Outils en carbure monobloc
De la circularité à l'impression 3D
Les outils en carbure monobloc font partie intégrante de l'usinage moderne. Certains chercheurs pensent avoir trouvé une solution pour l'usinage à sec avec ces outils tandis que d'autres misent sur l'impression 3D avec du carbure de tungstène.
Les outils en carbure monobloc (VHM) sont largement utilisés dans l'usinage. Ils sont constitués de carbure de tungstène et d'un métal plus souple servant de liant. Le carbure de tungstène (tungstène et carbone) est dur (comme le diamant, d'où le nom de Widia, qui signifie Diamant en allemand) et présente l'avantage supplémentaire que cette dureté ne change pratiquement pas lorsque la température augmente. C'est idéal pour l'usinage. On ajoute souvent du cobalt comme matériau liant. En frittant le carbure de tungstène, les fabricants peuvent contrôler les propriétés et rendre le matériel de coupe encore plus dur. Une modification des paramètres de frittage permet d'augmenter le pourcentage de cobalt dans les couches extérieures, d'environ 20-30 μm. Cela améliore la ténacité, ce qui se traduit par une plus grande résistance à la déformation. Grâce à l'élasticité du substrat, il est possible d'appliquer un revêtement sur un outil en carbure de tungstène manière durable.
Certains chercheurs pensent avoir trouvé une solution pour l'usinage à sec avec ces outils
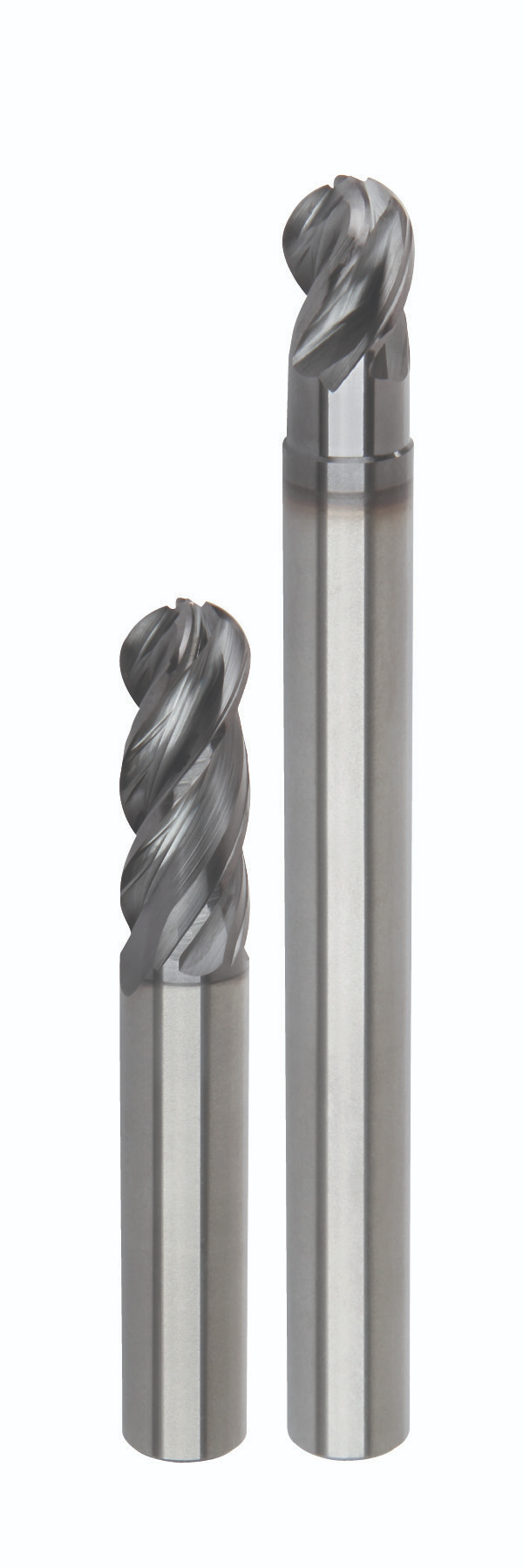
Différents procédés
Les fabricants d'outils en carbure de tungstène n'utilisent pas tous le même procédé pour fabriquer leurs outils. Outre leurs propres paramètres de substrat et de processus, ils peuvent utiliser le frittage dans un four à vide ou combiner cette étape avec une presse isostatique à chaud. Outre l'effet de température, la poudre est alors compactée par pression. Cette étape du processus permet aux fabricants d'influer sur la densité et la quantité de cobalt requises pour un outil. Elle permet aussi de modifier la microstructure du carbure de tungstène. Il existe des centaines de nuances de carbure, souvent adaptées à l'usinage d'un matériau spécifique ou à des fins particulières. Un développement assez récent dans le monde universitaire consiste à soumettre le substrat non revêtu à un post-traitement cryogénique supplémentaire. Cela implique de refroidir le matériau à -193 °C et de le laisser pendant environ 27 heures dans un environnement présentant cette température extrêmement basse. La température est ensuite ramenée lentement à la température ambiante et éventuellement chauffée à 200 °C. La microstructure du substrat WC-Co n'en est pas modifiée, mais cela entraîne un effet précis: les flancs des outils en carbure présentent une usure réduite de 4 à 7%.
Microstructures ou revêtements
Aujourd'hui, la plupart des outils VHM sont revêtus. Ce revêtement empêche l'oxydation due à l'augmentation de la température sur les côtés, augmente la dureté et procure un effet lubrifiant. En pratique, ce dernier point est complété par un lubrifiant réfrigérant. Certaines entreprises souhaitent s'en débarrasser parce qu'elles veulent un processus de production plus durable ou parce que les exigences de propreté imposent un nettoyage très complet par la suite. Ces dernières années, plusieurs études ont été menées dans le monde entier sur le fraisage à sec avec des outils VHM. Dans une étude récente, on a introduit des microstructures dans la surface de la fraise. Cela améliore ses propriétés tribologiques. Ces microstructures mécaniques (MµT) semblent bien fonctionner lorsqu'elles sont associées à un revêtement en bisulfure de molybdène. Les performances des outils VHM sont telles que l'usinage à sec peut être une véritable alternative à l'usinage avec des fluides réfrigérants. A l'Université de Johannesburg, des essais ont été réalisés avec le fraisage à sec de 316L avec des outils VHM, sur lesquels on avait appliqué une microtexture par électroérosion. Cette texture est située sur les flancs de la fraise. Les tests ont montré que ces outils sont de loin supérieurs aux fraises non revêtues en termes de comportement à l'usure, de formation de copeaux et de taux d'enlèvement de matière (MRR). Les textures réduisent les forces de coupe sur l'outil, contribuant ainsi à une plus longue durée de vie de l'outil et à de meilleures performances de coupe. A Johannesburg, de nombreux essais ont été réalisés avec différentes conditions de coupe. Ces résultats montrent que des vitesses plus élevées avec une avance et une profondeur de coupe moyennes sont les conditions idéales pour le fraisage à sec du 316L avec des fraises VHM texturées. Une université turque étudie les possibilités offertes par les revêtements nanocomposites combinés à un post-traitement cryogénique pour permettre l'usinage à sec. Ce genre de revêtement nanocomposite est une couche autolubrifiante. Ces outils sont plus performants dans les mêmes conditions de coupe. Les chercheurs ont examiné les forces de coupe, la température survenant à l'arête de coupe, le coefficient de friction, l'usure et la qualité de la surface de la pièce. Afin de prolonger la durée de vie du revêtement, les scientifiques expérimentent un post-traitement cryogénique du revêtement. Un revêtement mince TiAlSiN/TiSiN/TiAlN qui subit un post-traitement cryogénique après application a une durée de vie plus longue. Les tests montrent que cette longévité peut augmenter de 30% à 110%. L'essai a été réalisé en fraisant de l'Inconel 718 à une vitesse de coupe de 30 m/min.

Afin de prolonger la durée de vie du revêtement, les scientifiques expérimentent un post-traitement cryogénique du revêtement
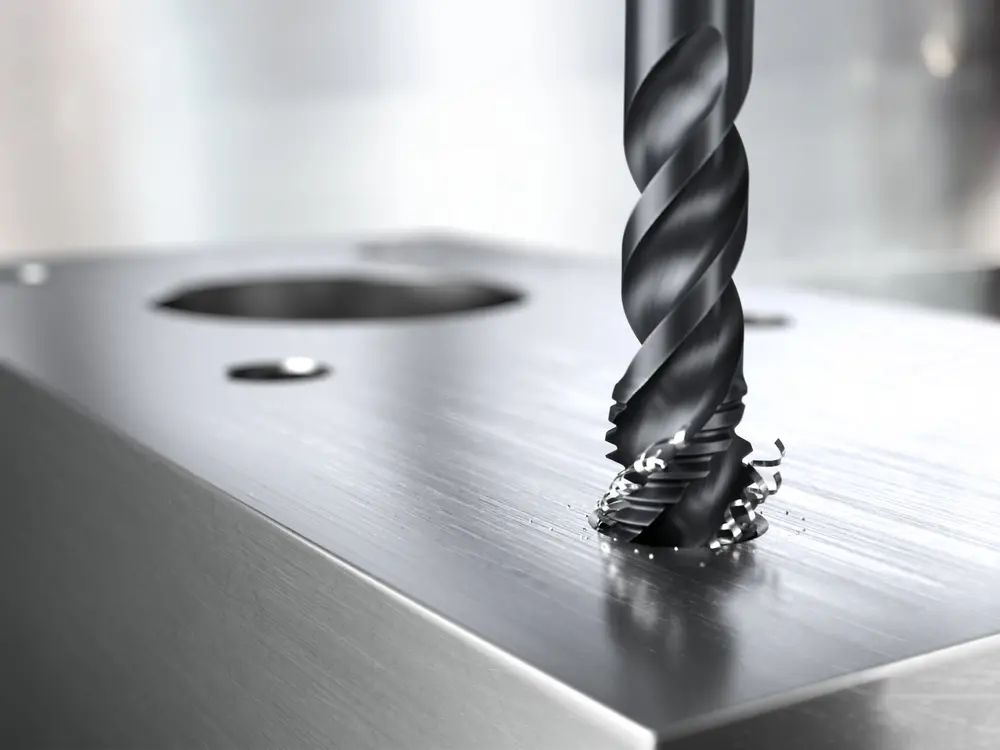
Pourquoi la circularité est nécessaire
Le marché du carbure de tungstène a beaucoup évolué ces dernières années. C'est principalement dû à la forte position de la Chine sur le marché mondial du tungstène, l'élément de base du carbure de tungstène. La Chine possède environ 80% de la production mondiale grâce à ses propres mines. Ce pays a pratiquement la même position dominante sur le marché de l'APT, un produit intermédiaire nécessaire à la production de carbure de tungstène. Les mesures prises en Chine ont donc un impact direct sur les prix. Les réserves sont estimées à 7 millions de tonnes, assez pour durer un siècle, mais ensuite elles s'épuisent. C'est pourquoi presque tous les fabricants d'outils en carbure ont désormais mis en place des programmes de recyclage. Souvent, la première chose qui vient à l'esprit des usineurs est de récupérer les plaquettes usagées pour ces programmes, mais les outils en carbure monobloc sont également recyclés en nouveaux outils. Ils sont décomposés en poudres dans un processus de zinc, ou les broyeurs utilisent un processus chimique pour décomposer les outils usagés en leurs composants atomiques. Les propriétés des nouvelles fraises fabriquées avec ce matériau de base recyclé restent bonnes, elles s'améliorent même à certains égards car les poudres recyclées ont une surface plus petite. La densité lors de la transformation ultérieure en outils est ainsi plus prévisible. Selon le type d'outil, il est possible d'incorporer jusqu'à 40 % de carbure de tungstène recyclé dans un nouvel outil en carbure. Dans ce cas, la circularité peut générer directement de l'argent car certains fabricants paient pour le retour des outils. Mais surtout, les entreprises contribuent à une meilleure empreinte environnementale.
- Sandvik a récemment mis à jour sa gamme de tarauds en carbure monobloc CoroTap pour y inclure le T300. Les outils subissent un nouveau traitement de surface. Cela augmente leur durée de vie de 57%.
- Le recyclage des outils en carbure de tungstène joue un rôle important dans l'ambition de Seco Tools de devenir circulaire à 90% d'ici 2030.
- Kennametal a breveté le relief nervuré de la fraise hémispérique Harvi I TE. Ce relief permet des avances et des vitesses plus élevées tout en réduisant les efforts de coupe et en diminuant les vibrations de l'outil.
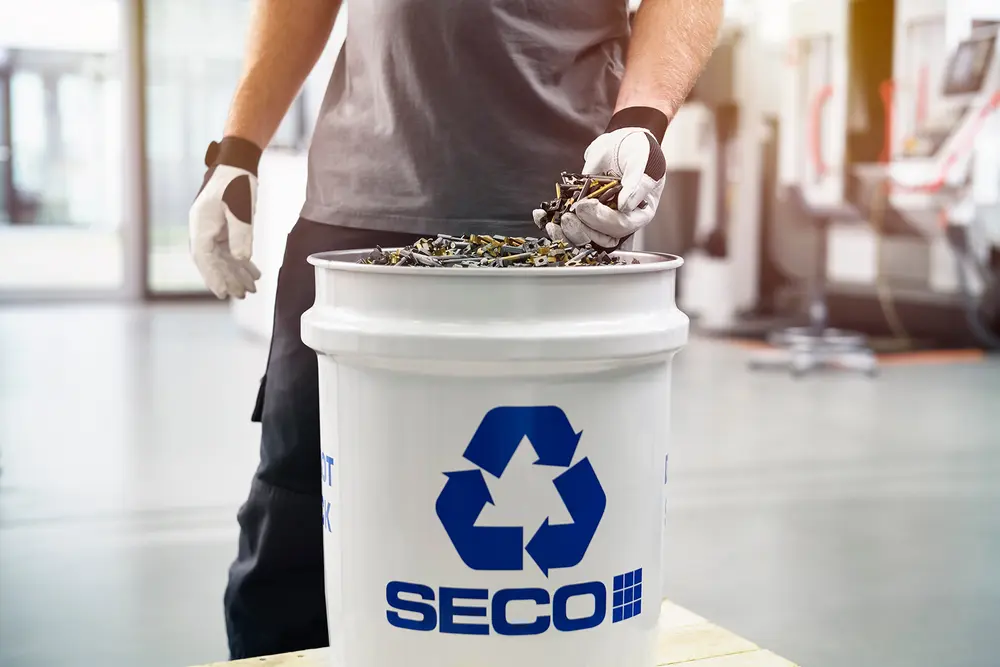
Carbure de tungstène et impression 3D
L'impression 3D a-t-elle déjà fait son entrée dans le monde du carbure de tungstène? Oui. Il y a déjà des fabricants d'outils qui impriment les premiers outils en carbure. Ou alors ils impriment directement en 3D des produits finis dont la dureté est comparable à celle du diamant.
L'impression 3D de métaux en carbure de tungstène n'est pas encore très répandue pour la production en série. Et ce n'est probablement pas près d'arriver. Mais cela ne change rien au fait que l'industrie du carbure de tungstène suit les développements de la fabrication additive avec un intérêt plus que moyen. D'une part, les fabricants d'outils sont à la recherche d'une technologie permettant de fabriquer des prototypes plus rapidement, d'autre part, ils souhaitent réduire les délais de production d'outils spéciaux, souvent spécifiques aux clients, en utilisant l'impression 3D. A cette fin, ils utilisent la technologie EBM (faisceau d'électrons) en plus de la fusion sélective au laser et l'impression par jet de liant est en cours de développement.
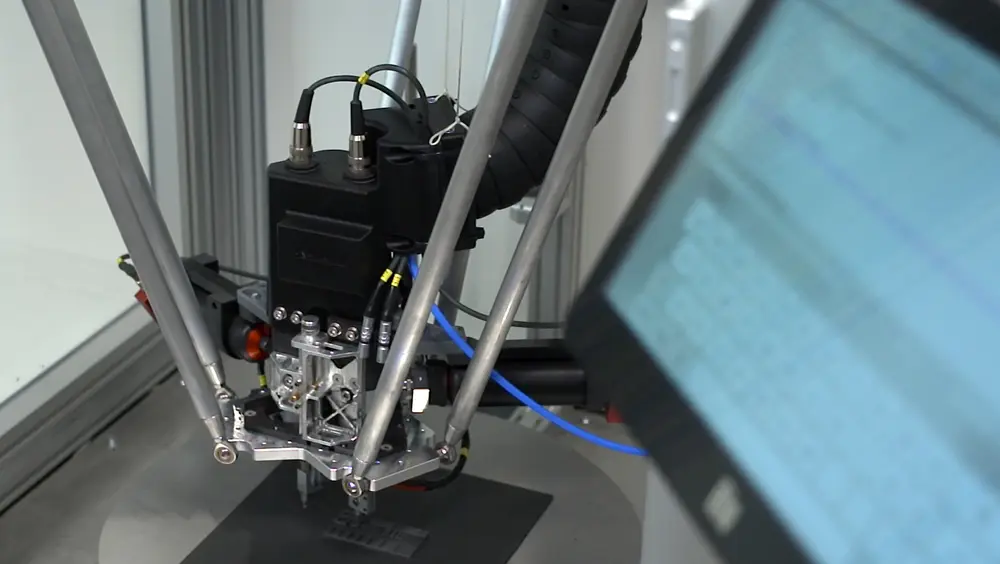
Deux métaux dans un seul produit
Le matériau le plus dur que l'on puisse actuellement imprimer en 3D a une dureté comprise entre 68 et 72 HRC (à une température maximale de 750 °C). Cette dureté est bien supérieure à celle d'un acier à outils standard et rend ces outils populaires pour les opérations où l'usure est extrêmement élevée. Toutefois, l'un des aspects les plus intéressants de cette technique de production est que l'on peut combiner des propriétés spécifiques dans un produit en utilisant deux poudres dans le même outil. Pensez par exemple à une tige en carbure sur laquelle on imprime un matériau plus dur sur la partie coupante. On peut ainsi combiner une dureté extrême à une bonne résistance à l'usure, par exemple. Les carbures étant uniformément répartis dans la poudre, il est possible d'obtenir une structure dure similaire à celle des outils en carbure fritté, comparable à celle du diamant. Le grand avantage reste la liberté de forme qu'offre la fabrication additive. Cela permet de faire passer des canaux de refroidissement à l'intérieur des outils. Dans le cadre de techniques de production conventionnelles, ceux-ci ne peuvent être appliqués qu'après coup et non dans une géométrie optimale, ce qui est possible avec l'impression 3D. Cette liberté de forme est également un avantage car elle permet de développer de nouvelles géométries pour de meilleures performances de coupe ou une durée de vie plus longue des outils. Jusqu'à présent, la liberté de forme est limitée par les techniques de production existantes telles que le pressage et l'extrusion. Toutefois, une dureté extrêmement élevée présente un inconvénient: la finition nécessaire n'est pas facile. La technologie laser constitue la solution la plus évidente à cet égard.
Sans cobalt
Depuis quelque temps, l'armée américaine étudie l'impression 3D avec une poudre de carbure de tungstène sans cobalt. Cela pourrait déboucher sur une plus grande solidité, une plus grande dureté et une meilleure résistance à l'usure. En outre, on n'a plus besoin de cobalt, un matériau qui se fait de plus en plus rare et qui a une lourde empreinte écologique. En 2020, l'armée américaine a fait breveter un nouveau nanomatériau à base de FE qui est utilisé pour la matrice dans les produits en carbure cémenté.