etc. Toutes doivent être prétraitées et, en fonction du type, comblées par injection.
SYSTEMES DE SOL
Sealers
Sur les sols soumis à une charge légère à moyenne, on peut appliquer un sealer pour une action protectrice. Les sealers épousent la structure du support et sont efficaces en coûts. Ils peuvent être utilisés dans des espaces de production et des entrepôts.
Revêtement coulé
Ce système permet d'égaliser les petites irrégularités dans le support. Le matériau pigmenté est autonivelant et s'étale bien, ce qui permet d'obtenir une surface bien lisse. Le revêtement coulé s'applique en couche d'environ 3 mm. Un revêtement coulé s'applique sur les sols où l'on ne travaille pas avec des tissus: si un chiffon en tissu tombe sur le sol, on risque de glisser dessus. A côté de ça, le sol peut aussi être utilisé dans les environnements soumis à une charge dynamique.
Sol avec couches de saupoudrage
Pour une charge mécanique et thermique élevée, on peut installer un sol avec des couches de saupoudrage. Celui-ci se compose d'une couche de base autonivelante, dans laquelle on saupoudre du sable de quartz ou Hardkorn. Les épaisseurs de couche peuvent varier entre 1,5 et 9 mm. La couche de saupoudrage est antidérapante et peut donc être appliquée dans les environnements humides. L'industrie métallurgique aussi utilise ces sols.
Plancher truellé
Ce plancher possède la plus faible part de liant, avec une ligne de flottaison de charges qui y est adaptée. Le mortier peut être traité sous une latte et doit ensuite être épaissi et lissé avec une spatule. La couche doit faire au moins 4 mm d'épaisseur. Les planchers truellés sont naturellement antidérapants et supportent de lourdes charges mécaniques.
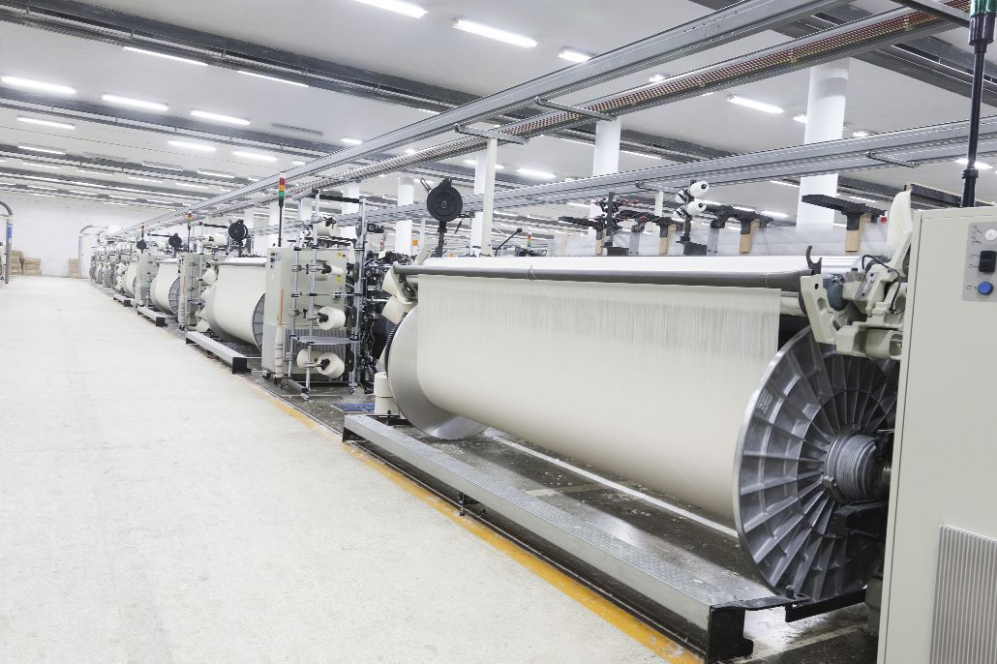
EXIGENCES SPECIFIQUES
Outre la charge mécanique, thermique ou chimique, il existe aussi des caractéristiques spécifiques qui doivent répondre à certaines normes.
Sols conducteurs
Les sols conducteurs sont dotés d'un revêtement qui doit éviter le chargement électrostatique. Ces sols sont composés et testés pour assurer la sécurité de l'homme et de la machine. A cela viennent s'ajouter d'autres normes en fonction du type de sol, telles que la norme EN 1081 pour les revêtements de sol élastiques.
Sols antidérapants
Les sols antidérapants aussi doivent répondre à différentes normes telles que NEN EN 13329 et DIN 51130. On y retrouve la méthode pour déterminer la résistance au dérapage. Dans certaines conditions, il est également nécessaire de déterminer le volume de refoulement (l'espace 'creux' dans le grain du sol pour recueillir diverses substances) dans la surface du sol. Notamment aux endroits où des substances liquides arrivent sur le sol et peuvent entraîner un risque de dérapage.
Merci à Remmers