De nouvelles variantes de la machine combinée
De la fabrication additive aux plastiques renforcés de fibres pour l'usinage de la tôle
Parmi les machines combinées pour l'usinage de la tôle, la combinaison du poinçonnage et de la découpe laser est la plus évidente. Ce type de machine allie les avantages des deux techniques. Les constructeurs de machines ne pensent-ils pas à d'autres combinaisons de techniques à intégrer dans une même machine, comme cela se produit de plus en plus avec les machines d'usinage?
Commençons par répondre à la dernière question: oui et non. Certains constructeurs de machines intègrent des technologies spécifiques pour améliorer un processus existant. Un exemple bien connu est le formage à chaud, où les aciers à haute résistance sont chauffés à 200 à 600 degrés dans le moule puis pressés. La chaleur les rend plus faciles à modeler. Dans un certain sens, il s'agit aussi d'une technologie combinée. Ce que l'on connaît moins, c'est la combinaison de l'emboutissage et de la vibration. Si l'on soumet la tôle dans le moule inférieur à des vibrations à une fréquence de 20 Hz, le matériau s'écoule mieux et la tôle peut être formée plus précisément et plus facilement. Les vibrations à basse fréquence réduisent la force de friction, ce qui a un effet visible sur la qualité de la pièce finale. On peut ainsi produire des formes plus profondes et l'opération nécessite moins de puissance.
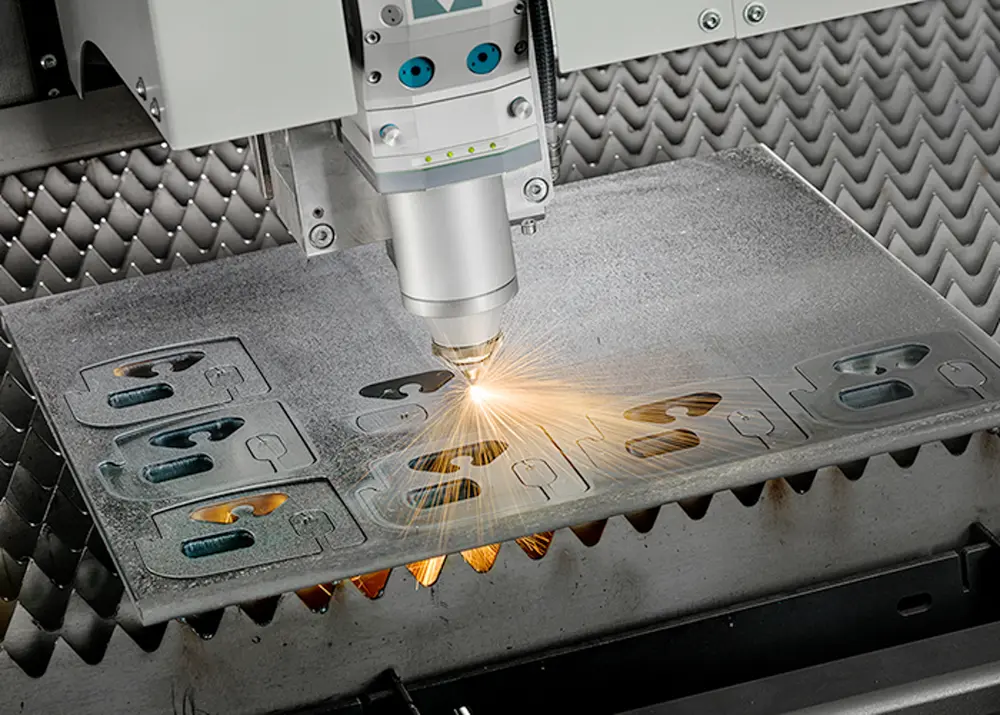
fabrication additive et usinage de la tôle
En général, une machine combinée signifie autre chose: combiner des opérations qui se déroulent généralement sur deux machines autonomes. Selon cette définition des machines combinées, une nouvelle combinaison est en cours de développement: le formage combiné à la fabrication additive. Il existe plusieurs variantes en cours de développement afin de répondre à la demande de constructions plus légères, en particulier dans l'industrie du transport, qui veut réduire le poids pour diminuer les émissions de CO2. Cela fait plusieurs décennies que l'industrie automobile utilise des flans sur mesure depuis des décennies. En fait, ils sont produits par la combinaison sur une même passe de l'emboutissage et du contrôle précis du matériau. Cela crée des épaississements dans le matériau, généralement de 1 à 5 mm d'épaisseur. Ainsi, on ne doit pas utiliser une pièce entière de tôle plus épaisse car à un certain point, on a besoin d'une épaisseur minimale.
La principale restriction des flans sur mesure est que le flux de matière a ses limites. On ne peut pas faire couler un matériau de manière illimitée jusqu'à un certain point de la pièce, la géométrie étant un facteur important à cet égard. Et cette dernière est étroitement liée à la forme de la pièce finale. En outre, il s'agit d'un processus relativement coûteux, en raison des outils spéciaux nécessaires. C'est pourquoi il est principalement utilisé dans l'industrie automobile, où les séries sont importantes et où les coûts d'outillage coûteux peuvent être amortis sur de nombreuses pièces. Des chercheurs de l'université d'Erlangen (Allemagne) sont en train de travailler pour ajouter la fabrication additive en guise de technologie à la production de flans sur mesure.
La principale restriction des flans sur mesure est que le flux de matière a ses limites
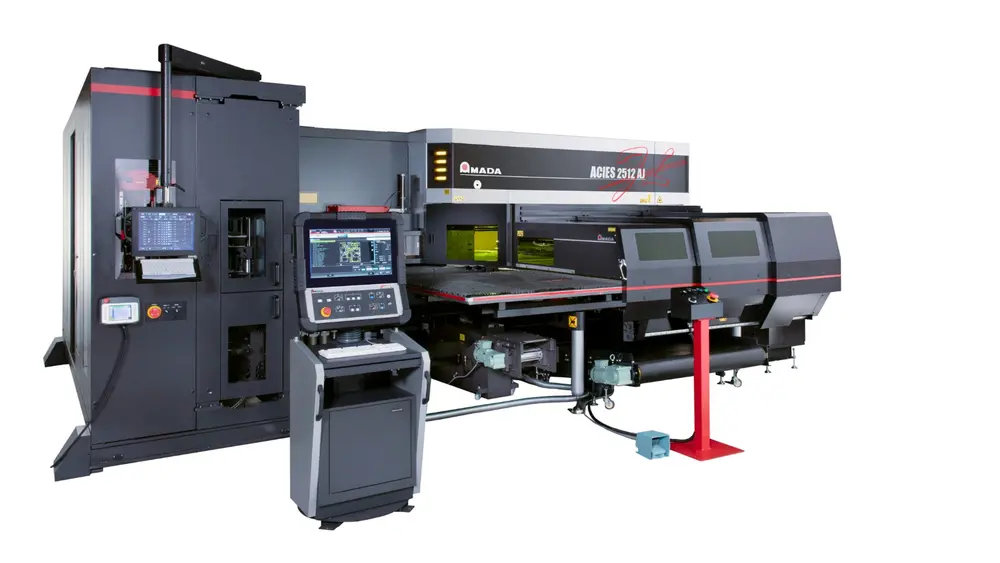
Moins d'outils nécessaires
Cela permet de limiter au maximum l'épaisseur - et donc le poids - des tôles et, le cas échéant, d'appliquer des renforts par fabrication additive (impression 3D). En outre, aucun outil coûteux n'est nécessaire, de sorte que la technologie de combinaison peut également s'appliquer à des séries plus petites.
La technologie de la fusion laser sur lit de poudre est utilisée comme technologie de fabrication additive. Un matériau supplémentaire est appliqué sur la tôle aux endroits nécessitant plus de matière. Les chercheurs allemands utilisent une fine plaque ayant les dimensions de la plateforme de construction de l'imprimante 3D métal. Une fois le matériau supplémentaire appliqué, la forme adéquate est découpée au laser et la pièce est formée comme cela se fait habituellement dans la production de flans sur mesure. Le produit final contient alors beaucoup plus de matière à l'endroit où c'est nécessaire que ce qu'il n'y aurait sans l'ajout de la fabrication additive. La recherche s'est concentrée sur la création d'une denture par emboutissage du matériau. Cette technologie n'est pas encore directement applicable car l'application additive du matériau entraîne des différences de dureté, ce qui augmente le risque de fissures dans le matériau. Néanmoins, les chercheurs sont optimistes et voient des avantages dans cette technologie de combinaison car la forme des dents - ou toute autre géométrie - peut être modifiée facilement dans la mesure où la fabrication additive ne nécessite pas d'autres outils.
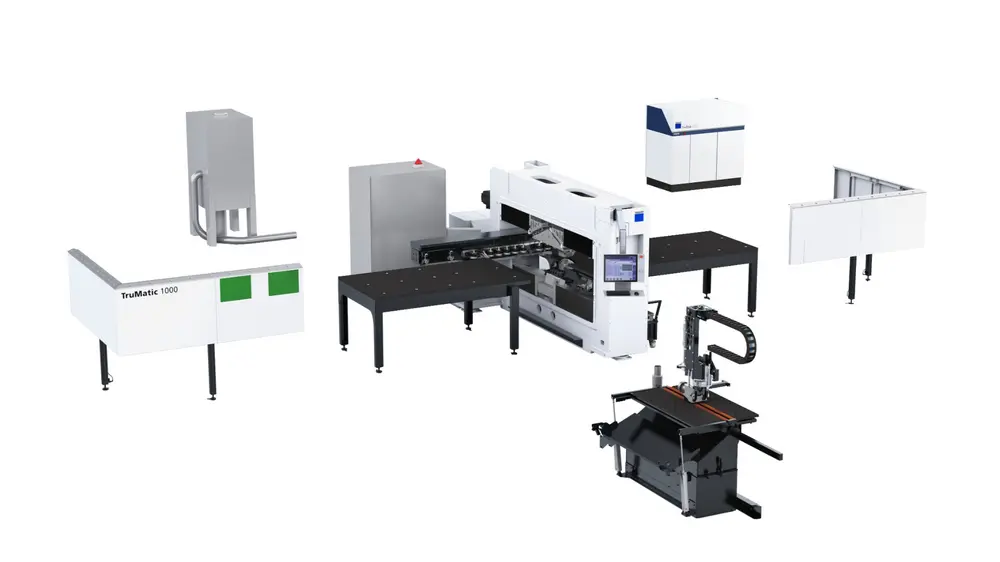
une Bride pour renforcer un trou
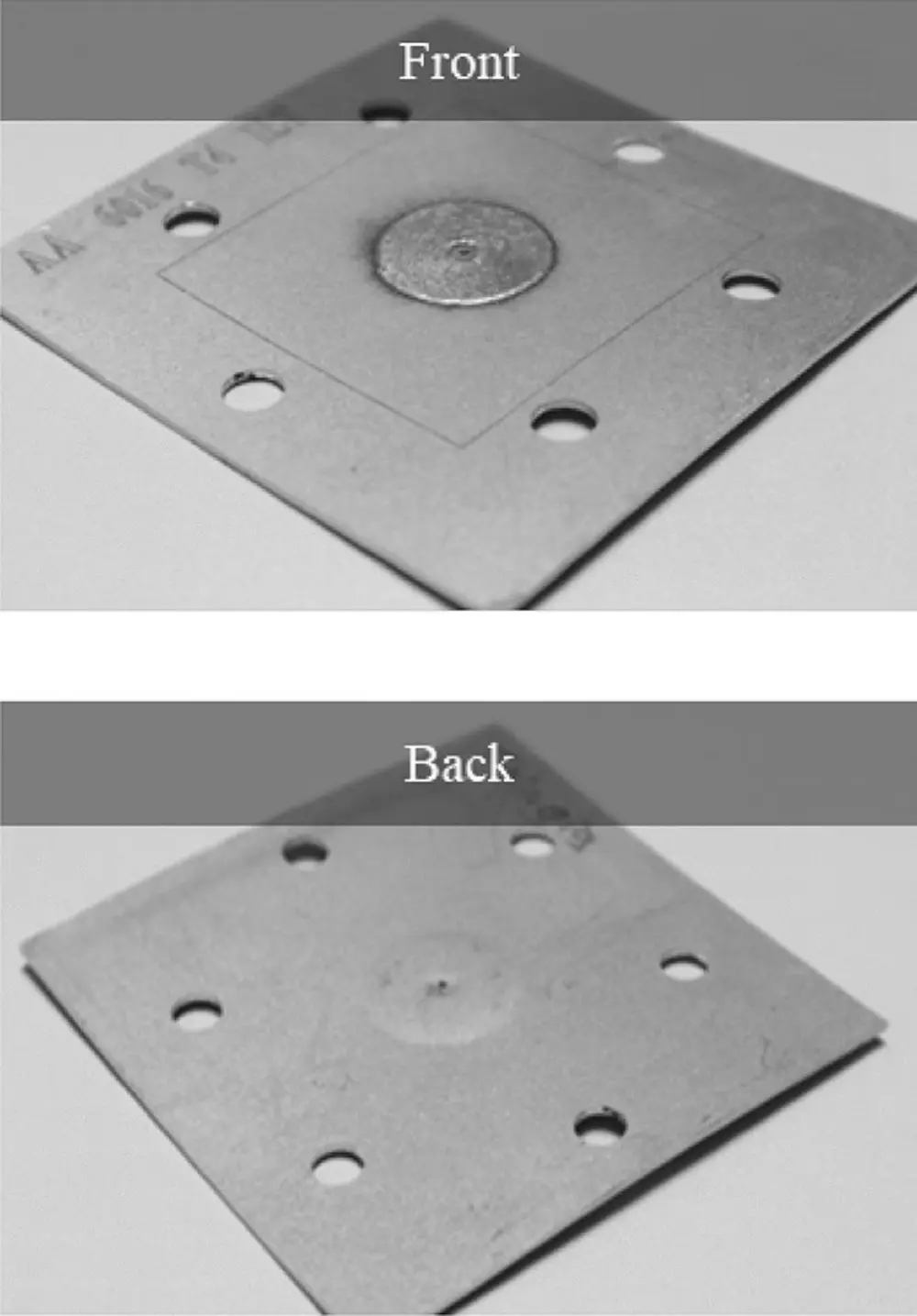
Voici à quoi ressemble la bride appliquée par fabrication additive, telle que testée par des chercheurs de l'ETH Zurich
Les chercheurs allemands ne sont pas les seuls à vouloir combiner la fabrication additive avec l'emboutissage ou une autre technologie de formage de tôles minces. En Suisse, les scientifiques de l'ETH de Zurich étudient comment renforcer par fabrication additive les trous de poinçonnage dans la tôle fine, dans lesquels on presse un élément fonctionnel tel qu'un goujon.
En utilisant la laser metal deposition (LMD), les chercheurs construisent une bride autour d'un trou de 6 mm dans une tôle d'aluminium (6061, un alliage d'aluminium couramment utilisé dans l'industrie automobile). Cela prend relativement peu de temps: en 20 secondes, on obtient une couche de matériau fondue. Dans leur recherche, il s'agit d'un épaississement de 0,3 à 0,4 mm. Ce renfort ne présente aucune porosité et la déformabilité du matériau ne diffère que très peu par rapport à l'aluminium 6061 standard.
L'élément fonctionnel est alors enfoncé. L'ensemble subit un nouveau traitement thermique pour éliminer les tensions du matériau et améliorer sa résistance. Un bouchon à vis 7/16 UNF est enfoncé dans le trou, en adaptant le trou de la bride d'un diamètre de 10 mm et d'une épaisseur de paroi comprise entre 1 et 1,5 mm. Bien que les propriétés mécaniques changent au cours du processus, tout reste dans les marges. Avec une couche de matériau appliquée autour du trou, la résistance au cisaillement s'améliore déjà de 14 %, et après traitement thermique, elle s'améliore même de 196 %. Avec 3 couches (un total d'une minute de temps de cycle supplémentaire), ces pourcentages sont respectivement de 164 et 380%, selon les chercheurs de Zurich.
Renforcer la tôle fine avec des fibres synthétiques
Une autre équipe de scientifiques allemands cherche à innover dans une autre direction: combiner le métal et le plastique en une seule étape de processus. En utilisant le principe MultiForm, les chercheurs ont développé un procédé hybride pour la production de pièces structurelles légères pour des applications de mobilité, entre autres. Le procédé hybride est une combinaison du formage du métal et de l'extrusion de polyamide rempli à 40% de fibres longues. Jusqu'à présent, les composants hybrides de ce type ont été produits en plusieurs étapes: d'abord, la tôle mince est formée dans une presse; ensuite, un revêtement est appliqué pour assurer une meilleure adhérence du plastique, après quoi la partie métallique est revêtue de plastique (in-mold assembly). Alternativement, les deux pièces sont produites séparément puis collées ensemble (post-molding assembly).
Les chercheurs de l'université de Siegen combinent tout dans une seule étape. Pour ce faire, les longues fibres sont placées dans une matrice chauffée à l'état fondu. Une fine tôle, qui est prétraitée avec un revêtement pour renforcer la liaison avec les fibres, est placée entre la retenue et la matrice. Ensuite, le système se ferme et le poinçon presse la plaque et les fibres longues dans le moule. Sous la pression, les fibres de polyamide fondues se répandent dans toute la tôle, créant ainsi une pièce hybride. Celle-ci est découpée à la bonne forme par un découpage au jet d'eau.
L'impact sur le poids est évident lorsqu'on compare les spécifications de matériel d'une poutre longitudinale et transversale pour une voiture. Avec la nouvelle technologie, une tôle d'au moins 2 mm d'épaisseur est suffisante, tandis que sans le renforcement en fibres, on a besoin d'une tôle d'au moins 3,5 mm d'épaisseur pour obtenir les mêmes propriétés mécaniques. Par rapport à un élément en acier, le longeron hybride est 20 % plus léger. Le temps de cycle serait d'environ 25 secondes par longeron, ce qui est suffisamment court pour une production en série, selon les chercheurs.
Par rapport à un élément en acier, le longeron hybride est 20 % plus léger
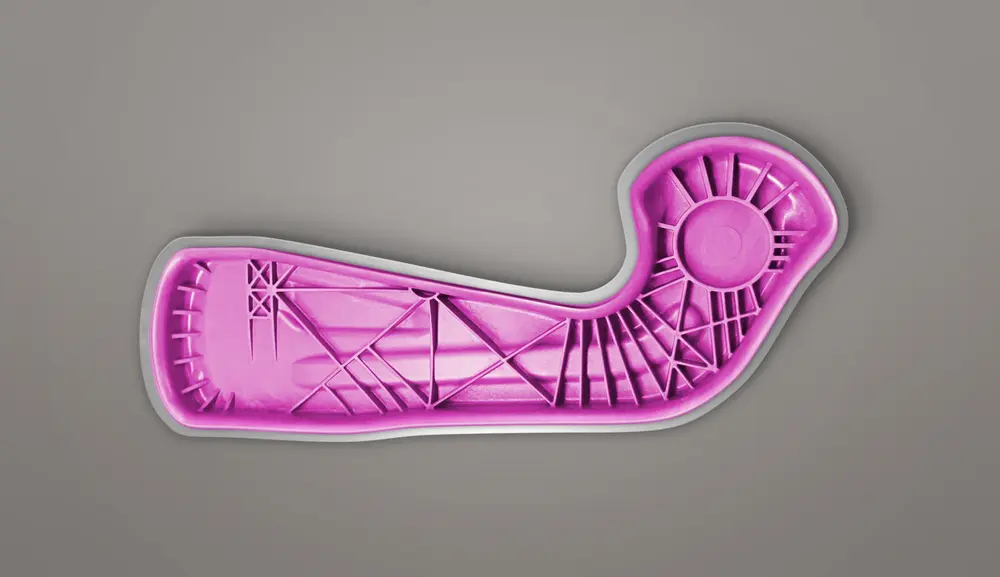
La démonstration de la technologie Multiform de l'université de Siegen. Ce longeron pour roue est constitué d'une tôle mince renforcée de fibres. Pour la combinaison de l'emboutissage et du pressage, les Polyamide 6, 12 et 610 sont remplis à 40% de fibres longues reliées à une fine plaque avec Vestamelt Hylink d'Evonik
Laser à plaque et à tube en un seul appareil
Les trois exemples de machines combinées décrits ci-dessus sont toujours en cours de développement. Le projet Multiform est le plus avancé. La combinaison du laser à tube et à plaque dans une seule machine, disponible sur le marché depuis un an et demi, est plus concrète. Bien qu'elle ne soit pas totalement intégrée, les entreprises qui commencent avec un laser à plaques peuvent ensuite ajouter un module pour la découpe laser de tubes, sans avoir à investir dans une nouvelle source laser. Cela leur permet d'utiliser plus efficacement la coûteuse source laser, bien que, comme pour toute machine combinée, une technologie est à l'arrêt. Cela nécessite de bien calculer les choses.
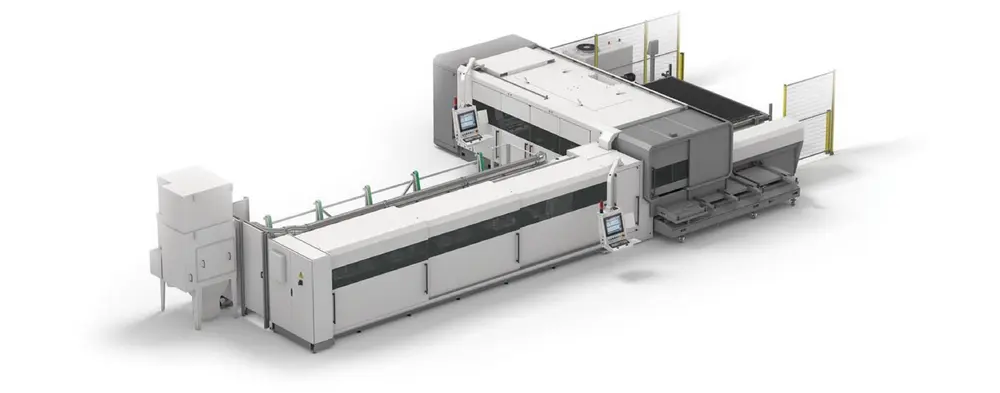
Le groupe BLM offre aux tôliers la possibilité d'intégrer un laser à tube et un laser à plaque dans un seul système avec le LC5. Ainsi, le système peut évoluer avec l'entreprise ou permet d'être flexible dans les commandes à traiter sans avoir à faire d'investissements. Le système est disponible avec un laser à fibre jusqu'à 6 kW