hoe fouten bij lassen voorkomen?
controleer de laskantvoorbereiding!
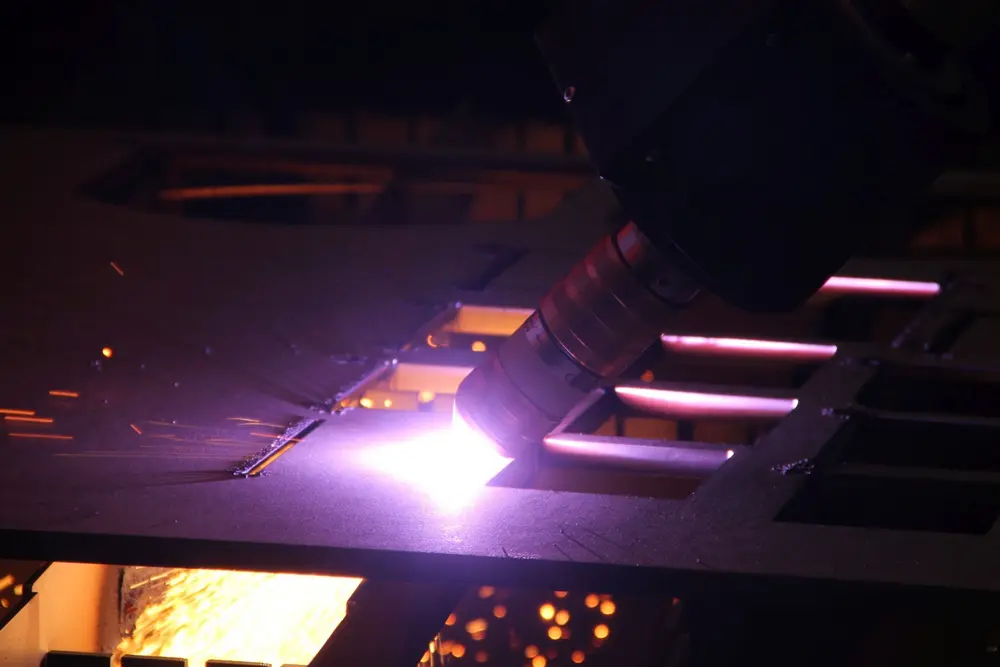
Soms kijk je bij de nacalculatie van een project raar op van de foutenlast, of omdat het aantal gepresteerde lasuren veel hoger ligt dan verwacht. Een slechte kwaliteit van laskantvoorbereiding zou daar weleens de oorzaak van kunnen zijn: een te grote openingshoek, slechte uitlijning … Nochtans staan in de EN ISO 9692-1-norm (staal) duidelijke aanbevelingen over de te gebruiken naadvorm, afhankelijk van het lasproces en de plaatdikte. Het probleem is dat het belang van een correcte laskantvoorbereiding wordt onderschat.
Wat is laskantvoorbereiding?
Aanbrengen van afschuiningen
Ontvetten is altijd een essentiële stap net voor het lassen. Als de oppervlaktegesteldheid dat vereist, kan je het best ook even stralen of lichtjes slijpen. De laskant schoonmaken kan echter ook na de laskantvoorbereiding, waardoor het dus geen onderdeel van die voorbereiding is. Met laskantvoorbereiding wordt het afschuinen van een of meerdere plaatkanten bedoeld.
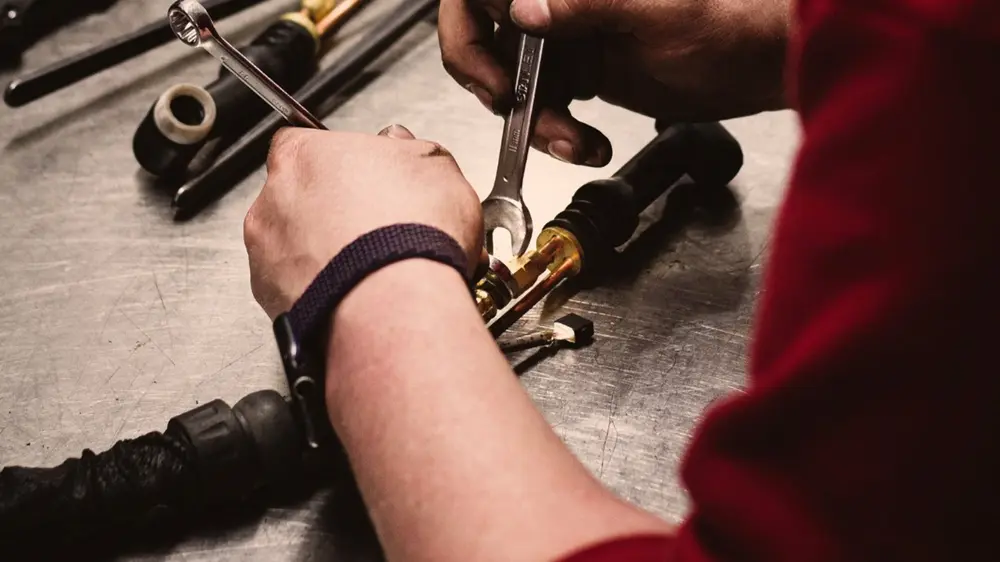
Lasnaadtypes
Er bestaan heel wat types lasnaden. De meest voorkomende zijn wellicht de X-naad, Y-naad, V-naad en de K-naad. Afhankelijk van het type lasnaad zal de vorm van de laskantvoorbereiding verschillen. Zo bestaat een V-naad uit twee platen die op een bepaalde afstand van elkaar moeten worden gezet. Soms lukt dat met een mal. Bij een V-naad schuin je dus beide platen af. Daartegenover staat, bijvoorbeeld, de X-naad. Die heeft twee schuine zijden en vaak ook een ‘neus’ of opstaande kant om het lasbad te ondersteunen. Het kruispunt kan in het midden liggen, maar evengoed boven of onder de plaat. Dat laatste wordt een asymmetrische X-naad genoemd. Een X-naad zal grofweg slechts half zoveel lasnaadvulling hebben als een V-naad, omdat ook het oppervlak maar de helft zo groot is. Ook de krimp en vervorming zullen kleiner zijn. Dezelfde redenering gaat op voor de K-naad, nog een ander voorbeeld. Bij een K-naad bereid je maar één plaat voor (maar wel twee kanten ervan).
Ontwerpkeuze
De vorm van de laskantvoorbereiding verandert dus samen met het naadtype. Het naadtype is op zijn beurt vooral een ontwerpkeuze, die in de eerste plaats rekening houdt met de toepassing en het soort belasting waaraan het gelaste stuk zal worden blootgesteld. Bij industriebouw zal die vooral statisch zijn, waardoor je daar vooral hoeklassen tegenkomt. Een heel ander verhaal vind je bij kraanmachines. Die worden dynamisch belast, en dat impliceert veeleer stompe lassen. Naast de aard van belasting spelen nog andere factoren een rol: het soort materiaal, de dikte van de platen, vervorming, toegankelijkheid van lassen (laspositie), het soort lasproces …
Voordelen laskantvoorbereiding
Niet altijd nodig
Lasnaadvoorbereiding komt vooral voor bij het dikkere plaatwerk om tot een goede hechting te komen bij het lassen. Zodra het vermogen bij het lassen onvoldoende is om een goede doorlassing te krijgen, wordt overgegaan tot laskantvoorbereiding. Bij offshore en tankbouw, bijvoorbeeld, is dat heel vaak het geval. Dat wil echter ook zeggen dat laskantvoorbereiding niet altijd nodig is. Bij dunne plaatdiktes en stompe lassen – in de range van 2 à 3 mm – kan je gerust zonder. We spreken dan van een gesloten I-naad. Het spreekt voor zich dat de platen dan netjes recht en haaks moeten zijn. Bij hoeklassen is er zelfs helemaal geen laskant nodig, ook niet bij grotere diktes.
Beschreven in de WPS
Vaak zal in de tekenfase al worden bepaald of een laskantvoorbereiding überhaupt nodig is, en, indien dat zo is, waaruit die dan moet bestaan. Dat is de verantwoordelijkheid van de lascoördinator, want de lasnaadvoorbereiding is procesafhankelijk. De informatie over de laskantvoorbereiding vind je heel expliciet terug in de lasmethodebeschrijving of de Welding Procedure Specification. Het is dus zeker niet zo dat de lasser daarin altijd de vrije keuze heeft, wel integendeel.
TIPS VOOR EEN GOEDE LASKANTVOORBEREIDING BIJ PLASMASNIJDEN
Het is heel belangrijk dat de rotator (de snijkop die laskant kan snijden) correct is uitgelijnd. Dat is iets wat de operator kan controleren.
Ook de hoogte is zeer belangrijk. Bij een verkeerde hoogte kan het product afwijken in grootte (bij V-naad), het neusje kan afwijken in grootte of de positie (Y-, K- en X-naden).
Gebruik zuivere platen waar geen vuiligheid of rommel op de bovenkant ligt. Dat kan de hoogte van het snijden beïnvloeden.
Gebruik de geschikte snijstroom voor een bepaalde plaatdikte. Er zijn meerdere snijstromen mogelijk voor een bepaalde plaatdikte. De plasmabronproducenten geven aan welke snijstroom het meest geschikt is voor een bepaalde plaatdikte. Controleer de ruwheid en de haaksheid om de juiste keuze te maken.
Gebruik een proper snijbed of propere snijlammelen zodat de plaat al zo recht mogelijk ligt.
Meerkost weegt niet op tegen voordelen
Maar als een lasser of een bedrijf de keuze heeft, waarom zou je het wel doen? En waarom zou je belang hechten aan de correcte uitvoering ervan? Met andere woorden, wat zijn de voordelen van laskantvoorbereiding? Om een doorlassing te realiseren in een (dikkere) plaat of buis kan je dikwijls niet anders dan een naadvoorbewerking aan te brengen. De doorlassing is vaak noodzakelijk voor de sterkte, de corrosiebestendigheid (bv. het vermijden van spleetcorrosie), de vermoeiingsweerstand, enzovoort. Een stevigere lasconstructie is dus misschien wel de belangrijkste reden om aan laskantvoorbereiding te doen. Door te kiezen voor een V-naad, om dat voorbeeld te nemen, zal je de las dieper kunnen aanbrengen. Een goede naadvoorbereiding, vooral de correcte openingshoek, vermijdt inbrandings- en plakfouten. Een laskant zorgt namelijk voor een groter lasoppervlak, waardoor het smeltbad de ruimte heeft om zich goed te vormen en het lastoevoegmateriaal zich op meer plekken kan hechten. Dat is duidelijk.
De meerkost die het aanbrengen van laskanten met zich meebrengt, weegt niet op tegen de kwaliteitsverbetering
En mocht je erover twijfelen: de meerkost die het aanbrengen van laskanten met zich meebrengt, weegt niet op tegen de kwaliteitsverbetering. Bovendien zal je door het aanbrengen van laskanten minder toevoegmateriaal nodig hebben als je streeft naar een optimale laskantvoorbereiding. Het is wat schipperen tussen een zo klein mogelijke hoek om het verbruik van lasmateriaal te minimaliseren en een hoek die toch groot genoeg is om het risico op plakfouten te vermijden.
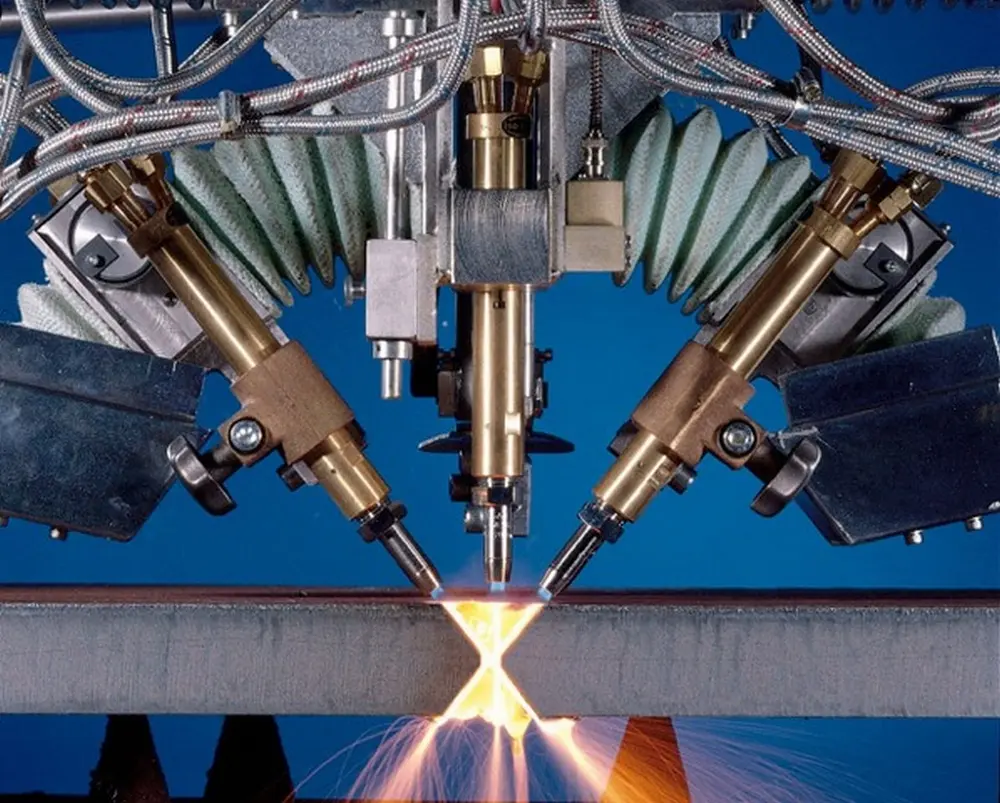
Uitvoeringstechnieken
Nadat beslist is dat de toepassing om een laskantvoorbereiding vraagt, en eens de geometrie ervan vastligt, is het zaak om wat gevraagd wordt naar behoren uit te voeren. Dat lijkt misschien vanzelfsprekend, maar in de praktijk blijkt dat vaak niet zo te zijn. Deels heeft dat te maken met de genereuze toleranties van bepaalde machines, al wijst de laksheid waarmee die worden getolereerd, toch vooral op een schromelijke onderschatting van het belang van een goede laskantvoorbereiding. Een te kleine vooropeningshoek, een van de veelvoorkomende fouten, geeft een verhoogde kans op doorlas- en bindingsfouten. In het ergste geval kan het zelfs tot falen van de constructie leiden. De gevolgen zijn dus niet min.
Vandaar ook dat je vanuit sommige toepassingsnormen zoals EN ISO9013 als gebruiker van een snijmachine richtlijnen krijgt om de snijkwaliteit te beoordelen voor de beoogde toepassing. De norm hanteert objectieve parameters zoals haaksheid en ruwheid. Door het snijden van verschillende stukken (diktes, gatenpatroon, schuine kanten) kan de werkelijke snijcapaciteit van de machine in kaart worden gebracht. Zo weten de lascoördinator en de tekenkamer wat de limieten zijn van de machine en of er voor een andere machine moet worden gekozen of niet.
Dat neemt niet weg dat er vandaag dankzij nieuwe technologieën een trend is ontstaan naar kleinere hoeken. In de praktijk zijn bindingsfouten meestal het gevolg van een lasser die door een slechte toegankelijkheid geen juiste positie kan aannemen van zijn laspistool. Tot slot kijken we nog even naar de uitvoeringstechnieken zelf. Vele snijtechnologieën en machinale bewerkingen bieden zich aan als een geschikte kandidaat. Elk met specifieke voor- en nadelen. We lijsten ze op in de tabel hieronder.
Met dank aan B.I.L., dwk-welding, Weldone en Wouters Cutting & Welding