Ne vous laissez pas duper
Malgré l'essor du multitâche, le tour CNC universel reste la meilleure solution pour certaines applications
Il semblerait parfois que les machines CNC multitâches dominent le marché au détriment du bon vieux tour CNC universel. Mais ce n'est qu'une impression. Le tour classique, aujourd'hui souvent équipé de deux, voire trois tourelles et d'une broche de reprise, continue de jouer un rôle important dans l'industrie de l'usinage. Au final, c'est le coût du produit à tourner qui détermine le choix de la machine.
Tour universel et machines multitâches
Le tour CNC universel, où le matériau est serré dans les griffes du mandrin, existe toujours. Les tourneurs CNC trouvent la programmation de ces machines particulièrement attrayante. En effet, dans la version de base, il n'y a qu'un axe qui tourne. Et pourquoi se donner la peine de fabriquer une pièce cylindrique quand on peut la programmer facilement?
Si le temps de cycle est primordial et que l'on peut réaliser l'usinage avec le burin rotatif, le choix est vite fait. Comme les outils se trouvent dans la tourelle, le temps de copeau à copeau lors du changement d'outil est court. Il est vrai que les machines multitâches d'aujourd'hui sont attrayantes, car elles permettent souvent d'usiner des pièces entièrement en une seule fois, même si des opérations de fraisage sont nécessaires.
Cependant, les investissements élevés constituent souvent un obstacle. Les fournisseurs affirment que pour des produits qui peuvent être très bien fabriqués sur des tours CNC ordinaires, on ne peut pas se permettre le prix horaire des machines multitâches . Ce n'est que lorsque les pièces deviennent plus complexes que le cost per part (cpp) peut être un facteur décisif. Mais le tour CNC universel reste un concept attrayant pour la fabrication de nombreux composants impliquant une mécanique de précision.
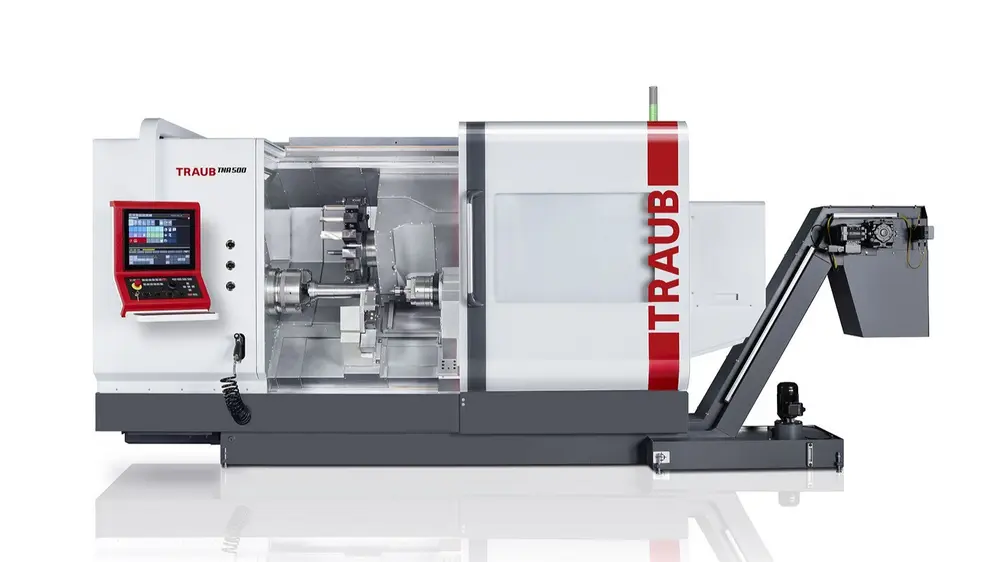
Plus de tourelles et une broche de reprise
En outre, le tour CNC est désormais également disponible en tant que machine haut de gamme. Dans ce cas, il convient d'envisager des versions dotées d'une tourelle supérieure et d'une tourelle inférieure, afin de pouvoir effectuer deux opérations simultanément et de disposer d'un plus grand nombre d'outils.
En outre, si la machine est équipée d'une broche de reprise, il est possible d'usiner le dernier côté de la pièce, tandis que la broche principale effectue les opérations principales d'une pièce ultérieure. De cette manière, on réduit les temps de cycle et on minimise le facteur humain.
Outils entraînés pour les opérations de fraisage sur tour
Les outils entraînés dans les tourelles peuvent également être utilisés pour effectuer des opérations de fraisage sur un tour, bien que leur puissance et leur couple soient plus limités que ceux d'une véritable fraiseuse. Ceci dit, ils sont suffisants pour de nombreuses applications, surtout si le tour est équipé d'un axe Y. L'axe Y permet d'effectuer des opérations supplémentaires de fraisage, de perçage et de taraudage hors centre, comme le fraisage d'une rainure de clavette.
Toutefois, cela n'a guère de sens d'utiliser des outils entraînés puissants sur un tour CNC. Pour l'un des fabricants de tours CNC de haute qualité, ce serait comme installer un moteur V8 dans une Golf VW. La chaleur dégagée lorsqu'on augmente fortement la puissance des outils entraînés crée d'autres inconvénients, car le tour CNC n'est pas conçu pour dissiper rapidement cette chaleur. La chaleur ne peut alors qu'entraîner des écarts de précision dimensionnelle et un processus de tournage moins stable.
Cela n'a guère de sens d'utiliser des outils entraînés puissants sur un tour CNC. Ce serait comme installer un moteur V8 dans une Golf VW
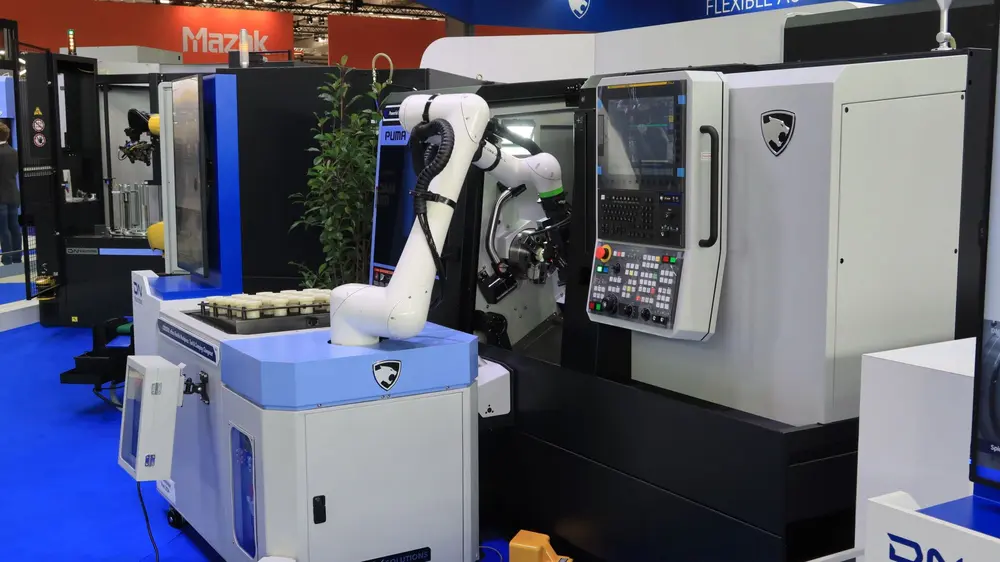
La stabilité du processus est une condition pour l'automatisation
C'est précisément l'un des points attrayants d'un tour CNC: le processus peut être rendu très stable, en partie grâce à la méthode de serrage dans le mandrin ou la pince de serrage. Et c'est précisément cette stabilité qui est recherchée lors de l'automatisation. C'est pourquoi il existe toujours un marché pour le tour à banc incliné avec bloc de guidage: une combinaison robuste et précise.
En fonction de l'application, un large éventail de solutions d'automatisation est disponible, allant d'un simple cobot à un robot industriel, en passant par un gantry loader ou un ravitailleur de matériau brut avec des pinces qui prélèvent la pièce.
En fonction de l'application, une large gamme de solutions d'automatisation est disponible
Ravitaillement en barres
Le ravitaillement en barres est une manière d'automatiser relativement simple et peu coûteuse. Le matériau est alimenté automatiquement par l'entrée et retiré après l'usinage. De cette manière, il est possible d'augmenter le nombre d'heures sans personnel avec un faible investissement.
L'inconvénient est que l'on commence toujours avec le même diamètre et qu'il faut parfois tourner plus de matériau que lorsqu'on travaille avec un diamètre plus petit. Un développement récent dans les ravitailleurs de barres est que les guides pour freiner le matériau s'ajustent automatiquement à un diamètre différent après la programmation. En moins d'une minute, l'installation est ajustée à un diamètre différent. De cette manière, il est également possible de travailler sans personnel à partir de différents diamètres.
Un autre développement dans ce domaine est l'évacuation automatisée de longues barres via la sous-broche de la machine. Les barres inutilisées sont ensuite placées dans un magasin de stockage.
Le ravitaillement en barres est l'automatisation la plus évidente, en particulier pour les petits diamètres.
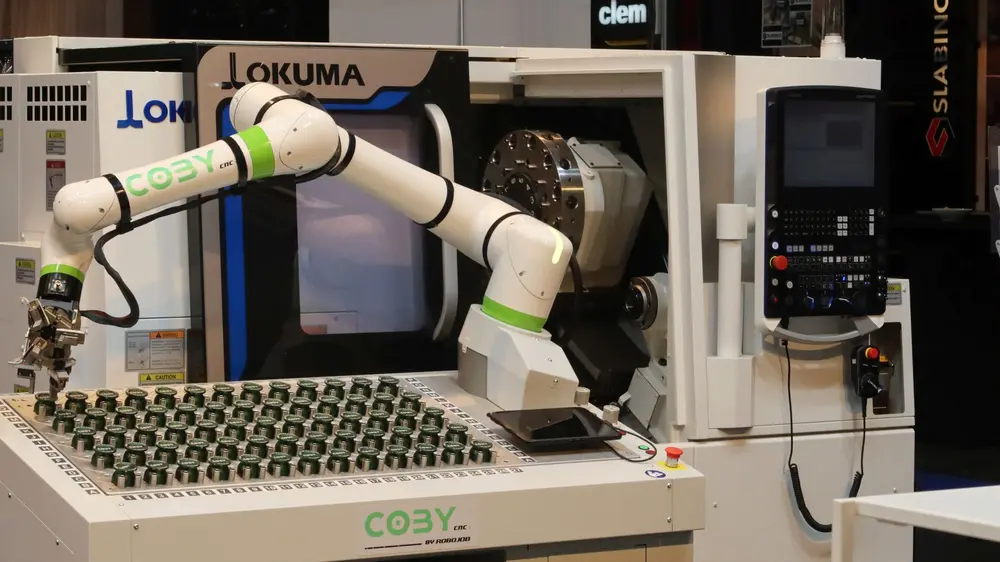
Chargement par robot
Lorsque des pièces sont tournées à partir d'un diamètre plus important, le chargement par robot entre en jeu. En principe, il s'agit toujours d'une manipulation de produits. On peut alors choisir d'empiler les pièces brutes et les composants finis ou de travailler avec une plaque quadrillée.
Les systèmes permettant de changer les éléments de serrage d'un tour CNC sont plus avancés. Les éléments de serrage tels que les mandrins peuvent être changés automatiquement par un robot, un portique ou directement via la broche de la machine, avec ou sans butée. Le préhenseur du robot prend le mandrin, y compris la butée de pièce, dans le magasin et règle le mandrin en quelques secondes avec le diamètre, le profil de serrage et la variété de butée adaptés à l'opération et à la pièce à usiner.
Le changement d'un système de serrage complet, d'un mandrin ou d'un mandrin avec les fixations correspondantes, est l'étape suivante de l'automatisation. La technologie des capteurs devient alors indispensable pour garantir un usinage sûr et correct par la suite.
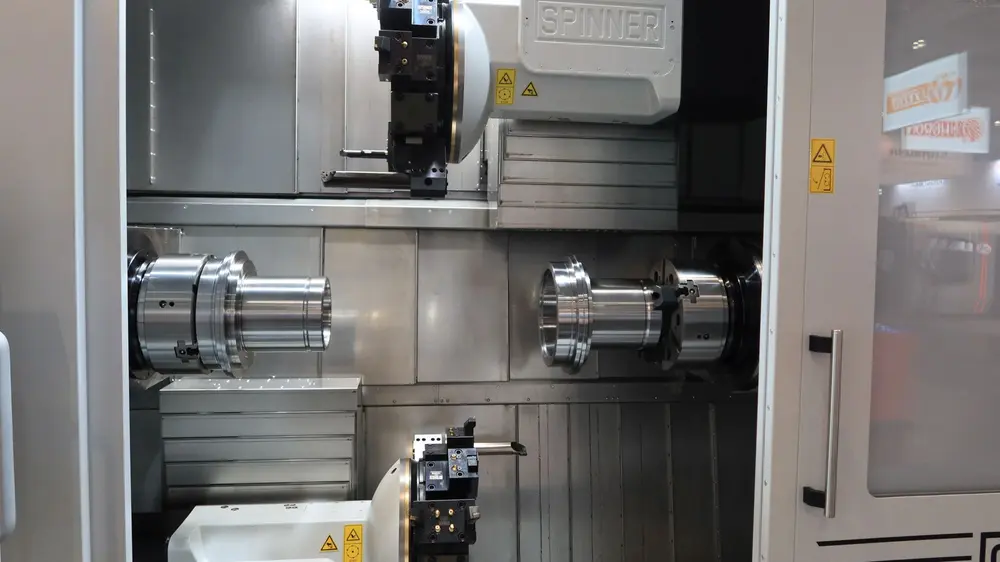
Changements d'outils automatiques
L'une des principales limitations d'un tour CNC par rapport à un centre de tournage-fraisage standard est que la tourelle dispose d'un nombre limité de positions d'outils. En général, ces positions sont au nombre de 12 ou 24, parfois même pas toutes adaptées aux outils entraînés.
24 positions, c'est le cas d'une tourelle qui peut indexer par demi-position. Par rapport à une fraiseuse CNC, c'est encore peu, surtout si une ou deux positions sont perdues au profit d'un palpeur de mesure pour déterminer la précision dimensionnelle dans la machine.
Le deuxième inconvénient est que le changement et le réglage des outils prennent du temps, car ils sont généralement effectués manuellement lorsque la machine est à l'arrêt. Il s'agit là d'une différence substantielle par rapport à une machine moderne multitâche dotée d'une broche de fraisage et d'un vaste magasin d'outils.
Aujourd'hui, cependant, il est possible de demander à un robot de changer les outils dans la tourelle du tour. Cela augmente l'autonomie, même si un nouveau lot de pièces à usiner nécessite un outillage différent. En automatisant le changement d'outils dans une tourelle, on peut économiser jusqu'à 85% du temps pendant lequel la machine est normalement à l'arrêt pour cette raison.
Le système convient aux outils les plus couramment utilisés, tels que HSK, Capto, Hydrodehn et les pinces de serrage peuvent également être changées manuellement. Lors d'un changement automatisé ou robotisé de la pince de serrage, il est important de vérifier qu'il ne reste pas de copeaux.
Dans les systèmes modernes, on vérifie automatiquement si l'outil est placé à plat dans le support. Des capteurs sont utilisés pour accroître la fiabilité du processus. Ils enregistrent la force de serrage, si la surface de contact est plane et si le diamètre de la pièce est correct. Les données sont transmises à la commande du tour, pour d'éventuelles corrections ou pour une assurance qualité.
Une nouvelle étape consiste à lire ces données pour une application externe, les fabricants de tourelles et de porte-outils utilisant également la norme umati pour standardiser l'échange de données.
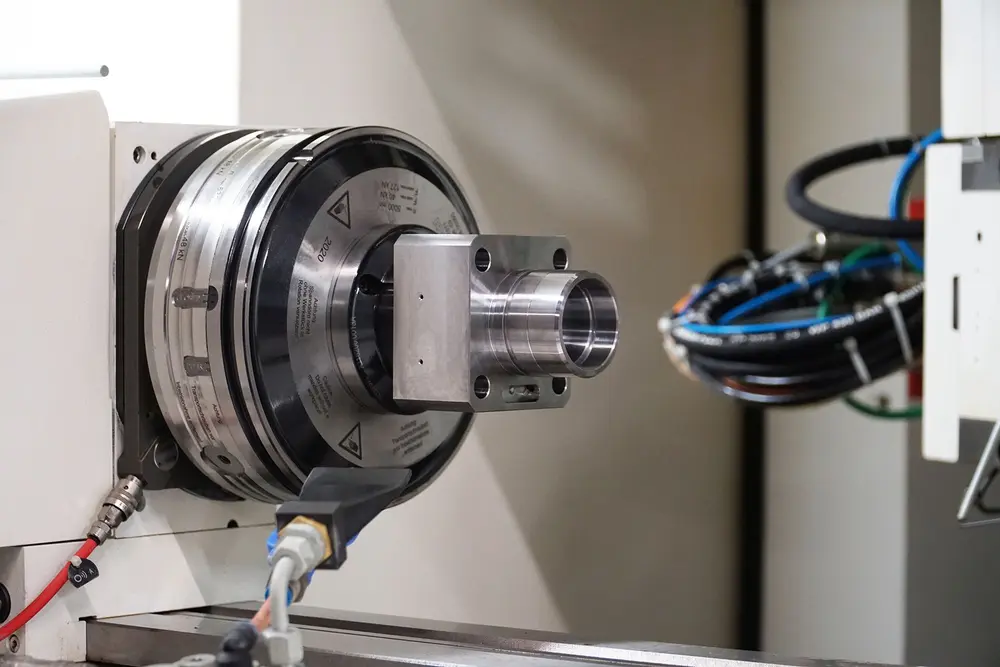
Les systèmes de changement rapide, tels que le centroteX AC de Hainbuch pour le serrage externe et interne, permettent un degré d'automatisation plus élevé, même pour les petites séries. Il est ainsi possible de changer un dispositif de serrage complet sans personnel. Dans la pratique, il s'agit d'un mandrin ou d'un mandrin avec les éléments de serrage correspondants. Le système de changement rapide se verrouille au moyen d'un mécanisme à baïonnette actionné par un actionneur mécanique. Le concept de propreté intégré utilise des processus de soufflage et de rinçage pour garantir la fiabilité du processus de changement
Le tronçonnage, une opération critique
Le tronçonnage de la pièce est une étape critique du processus de tournage CNC avec ravitaillement en barres. Une fois l'opération terminée, la pièce est détachée de la barre alimentée depuis l'extérieur de la machine avec un outil de tronçonnage. Cette opération est essentielle à la fois pour éviter d'endommager la pièce et pour garantir la stabilité de l'ensemble du processus de tournage.
Le choix d'une plaquette qui crée un copeau plus étroit que la largeur de la rainure permet un bon enlèvement des copeaux, ce qui évite d'endommager la pièce. Cela permet également d'éviter que les copeaux laissés sur place n'entraînent des problèmes.
Veillez toujours à ce que la longueur de porte-à-faux de l'outil de tronçonnage soit la plus courte possible. Une rupture de l'outil de tronçonnage peut endommager la pièce, ce qui est d'autant plus préjudiciable qu'elle a probablement déjà subi la majeure partie de l'usinage.
Le refroidissement de la surface de coupe est également important. Il permet en effet de mieux contrôler les copeaux. Les plaquettes avec refroidissement intégré sont un plus.
Une nouvelle méthode de tronçonnage est le tronçonnage sur l'axe Y, où la force de coupe circule dans une direction plus favorable parce que la face supérieure de la plaquette est perpendiculaire à la lame. Cela permet de réduire les vibrations par rapport au tronçonnage conventionnel. Ce dernier utilise une avance le long de l'axe X et la force de coupe est dirigée dans le sens de la partie la plus faible de la lame. La condition préalable est bien sûr que le tour dispose d'un axe Y.