LA DÉCOUPE LASER CONTINUE À SE DÉVELOPPER
L'innovation technologique et le contrôle du processus sont des sujets brûlants
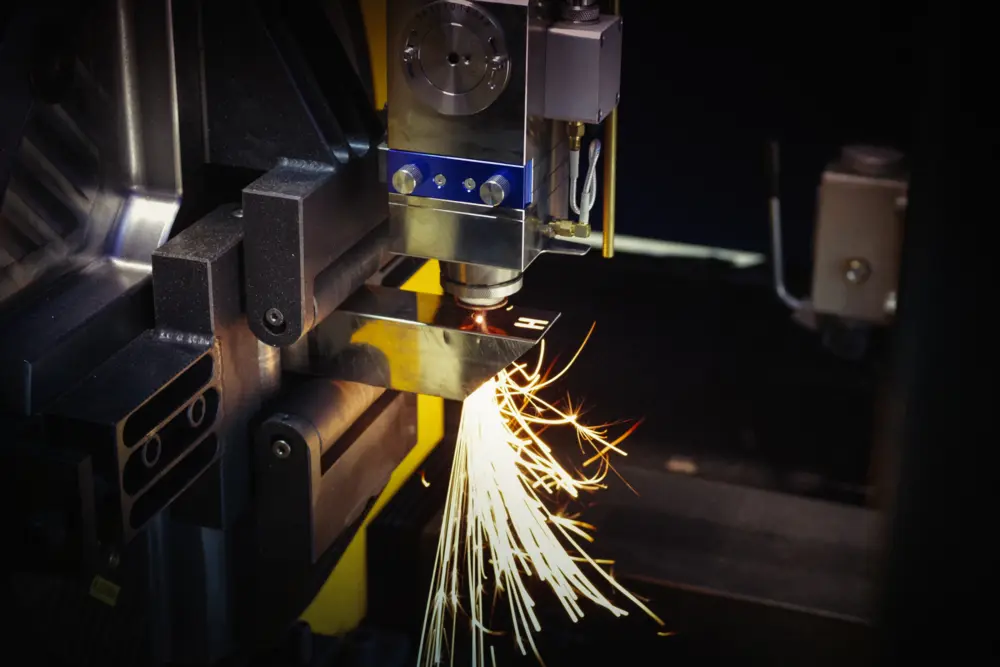
Depuis son introduction en 1965, la technique de la découpe laser a connu de nombreux développements et est toujours en pleine évolution. D'une part, il y a les innovations liées à la technologie de coupe, d'autre part, il y a les développements dans le domaine du support et de l'intégration de processus, avec pour objectif ultime une tôlerie autonome. C'est l'heure du bilan avec Kurt Van Collie (LVD), Luc Creemers (Yamazaki Mazak), Matthieu Deram (Haco) Marc Leeman (Metanox), Hans van de Meerakker (Bystronic) et Karel Vincke (V.A.C. Machines).
Innovations technologiques
Laser à fibre
Le laser à fibre gagne du terrain par rapport au laser CO₂. Selon certains, cette technologie va progressivement disparaître, tandis que d'autres pensent qu'elle restera la technologie de référence pour certaines applications. Les pourcentages mentionnés lors de la discussion varient - 90 à 10%, 95 à 5% - mais tous sont en faveur du laser à fibre. Haco et LVD ont arrêté de vendre des machines avec des lasers CO₂ il y a quelques années, Metanox aussi. Chez Mazak, la variante CO₂ est encore disponible, mais cela ne devrait plus durer très longtemps. Chez Bystronic, les produits encore disponibles sont éliminés progressivement.
Deram (Haco) reconnaît la position de leader du laser à fibre, mais note que le laser CO₂ a encore une part importante dans des applications telles que la découpe et le soudage de matériaux organiques. Karel Vincke (V.A.C. Machines) fait partie de ceux qui croient en la technologie CO₂: " Les deux technologies ont leurs points forts, mais le CO₂ reste plus performant que la fibre dans certaines applications. LVD fait figure d'exception. Van Collie: "D'après ce que je sais, 95% des lasers vendus sont des 'solid state lasers'. On parle de solid state car Trumpf préfère pour l'instant la technologie du laser à disque."
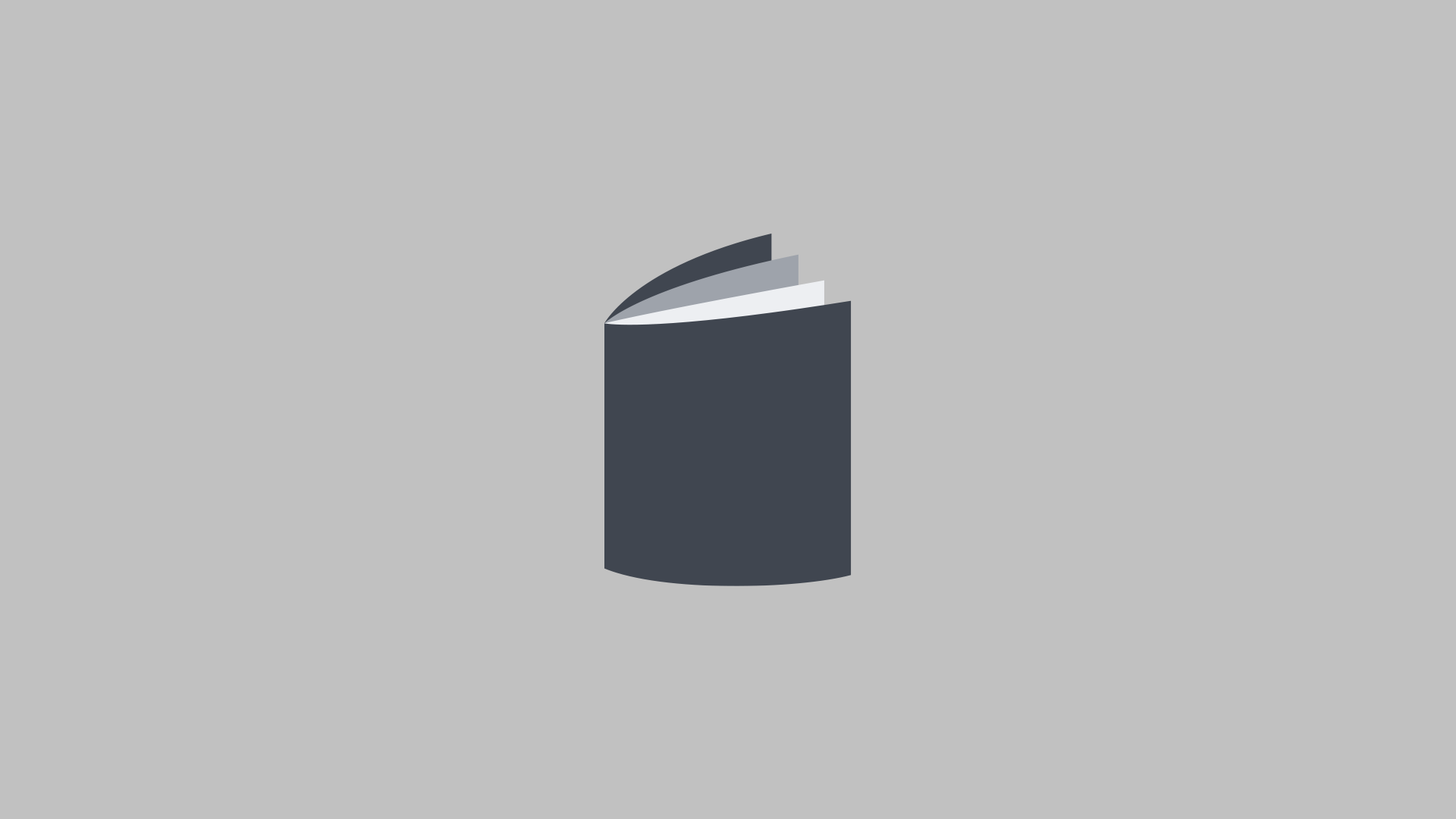
Qu'est-ce que la découpe au laser ?
La découpe au laser est une technique de découpe thermique permettant de traiter le métal de manière rapide et précise. Le faisceau laser est généré dans la source laser - un laser à CO₂, à diode, à disque ou à fibre - et est guidé vers la tête de coupe de la machine par des miroirs ou un câble fibre. Une fois là, il est fortement convergé à l'aide d'une optique de mise au point. La tôle fond localement, ce qui permet une découpe extrêmement précise à l'aide d'une buse fixée à la tête du laser. Un jet de gaz expulse le matériau fondu et réduit l'oxydation des arêtes de coupe. Selon le type de matériau, l'épaisseur de la tôle et les opérations de finition, le gaz de coupe est de l'azote, de l'oxygène, de l'air comprimé ou un mélange de ceux-ci. Avec la découpe au laser, la zone affectée par la chaleur est petite, la coupe est très fine et la perte de matériau est limitée.
PUISSANCES plus élevées
La demande de puissances plus élevés va se poursuivre, compte tenu des avantages qu'elles offrent. Van Collie (LVD): "A ma connaissance, un fabricant chinois est déjà sur 40 kW, plusieurs autres sur 30 kW et un grand nombre sur 20 kW. Deram (Haco) pense qu'en ce qui concerne les tôles de (plus) petite épaisseur, la limite de 15 kW n'a pas encore été atteinte, mais que c'est différent pour les matériaux de plus de 25 mm. Ils offrent déjà des puissances allant jusqu'à 20 kW. Leeman (Metanox), Creemers (Mazak) et Van Collie (LVD) s'attendent à ce que le prix devienne de plus en plus important. Van Collie: "A mon avis, le coût par pièce est le facteur clé, et il diminue considérablement avec les puissances plus élevées: dans l'acier inoxydable épais, un laser de 20 kW coupe deux fois à deux fois et demie plus vite qu'un laser de 10 kW, en utilisant la même quantité d'azote."
Creemers (Mazak) a tout de même une remarque: "Les puissances plus élevées sont surtout intéressantes pour les travaux de masse/série où une automatisation appropriée et une grande capacité de stockage sont inhérentes à l'obtention d'une efficacité maximale. L'investissement que cela nécessite n'est pas à la portée de toutes les entreprises métallurgiques". Van de Meerakker (Bystronic) est également de cet avis: "Pour une journée entière de découpe d'acier inoxydable épais, une capacité plus élevée a du sens, mais pour une épaisseur de 1 mm, ce n'est pas du tout le cas. C'est pourquoi les décisions concernant l'alimentation, les systèmes de chargement, les solutions logicielles et l'automatisation doivent toujours être prises en concertation avec le client."
Vincke (.machines) se demande s'il ne vaut pas mieux se concentrer sur (l'automatisation des/)les processus entourant le processus de coupe plutôt que sur la puissance. "Une machine de plus faible puissance peut travailler pendant plusieurs périodes de travail en rotation sans intervention humaine grâce à l'automatisation et donc avoir un débit plus important qu'une machine de forte puissance."
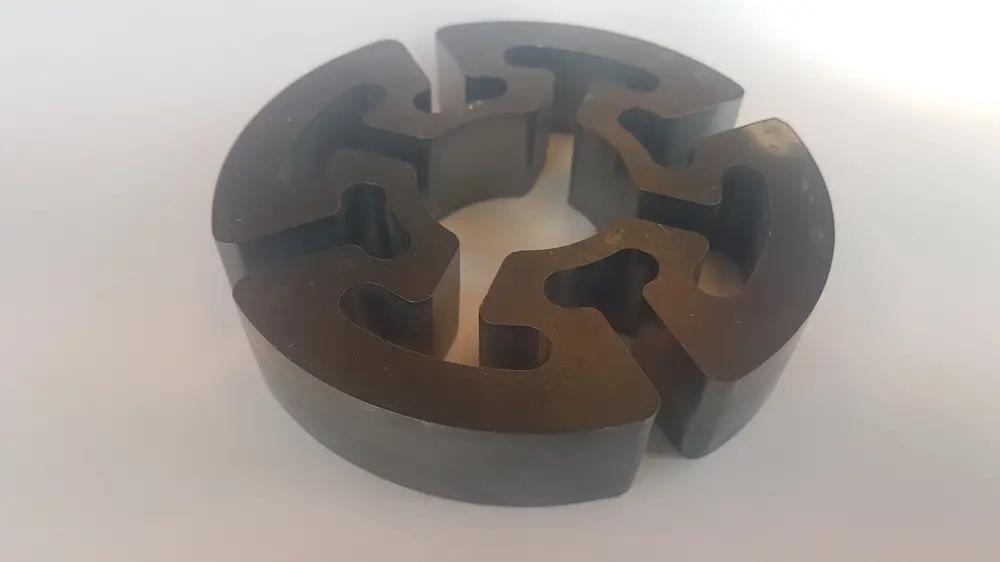
Points à améliorer
Creemers (Mazak): "La qualité de coupe dans certains matériaux reste une préoccupation - pensez aux arêtes vives et à la légère formation de bavures et de grains - mais à mesure que la puissance et la vitesse de coupe augmentent, ces phénomènes sont moins fréquents." Deram (Haco): "Il est certain que la découpe de tôles épaisses avec une puissance élevée peut être améliorée: l'un des rares avantages de la technologie CO₂ reste la meilleure qualité de coupe avec des matériaux épais (20mm+)." Pour Van Collie (LVD), ce sont les sources laser plus puissantes et abordables qui doivent être au centre des préoccupations. Vincke (V.A.C. Machines) cite deux exemples des améliorations déjà réalisées par Trumpf: la fibre BrightLine qui permet de régler la qualité de faisceau de la machine et la High Speed Eco, qui réduit la consommation d'azote jusqu'à 70%.
"L'un des rares avantages de la technologie CO₂ reste la meilleure qualité de coupe avec des matériaux épais"
Van de Meerakker (Bystronic) indique que la technologie de coupe est désormais conforme aux normes et que les efforts sont entièrement axés sur la capacité à fonctionner de manière autonome. Creemers rapporte que Mazak travaille sur la technologie double core, une technologie de puce qui permet d'exécuter des tâches en flux parallèles, ce qui se traduit notamment par des temps de traitement plus courts. Van Collie (LVD): "Dans le contexte d'une puissance plus élevée, nous examinons la tendance à utiliser, en plus de l'oxygène et de l'azote, un mélange des deux - en particulier pour la découpe de tôles épaisses."
Vincke (V.A.C. Machines) garde encore un peu de suspense: "Plus tard dans l'année, nous introduirons un nouveau procédé de coupe dont je ne peux rien dire pour l'instant, si ce n'est qu'il y a la possibilité de rétrofiter cette technologie. Deram termine en annonçant que Haco travaille sur le 'water guide laser cutting', une technique qui peut être appliquée là où une grande précision géométrique est requise.
manipulation des pièces laser
Compte tenu du cauchemar logistique que représente souvent la manipulation des pièces laser, il est nécessaire de disposer de systèmes qui font en sorte que l'on sache exactement où se trouve chaque pièce à tout moment dans la chaîne. Il existe plusieurs possibilités pour une 'gestion intelligente' des pièces laser. Dans l'une des usines japonaises de Mazak, par exemple, un code QR est désormais utilisé pour suivre chaque pièce jusqu'au niveau suivant, de la découpe et du pliage au soudage et à la peinture. V.A.C. Machines aide les clients à réaliser un audit étape par étape pour rendre leur organisation intelligente et Bystronic vend déjà des machines de tri qui fonctionnent 24 heures sur 24, ce qui, selon Van de Meerakker, lui procure un avantage sur ses concurrents.
Les avis divergent quelque peu quant à savoir laquelle des deux méthodes de codage a le plus d'avenir. Vincke ( V.A.C. Machines) et Creemers (Mazak) estiment que les deux présentent des avantages: un numéro de pièce est immédiatement visible alors qu'un code 2D nécessite un scanner, mais l'appel du programme ultérieur correct n'est possible qu'avec un scanner.
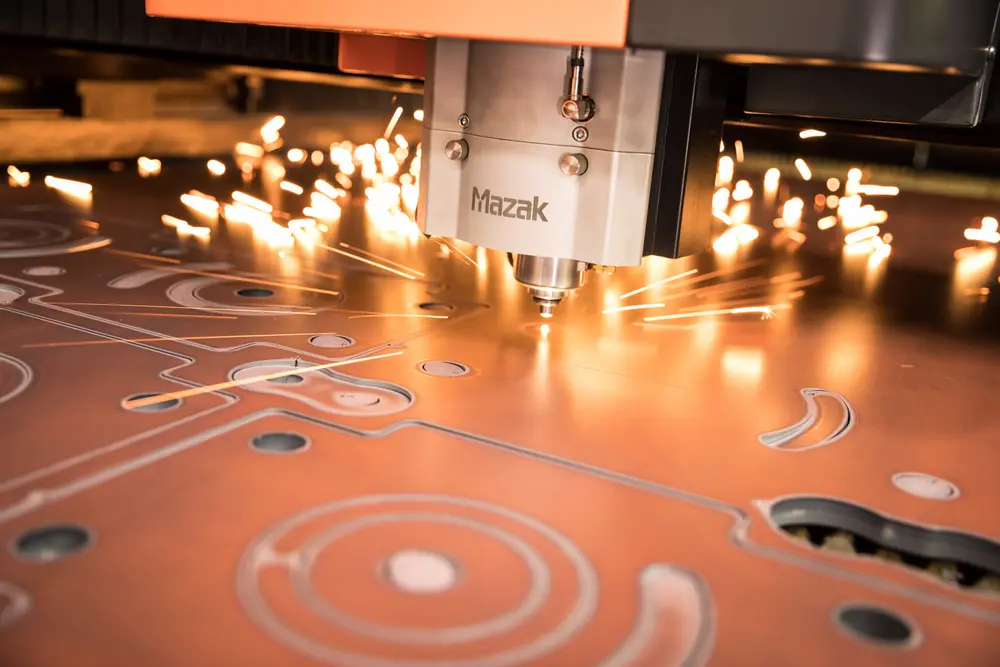
Deram (Haco) indique que la plupart des clients optent encore pour le marquage des pièces, mais pense que le codage gagnera en popularité à l'avenir. Leeman (Metanox) partage cet avis: "L'avantage du codage est qu'un code QR peut contenir beaucoup d'informations." Van de Meerakker (Bystronic) est d'accord mais ajoute que, bien qu'il existe de nombreuses méthodes de codage, il manque encore une solution universelle. "L'utilisation est déterminée par ce que le client veut en faire et par le produit final".
Selon Van Collie (LVD), un code QR est le plus fiable en termes de lecture, mais pas particulièrement rapide. "Ce problème peut être surmonté en gravant avec une tête laser séparée de faible puissance, beaucoup plus rapide. Dans ce cas, c'est le miroir qui se déplace et les axes de la machine restent en place."
Contrôle du processus
Le contrôle du processus est la planification et la régulation d'un processus; le support et l'intégration de processus en font partie.
support de processus
Dans les années à venir, l'intérêt pour les systèmes de support de processus va croître. Ces derniers contribuent à rendre le processus plus efficace, plus sûr et plus rentable. Deram (Haco) à ce sujet: "La surveillance intelligente du processus permet de se faire une idée de la qualité. Grâce à la surveillance automatique, l'usure peut être identifiée à un stade précoce, par exemple. Cela permet d'éviter les temps d'arrêt de la machine et d'améliorer la qualité globale de la coupe."
Interrogé sur des exemples concrets, Creemers (Mazak) mentionne que la surveillance de l'image de coupe dans leur usine est actuellement basée sur la mesure de la réflexion via des capteurs dans la tête de coupe. "Lorsque les valeurs changent, la vitesse est ajustée jusqu'à ce que les valeurs reviennent à leur niveau normal; si cela échoue, la machine s'arrête automatiquement." Selon Leeman, Metanox utilise un système de caméras pour optimiser l'imbrication, le positionnement de la plaque et celui des pièces sur la table de coupe.
"La surveillance intelligente du processus permet d'avoir un meilleur aperçu de la qualité"
A cet égard, Van de Meerakker (Bystronic) mentionne la fonction TiltPrevention: "Elle permet de créer des séquences de coupe qui minimisent le risque de parties saillantes. Cela réduit les perturbations des processus de coupe et les temps d'arrêt causés par les collisions avec la tête de coupe." En ce qui concerne les machines Vincke ( V.A.C. Machines), il s'agit d'Active Speed Control et de Coolline. Le premier assure un contrôle en temps réel du processus de coupe depuis le haut, grâce à une surveillance via la buse en cuivre. Coolline est un système de support de processus qui utilise le refroidissement par eau pour éliminer la chaleur, notamment des plaques épaisses,
Van Collie (LVD) salue les efforts déployés pour améliorer la fiabilité des processus, mais voit aussi des 'impossibilités': "La surveillance de l'écoulement de la matière fondue est intéressante, mais avec un capteur/caméra, on ne voit que la partie supérieure du bain de soudure et on n'a aucune visibilité sur ce qui se passe en dessous."
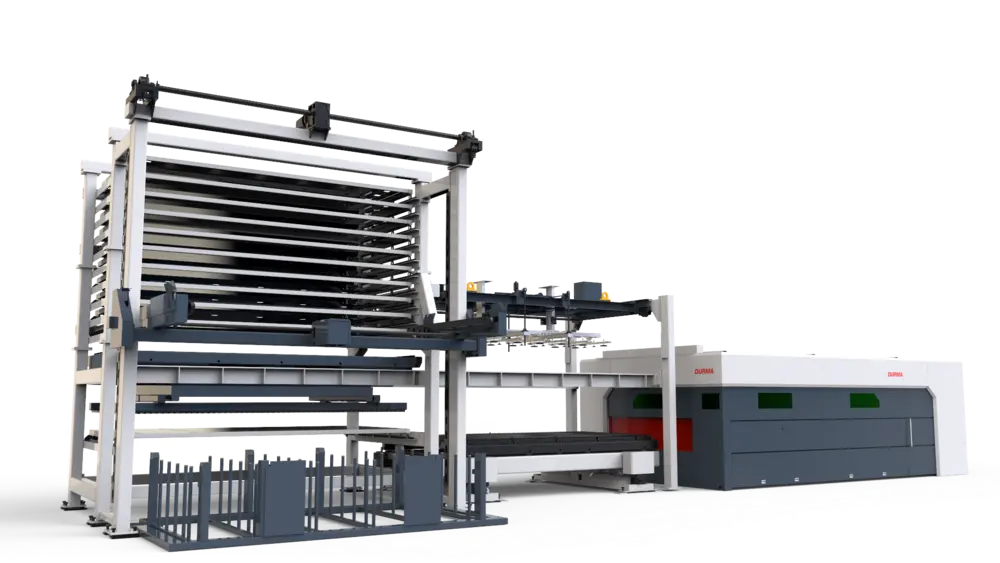
Intégration de processus
On s'attend à ce que l'usinage des métaux mette de plus en plus l'accent sur l'intégration de la technologie. Cela nécessite non seulement une automatisation poussée, mais aussi l'intégration, par exemple, de systèmes de gestion des stocks et le support des processus. Les participants à la discussion en sont bien conscients et s'y préparent, la coopération constituant le fil conducteur.
Van de Meerakker (Bystronic): "Nous créons un écosystème au sein duquel nous pouvons très facilement collaborer avec des parties externes, tant sur le plan matériel que logiciel. Chez LVD, on ne lance pas à la légère non plus. Van Collie: "L'intégration est une priorité pour nous depuis plus de 10 ans. Nous avons besoin d'une interface avec des parties externes et nous sommes bien préparés à travailler avec d'autres machines/processus.
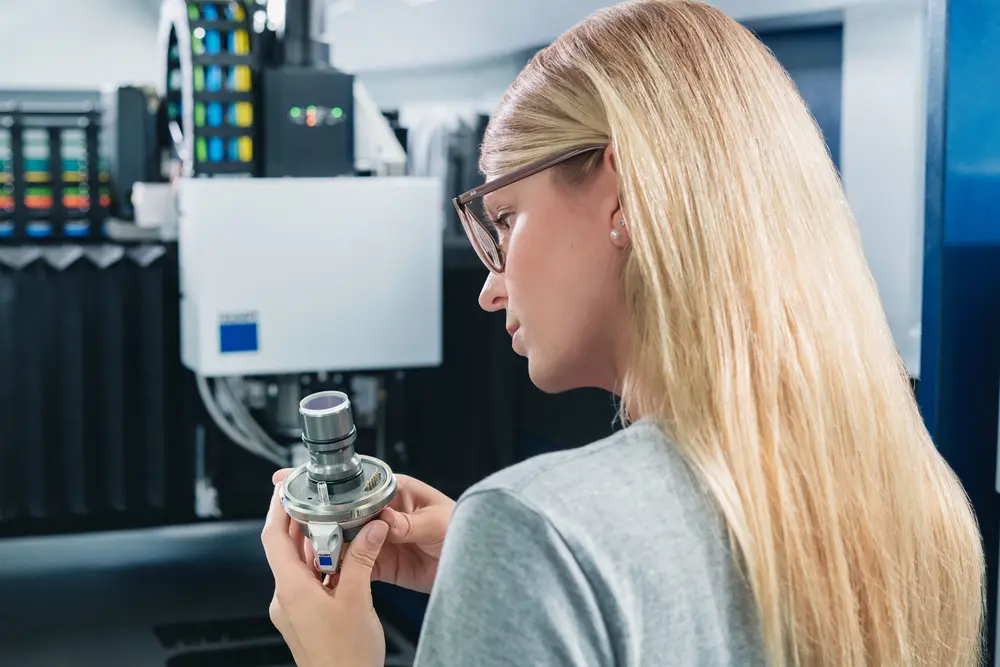
Selon Creemers, cela s'applique également à Mazak: "La communication avec différents types de machines et de systèmes d'automatisation et l'intégration des processus administratifs et de la gestion des stocks sont indispensables. Nos machines seront équipées des interfaces nécessaires pour pouvoir fonctionner en tant qu'intégrateur dans un concept global." En matière de R&D et de solutions logicielles, Haco travaille en étroite collaboration avec des partenaires qui sont des experts absolus dans ce domaine. Toutes nos machines peuvent facilement être reliées à des systèmes d'alimentation et de déchargement automatiques, ce qui permet une utilisation plus optimale de la tôle et de la machine. Cela améliore le rendement et la compétitivité du département de la tôlerie."
Metanox est également prêt pour ça, selon Leeman: "En ce qui nous concerne, nous pouvons livrer dès demain, pour ainsi dire. Nos fournisseurs Salvagnini et Durma possèdent l'expertise nécessaire et sont tout à fait capables de contribuer à l'intégration de la technologie."
Le facteur humain
Bien que la technologie de découpe au laser soit de plus en plus avancée, les choses tournent encore (trop) souvent mal en raison d'actions humaines incorrectes:
- erreurs lors de la préparation du travail et/ou de la programmation;
- utilisation, positionnement ou remplacement incorrects des pièces;
- utilisation de gaz de coupe insuffisamment purs;
- préférence pour la vitesse plutôt que pour la fiabilité du processus.
Dans de nombreux cas, cela peut être imputé à un manque de connaissances et/ou au non-respect des directives et/ou des instructions. Cette situation ne peut être évitée que par une formation appropriée, une responsabilité partagée entre le fournisseur et l'utilisateur. La technologie n'est rien si elle n'est pas utilisée correctement.
La tôlerie autonome
Selon beaucoup, l'objectif ultime de l'intégration des processus est l'usine de tôlerie autonome, mais tout le monde ne considère pas la réalisation de cet objectif comme évidente. Pour Creemers (Mazak), le concept existe déjà pour le travail répétitif et en série et l'étape suivante est la généralisation. "Toutefois, je me demande à quelle vitesse cela pourra se faire, car il y a encore trop de variables à l'heure actuelle qui nuisent à un processus stable et autonome."
"Je pense qu'il faudra encore un certain temps avant que le travail autonome puisse se faire sans intervention humaine"
Deram (Haco) est modérément optimiste: "Il devrait être possible de réaliser une usine hautement spécialisée et plus ou moins entièrement automatisée dans les 5 à 10 prochaines années. Toutefois, pour l'instant, nombre de nos clients préfèrent investir dans des travailleurs compétents et fidèles et ne veulent/peuvent pas (encore) investir dans des formes d'automatisation 'autonome' de grande envergure et à forte intensité de capital." Leeman, (Metanox) est d'accord: "Je pense aussi qu'il faudra un certain temps avant que le travail autonome puisse se faire sans intervention humaine."
Van Collie (LVD): "A mon avis, l'autonomie est une utopie pour la plupart des entreprises de tôlerie. Selon notre vision, c'est un pas trop loin; nous préférons parler de 'bras opérateur'. Pour les travaux répétitifs et en série, c'est largement faisable, mais là aussi, la grande question est la suivante: quel est le poids de l'investissement supplémentaire sur le coût/la pièce? Van de Meerakker (Bystronic) ne pense pas que c'est aller trop loin: "Nous investissons beaucoup dans l'usine intelligente et travaillons avec et sur des systèmes modulaires et évolutifs. Cependant, il reste encore de nombreux problèmes pratiques à résoudre, et c'est celui qui sera le plus à même de le faire qui créera en fin de compte l'usine intelligente."
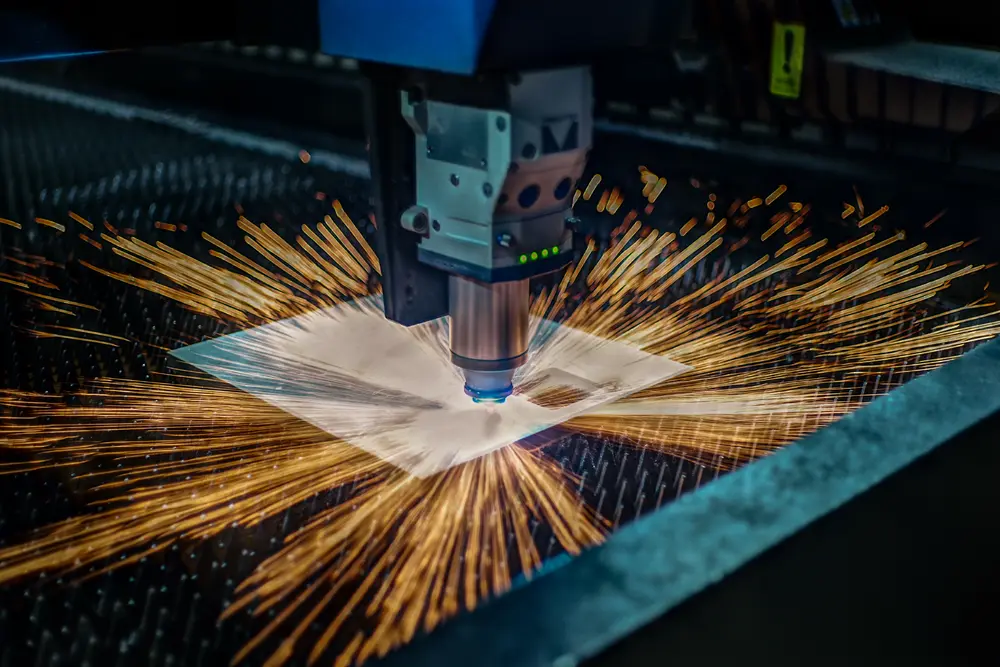