Fieldlab Smart Maintenance maakt de balans op
'Lessons learned' vertaald naar nieuwe initiatieven
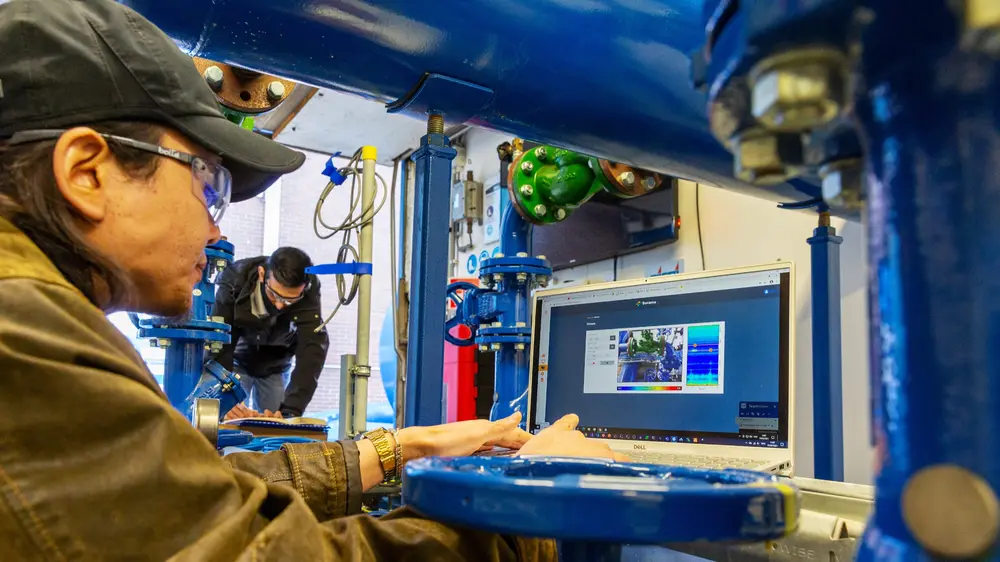
Vier jaar geleden, in 2018, werd het Fieldlab Smart Maintenance opgericht vanuit Techport. In die periode is door alle partners keihard gewerkt om bedrijven, scholen en onderzoeksinstituten samen te laten werken op het gebied van slim onderhoud. Met mooie resultaten. Just Schornagel, technisch programmamanager bij Techport, en Mark Denys, directeur technology transition bij Tata Steel en tevens voorzitter van Techport, blikken terug op de 'lessons learned' en kijken vooral ook naar de toekomst.
Kennis tot in de bedrijven krijgen
Een van de speerpunten van Techport (zie ook kader) is 'slim onderhoud'. Daarbij ziet de organisatie onder andere een bottle neck in het feit dat de ontwikkelingen binnen Smart Maintenance hard gaan, maar dat de vertaling naar het bedrijfsleven vaak te wensen overlaat. En dat is geen onwil, maar veel vaker een gebrek aan kennis, tijd, mensen en middelen.
Over Techport
Techport is een netwerk van meer dan 60 scholen, bedrijven en overheden in de Metropoolregio Amsterdam, met de IJmond als kern. Zij heeft de ambitie om in 2030 dé excellente economische regio van de Nederlandse maak- en onderhoudsindustrie te zijn. Hiervoor legt de organisatie een focus op een gezonde arbeidsmarkt, een actueel en uitdagend opleidingsaanbod en aan voldoende talent.
Techport besloot daarom het Fieldlab Smart Maintenance op te zetten. Een 'proeftuin' waar bedrijven en scholen samenwerken en naar hartenlust kunnen testen en experimenteren met zowel techniek als de benodigde organisatiekunde en projectmanagement.
Just Schornagel: "We zijn daarbij begonnen met een aantal partners, waaronder Tata Steel als grote asset owner, toeleveranciers van onder meer sensoren en software, en de Vrije Universiteit Amsterdam als kennisinstelling. Specifiek deze partijen konden invulling geven aan onze behoefte om big data te genereren, wat onlosmakelijk verbonden is met Smart Maintenance. Hiermee kunnen we weer vragen beantwoorden waar bijna elk bedrijf dat slim onderhoud in de bedrijfsvoering wil implementeren mee te maken heeft: welke grootheden zijn relevant om te meten, welke sensoren moeten hiervoor op welke plaats komen en hoe interpreteer je de grote hoeveelheden data die je hiermee genereert? Met deze vraagstukken zijn we aan de slag gegaan binnen drie werkpakketten die binnen het Fieldlab zijn ontwikkeld."
Proefinstallatie
Het 'pareltje' van deze werkpakketten is de proeffabriek. Hier is een proefinstallatie opgebouwd, bestaande uit vier industriële elektrische pompen die via een leidingsysteem zijn verbonden met een buffervat met een capaciteit van maar liefst 64.000 l.
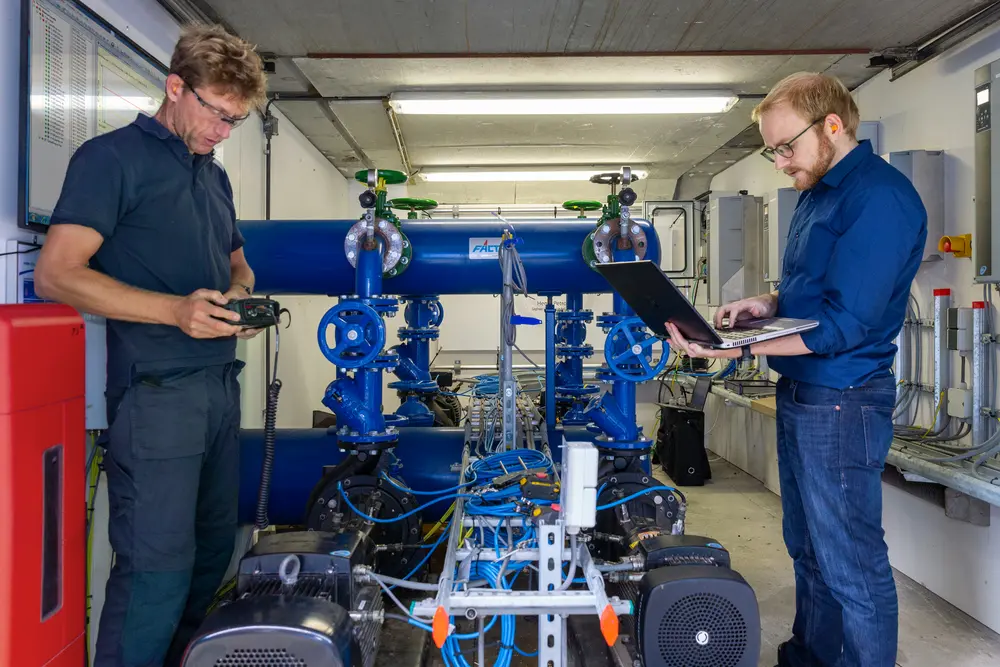
Schornagel: "Met deze opstelling hebben we een aantal veel voorkomende elementen uit de maakindustrie beschikbaar voor onderzoek: pompen, elektromotoren, leidingwerk en lagers. Hier kunnen we sensoren testen, data genereren en analyses uitvoeren. Tot de gegenereerde data behoren overigens ook faaldata. Veel data behoren in principe bij een goed werkende installatie. Vergelijkingsmateriaal van defecte of versleten assets is in veel mindere mate beschikbaar, terwijl je dat juist nodig hebt om algoritmes te trainen."
"Faaldata genereren, is noodzakelijk voor het trainen van algoritmes"
Onder andere de Koninklijke Marine heeft de installatie zes weken gehuurd om allerlei defecte en bijna-defecte assets door te meten. "Hiermee is een schat aan data gegenereerd, waarmee ze verder kunnen tijdens onder meer de ontwerpfase van hun nieuwe schepen", weet de programmamanager. "Bovendien is rondom de proefinstallatie een Masterclass ontwikkeld: een bijscholingstraject waar monteurs en operators in vijftien dagdelen op onze proeflocatie worden opgeleid. Vorig jaar hebben we de eerste sessie gehad, die zeer goed ontvangen is. Later dit jaar staat er een nieuwe op de rol."
In de fabriek
Het tweede werkpakket omvat projecten die niet op de proefinstallatie worden uitgeprobeerd, maar rechtstreeks in de fabriek. Onder andere bij Tata Steel zijn binnen dit kader de nodige projecten uitgevoerd. Eén daarvan speelt zich af langs de beitsbaan, waar de bijbehorende aandrijflijn door het nieuwe hogesterktestaal steeds zwaarder wordt belast. Hier zijn in een samenwerking met diverse partners sensoren geplaatst die de elektromotoren en tandwielkasten in de gaten houden. Inmiddels is hiermee op basis van temperatuur- en trillingsmetingen behoorlijk betrouwbaar te voorspellen wanneer overbelasting dreigt. Dit zijn tijdstippen die uitnodigen om de snelheid wellicht iets te verlagen of tijdig onderhoud uit te voeren.
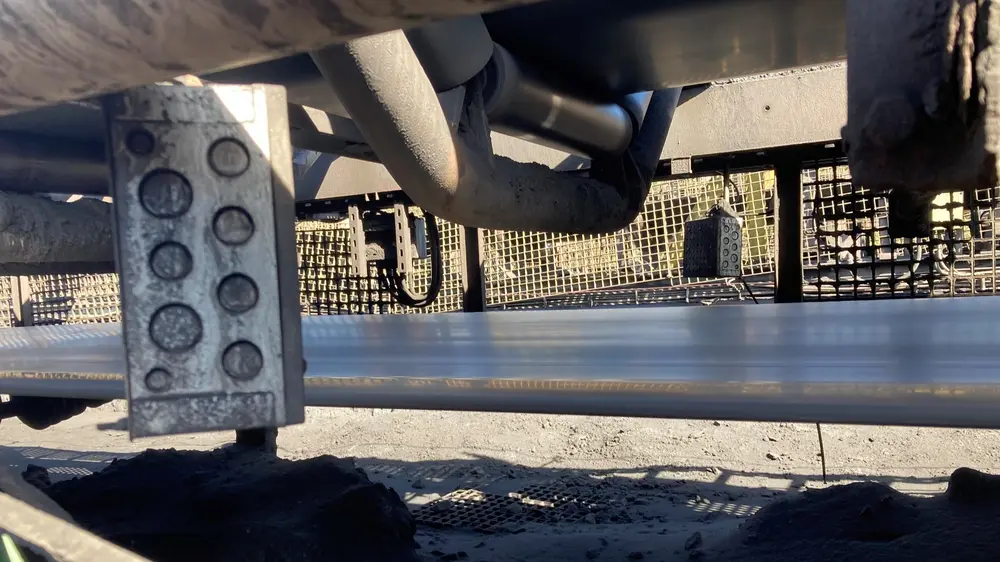
Een ander mooi voorbeeld zijn de akoestische sensoren die het Eindhovense bedrijf Sorama ontwikkelde voor het detecteren van onrust in uitgaansgebieden. Deze sensoren bleken ook in staat om slijtage van lagers te detecteren op basis van geluid; beter en nauwkeuriger dan dat wij dat met onze oren kunnen. Het proefproject langs de kilometerslange transportbanden van Tata Steel was dermate succesvol dat de sensoren nu ook in de praktijk worden ingezet. Hiermee voorkomt het bedrijf ongewenste stilstand of een te vroege vervanging, en heeft het als bijkomstigheid ook de mogelijkheid om de geluidsbelasting voor de omgeving te monitoren.
Schornagel: "Voor bovenstaande projecten geldt dat de ruwe data op het platform van het Fieldlab worden gedeeld. Hier zijn ze voor alle aangesloten partijen zichtbaar en te gebruiken. Op deze manier wordt gezamenlijk kennis opgebouwd en ondersteunen de partners elkaar, waarbij iedereen zijn eigen specifieke kennis en ervaring kan inzetten."
Business innovaties
Het derde werkpakket wordt geleid door de VU en richt zich op business innovation. Aandacht voor innovatieve onderhoudstechniek is immers één, maar het opschalen van deze technieken en succesvol implementeren in de praktijk is een heel ander verhaal. Daar is samenwerking voor nodig. De VU analyseert hoe deze samenwerking het beste is vorm te geven en zich vertaalt naar nieuwe implementatie- en verdienmodellen.
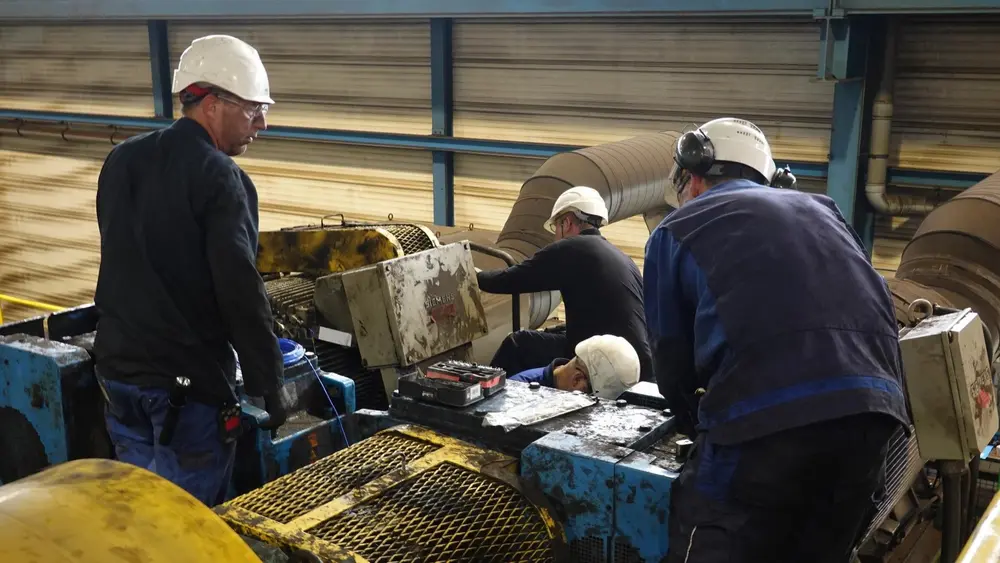
Schornagel: "We hebben vier bomvolle jaren achter de rug waarin veel kennis is ontwikkeld. Een van de belangrijkste lessons learned is de rol van de werkvloer: uit de vele projecten is gebleken hoe belangrijk het is om de werkvloer bij ontwikkelingen op het vlak van smart maintenance te betrekken. Deze mensen moeten er immers uiteindelijk mee werken en hoe enthousiaster zij zijn, hoe beter de oplossing in de praktijk zal werken. Bovendien zitten daar ook de ideeën en is de kennis beschikbaar over mogelijke verbeterpunten."
Toekomst
Gezien de ontwikkelingen binnen Smart Maintenance en de resultaten van het Fieldlab tot nu toe, is er alle reden om op de ingeslagen weg door te gaan en misschien zelfs uit te breiden.
Mark Denys: "Voor de toekomst zien we drie speerpunten binnen Techport die ook betrekking hebben op smart maintenance. Dat zijn de drie D’s: Duurzaamheid, Digitalisering en Demografie. Met het laatste bedoelen we dat de aanwas van jong, goed opgeleid technisch personeel op dit moment te klein is. Willen we onze doelstelling halen om in 2030 de excellente economische regio van de Nederlandse maak- en onderhoudsindustrie te zijn, dan zal er echt wat moeten gebeuren; bijvoorbeeld zij-instromers opleiden."
"We zien drie D's als speerpunten: Duurzaamheid, Digitalisering en Demografie"
In het kader van digitalisering zijn er ideeën om een tweede Fieldlab op te zetten, dat nog meer gebaseerd is op de usecase. De achterliggende gedachte is om hiermee binnen bedrijven zelf een snelle pilot te kunnen opzetten om te kijken of de inzet van bepaalde sensoren voor specifieke doeleinden loont.
Denys: "Ik zou het geen quick & dirty willen noemen, maar het gaat erom dat we niet een heel compleet systeem ontwikkelen met alle sensoren op de juiste plaats en de perfecte analysesoftware met aandacht voor cybersecurity enzovoort. Dat vraagt immers hoge investeringen en als het dan niet zo werkt als beoogd, verdien je die ook niet meer terug."
"De bedoeling is juist om wat goedkopere sensoren in te zetten, die bijvoorbeeld zes maanden meegaan. Die willen we dan koppelen aan het eigen netwerk; niet aan de buitenwereld. Dit geeft de mogelijkheid om snel en goedkoop data te genereren en je vervolgens te richten op het deel waar het echte vraagstuk ligt: welk algoritme heb je nodig om relevante informatie uit deze data te halen? Als uit deze relatief simpele opstellingen blijkt dat de oplossing voldoende waarde toevoegt, dan kun je als bedrijf de case verder uitwerken en implementeren. Vanuit Tata Steel zouden we dit soort projecten binnen Techport ook graag met andere partijen willen oppakken."
Innovation Centre
Een ander toekomstidee is de inrichting van een Techport Innovation Centre, vlakbij de Tata Steel Academy.
Denys: "Tata Steel en het Nova College runnen al jaren een bedrijfsschool, waar we mensen opleiden om bij Tata Steel aan de slag te kunnen. Deze willen we graag uitbreiden met een fysieke plek waar bedrijven uit het Techport-netwerk en studenten van de deelnemende scholen naar hartenlust kunnen experimenteren met verschillende opstellingen."
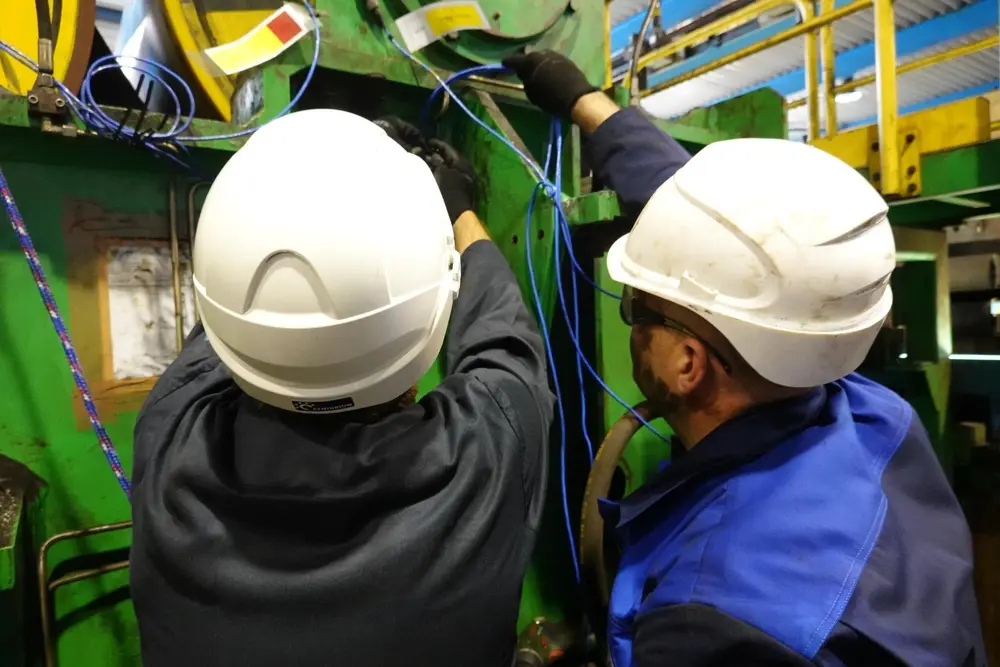
Denys: “Alleen maar door kennis te delen, kunnen we nieuwe mensen opleiden die morgen in staat zijn om met de beschikbare technologieën te werken. Daarvoor is vernieuwend onderwijs nodig, want ook de mindset moet veranderen. Meer gericht op voorspellend en preventief onderhoud; weg van het brandjes blussen maar richting controle over je eigen assets. Je introduceert dan overigens wel weer nieuwe fenomenen: als je namelijk in staat bent om door smart maintenance bijna alle problemen te voorkomen, hoe meet je dan succes? Hoe vier je dat je geen problemen hebt?"
Bedrijven die zich aangesproken voelen tot het concept van het Fieldlab Smart Maintenance of een idee hebben voor het Techport Innovation Center kunnen zich aanmelden via www.techport.nl en partner worden. Dat kunnen zowel grote asset owners, kleine leveranciers of innovatieve specialisten zijn.