Flanders Make montre des technologies pour un travail faisable
Open Atelier à Pelt fait la démonstration de l'industrie 4.0
Pour atteindre un taux d'emploi de 80% et remédier à la pénurie sur le marché du travail, nous devons également maintenir les travailleurs actuels au travail. Les technologies innovantes, telles que les exosquelettes, la réalité augmentée, la réalité virtuelle et les cobots, peuvent jouer un rôle important dans la faisabilité et la préservation des emplois. Le ministre flamand du travail et de l'innovation Jo Brouns a donc lancé le laboratoire "Technologie pour le travail faisable". Les premiers résultats du projet ont été présentés à l'Open Atelier de Pelt le 6 février.
laboratoires
En Flandre, VLAIO dessine la politique de transition autour de l'industrie 4.0, le passage à une industrie manufacturière numérique et connectée. Les laboratoires de l'industrie 4.0 sont l'une des actions visant à aider les entreprises à évoluer vers des processus, des produits et des services plus axés sur les données. Le laboratoire de Pelt a présenté un total de sept technologies, qui devraient contribuer à un travail durable. Ces technologies doivent faciliter le travail existant et ainsi atténuer en partie la pénurie de main-d'œuvre. L'aspect physique n'est pas le seul à être important, il faut aussi savoir gérer la charge mentale.
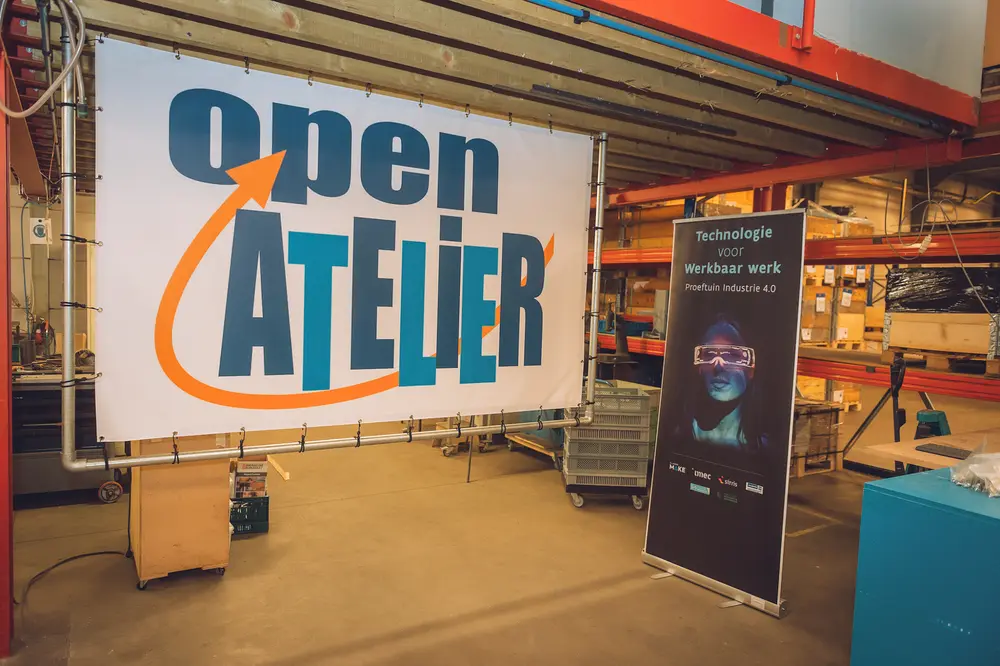
Les principaux obstacles au maintien au travail des travailleurs flamands du secteur industriel sont la charge de travail élevée, les contraintes physiques et la monotonie du travail. Selon les dernières données du moniteur flamand de la faisabilité, un peu moins de la moitié des travailleurs flamands avaient un travail faisable en 2019. L'autre moitié avait un travail qui les confrontait à la fatigue mentale, à des plaintes physiques, à une faible implication dans le travail, à des possibilités d'apprentissage insuffisantes et/ou à un mauvais équilibre entre vie professionnelle et vie privée.
ambition
Au cours de l'année écoulée, 144 entreprises ont déjà participé à des actions du laboratoire. L'ambition du ministre Brouns et des partenaires du projet est d'atteindre environ 800 entreprises avec les technologies et autres actions du projet d'ici la fin de 2024. Le défi consiste à combiner des solutions technologiques, qui visent souvent un goulot d'étranglement spécifique, lorsque cela est nécessaire, et à les intégrer dans l'organisation de manière à ce que les employés soient au centre de l'action et reçoivent le soutien nécessaire pour faire leur travail de manière saine et avec la satisfaction professionnelle requise. 2,4 millions d'euros seront investis sur 3 ans par le biais de VLAIO.
Soutien cognitif aux opérateurs
Un cadre spécial a été développé pour faciliter la génération d'instructions de travail numériques et pour soutenir l'opérateur dans l'exécution de ses tâches grâce à ces instructions de travail en réalité mixte. Une application Hololens2 présente les instructions de manière intelligente et adaptée au contexte à l'opérateur dans l'atelier. L'opérateur est assisté au bon moment par divers indicateurs holographiques (par exemple, pick-to-light et prévisualisation de l'action), ainsi que projeté à l'endroit de l'action dans la cellule de travail physique. Grâce à ce cadre, les opérateurs peuvent effectuer eux-mêmes de nouvelles tâches plus rapidement, avec moins d'erreurs. Ce système peut être appliqué à différents types de tâches, de la préparation de commandes à l'assemblage.
Système de caméra pour les mesures d'ergonomie
Dans le cadre d'un travail essentiellement physique, les employés souffrent souvent de troubles physiques tels que des douleurs articulaires ou musculaires. Cela entraîne souvent une période d'incapacité de travail et donc des coûts considérables pour l'entreprise. Flanders Make a développé un système portable à cet effet, qui permet d'examiner en peu de temps un grand nombre d'employés pendant qu'ils sont au travail. Il est ainsi possible d'effectuer une analyse de chaque employé concerné, ce qui constitue la base d'une conception plus ergonomique de son poste de travail et donc d'un travail faisable dans un environnement confortable. Le système filme le travailleur pendant qu'il effectue son travail. Un écran montre ensuite le travailleur, avec une projection sur le corps des principales lignes du corps. En cas de mauvaise posture d'une partie du corps, la ligne correspondante s'allume en orange ou en rouge. Il s'agit d'un avertissement qui permet au travailleur d'ajuster sa posture à temps, avant qu'une gêne physique ne se produise.
Les capteurs qui soutiennent les opérateurs
Dans un environnement de production, un opérateur doit souvent surveiller plusieurs machines et/ou processus. Chaque processus, chaque machine, chaque dispositif a ses propres spécifications et il n'est pas toujours évident pour un opérateur de savoir ce qu'il doit surveiller. Par exemple, les machines peuvent être équipées de témoins lumineux, utilisant des codes de couleur qui nécessitent une certaine action en fonction du type de machine. Sur d'autres machines, certains signaux sonores peuvent indiquer un problème dangereux. Pour les opérateurs moins expérimentés, cela peut être source de stress ou d'erreurs.
Sirris montre comment toutes ces informations peuvent être rassemblées et visualisées de manière très intuitive et sans ambiguïté dans un système de tableau de bord, qui permet à l'opérateur moins expérimenté de voir très rapidement quel processus ou quelle machine nécessite une certaine action. Ainsi, des processus typiques interprétables peuvent être traduits en actions très claires. L'objectif est de convertir une multitude de signaux divers en actions concrètes, qui tiennent compte de l'urgence des actions à entreprendre.
Apprentissage des séquences d'assemblage dans la RV
La réalité virtuelle a le potentiel pour jouer un rôle important dans l'apprentissage de divers processus d'assemblage. Grâce à une interaction intuitive et à un support virtuel, les personnes en formation apprennent quels composants interviennent dans l'assemblage d'un produit particulier et dans quel ordre ils doivent les assembler. L'objectif est qu'après avoir suivi le processus de formation en RV, les opérateurs soient capables d'assembler le produit physique sans erreur.
Organiser une formation en RV offre aux entreprises des avantages significatifs par rapport à la formation traditionnelle sur le lieu de travail. Premièrement, la formation en RV n'a pas lieu dans l'atelier et la production peut donc se poursuivre normalement, ou démarrer plus rapidement dans le cas d'un nouveau produit. Deuxièmement, les opérateurs peuvent apprendre de nouvelles tâches en toute sécurité dans la RV, ce qui réduit le risque d'accidents du travail s'ils les exécutent ensuite dans l'environnement de production réel. Troisièmement, la formation en RV n'entraîne pas de gaspillage dû à des tentatives ratées de fabriquer un produit correctement, ce qui est le cas avec la formation sur le lieu de travail.
Cobots pour l'assemblage
L'utilisation de cobots dans diverses tâches d'assemblage a pris de l'ampleur ces dernières années. Cette technologie utilise un bras robotique dont la tâche principale est de soulager le travailleur. Ainsi, le robot va tenir les pièces ou la pièce d'assemblage, laissant au travailleur les deux mains libres pour travailler. De cette façon, le travailleur a plus de liberté et évite d'avoir les deux mains occupées, ce qui retarde l'assemblage. Non seulement l'assemblage est pris en charge par un robot, mais un écran d'accompagnement guide également le travailleur tout au long du processus. Ainsi, le processus devient non seulement plus pratique sur le plan physique, mais permet également d'éviter les erreurs d'assemblage.