Duurzaam lassen kan geld opleveren
Welke factoren hebben invloed op de ecologische voetafdruk van lassen?
Automatisering en robotisering zijn slechts één onderdeel van de verandering die het lassen doormaakt. Duurzaamheid gaat komende jaren eveneens een stempel drukken en tot veranderingen leiden. Dat hoeft niet eens zo heel erg slecht uit te pakken voor lasbedrijven. Integendeel.
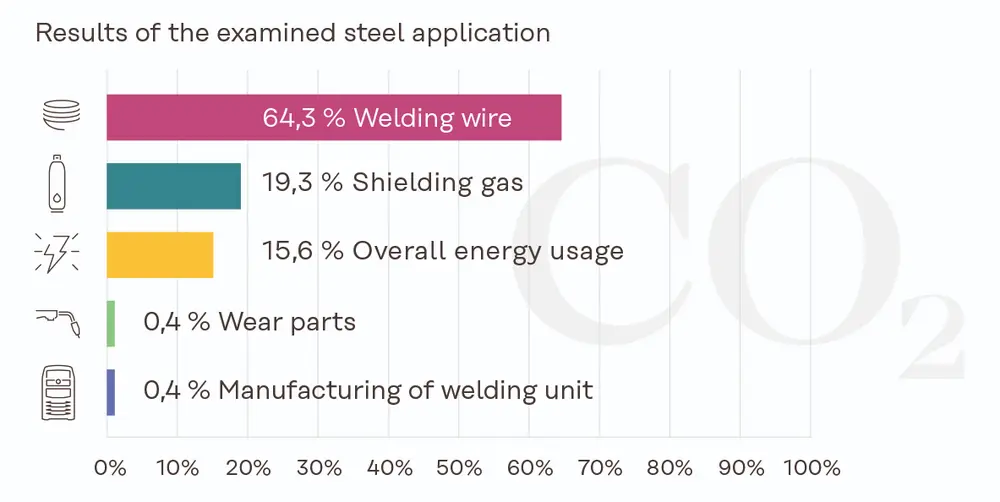
Fronius heeft samen met de onderzoekers van Fraunhofer IPK een lifecycle assessment (LCA) gemaakt voor zowel TPS als CMT (cold metal transfer) lassen. De draad neemt volgens deze LCA bijna twee derde van CO2-emissie voor z’n rekening: 64,3% om precies te zijn. Beschermgas komt met 19,3% op de tweede plaats en energieverbruik is goed voor 15,6%. De rest, amper een half procent, zit in de productie van de lassystemen zelf. De belangrijkste knop om aan te draaien is dus het materiaal
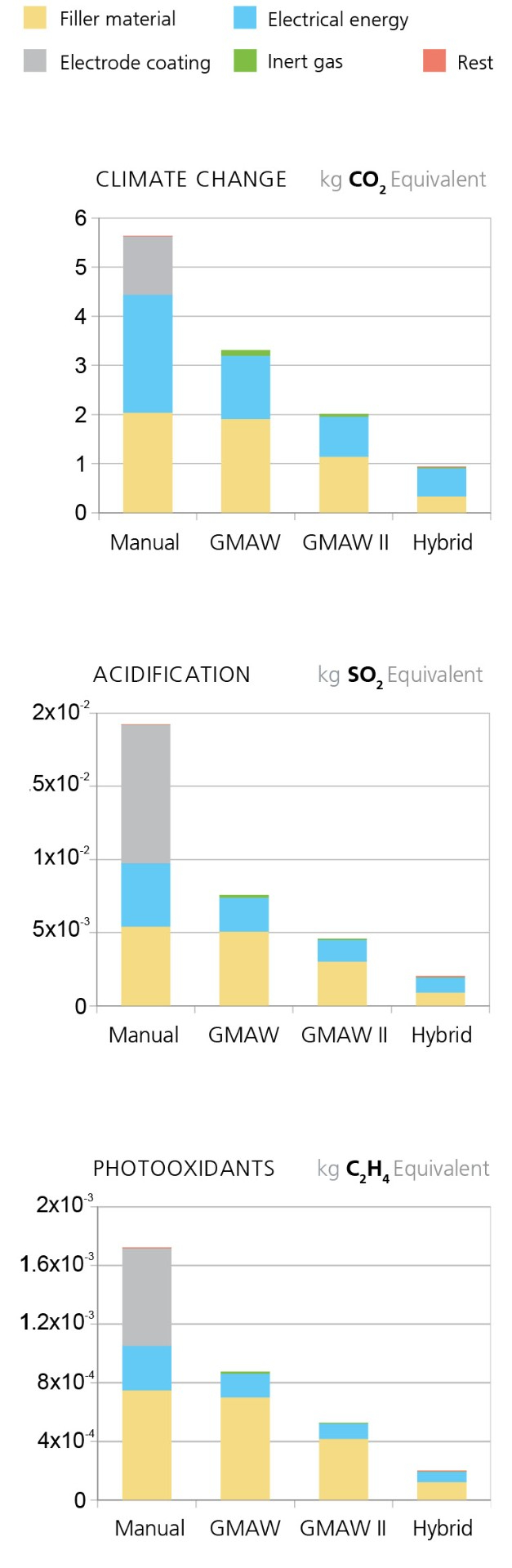
Het hybride lasproces heeft volgens het Fraunhofer IPK de kleinste ecologische voetafdruk van de technieken die men heeft onderzocht. Dit hybride concept combineert laserlassen met lichtbooglassen. De kleine ecologische voetafdruk is met name te danken aan het feit dat men minder materiaal verbruikt
Duurzaamheid
Het lijkt er weliswaar op dat de Europese Commissie de duurzaamheidsteugels komende tijd iets laat vieren, omdat men in Brussel inziet dat de druk op de industrie erg groot is, duurzaamheid zal desalniettemin een thema blijven.
Het Federal Institute for Materials Research and Testing (Bundesanstalt für Materialforschung und -prüfung – BAM) in Duitsland heeft vier factoren gedefinieerd die van belang zijn als men een lifecycle assessment (LCA) van een lasverbinding gaat maken. Daarbij baseren de Duitse ingenieurs zich mede op inzichten van de World Steel Association. Deze vier factoren zijn het materiaalverbruik (lasdraad en toevoegmateriaal); energieconsumptie; gasverbruik en het gebruik van beschermmiddelen, zoals een lasbril.
Om appels met appels te kunnen vergelijken, hebben de onderzoekers meerdere lassen gemaakt met uiteenlopende lastechnieken. Het gaat hierbij telkens om een las van één meter lengte. De drie onderzochte lastechnieken zijn handmatig elektrode lassen, gasbeschermd booglassen (GMAW) en laser-GMAW lassen (hybride).
Lasdraad / vulmateriaal en energie zijn volgens deze onderzoekers de belangrijkste factoren die bijdragen aan de CO2-emissie tijdens het lassen. De CO2-voetafdruk van het lasproces wordt enerzijds bepaald door de energiebron: last men met groene stroom of niet? Anderzijds blijken de lasdraad en het beschermgas een groot aandeel te hebben in de ecologische voetafdruk.
Interessant is dat de onderzochte technieken onderling grote verschillen laten zien. Manueel elektrodelassen veroorzaakt de grootste emissie (een equivalent van bijna 5 kg CO2-emissie), tegenover hybridelassen ongeveer 1 kg. Lichtbooglassen onder een beschermgas is eveneens aanzienlijk ecologischer dan manueel lassen, maar blijft slechter scoren vergeleken met hybridelassen.
De lasdraad (of vulmateriaal), de beschermgassen en energieverbruik hebben de grootste invloed op de CO2-emissie van lassen
Hoe de voetafdruk verkleinen?
Je zou kunnen denken: aan deze drie aspecten valt weinig te doen, dus de ecologische voetafdruk van het lasproces is een gegeven. De lasindustrie probeert echter wel degelijk, met onder andere digitalisering, deze drie factoren te beïnvloeden.
De hoeveelheid gas die nodig is, kan men met moderne lassystemen aanzienlijk reduceren. De nieuwe generatie gasdiffusors zijn aanzienlijk efficiënter doordat ze het gas gelijkmatiger verdelen. Dat betekent met minder gas hetzelfde resultaat.
Anderen kijken weer naar alternatieve gassen of naar menggassen. Omdat dit direct de kwaliteit van de lasverbinding beïnvloedt evenals de productiviteit, moet men hier weloverwegen mee te werk gaan. Koolstofdioxide heeft bijvoorbeeld een kleinere ecologische voetafdruk, maar kan de kwaliteit van de lasverbinding beïnvloeden. Helium kan een alternatief zijn voor argon bij het lassen van dikke materialen of voor het TIG- of MIG-lassen van aluminium of roestvaststaal. In toepassingen waarin een las wat ruwer mag zijn, bijvoorbeeld in bouwconstructies, kan koolstofdioxide soms een goed alternatief beschermgas zijn omdat dit tevens de kosten verlaagt.
Vergeet bovendien niet naar de zuiverheid van het beschermgas te kijken. Dit heeft ook direct invloed op de laskwaliteit. Men kan ook naar een ander lasproces op zoek gaan, wat wellicht geen beschermgas vereist.
Is hybride lasproces de heilige graal?
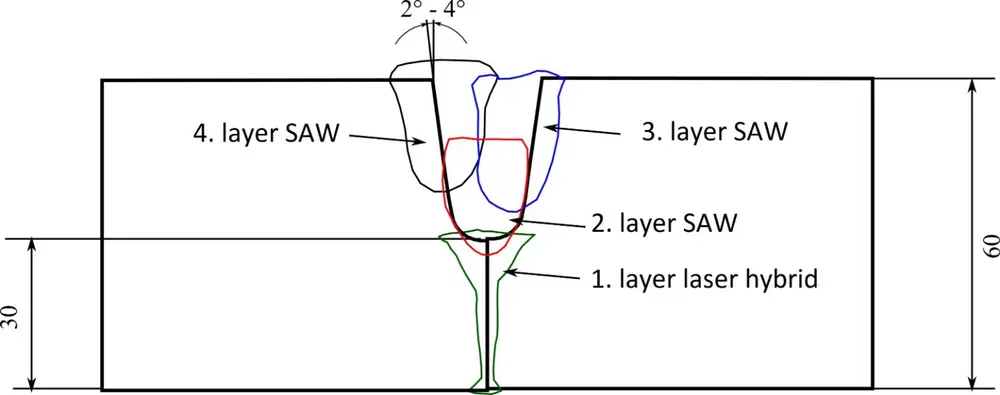
De onderzoekers zien veel potentieel in het hybride lasproces: de combinatie van hoog vermogen laserlassen met booglassen onder poederdek. De combinatie van deze twee processen verkort de doorlooptijd tijdens het lassen, verhoogt de kwaliteit en verbetert de winstgevendheid in de kmo’s.
Met het hybride lasproces kan men namelijk een diepe penetratie realiseren met relatief weinig lagen. Het diepste deel last men met de laser, de bredere delen met het booglasproces. Hierdoor is minder vulmateriaal nodig. Met deze procesvariant kunnen grote plaatdiktes worden gelast met een lager aantal lagen en een lagere warmte-inbreng.
Ecologie lijkt hier hand in hand te gaan met kosten, want doordat men minder warmte inbrengt, zullen er weinig restspanningen in het materiaal zijn en is spanningsarm gloeien wellicht niet noodzakelijk.
Automatiseren
Een andere manier om de voetafdruk van een lasproces te verkleinen, is automatiseren en digitaliseren. Een geautomatiseerd lasproces zal veel efficiënter met energie en materialen omgaan dan bij handmatig lassen mogelijk is. Geautomatiseerd lassen vermindert afkeur en afval. Dit heeft direct invloed op de kostprijs en dus op de winstgevendheid van de onderneming.
Automatisch lassen komt voor steeds meer toepassingen beschikbaar, ook voor kleinere series, doordat het programmeren van de lasrobot alsmaar minder tijd kost. De oplossingen hiervoor zijn parametrisch programmeren bij kleinere, eenvoudige stukken en vanuit het CAD-model het lasprogramma genereren. Dit laatste is in feite een toepassing van Model Based Definition. Een STEP-file wordt gebruikt voor de geometrische data; hier worden de lasparameters aan toegevoegd middels een xml-file. Hiermee kan men het aantal programmeeruren fors verkleinen, waardoor kleinere series wel door een robot gelast kunnen worden. Ook de offline robotprogrammeersystemen die verschillende spelers in de lasindustrie aanbieden, maken een verdergaande robotisering van het lassen mogelijk.
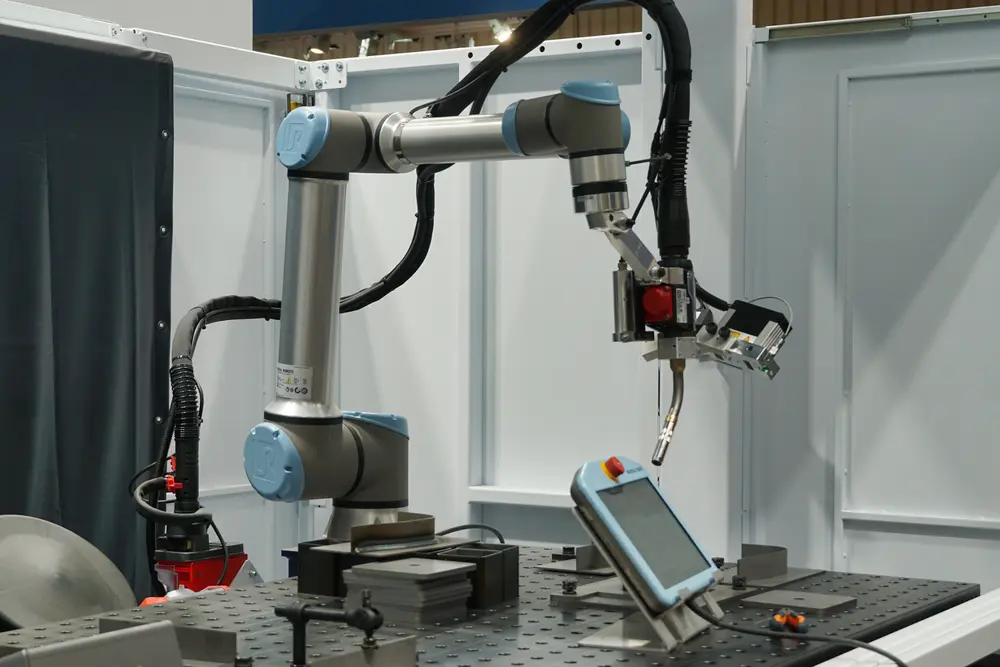
Trumpf brengt met de TruArcWeld 1000 een lascobot op de markt die amper geprogrammeerd hoeft te worden. Het systeem heeft een heel nieuw type lasnaadvolgsysteem. De software berekent aan de hand van de beelden de laspunten en de parameters
Alternatieve lastechnieken
Wrijvingslassen als alternatief
Daarnaast kan men een andere lastechniek overwegen, die minder toevoegmateriaal of lasdraad vergt of wellicht minder energie verbruikt. Een voorbeeld hiervan is wrijvingslassen dat de laatste jaren erg opkomt, onder andere in toepassingen in een elektrische auto.
Bij wrijvingslassen is geen extra materiaal nodig; evenmin een beschermgas. En de energie-inbreng ligt vele malen lager. Met name bij aluminium wordt het veel toegepast. De sterkte van de las komt dan dicht in de buurt van de sterkte van aluminium zelf.
De sterkte van de lasverbinding kan men verder verhogen door met minimale hoeveelheden koelmiddel te koelen tijdens het lassen (MQL, Minimal Quantity Lubrication). Hierdoor kan men de voeding en het toerental van de spindel verhogen, wat een kortere lastijd meebrengt, en een positief effect heeft op de sterkte van de verbinding.
Omdat wrijvingslassen een geautomatiseerd proces is, ligt de herhaalnauwkeurigheid op een hoog niveau. Onderzoekers zeggen dat wrijvingslassen 40 % minder energie verbruikt dan lichtbooglassen met beschermgas en 31% minder broeigasgassen veroorzaakt.
Is wrijvingslassen een ecovriendelijk alternatief voor andere lastechnieken? Ja, maar het moet wel passen bij de toepassing. Voor aluminium blijkt dit heel goed te kunnen. Op de foto een voorbeeld van een warmtewisselaar die met wrijvingslassen geïntegreerd in een Mazak bewerkingscentrum wordt gemaakt.
Laserlassen
Ook laserlassen kan een alternatief zijn. In Duits onderzoek is de energie-input bij laserlassen van staalconstructies vergeleken met het traditionele lichtbooglassen. Omdat de laser veel efficiënter de energie in de lasnaad brengt, ligt de energiebesparing vergeleken met conventionele lasprocessen op tot wel 80%. Dit geldt zowel voor staalconstructies voor containers, windturbines, schepen alsook railvervoer en infrastructurele projecten.
De forse besparing komt enerzijds doordat een groot deel van de energie van de lichtboog niet effectief gebruikt wordt voor het lassen en anderzijds door – zoals eerder aangegeven – het spanningsarm gloeien vaak nodig is. Dat kost nog eens net zoveel energie als het lassen zelf.
Omdat bij dergelijke lasconstructies de lasspleet vaak breder is dan normaal gangbaar bij laserlassen, hebben onderzoekers samen met het werkveld een technologie ontwikkeld speciaal voor het laserlassen van grote staalconstructies. Naast de 80% energiebesparing heeft men ook tot 85% minder vulmateriaal nodig vergeleken met de klassieke lastechnieken.
De toepasbaarheid van de techniek is door het Fraunhofer IWS aangetoond in een profiel voor de constructie van een kraan van 4 meter lengte. Het materiaal was 30 mm dik. Met de nieuwe techniek kon men de kosten halveren vergeleken met onderpoederlassen; bij 20 mm dikke plaat komt men zelfs nog tot hogere besparingen.
Hoe werkt deze technologie (laser multi-pass narrow-gap welding)? De laser wordt op de naad tussen de twee te lassen plaatranden geplaatst, terwijl een toevoegmateriaal wordt toegevoegd. De energie van de laserstraal smelt de randen van de werkstukken en het toevoegmetaal van de draad, die vervolgens de ruimte tussen de twee plaatdelen vult. De plaat is met plasma gesneden en de afstand die de laser moet overbruggen is tot 2 mm, wat voor de laser geen probleem is.
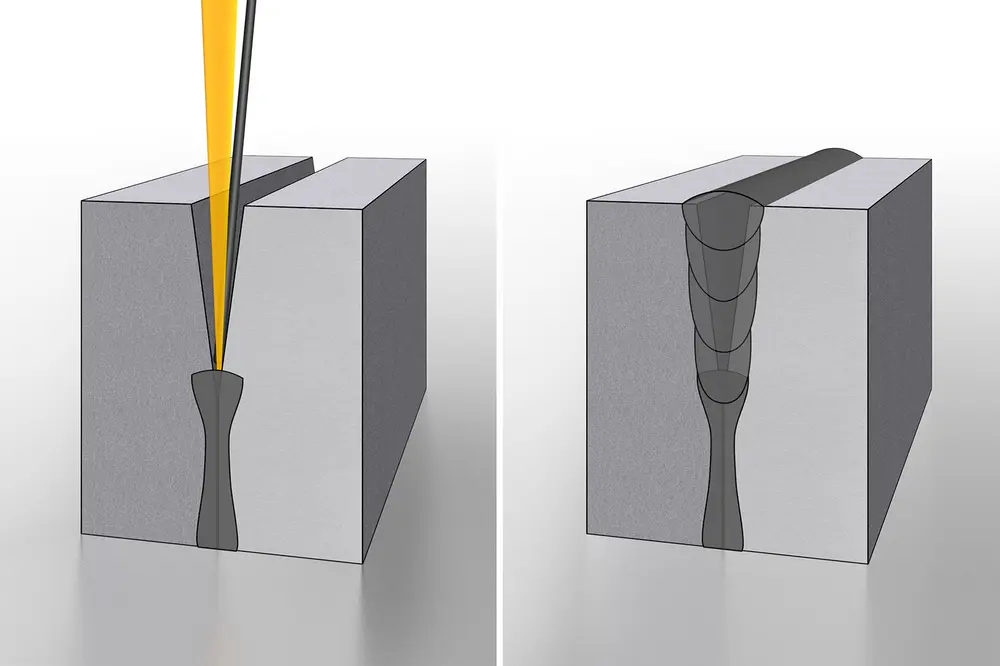
Zo ziet het laserlassen van dikke plaat voor staalconstructies er uit (foto Fraunhofer IWS)
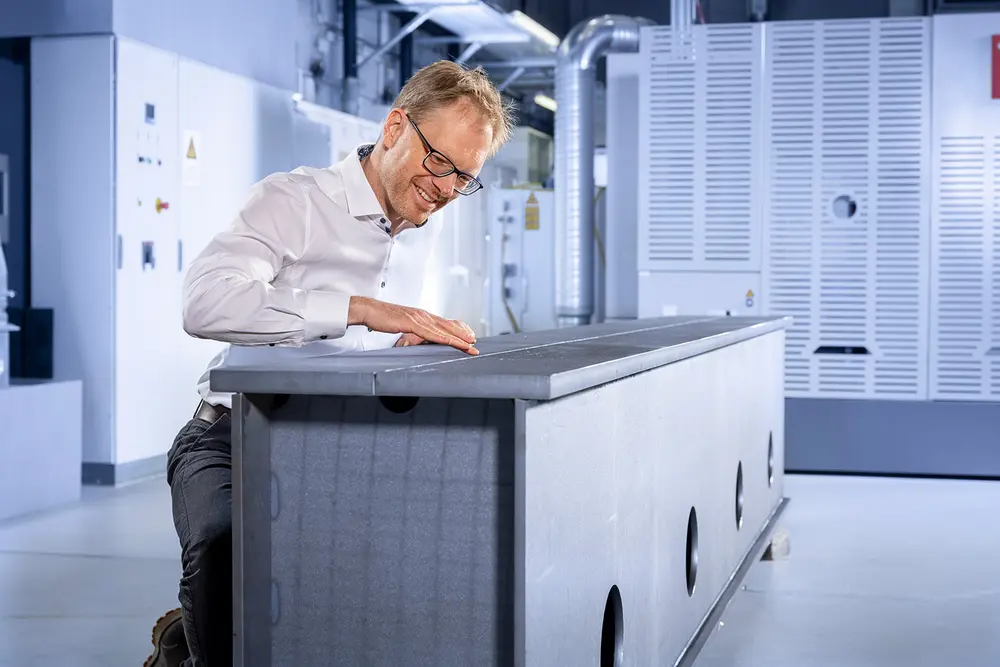
Microlaserlassen
Bij lassen wordt al snel gedacht aan het maken van relatief grote constructies. Er wordt echter ook op microschaal gelast. Onder andere in de halfgeleider- en medische industrie gebeurt dit veelvuldig. Daarbij is laserlassen de gangbare technologie, omdat het cruciaal is om de warmte-inbreng heel gecontroleerd te doen. Bij microlaserlassen luistert de materiaalsamenstelling heel precies. Kleine verschillen kunnen tot een totaal ander procesbeeld leiden. De verhouding van de legeringselementen moet binnen de norm vallen omdat het proces anders onvoorspelbaar wordt en de kwaliteit niet constant blijft.