Travailler sans scanner: l'entrepôt du futur
L'innovation bat son plein chez Atlas Copco
Chez Atlas Copco Airpower à Wilrijk, on n'a pas pour habitude de se reposer sur ses lauriers. L'innovation permanente est une véritable stratégie, et elle porte ses fruits. Des gains d'efficacité significatifs ont une fois de plus été réalisés dans l'entrepôt. Grâce à un système doté de toutes sortes de capteurs et de caméras, les chariots élévateurs et les palettes contenant les matériaux nécessaires peuvent être parfaitement tracés sans avoir à être scannés à plusieurs reprises. En outre, l'initiative a encore de beaux jours devant elle: l'avenir pourrait donc être totalement exempt de scanners.
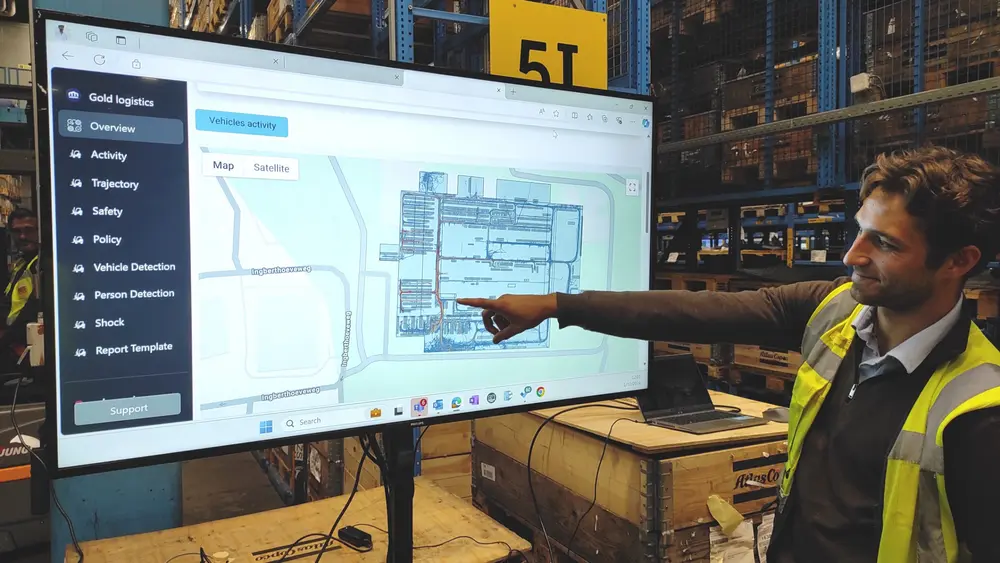
Moins de scans, un travail plus fluide
Rationalisation de l'entrepôt
Nous visitons l'entrepôt d'Atlas Copco Portable Air à Aartselaar, que l'on appelle affectueusement le 'supermarché'. C'est là que se déroule l'un des derniers projets d'innovation du spécialiste des compresseurs: la manutention sans scannage des palettes de pièces destinées à ses lignes de production. Il s'agit donc d'une zone très fréquentée, avec un total de près de 40 véhicules.
Le projet s'inscrit dans le principe de la vision intelligente, qui consiste à analyser et à traiter les images des caméras à l'aide de l'intelligence artificielle. Tous les chariots élévateurs sont équipés de caméras et de capteurs qui surveillent en temps réel la position des véhicules et des palettes transportées. L'objectif est de pouvoir suivre les palettes - et donc les pièces nécessaires - de cette manière, sans avoir à les scanner.
Auparavant, une palette dans l'entrepôt devait être scannée au moins trois fois. De plus, ce scannage consistait souvent en une opération peu ergonomique, qui n'améliorait pas le confort des opérateurs. Le nouveau système permet donc de gagner beaucoup de temps, mais aussi de réduire le risque d'erreur humaine. Tout cela garantit en fin de compte une production plus fluide avec moins de temps d'arrêt.
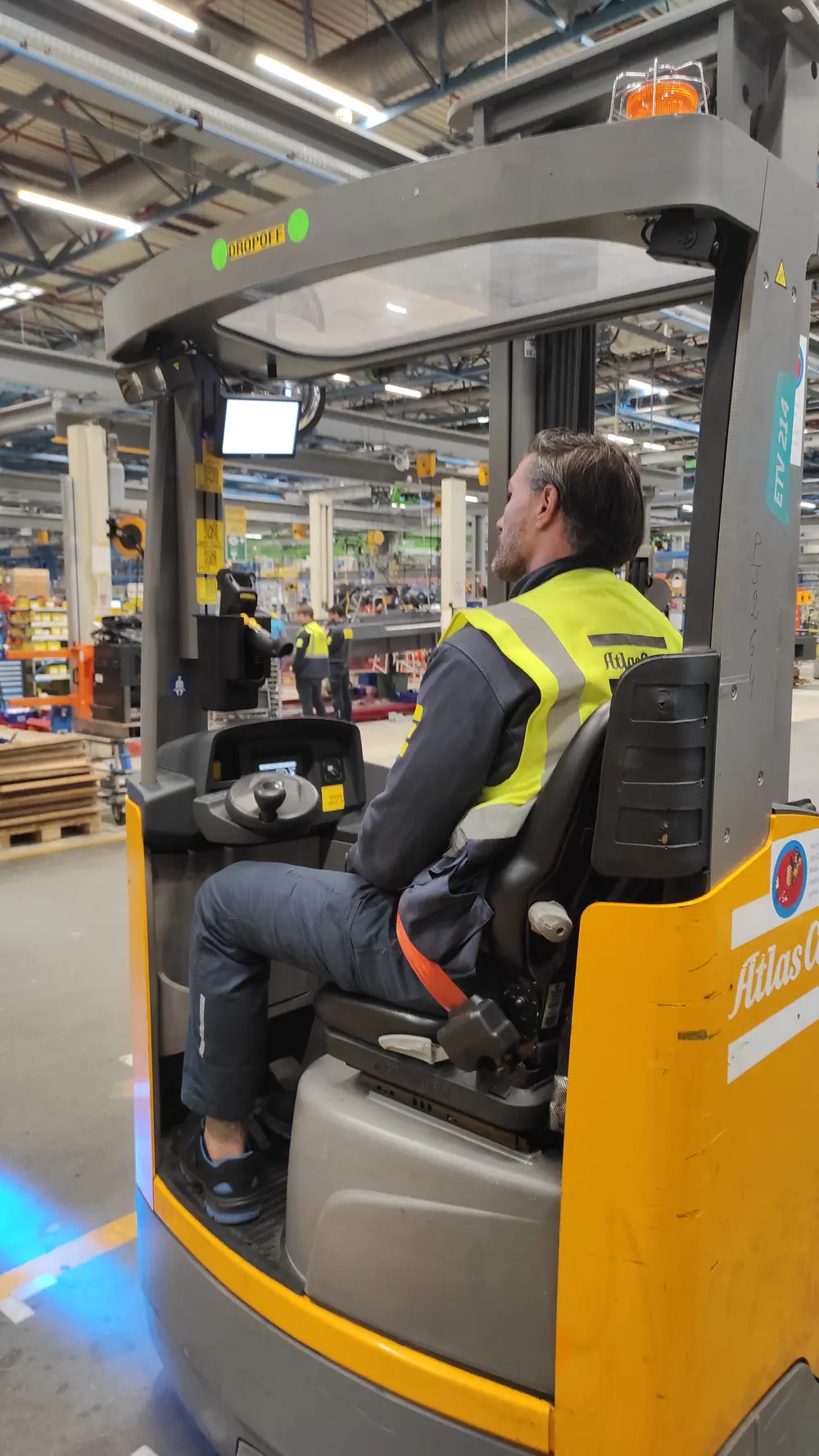
Principe de fonctionnement
Comment tout cela fonctionne-t-il? Une caméra placée sur le toit du chariot élévateur scanne en permanence le toit de l'entrepôt, sachant dans les moindres détails où se trouve le véhicule, grâce à un modèle d'apprentissage profond. En effet, l'ensemble du bâtiment est cartographié grâce à un jumeau numérique, où l'on peut voir les chariots élévateurs se déplacer en temps réel. Cette technologie est beaucoup plus précise que le GPS.
Ensuite, de nombreux capteurs ont été installés sur les chariots élévateurs. "Outre les capteurs qui assurent la sécurité, deux sont particulièrement importants: l'un indique la hauteur des palettes et l'autre permet de savoir si les palettes sont chargées ou non. La caméra située sur le toit fournit les coordonnées x et y, tandis que l'un des capteurs situés sur les palettes surveille l'axe z. De cette manière, le système sait exactement où se trouvent les palettes. De cette manière, le système sait exactement où une palette est placée, sans avoir à scanner le nouvel emplacement pour relier manuellement la palette à sa nouvelle destination", commente Rik Van de Velde, vice-president Operations Portable Air.
Chaque étape du processus - par exemple, le placement d'une palette dans le rack - est enregistrée séparément. À la fin du trajet, ils disposent d'un carnet de bord complet contenant des données sur les itinéraires empruntés et sur la manière dont ils se sont déplacés: à vide ou plein.
Innovation continue
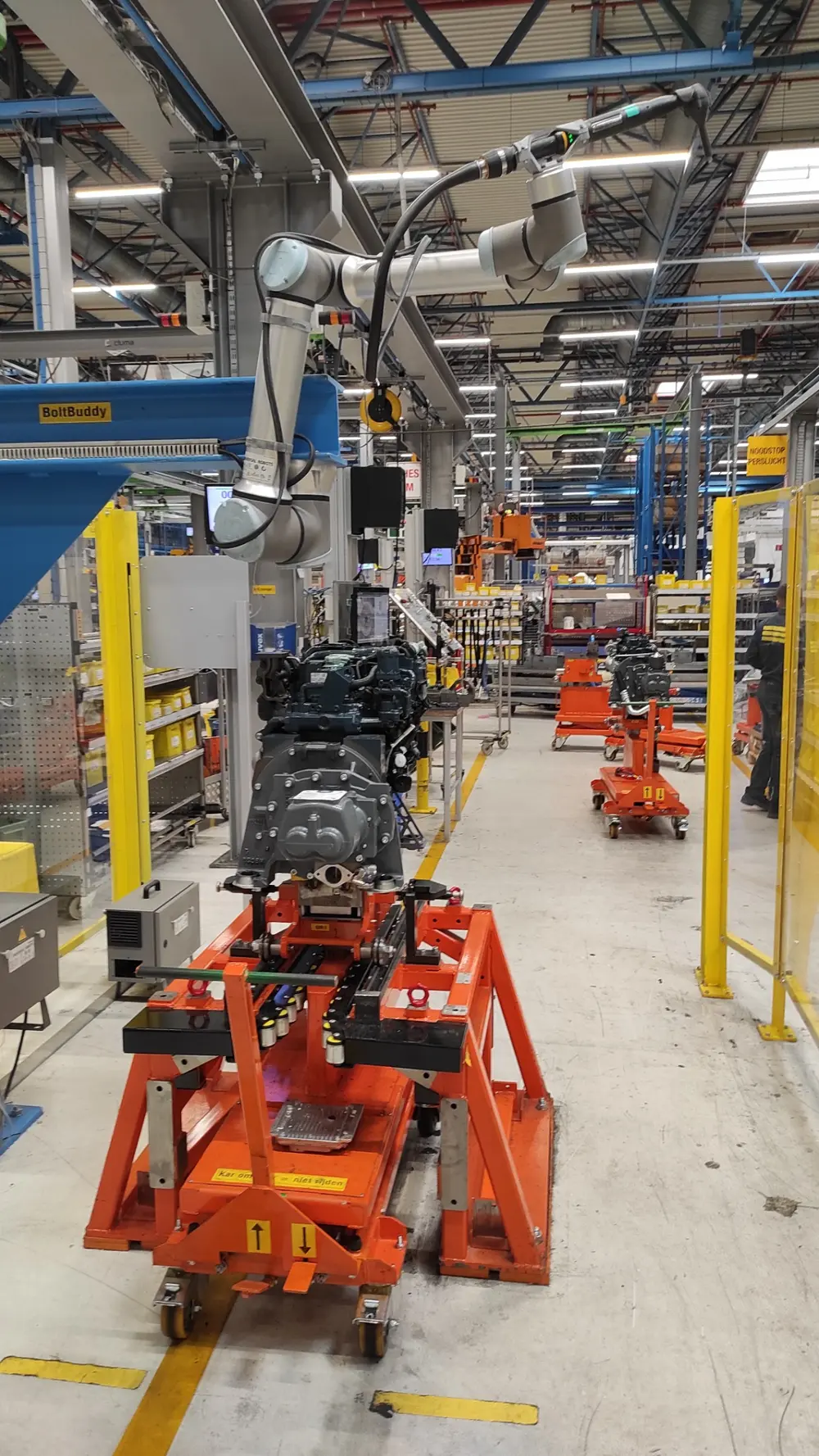
Revenons un peu en arrière. Habituellement, de telles initiatives naissent d'un besoin concret, mais à Aartselaar, c'est un peu différent. "Nous sommes constamment à la recherche de moyens d'améliorer non seulement nos produits, mais aussi nos processus. Par exemple, nous utilisons désormais des caméras dotées d'une IA pour l'inspection de la qualité et nous avons quelques cobots sur les lignes de production. L'innovation est essentielle pour nous et nous sommes donc prêts à essayer de nouvelles technologies, en particulier lorsqu'il s'agit d'efficacité et de durabilité. Atlas Copco Airpower est souvent un site pilote ici, où des projets sont développés puis souvent déployés ailleurs", poursuit Rik.
Le dernier projet en date, qui est en train d'être étendu à tous les véhicules de l'atelier, s'est déroulé en plusieurs étapes. "En 2020, dans le cadre d'un cours de troisième cycle en Smart Logistics, j'ai découvert cette technologie et j'ai immédiatement vu le potentiel de notre application. Après quelques développements, nous avons réalisé une étude de faisabilité en 2022 avec l'aide de deux étudiants. Ils ont fini par rejoindre l'équipe aussi", explique Anja Van Steen, teamleader Supply Chain & Production Logistics.
Bowout Broucke, logistics engineer, était l'un de ces étudiants. "Ma thèse portait sur l'application concrète de la technologie de vision intelligente dans le contexte du suivi des palettes chez Atlas Copco. En effet, les trackers ordinaires et la RFID (identification par radiofréquence) ne se sont pas avérés être la solution appropriée. Pour le projet, nous avions initialement deux piliers en tête: la qualité et l'efficacité. Au fil du temps, l'aspect sécurité s'est ajouté. En enquêtant sur ce sujet, je suis entré organiquement en contact étroit avec Atlas Copco, qui m'a ensuite proposé un emploi.
Le nouveau système permet de gagner beaucoup de temps, mais aussi de réduire le risque d'erreur humaine
Se sentir en sécurité
Malgré le grand nombre de chariots élévateurs, l'entrepôt reste extrêmement sûr. En effet, la moitié de la flotte est équipée de divers capteurs qui aident à signaler les personnes au conducteur. Ils projettent également une lumière bleue sur le sol, qui alerte immédiatement du danger potentiel même les personnes qui fixent un équipement ou une lame. Combiné à une caméra fixe qui transmet des informations supplémentaires sur les piétons et à un système qui ralentit automatiquement le chariot élévateur en cas de collision imminente, l'entrepôt donne l'impression d'être un lieu de travail agréable.
"Notre projet d'innovation a apporté des améliorations significatives en matière de sécurité. C'est un avantage secondaire que nous n'avions pas vraiment à l'esprit au départ", déclare Rik. "Petit à petit, c'est devenu l'un des trois piliers centraux du projet. Nous en sommes assez fiers, car la sécurité reste un aspect fondamental."
Des améliorations concrètes
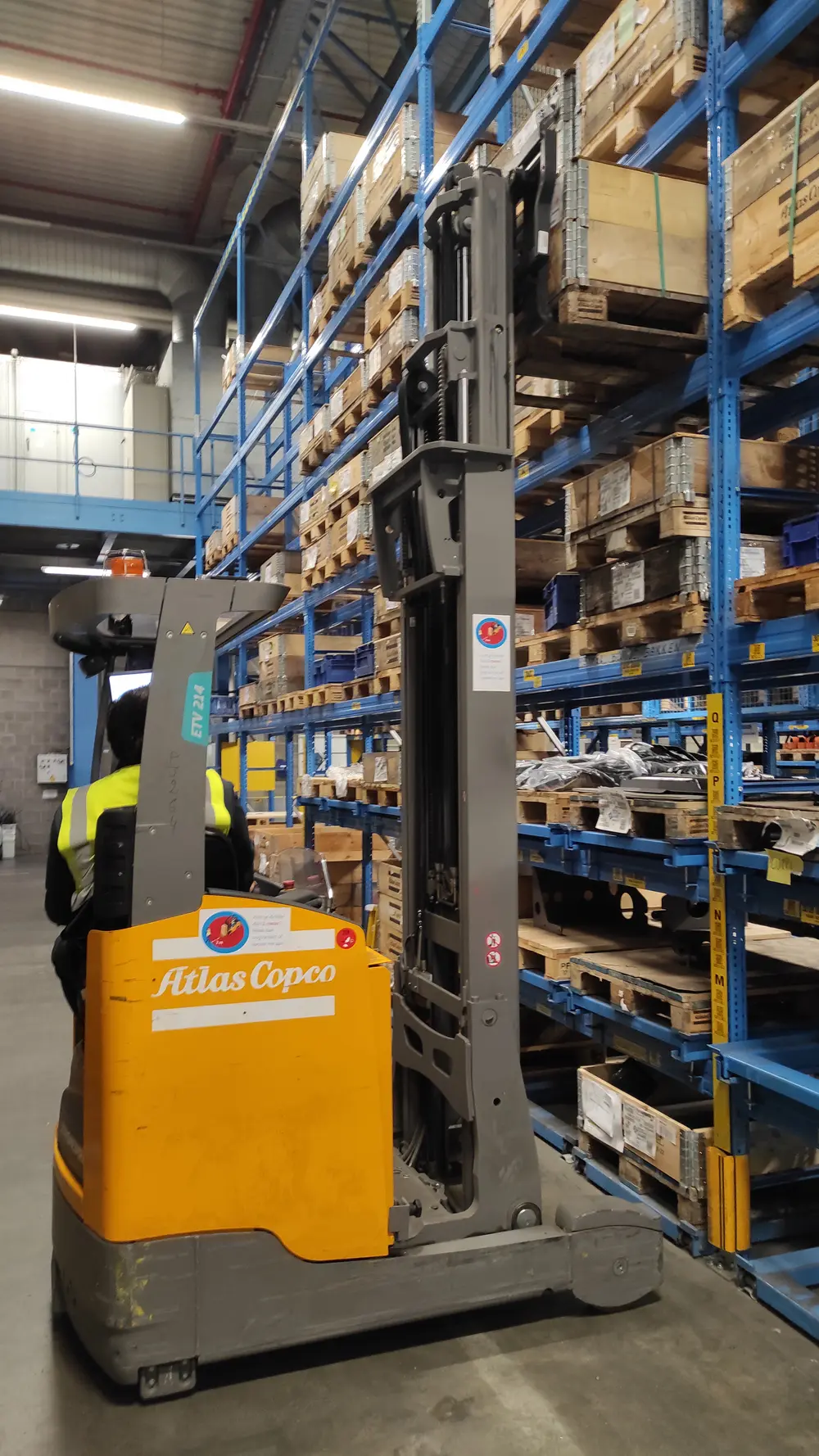
"Le suivi des véhicules offre de nombreux avantages. Il y a l'amélioration de la sécurité, mais la gestion des emplacements est également plus rationnelle et comporte moins d'erreurs. Enfin, la collecte de toutes ces données permet d'optimiser les itinéraires de conduite et les lieux de stockage et, le cas échéant, de réorganiser l'entrepôt. À terme, cela offre de nombreuses possibilités de travailler plus efficacement et plus rapidement", explique Bowout.
Le système a encore un grand potentiel de développement. "La prochaine étape consistera à relier le jumeau numérique et les mouvements des chariots élévateurs au système de gestion de l'entrepôt (WMS), afin d'intégrer les instructions que les conducteurs reçoivent sur le placement des palettes dans l'affichage du système de vision intelligente. De cette manière, nos employés verront non seulement quelle étape ils ont franchie correctement, mais la même interface leur indiquera immédiatement quelle devrait être l'étape suivante. Au cours de ce processus, l'IA fournira également des recommandations. Nous voulons réaliser cette intégration dès l'année prochaine", explique Rik.
À terme, l'objectif est de travailler sans scanner. Actuellement, le scannage doit encore être effectué une fois lorsqu'une palette arrive à la réception. Cela permet à la palette d'être introduite dans le système de l'entrepôt, ce qui permet ensuite de suivre la palette affectée n'importe où. "Il existe des technologies permettant d'éliminer ce premier balayage et de rationaliser encore davantage l'ensemble. Nous sommes en train d'évaluer ces options pour voir ce qui nous convient le mieux. Quoi qu'il en soit, nous sommes bien décidés à continuer à innover et à nous perfectionner", conclut Anja.