Lassen van Dual Phase kokerprofielen
In het Steel S4 EV project worden lichtgewicht elektrische voertuigen ontwikkeld voor stadsverkeer, die voldoen aan alle reglementeringen op gebied van crashbestendigheid en andere Euro NCAP-eisen (European New Car Assessment Program). Het frame van het elektrische voertuig wordt slim ontworpen door gebruik te maken van geplooide en lasergesneden buizen die aan elkaar worden gelast. Hiervoor wil men gebruik maken van hoogsterkte staal. Het opzet is om door het toepassen van geavanceerde hoogsterkte stalen een zeer licht maar uiterst sterk en stijf frame te ontwikkelen. In deze ontwikkeling wordt gewerkt met Dual Phase (DP) stalen. Dit zijn innovatieve materialen waarbij het staal zijn eigenschappen verkrijgt door een unieke structuur, opgebouwd uit twee fasen (ferritisch-martensitische microstructuur).
Doel van het onderzoek
Het Belgisch Instituut voor Lastechniek onderzoekt het lassen van deze materialen uit het ontwerp. DP stalen zijn lasbaar, maar vaak wordt echter de microstructuur teniet gedaan als gevolg van het lassen. In dit project werd gezocht naar de optimale lasparameters waarbij er een aanvaardbare laskwaliteit wordt verkregen zonder te veel implicaties naar de mechanische eigenschappen.
De volgende aspecten werden hierbij onderzocht :
- invloed van de lascyclus op de verzachting in de warmte-beïnvloede zone (WBZ)
- invloed van toevoegmateriaal
- invloed van geforceerde koeling na het lassen
Er werd gezocht naar optimale lasparameters waarbij een aanvaardbare laskwaliteit wordt verkregen
Proefopstelling
In dit onderzoek werden langsgelaste kokerprofielen met afmeting 40x40x1.3 mm beproefd in de kwaliteiten DP800 en DP1000. In de kwaliteit DP800 werden ook lasproeven uitgevoerd op kokers van 40x40x2mm. De kokers werden zowel stomp aan elkaar gelast (stompe las) als in een hoekverbinding (flare bevel en hoeklas). Beide opstellingen werden zowel met een robot als manueel afgelast met het proces 135 (MAG lassen met massieve draad). Er werd gebruik gemaakt van hoogsterkte toevoegmateriaal, respectievelijk EN ISO 16834-A : G 69 4 M Mn3Ni1CrMo - Ø0.8mm voor DP800 en EN ISO 16834-A : G89 4 M Mn4Ni2CrMo - Ø1.0mm voor DP1000. De opstelling van de kokers voor zowel de stompe verbindingen als de hoekverbindingen worden weergegeven in Figuur 1.
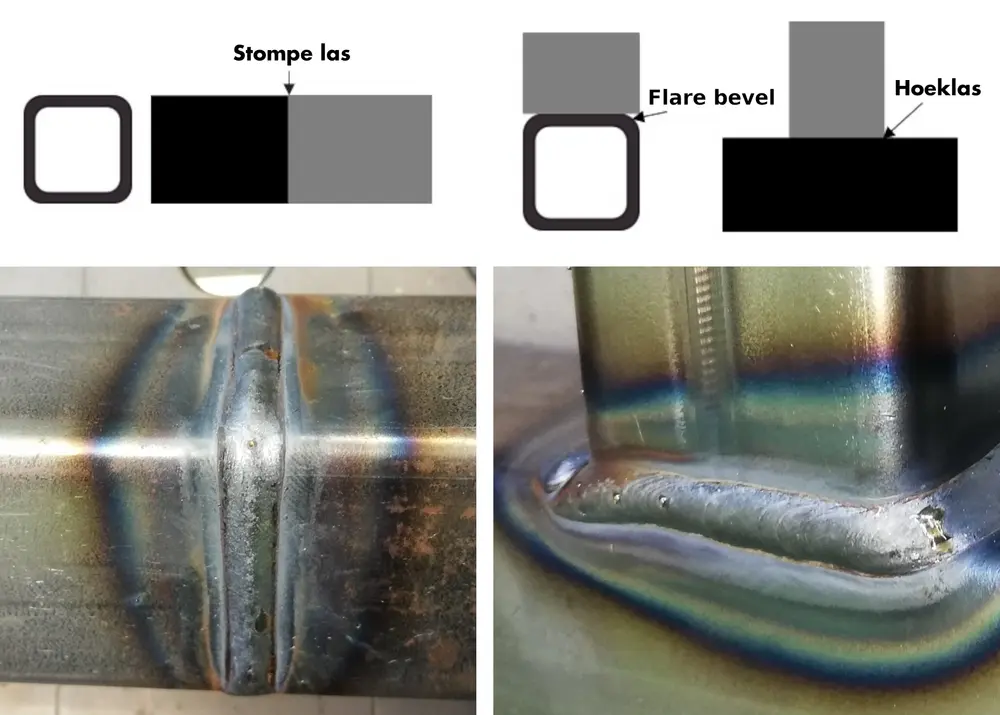
Figuur 1: Stompe opstelling (links) versus hoekopstelling (rechts)
Invloed van de lascyclus
Bij het onderzoek naar de geschikte lasparameters (lasvenster) konden 2 grenzen vastgesteld worden: een bovengrens met een hoge warmte-inbreng waarbij doorbranding kon vastgesteld worden en een ondergrens met een lage warmte-inbreng waarbij bindingsfouten optraden (zie Figuur 2).
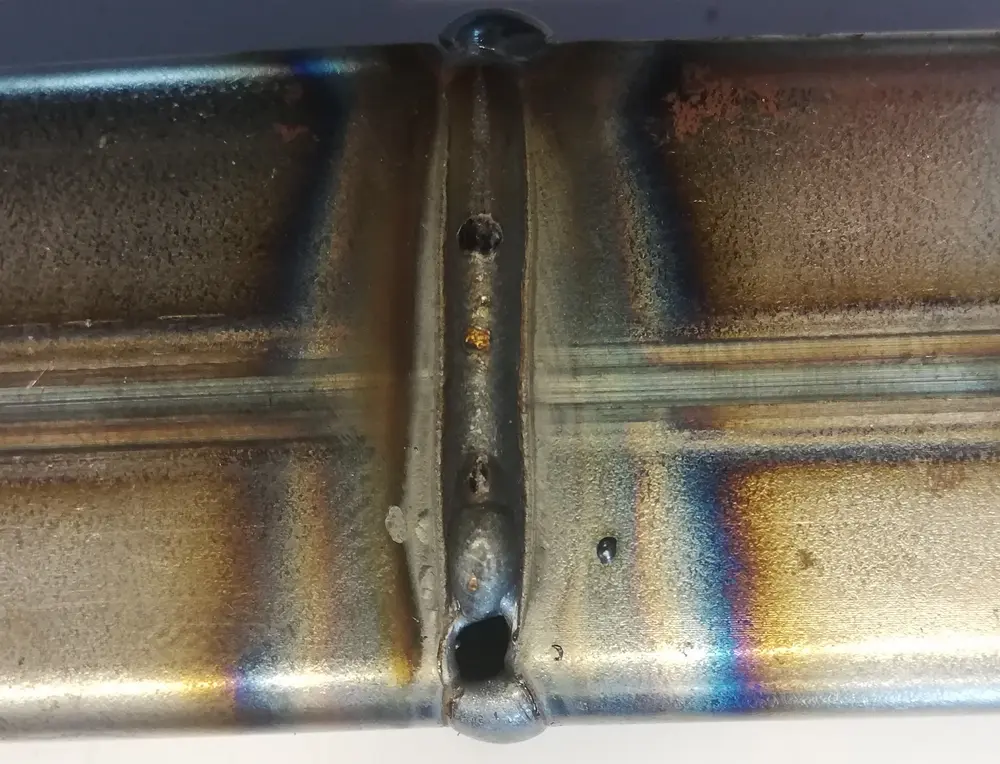
Figuur 2: Bindingsfout (boven), doorbranding (onder)
Deze grenzen en bijgevolg ook hun optredende imperfecties werden op hun beurt sterk beïnvloed door toleranties op de afmetingen van de doorsnede van de kokers. Dit resulteerde in de meeste gevallen in een uitlijningsfout (high-low) van minstens 2 kokeroppervlakken bij de stompe verbindingen en van 1 oppervlak (flare bevel) bij de hoekverbindingen (Figuur 3). Bovendien zorgden deze uitlijningsfouten ook voor een verschil in de te lassen doorsnede, met als gevolg dat aanvaardbare lasparameters plots aanleiding gaven tot doorbranding. Zeker bij de lasproeven uitgevoerd met de robot manifesteerde dit probleem zich, daar waar bij het manueel lassen de lasser nog enigszins kon bijsturen. Dit komt de reproduceerbaarheid van het gevonden lasvenster niet ten goede.
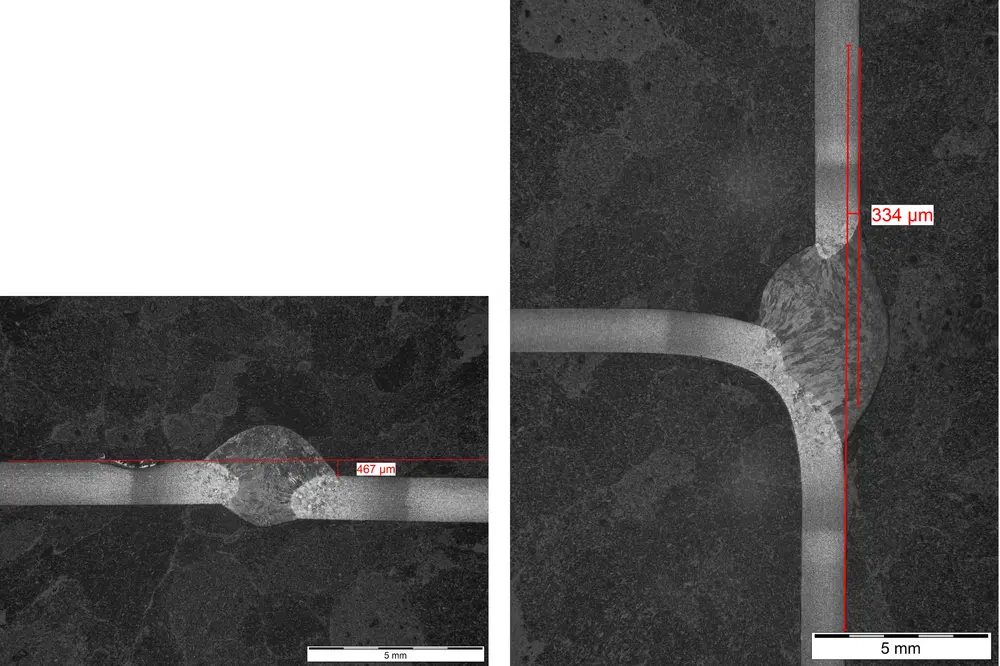
Figuur 3: Uitlijningsfout (high-low) bij stompe verbinding (links) en flare bevel van de hoekverbinding (rechts)
Verschillende zones
Uit het metallografisch onderzoek in combinatie met Vickers microhardheidsonderzoek (HV1) kon vastgesteld worden dat de warmte-beïnvloede zone (WBZ) van de lasverbindingen uit een aantal verschillende zones bestaat, waarbij o.a. de fasen en korrelgrootte variëren. Het basismateriaal van DP bestaat uit ferriet met eilandjes van martensiet. Hoe hoger de DP-kwaliteit, hoe hoger de volumefractie aan martensiet eilandjes. In de zone van de WBZ onmiddellijk naast het basismateriaal bestaat de microstructuur ook uit ferriet en martensiet, alleen is de structuur hier veel fijner en is het martensiet bovendien getemperd. Uit het microhardheidsonderzoek blijkt dat de hardheid in de fijne WBZ net naast het basismateriaal daalt tot een minimum. Bovendien bedraagt dit minimum steeds 190 à 200 HV, ongeacht de DP-kwaliteit (DP800 of DP1000), ongeacht de toegepaste warmte-inbreng en ongeacht de wanddikte van de koker (1,3 of 2 mm). De hardheid van het basismateriaal DP800 en DP1000 bedraagt respectievelijk 270-280HV en 350-360 HV; de verzachting die optreedt in de WBZ is dus significant. Figuur 4 toont de hardheidsverlopen voor de stompe verbindingen van DP800 (wandikte 1,3 en 2 mm) en DP1000, gelast met zowel de robot als manueel.
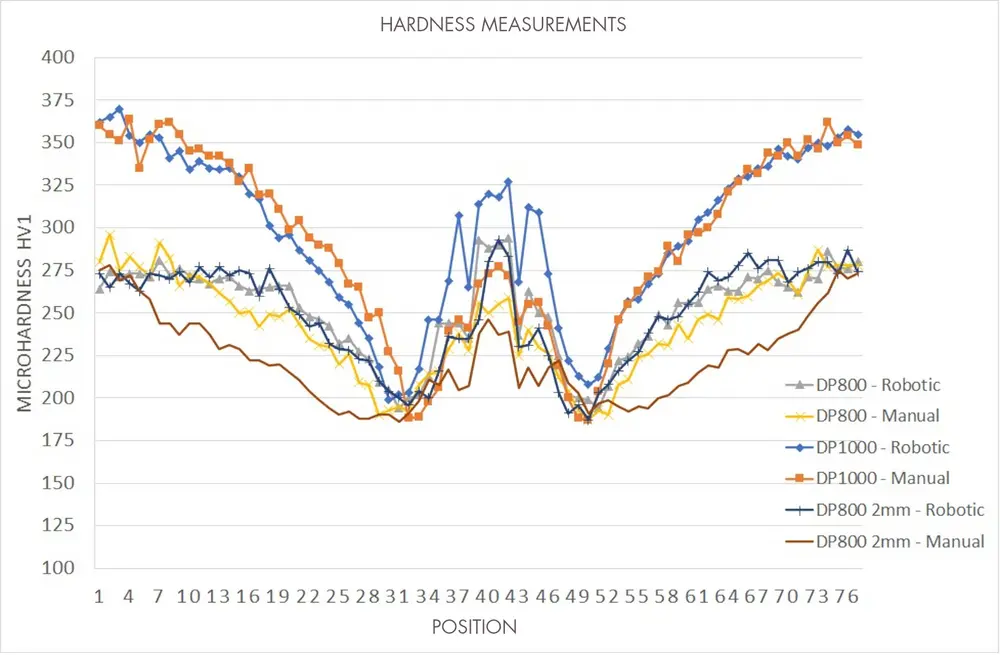
Sterkte van de las karakteriseren
Om de sterkte van de las te karakteriseren werden er dwarse trekproeven over de las uitgevoerd conform EN ISO 4136. Hiervoor werden platte trekproefstaven bewerkt uit de 3 verschillende zijden van de gelaste kokers (de zijde met de langste las werd niet beproefd). Uit de trekproeven blijkt dat de treksterkte van de lasverbindingen merkelijk lager ligt dan de treksterkte van de basismaterialen en zich situeert in de grootorde van 700 MPa. Metallografisch onderzoek toonde aan dat de breuk zich steeds manifesteert in de zachte zone van de WBZ zoals hierboven beschreven. Aan de niet gefaalde zijde kon in veel gevallen zelfs een insnoering vastgesteld worden in deze zone (zie Figuur 5). Voor DP800 kon een reductie van de treksterkte tussen de 18% (robotgelaste samples) en 24% worden waargenomen (manueel gelaste samples) in vergelijking met de treksterkte van het basismateriaal. Voor DP1000 werd zelfs een reductie van ongeveer 38% vastgesteld voor zowel de robotlassen als de manueel gelaste samples.
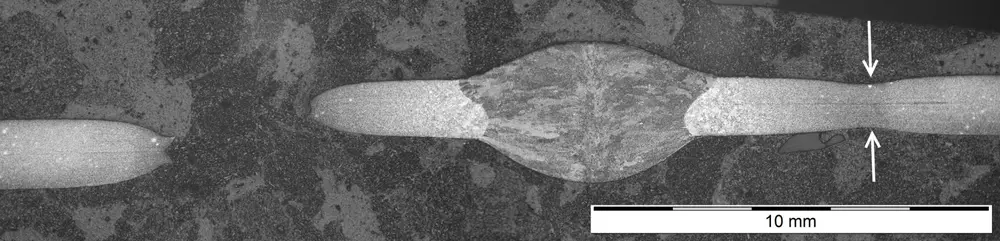
Figuur 5: Breuk in zachte WBZ – insnoering in zachte WBZ aan de niet-gefaalde zijde
Ook werden er trekproeven uitgevoerd op ware grootte van de kokers (zie Figuur 6), die werden gelast met de robot (DP800 40×40×1.3 mm). De behaalde gemiddelde treksterkte van de verbindingen (696 MPa) is van dezelfde grootorde als de gemiddelde treksterkte bepaald via genormaliseerde platte trekproefstaven (715 MPa).
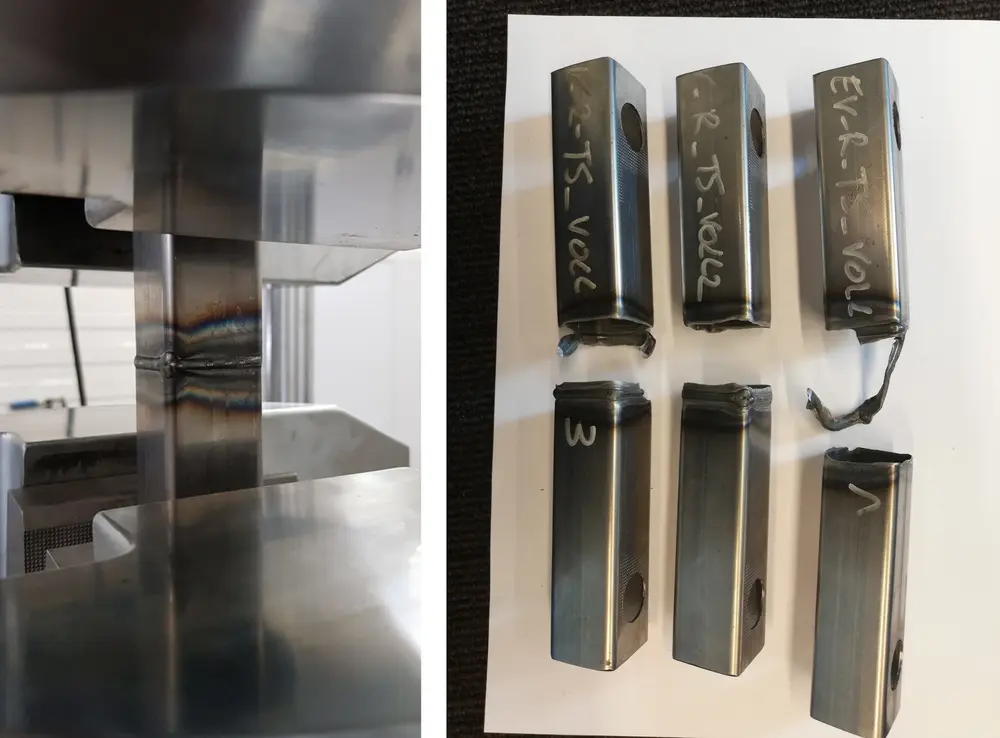
Invloed van toevoegmateriaal
De lasproeven werden standaard uitgevoerd met hoogsterkte toevoegmaterialen, zoals hierboven beschreven. Omdat echter bleek dat de trekproeven telkens faalden in de zachte zone van de WBZ bij treksterktes lager dan deze van het basismateriaal, werd een experiment opgezet waarbij gebruikt gemaakt werd van een laaggelegeerd toevoegmateriaal met lagere sterkte (zie Tabel 1).
Tabel 1: Overzicht van de gebruikte toevoegmaterialen om de invloed van het lasmetaal op de treksterkte na te gaan
Voor dit experiment werden DP1000 40×40×1.3 mm kokers gebruikt en werden de samples manueel gelast. De warmte-inbreng bij het lassen met beide toevoegmaterialen werd zoveel mogelijk constant gehouden om de eventuele invloed ervan op de trekproefresultaten te beperken. Uit de lasproeven blijkt dat ongeacht welke lasdraad werd gebruikt, de treksterkte van de lasverbinding gelijk bleef. In alle gevallen faalden de samples in de zachte zone van de WBZ.
INVLOED VAN GEFORCEERDE KOELING
Uit vorige experimenten is gebleken dat de treksterkte van de lasverbindingen nadelig wordt beïnvloed door de zachte zone van de WBZ. Er werden daarom een aantal lasproeven met de robot opgezet om te onderzoeken of deze verzachting kan beperkt worden en dus de treksterkte kan verbeterd worden. Deze proeven werden uitgevoerd met DP800 40×40×1,3 mm kokers. Om het temperatuurverloop in de zachte zone van de WBZ te evalueren, werd met behulp van metallografische doorsneden de locatie van deze zone bepaald ten opzichte van de fusielijn. Vervolgens werd op deze locatie een thermokoppel aangebracht op de voorlaatste (las #3) en de laatste (las #4) lassequentie (zie Figuur 7).
In eerste instantie werd de impact op de hardheid en treksterkte onderzocht als de gelaste koker direct na het lassen werd ondergedompeld (afgeschrikt) in water op kamertemperatuur (quenching).
Figuur 8 toont het temperatuursversloop tijdens en na het lassen, waarbij de blauwe curve de temperatuursmeting aan lassequentie #3 en de rode curve deze aan las #4 voorstellen. Het moment van afschrikken kan worden herkend doordat de curven op deze locatie sterk dalen. Zoals te zien in Figuur 8 gebeurt dit bij de blauwe curve bij een lagere temperatuur (las #3; ± 450°C) in vergelijking met de rode curve (las #4; ±600°C). Dit kan verklaard worden door het feit dat tijdens het uitvoeren van lassequentie #4 al een deel van de laswarmte uit de laszone van sequentie #3 werd gedissipeerd.
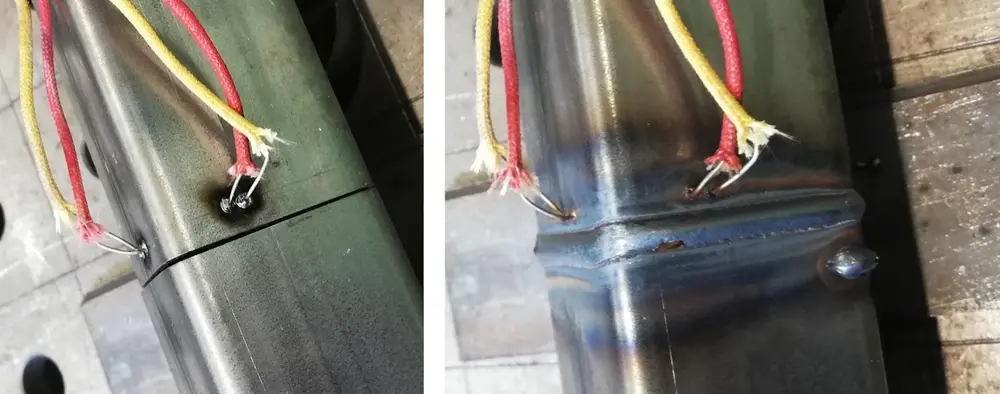
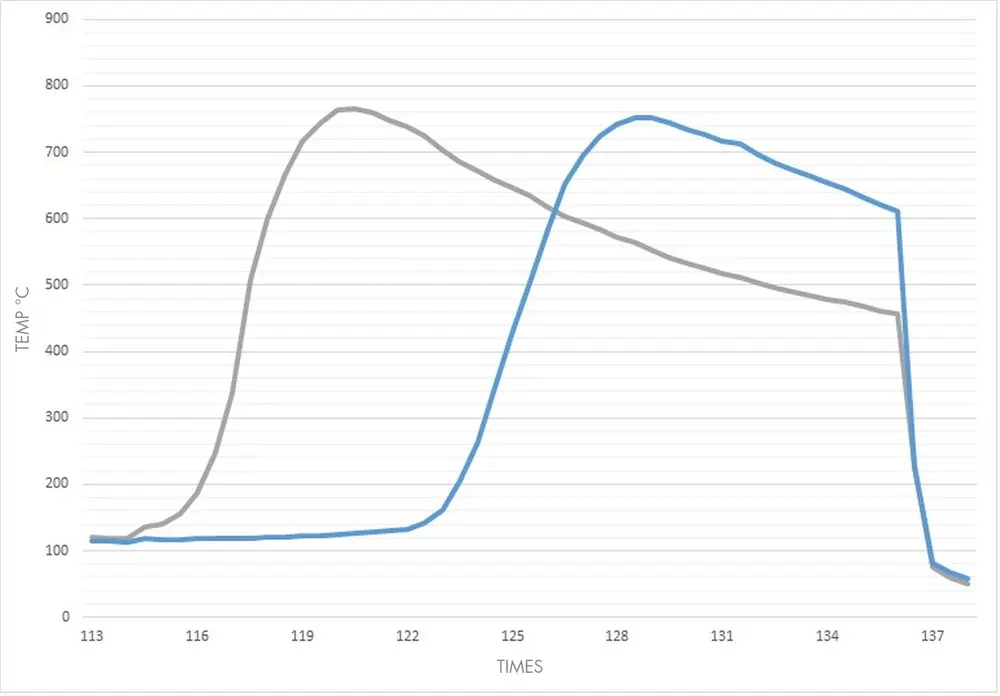
Figuur 8: Temperatuurverloop bij afschrikken in water; las #3 (grijze curve) en las #4 (blauwe curve)
Vervolgens werd een proef uitgevoerd waarbij er getracht werd om de warmte tijdens de lascyclus af te voeren door een op maat gemaakte koperen blok te bevestigen op de kokerprofielen. Het koperen blok werd zo dicht mogelijk tegen de laszone bevestigd zonder daarbij de lastoorts te hinderen (Figuur 9). De lasproeven werden uitgevoerd met gerobotiseerd lassen.
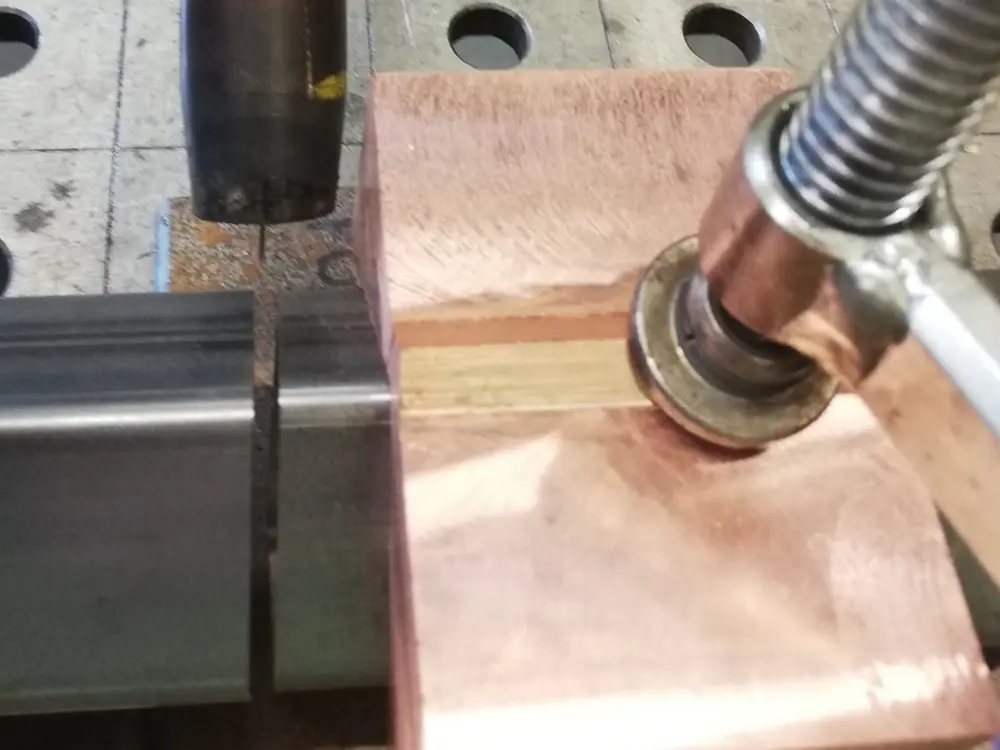
Uit het temperatuurverloop getoond in Figuur 9 blijkt dat er nagenoeg geen warmte gedissipeerd wordt door het koperen blok tijdens het lassen. Deze vaststelling werd bevestigd door het hardheidsonderzoek; zie Figuur 10.
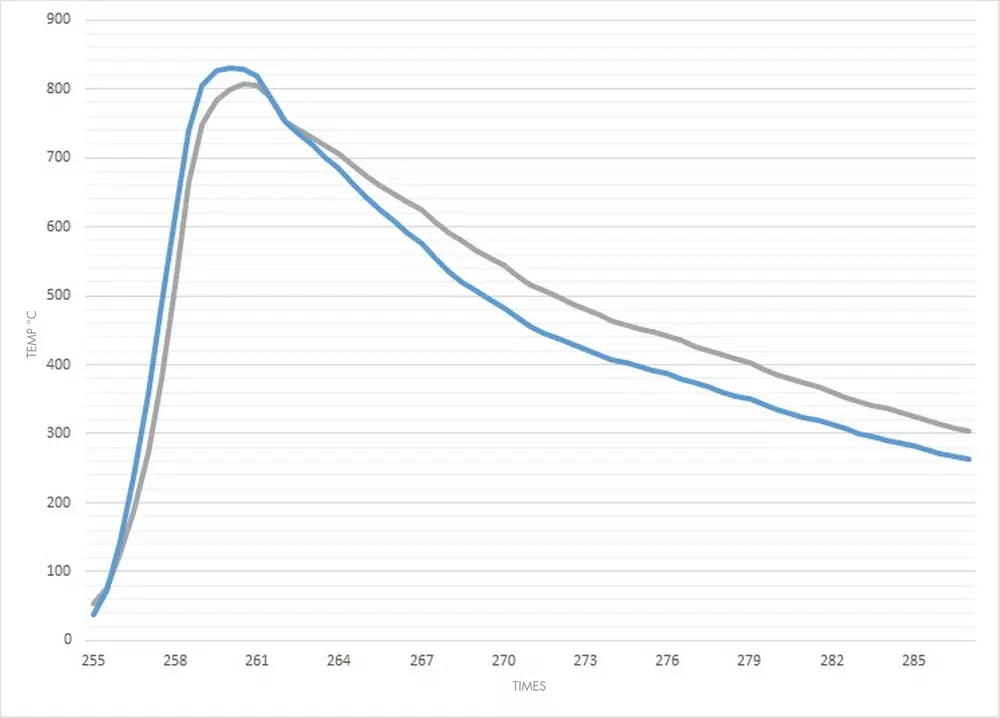
Figuur 10: Temperatuurverloop met koperblok (blauwe curve) en zonder koperblok (grijze curve)
Evaluatie
Wanneer het effect van beide experimenten op de hardheidsmetingen wordt geëvalueerd, valt het op dat de “hardheidswinst” in de zachte WBZ eerder beperkt is. Wanneer de samples worden afgeschrikt in water direct na het lassen neemt de hardheid met 40 à 50 HV toe. Het grootste effect wordt echter waargenomen in het lasmetaal zelf, waar er een hardheidstoename genoteerd wordt van ongeveer 150 HV. Trekproeven uitgevoerd op afgeschrikte samples toonden nog steeds een reductie van de treksterkte van 16% (in vergelijking met 18% bij niet-afgeschrikte samples, zie hierboven), vergeleken met de treksterkte van het basismateriaal. De beperkte invloed kan verklaard worden door het feit dat het effect van het afschrikken relatief laat begint. Immers, voor lassequentie #4 is de temperatuur in de zachte WBZ reeds gedaald tot 600 °C alvorens het afschrikken start. Een verbeterd resultaat kan verwacht worden als het afschrikken sneller na het lassen wordt uitgevoerd, maar dit is om praktische redenen niet altijd mogelijk.
Bij gebruik van een koperen blok tijdens het lassen is het effect zelfs nihil: de hardheid in de zachte WBZ situeerde zich rond 200 HV, wat dezelfde waarde is als de lassen uitgevoerd zonder koperen blok. De hardheidsverlopen worden voorgesteld in Figuur 11.
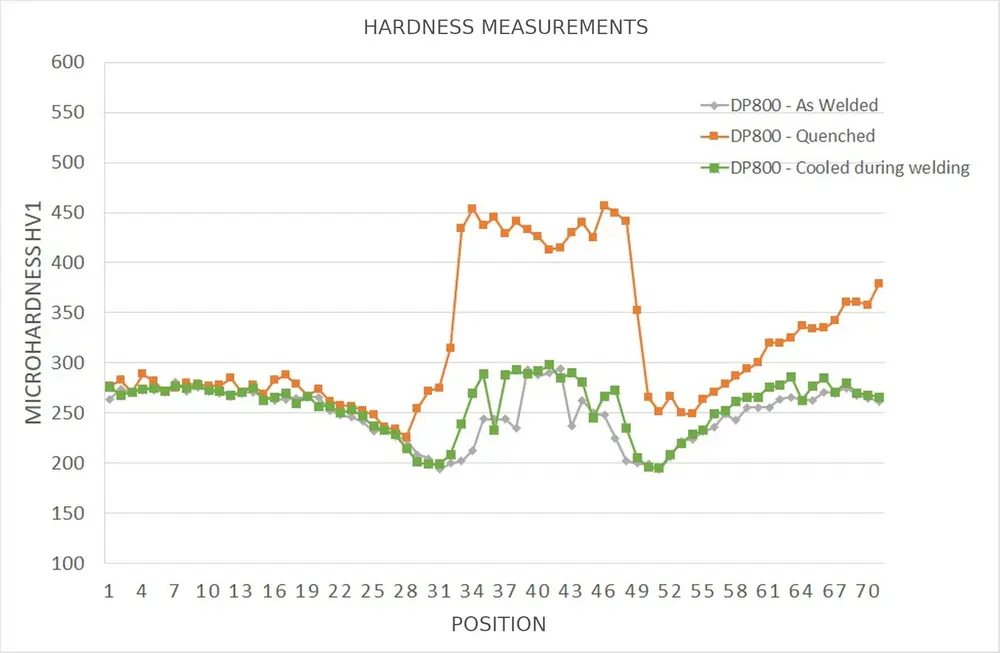
Figuur 11: Hardheidsverloop van DP800: zonder geforceerde koeling bij het lassen (grijze curve), afgeschrikt na het lassen (oranje curve), gekoeld tijdens het lassen met koperen blok (groene curve)
Meer info?
www.steel-s4-ev.eu
09/292.14.10
Jurgen.Feyaerts@bil-ibs.be
Het project krijgt een financiële ondersteuning van de Europese Commissie via het RFCS (Research fund for Coal and Steel) onder het contractnummer 800726 – STEEL S4 EV