Soudage de profilés tubulaires Dual Phase
Dans le cadre du projet Steel S4 EV, on développe des véhicules électriques légers pour le trafic urbain, conformes à toutes les réglementations en matière de résistance aux chocs et autres exigences Euro NCAP (European New Car Assessment Program). Le châssis est conçu intelligemment grâce à l’utilisation de tubes pliés et découpés au laser soudés entre eux. On veut utiliser ici de l’acier haute résistance. Le but est de développer, en utilisant des aciers haute résistance avancés, un châssis très léger mais extrêmement robuste et rigide. On travaille dès lors avec des aciers Dual Phase (DP). Il s’agit de matériaux novateurs, l'acier tirant ses propriétés d’une structure unique composée de deux phases (matrice ferritique avec îlots martensitiques).
objectif de la recherche
L'Institut Belge de la Soudure étudie la soudage des matériaux du projet. Les aciers DP peuvent être soudés mais souvent, le soudage élimine leur microstructure. Dans ce projet, on a cherché les paramètres de soudage optimaux permettant d'obtenir une qualité de soudure acceptable sans trop affecter les propriétés mécaniques.
Les aspects suivants ont été examinés:
- influence du cycle de soudage sur l'attendrissement dans la zone affectée thermiquement (ZAT)
- influence du matériau d'apport
- influence du refroidissement forcé après le soudage
On a cherché les paramètres de soudage optimaux permettant d'obtenir une qualité de soudure acceptable
dispositif d'essai
Dans cette recherche, on a testé des profilés carrés creux soudés longitudinalement avec des dimensions de 40x40x1.3 mm dans les qualités DP800 et DP1000. Avec la qualité DP800, on a également réalisé des essais de soudage sur des profilés tubulaires de 40x40x2mm. Les profilés ont été soudés aussi bien bout à bout (soudure bout à bout) qu'avec un assemblage en T (flare bevel et soudure d'angle). Les deux dispositifs ont été soudés aussi bien avec un robot que manuellement avec le procédé 135 (soudage MAG à fil plein). On a utilisé un matériau d'apport à haute résistance, respectivement EN ISO 16834-A : G 69 4 M Mn3Ni1CrMo - Ø0.8mm pour le DP800 et EN ISO 16834-A : G89 4 Mn4Ni2CrMo - Ø1.0mm pour le DP1000. La figure 1 montre la configuration des tubes pour les assemblages bout à bout et les assemblages d'angle.
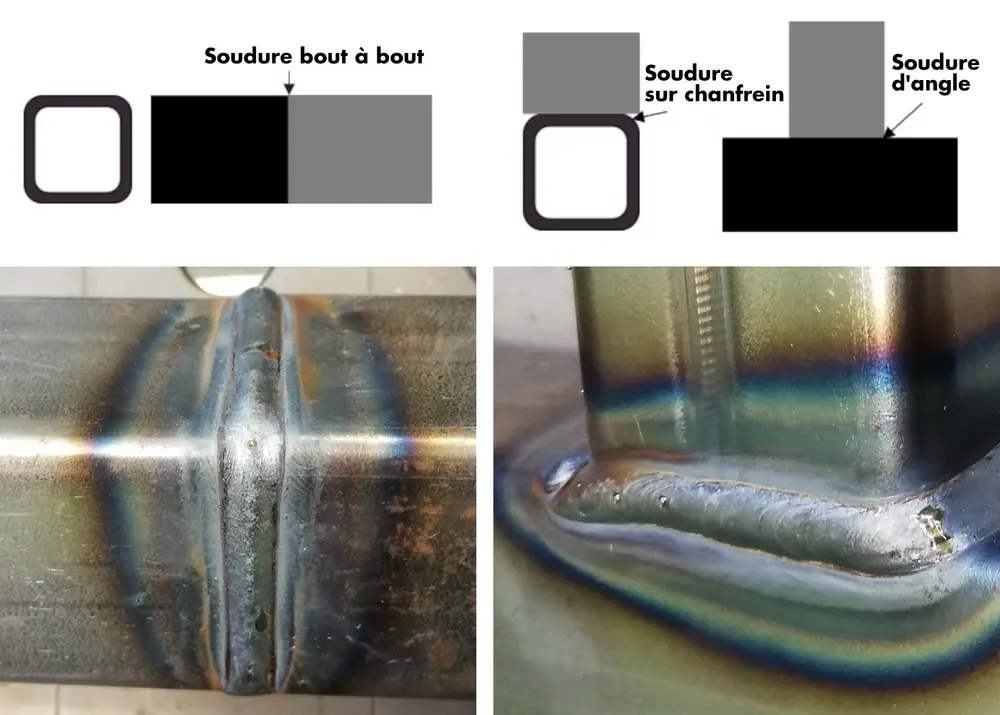
InFLUENCE DU CYCLE DE SOUDAGE
Lors de l'étude des paramètres de soudage appropriés (fenêtre de soudage), on a pu établir deux limites: une limite supérieure avec un apport de chaleur élevé où l'on a constaté un perçage, et une limite inférieure avec un apport de chaleur faible où l'on a constaté des défauts de liaison (voir la figure 2).
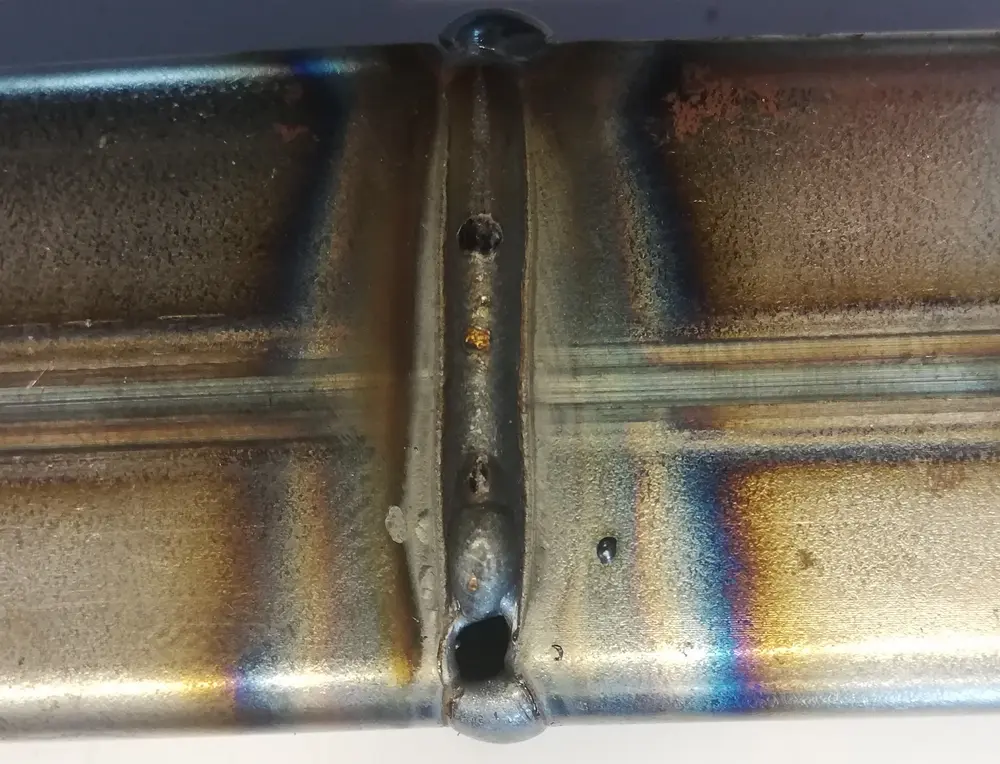
Figure 2: Défauts de liaison (au-dessus), perçage (en dessous)
Ces limites et, par conséquent, les imperfections qui en résultent, étaient à leur tour fortement influencées par les tolérances dimensionnelles de la section des tubes. Dans la plupart des cas, cela s'est traduit par une erreur d'alignement (haut-bas) d'au moins 2 surfaces de tube avec les assemblages bout à bout et d'1 surface (flare bevel) avec les assemblages d'angle (figure 3). En outre, ces erreurs d'alignement ont également entraîné une différence dans la section à souder. Conséquence: des paramètres de soudage acceptables ont soudain entraîné un perçage. Ce problème s'est surtout manifesté lors des essais de soudage effectués avec le robot, alors qu'en soudage manuel, le soudeur pouvait encore ajuster quelque peu les paramètres de soudage. Cela ne favorise pas la reproductibilité de la fenêtre de soudure trouvée.
Figure 3: Défaut d'alignement (haut-bas) avec un assemblage bout à bout (à gauche) et avec un assemblage d'angle (à droite)
DIFFérentes zones
L'examen métallographique combiné à l'essai de microdureté Vickers (HV1) a montré que la zone affectée thermiquement (ZAT) des assemblages soudés est constituée de plusieurs zones différentes, où les phases et les tailles de grain varient. Le matériau de base du DP est constitué de ferrite avec des îlots de martensite. Plus la qualité du DP est élevée, plus la fraction volumique des îlots de martensite est importante. Dans la partie de la ZAT immédiatement adjacente au matériau de base, la microstructure se compose également de ferrite et de martensite, mais la structure est ici beaucoup plus fine et la martensite est trempée. L'essai de microdureté montre que la dureté dans la ZAT fine juste à côté du matériau de base diminue à un minimum. Ce minimum est toujours de 190 à 200 HV, quelle que soit la qualité du DP (DP800 ou DP1000), quel que soit l'apport de chaleur appliqué et quelle que soit l'épaisseur de la paroi du tube (1,3 ou 2 mm). La dureté du matériau de base DP800 et DP1000 est respectivement de 270-280 HV et de 350-360 HV; l'attendrissement qui se produit dans la ZAT est donc important. La figure 4 montre les évolutions de dureté pour les assemblages bout à bout de DP800 (épaisseur de paroi 1,3 et 2 mm) et de DP1000, soudés avec le robot et manuellement.
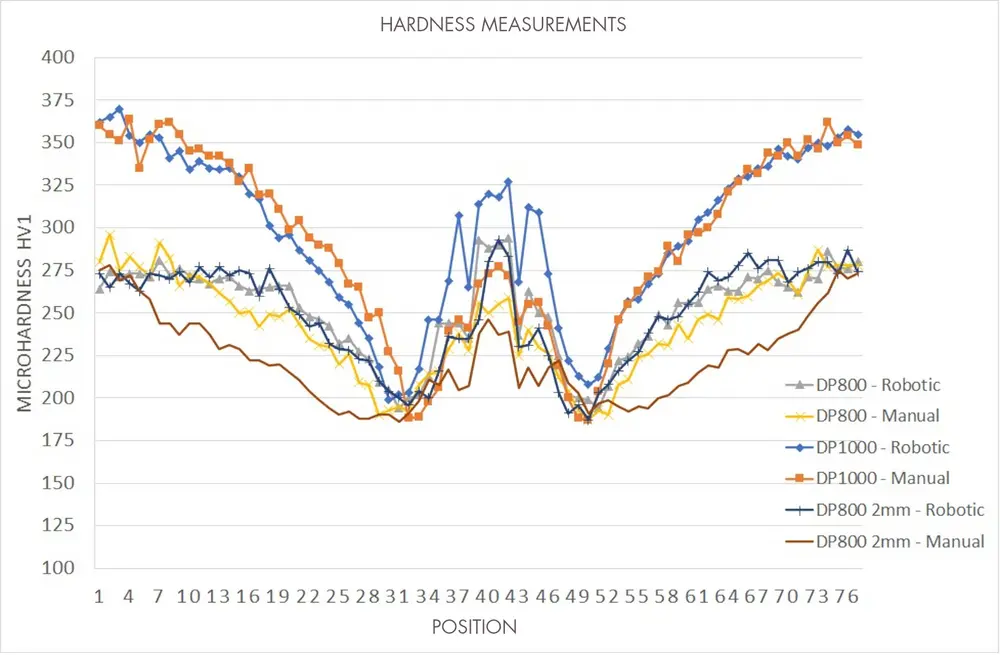
caractériser la résistance de la soudure
Pour caractériser la résistance de la soudure, des essais de traction transversale ont été réalisés sur la soudure conformément à la norme EN ISO 4136. Pour cela, on a traité des éprouvettes plates sur les 3 côtés des tubes soudés (le côté avec la soudure la plus longue n'a pas été testé). Il s'est avéré que la résistance à la traction des assemblages soudés était considérablement inférieure à celle des matériaux de base (de l'ordre de 700 MPa). L'examen métallographique a montré que la rupture se produit toujours dans la zone molle de la ZAT, comme décrit ci-dessus. Du côté non défaillant, on a même pu souvent constater dans cette zone un rétrécissement (voir figure 5). Avec le DP800, on a observé une réduction de la résistance à la traction entre 18% (échantillons soudés par robot) et 24% (échantillons soudés manuellement) par rapport à la résistance à la traction du matériau de base. Avec le DP1000, on a même observé une réduction d'environ 38% pour les échantillons soudés par le robot et ceux soudés manuellement.
Figure 5: Rupture dans la ZAT molle – rétrécissement dans la ZAT molle du côté non défaillant
Des essais de traction en grandeur réelle ont également été réalisés sur les tubes (voir figure 6), qui ont été soudés avec le robot (DP800 40×40×1,3 mm). La résistance moyenne à la traction obtenue pour les assemblages (696 MPa) est du même ordre de grandeur que la résistance moyenne à la traction déterminée via des éprouvettes plates normalisées (715 MPa).
Influence du matériau d'apport
Les essais de soudage ont été réalisés de manière standard avec des matériaux d'apport à haute résistance, comme décrit ci-dessus. Cependant, comme il est apparu que les essais de traction échouaient toujours dans la partie molle de la ZAT avec des résistances à la traction inférieures à celles du matériau de base, on a mis en place une expérience utilisant un matériau d'apport faiblement allié avec une résistance plus faible (voir tableau 1).
Tableau 1: Aperçu des matériaux d'apport utilisés pour examiner l'influence du métal de soudage sur la résistance à la traction
Pour cette expérience, on a utilisé des tubes DP1000 de 40×40×1,3 mm et les échantillons ont été soudés manuellement. L'apport de chaleur pendant le soudage avec les deux matériaux d'apport a été maintenu constant autant que possible afin de réduire son influence potentielle sur les résultats des essais de traction. Les essais de soudage ont montré que, quel que soit le fil à souder utilisé, la résistance à la traction de l'assemblage soudé reste la même. Dans tous les cas, les échantillons se sont rompus dans la zone molle de la ZAT.
INFLUENCE DU REFROIDISSEMENT FORCé
Des expériences antérieures ont montré que la résistance à la traction des assemblages soudés est affectée de manière négative par la zone de la ZAT. Par conséquent, un certain nombre d'essais de soudage avec le robot ont été mis en place pour étudier si cet attendrissement peut être réduit afin d'améliorer la résistance à la traction. Ces essais ont été réalisés avec des tubes en DP800 de 40×40×1,3 mm. Afin d'évaluer l'évolution de la température dans la zone molle de la ZAT, on a déterminé la localisation de cette partie par rapport à la ligne de fusion au moyen de coupes métallographiques. Un thermocouple a ensuite été appliqué à cet endroit lors de l'avant-dernière (soudure #3) et la dernière (soudure #4) séquence de soudage (voir figure 7).
Dans un premier temps, on a étudié l'impact sur la dureté et la résistance à la traction lorsque le tube soudé est immergé (trempé) dans de l'eau à température ambiante immédiatement après le soudage (quenching).
La figure 8 montre la progression de la température pendant et après le soudage, la courbe bleue représentant la mesure de la température lors de la séquence de soudage #3 et la courbe rouge représentant mesure de la température lors de la soudure #4. Le moment de la trempe peut être identifié car les courbes chutent brusquement à cet endroit. Comme on le voit sur la figure 8, cela se produit sur la courbe bleue à une température plus basse (soudure #; ± 450°C) par rapport à la courbe rouge (soudure #4 ; ±600°C). Cela peut s'expliquer par le fait que lors de l'exécution de la séquence de soudage #4, une partie de la chaleur de soudage de la zone de soudage de la séquence #3 était déjà dissipée.
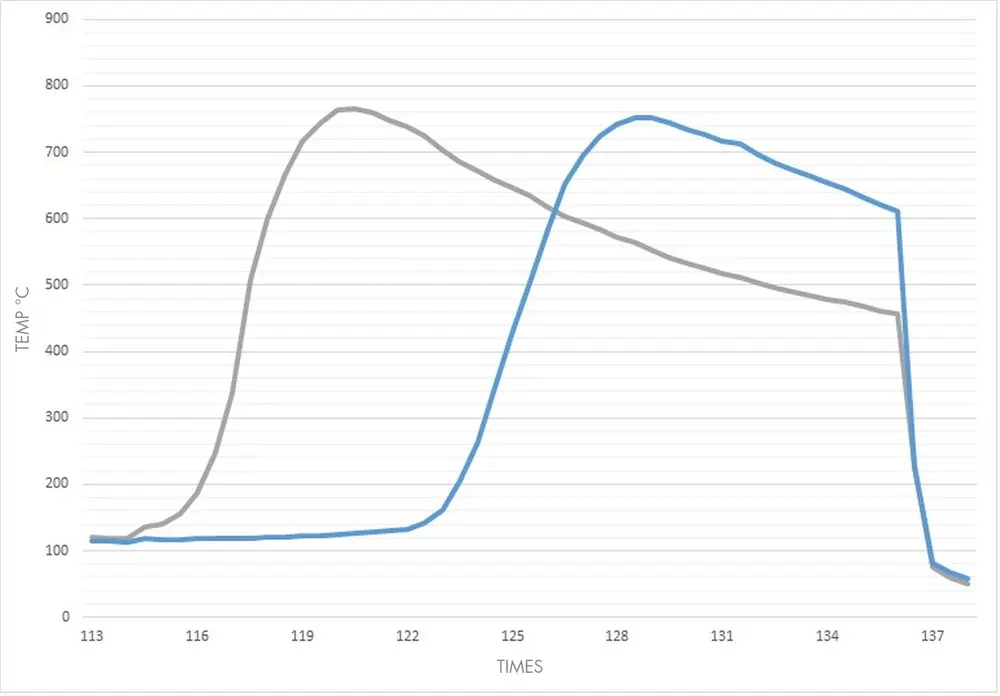
Figure 8: Evolution de la température lors de la trempe dans l'eau; soudure #3 (courbe grise) et soudure #4 (courbe bleue)
Ensuite, on a réalisé un essai dans lequel on a tenté d'évacuer la chaleur pendant le cycle de soudage en fixant un bloc de cuivre fabriqué sur mesure sur les profilés tubulaires. Ce bloc de cuivre a été fixé aussi près que possible de la zone de soudage sans gêner la torche (figure 9). Les essais de soudage ont été réalisés avec un soudage robotisé.
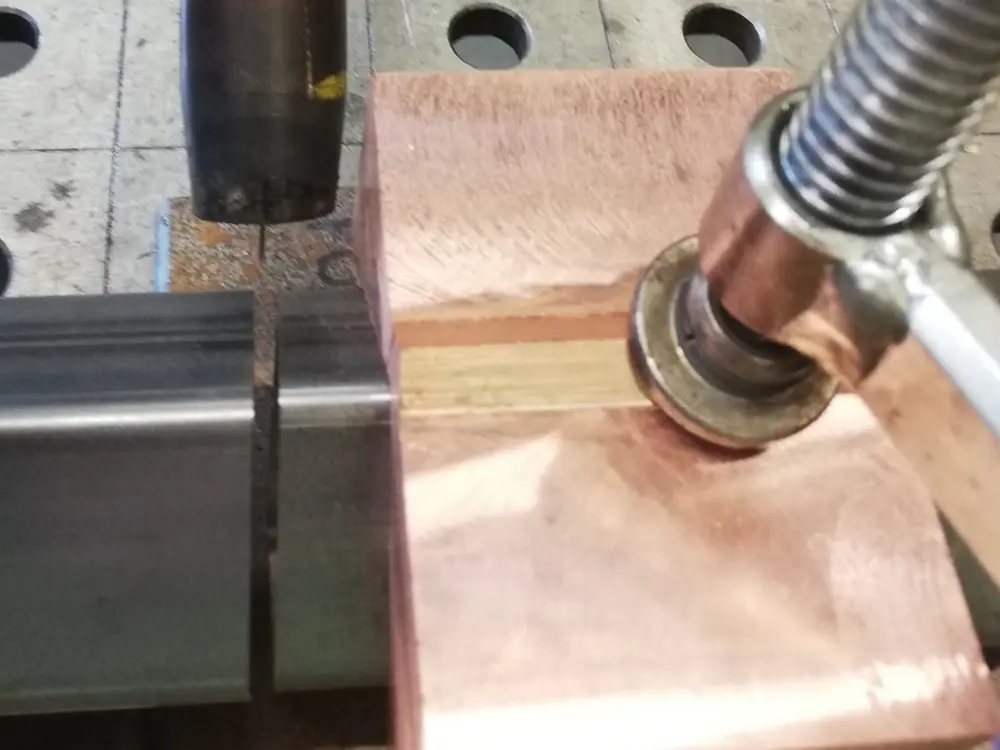
La courbe de température présentée à la figure 9 montre que le bloc de cuivre ne dissipe pratiquement pas de chaleur pendant le soudage. Cette observation a été confirmée par l'essai de dureté; voir la figure 10.
Figure 10: Evolution de la température avec le bloc en cuivre (courbe bleue) et sans le bloc en cuivre (courbe grise)
Evaluation
Lorsqu'on évalue l'effet des deux expériences sur les mesures de dureté, on remarque que le 'gain de dureté' dans la ZAT molle est plutôt limité. Lorsque les échantillons sont trempés dans l'eau immédiatement après le soudage, la dureté augmente de 40 à 50 HV. Cependant, l'effet le plus important est observé dans le métal de soudage proprement dit, où l'on observe une augmentation de la dureté d'environ 150 HV. Les essais de traction effectués sur les échantillons trempés ont encore montré une réduction de la résistance à la traction de 16% (contre 18% pour les échantillons non trempés, voir ci-dessus), par rapport à la résistance à la traction du matériau de base. Cette influence limitée peut s'expliquer par le fait que l'effet de la trempe commence relativement tard. En effet, pour la séquence de souduage #4, la température dans la ZAT molle a déjà chuté à 600 °C avant que la trempe ne commence. On peut attendre un meilleur résultat si la trempe est effectuée plus tôt après le soudage, mais cela n'est pas toujours possible pour des raisons pratiques.
Lorsque l'on utilise un bloc de cuivre pendant le soudage, l'effet est même nul: la dureté dans la ZAT molle est d'environ 200 HV, soit la même valeur que les soudures réalisées sans bloc de cuivre. Les évolutions de dureté sont présentées dans la figure 11.
Figure 11: Evolution de la dureté du DP800: sans refroidissement forcé lors du soudage (courbe grise), trempé après le soudage (courbe orange), refroidi pendant le soudage avec un bloc de cuivre (courbe verte)
Plus d'infos?
www.steel-s4-ev.eu
09/292.14.10
Jurgen.Feyaerts@bil-ibs.be
Le projet bénéficie d’un soutien financier de la Commission européenne via le programme RFCS (Research fund for Coal and Steel) sous le numéro de contrat 800726 – STEEL S4EV