Les erreurs qui condamnent votre projet d'AGV
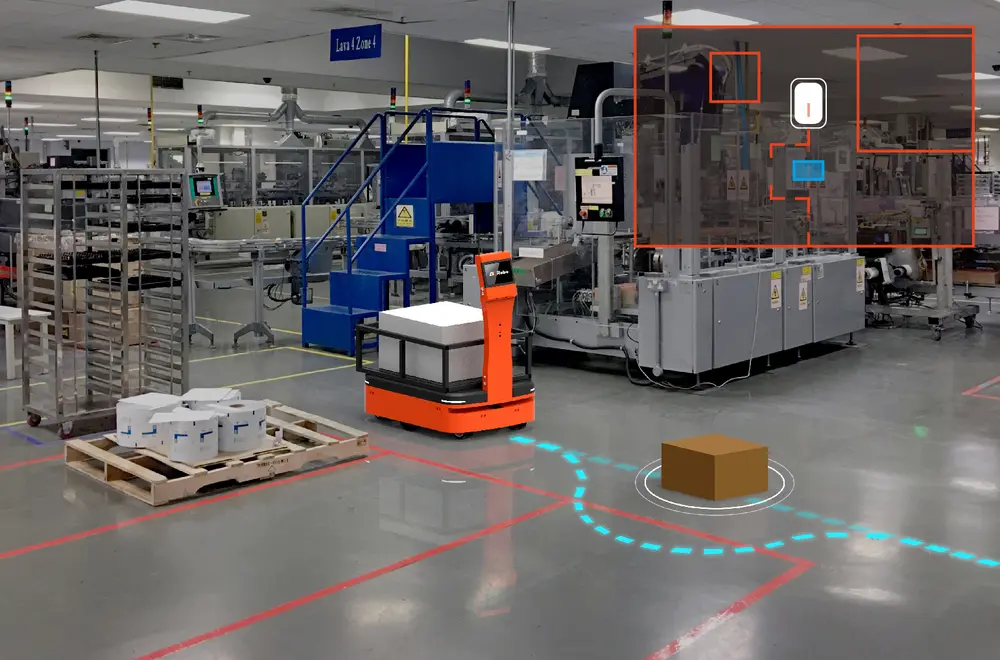
Il suffit de voir un AGV à l'œuvre quelque part dans une entreprise pour se dire qu'on ferait bien la même chose, n'est-ce pas? Malheureusement, tous les projets ne finissent pas en success story. Cela est souvent dû à une approche trop fermée, qui n'envisage pas l'utilisation des AGV dans une perspective plus large. D'autres obstacles sont évidemment à prendre en compte dans ce genre de projet. Nous vous présentons donc les six principales causes d'échec dans le processus de mise en œuvre, complétées par un exemple de la manière dont l'usine du futur Altachem a procédé.
erreur 1: considérer l'AGV comme une machine
En général, le déroulement d'un projet AGV est le suivant: un directeur de production ou un directeur technique voit un AGV sur la route lors d'un salon, dans les médias spécialisés ou dans l'entreprise d'un ami. Il réfléchit à la mise en œuvre dans sa propre entreprise et arrive à la conclusion: nous pouvons le faire aussi. Il en parle à la direction – car un tel projet a un impact majeur sur le budget et la logistique – et après mûre réflexion, la décision est prise: le directeur de production peut poursuivre le projet.
Ce qui nous amène à la première hypothèse erronée. Un AGV – comme beaucoup de nouvelles technologies – n'est pas une machine autonome, mais doit faire partie d'un ensemble plus vaste dans lequel tout est parfaitement coordonné. Le matériel reste évidemment important dans cette approche, mais les logiciels méritent au moins autant d'attention aujourd'hui. Ce qui nous amène sans transition à la prochaine cause d'échec.
erreur 2: continuer à METTRE LES CHOSES DANS DES CASES
La pensée cloisonnée est un obstacle majeur aujourd'hui. Un exemple concret que nous rencontrons tous de temps en temps: le service de maintenance veut donner à un fournisseur de machines ou de systèmes un accès en ligne à l'installation afin, par exemple, de lire à distance les codes d'erreur sur les automates programmables. Le département informatique s'y oppose (parce que la cybersécurité est un problème), la direction s'y oppose (parce que le budget n'est toujours pas là) et la production refuse (parce qu'il n'y a pas le temps d'arrêter les machines pour la conversion).
Ce n'est que lorsque tout le monde regarde dans la même direction et que la nécessité et les avantages de la nouvelle fonctionnalité sont clairs pour tous que des progrès peuvent être réalisés. Il en va de même avec les AGV. Ce qui est d'une logique absolue pour le département A semble souvent une décision absurde pour le département B.
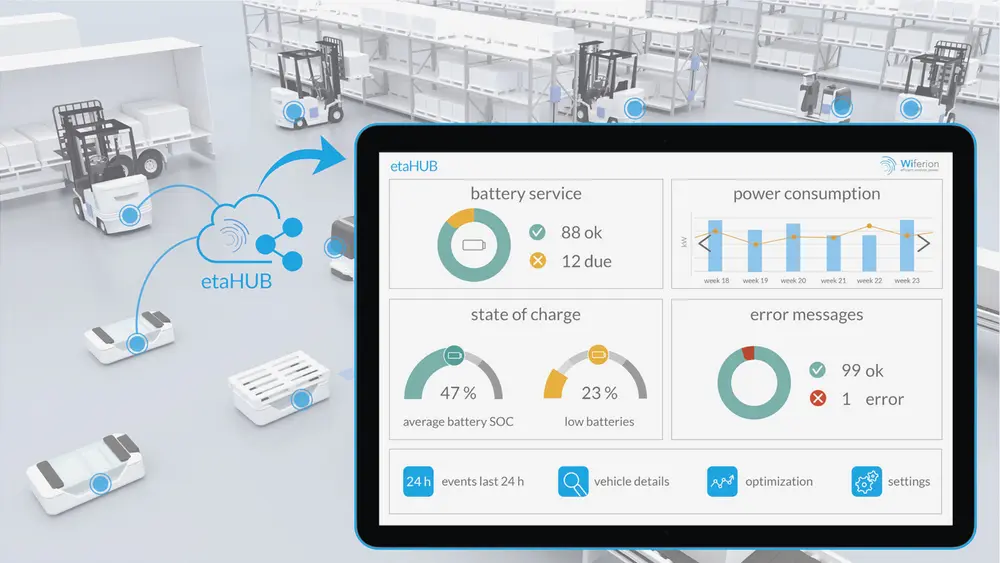
erreur 3: ne pas se préparer du tout
Il n'existe pas un AGV type. Chaque type a des tâches pour lesquelles l'appareil est idéalement adapté, pour d'autres tâches c'est plus difficile. Nous pouvons comparer cela au football: les Diables Rouges jouent mieux avec le fantastique Romelu Lukaku au poste d'attaquant et le prodigieux Thibaut Courtois au but. Avec Lukaku comme gardien et Courtois à l'attaque, nous pourrions gagner quelques matches ici et là, mais il serait déjà beaucoup plus difficile de se qualifier pour un grand tournoi.
"Il est en effet possible de faire dialoguer des AGV de différents fournisseurs"
Il en va de même dans le monde merveilleux des véhicules à guidage automatique. Un projet AGV dans lequel vous ne consultez que vos fournisseurs existants n'est donc pas voué à l'échec a priori, mais c'est de toute façon un gâchis d'appauvrissement. Il existe aujourd'hui tellement de solutions diverses en termes de vitesse, de routage, d'intelligence et de communication qu'il serait dommage de passer à côté d'opportunités. Par exemple, il est effectivement possible de faire dialoguer des AGV de différents fournisseurs, mais nous y reviendrons dans un instant.
erreur 4: des attentes trop élevées
En tant que gestionnaires de production, nous pensons principalement en termes de productivité: si j'achète une machine x, je peux produire x de plus, ou produire x fois plus vite, ou fabriquer de meilleurs produits, ou fabriquer des produits supplémentaires. En soi, ces considérations sont justes, mais un AGV ne les résoudra pas sur le fond. Il s'agit d'un appareil qui transporte (généralement) des produits du point A au point B, ce qui permet d'utiliser le personnel de manière plus efficace, mais encore faut-il que ce dernier soit efficace.
Trop souvent, les entreprises chargées de l'intégration du matériel ou des logiciels sont mises devant le fait accompli parce qu'elles sont intervenues trop tard. Dans l'idéal, vous vous engagez dès le départ avec une partie qui effectue une évaluation initiale complète de votre situation spécifique. C'est la bonne façon de poser les bonnes questions à partir de vos défis et d'exposer les points douloureux à temps.
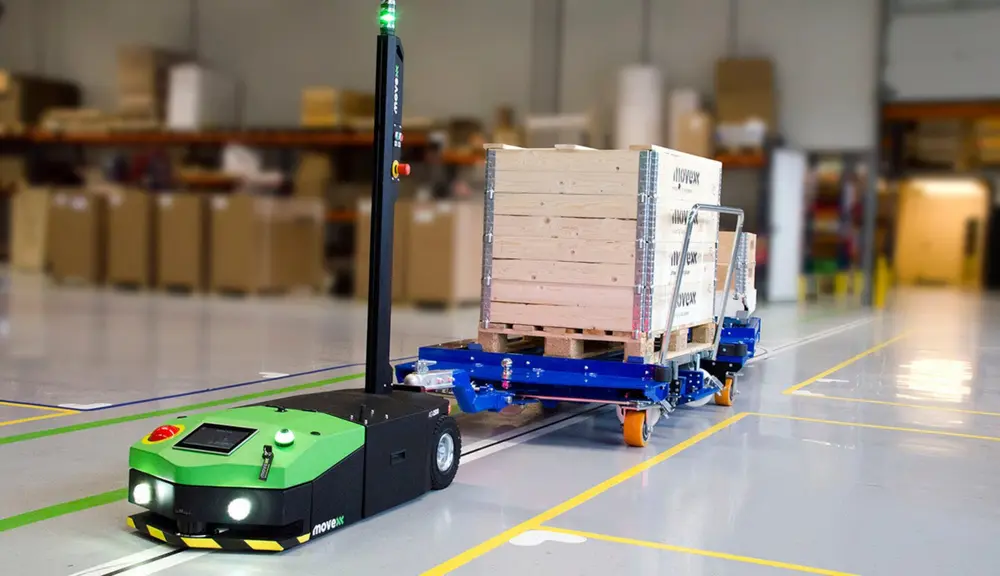
erreur 5: ne pas impliquer les collaborateurs
Bien que les AGV soient de plus en plus monnaie courante dans nos ateliers, leur arrivée suscite encore souvent de la nervosité. Non seulement le flux de travail s'en trouve légèrement modifié, mais des questions se posent souvent quant à la sécurité des personnes travaillant dans le même espace. Une communication claire à ce sujet peut déjà éliminer beaucoup de frustration. Expliquez clairement comment les systèmes de sécurité d'un AGV fonctionnent, comment ils voient leur environnement, comment ils voient les obstacles et comment ils les contournent (ou non).
erreur 6: opter pour des systèmes fermés
Les fabricants ont également du pain sur la planche. Les entreprises qui se sont bien renseignées arrivent parfois à la conclusion qu'il est préférable de déployer des AGV de plusieurs fournisseurs pour différentes tâches. C'est en soi une bonne approche, car ce n'est que de cette manière que chaque AGV peut être utilisé dans sa position la plus forte. Malheureusement, nous constatons que l'industrie de l'AGV a encore du chemin à faire à cet égard. Ces dernières années, l'accent a été mis sur les dispositifs (sécurité, guidage, etc.), mais on a oublié qu'un AGV doit être intégré dans un ensemble plus vaste. Et que leurs clients peuvent vouloir combiner leur AGV avec les AGV d'un ou plusieurs autres fournisseurs.
"Habituellement, un gestionnaire de flotte est utilisé pour contrôler plusieurs dispositifs, mais ceux-ci sont le plus souvent limités aux systèmes d'un seul fabricant"
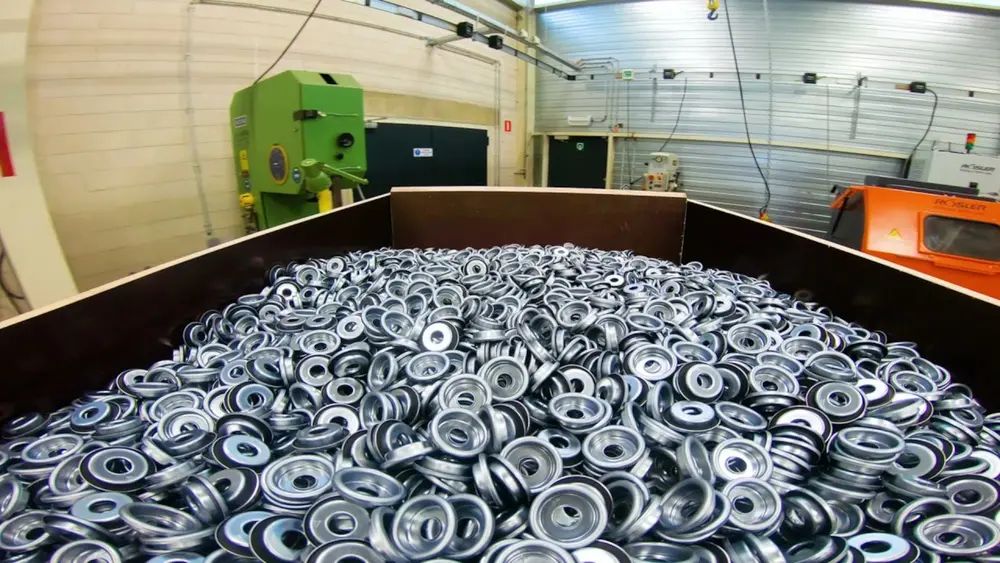
Altachem: une intégration exemplaire dans la chaîne de production
Après avoir évoqué six approches erronées, il convient de se pencher rapidement sur la manière de procéder. Et quelle meilleure façon de le faire que de jeter un coup d'œil à l'intérieur d'une usine du futur? La société Altachem, basée à Harelbeke, est spécialisée dans la production de valves haute pression, de pistolets et de pulvérisateurs professionnels de silicone. L'un des fers de lance de l'usine du futur a été l'utilisation d'AGV.
L'approche de l'entreprise consistait à éviter les déplacements inutiles des opérateurs. Le lien entre les AGV et le processus de production s'est fait par l'intermédiaire des systèmes Karakuri Kaizen. La solution finale consistait en deux types d'AGV. Le premier se déplace par l'intermédiaire d'une construction de tuyaux et de joints sur mesure avec des composants de bacs en vrac. L'AGV peut facilement transporter le bac et décharger le produit par gravité sans manipulation de la part de l'opérateur. L'autre AMR est équipé en haut d'un convoyeur à rouleaux motorisé sur lequel est transporté un paquet de produits, qui peut ainsi être facilement introduit dans une autre partie du processus.
"Il était important ici de rationaliser le contrôle des différentes marques, car elles ont leur propre logiciel et leurs propres interfaces utilisateur pour créer leur carte et leurs itinéraires. Dans ce cas, les deux fabricants ont utilisé le principe SLAM (Simultaneous Localisation And Mapping), selon lequel les appareils créent eux-mêmes leur carte en se déplaçant dans leur nouvel environnement.
Mais il reste ensuite à régler leur communication mutuelle. En général, un gestionnaire de flotte est utilisé pour contrôler plusieurs dispositifs, mais ceux-ci sont généralement limités aux systèmes d'un seul fabricant. Mais qu'en est-il si vous devez contrôler des appareils de plusieurs fabricants?
Nous avons résolu ce problème avec le logiciel de Flagstone, qui peut "parler" à tous les systèmes via des API REST. Il s'agit d'un document public fourni par le fabricant: sur la base de ce document, le logiciel peut obtenir les informations nécessaires pour contrôler l'AMR. Dans cette optique, l'initiative VDA 5050 mérite également d'être mentionnée, car elle vise à normaliser davantage la communication", peut-on lire.
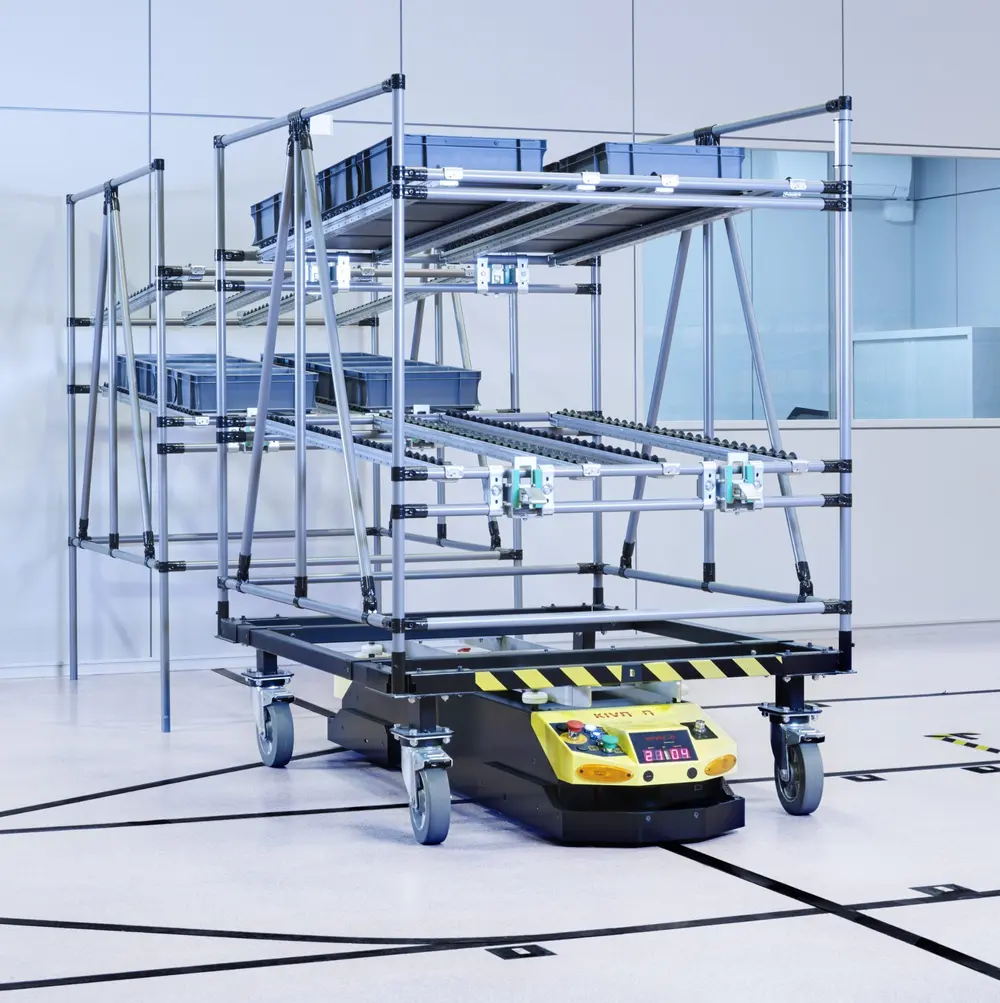
conclusion: importance de l'ergonomie numérique
Les logiciels b2b, contrairement aux logiciels b2c, sont plutôt limités. Comparez, par exemple, l'expérience utilisateur de bol.com avec les systèmes que nous utilisons aujourd'hui dans les ateliers: il y a un monde de différence. Le développement de systèmes tout aussi faciles à utiliser et qui aident les opérateurs dans leurs tâches est donc une priorité pour les développeurs; c'est ce qu'on appelle l'optimisation de la numérisation des ateliers.
L'intégration des AGV dans les processus d'entreprise s'inscrit parfaitement dans cette démarche. L'utilisation des AGV ne doit pas entraîner de frustration dans l'atelier. Supposons qu'un problème survienne avec un AGV. En tant qu'utilisateur, vous voulez savoir immédiatement où il se trouve et quel est le problème. Si vous devez passer des heures à dépanner et à reprogrammer, vous ne verrez bientôt plus que les défauts d'une nouvelle technologie et vous vous sentirez vite nostalgique de l'ancien temps.
Malheureusement, nous constatons aujourd'hui un manque de normalisation. Les fabricants d'AGV ont chacun leur propre système de gestion de flotte qui contrôle leurs appareils. Ce système ne fait pas que déterminer la trajectoire idéale, mais contrôle également les mouvements entre eux pour optimiser le nombre de mouvements et éviter les collisions. En soi, c'est bien, mais le problème est souvent qu'aucune communication n'est possible avec les systèmes de gestion de flotte des autres fournisseurs.
Par conséquent, il peut arriver que les AGV se bloquent lorsqu'ils se croisent, simplement en raison du manque de communication. Vous pouvez choisir de les éloigner les uns des autres en travaillant avec des itinéraires distincts, mais s'imposer une telle restriction dénature tout l'avantage de cette technologie. Il y a également du travail à faire en matière de communication avec d'autres composants du système.