LES NOUVEAUX SYSTÈMES ABRASIFS
AIDENT A RÉDUIRE LA CHARGE DE TRAVAIL
Moins d'erreurs d'application et un plus faible pourcentage de voitures ramenées
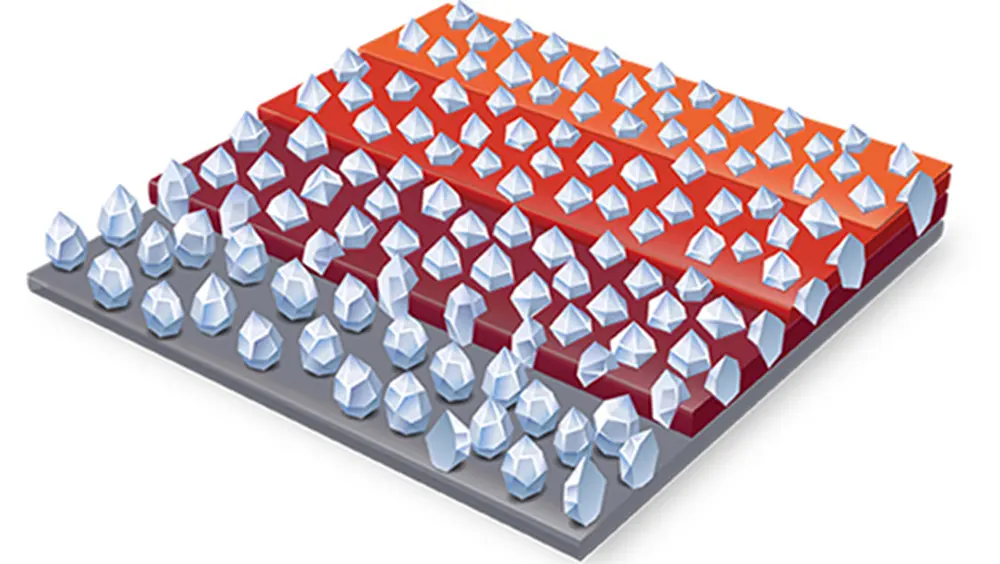
La charge de travail est élevée pour les réparateurs de carrosserie: ils doivent traiter un maximum de voitures le plus rapidement possible et il faut que ça avance! A cela s'ajoute le fait que les fabricants automobiles introduisent de temps en temps de nouveaux matériaux et finitions qui nécessitent des technologies de réparation adaptées. Mais les fabricants d'abrasifs y répondent avec des solutions sur mesure qui contribuent à alléger la charge de travail et à obtenir des résultats impeccables.
LE PONÇAGE RESTE UN ART
Pour les fabricants automobiles, le défi consiste à lancer chaque fois des nouveaux modèles qui se distinguent de manière originale au niveau de la forme, des couleurs, des finitions, … Pour cela, ils recourent à divers outils: vernis, primaires (primer fillers, gelcoat polyesters, primer coats, epoxy primer coats, revêtements à bain cathodique), plastiques (plexi), laques (anciennes et sans rayures), métaux (aluminium, acier), body fillers, composites (plastiques renforcés à la fibre de verre, composite), … Les fabricants de produits de réparation des dégâts doivent donc développer de nouvelles solutions permettent d'éliminer correctement les dégâts occasionnés à ces matériaux. Par exemple, on note depuis un certain temps une utilisation accrue de HSLA (acier haute résistance faiblement allié) et de matériaux légers tels que l'aluminium et les composites. A l'heure actuelle, toutes les voitures contiennent des pièces réalisées dans des matériaux très résistants (polymères renforcés à la fibre de verre, fibres de carbone, fibres d'aramide) qui sont destinés à amortir l'impact d'une collision. L'utilisation de ces matériaux permet d'utiliser de la tôle plus fine. Cela aide à réduire le poids sans compromettre la sécurité des passagers en cas de collision. Etant donné l'épaisseur réduite de la tôle, les méthodes de polissage et de ponçage doivent être effectuées avec plus de précision afin de maintenir l'intégrité structurelle.
Grâce aux nouveaux matériaux, le soudage par points est moins fréquent dans la carrosserie, mais l'utilisation de colle et de rivets a augmenté. L'utilisation de brasage fort et de colles combinés à des rivets exige également de nouvelles méthodes de réparation. Par exemple, l'acier haute résistance est plus sensible à la charge thermique.
NORME FEPA
En Europe, la taille de grain des abrasifs souples est indiquée selon la norme FEPA (FEPA est la fédération européenne des fabricants d'abrasifs). Le système FEPA suit la norme ISO 6344 (une norme internationale relative à la taille de grain avec des tests concernant la répartition des grains sur le papier abrasif et les abrasifs revêtus similaires). Chaque indication de grain selon cette graduation est précédée de la lettre 'P'. Le P40 est l'abrasif le plus gros, destiné à enlever beaucoup de matière, notamment au début du processus de réparation. A l'autre bout du spectre, il y a le P1500, destiné au polissage. Le diamètre de grain moyen peut être calculé simplement à l'aide du nombre qui suit le P: divisez un pouce carré (25,4 mm) par le carré du nombre qui suit le P. Dans le cas du P40, le diamètre de grain moyen est de 25,4 mm x 25,4 mm/40 x 40 = 0,4032 mm.
SYSTEME ABRASIF CLASSIQUE
De plus gros stocks
Aujourd'hui, lorsqu'on regarde l'armoire contenant le papier abrasif dans un atelier de réparation, on y trouve généralement plein de tailles de grain. Cette multitude de papiers abrasifs est liée à la méthode de ponçage traditionnelle - voir encadré. D'habitude, la plupart des réparateurs - en fonction de la nature spécifique et de la gravité du dégât - gardent quatre à six tailles de grain. Il n'existe pas de méthode de travail universelle. Certains réparateurs commencent toujours avec du P80, tandis que d'autres commencent toujours par du P100 ou du P120 en fonction du dégât. Lors d'une réparation, on ne peut pas passer plus de deux tailles de grain. Si un réparateur passe directement à du P180 après un premier ponçage au P100 - en sautant le P120 et le P150 - cela se reflétera tôt ou tard dans le résultat, par exemple après plusieurs passages au car-wash. Ce qu'on pourrait gagner comme temps en procédant de cette manière, on le perd au niveau de la satisfaction du client. Dans la pratique, un travail adéquat avec un système abrasif classique et son offre gigantesque de tailles de grain suppose plus de doigté de la part du réparateur. Et même si le réparateur maîtrise le ponçage, les gros stocks imposés par le système abrasif classique entraînent un certain fouillis. Les tailles de grain (éventuellement de différentes marques) sont utilisées pêle-mêle, avec toutes les conséquences que cela implique pour l'approvisionnement/l'administration. A cause du manque de clarté, on commande, par exemple, trop ou trop peu d'une certaine taille de grain.
NOUVEAUX SYSTEMES
Les fabricants d'abrasifs ont conçu des systèmes modulaires et compacts spécifiques permettant de travailler davantage à l'instinct afin de devoir passer moins de temps à chercher l'outil/le matériel vraiment adéquat et permettant des cycles de réparation nettement plus rapides. En tout cas, cela entraîne également un processus plus rationalisé.
Moins d'étapes de ponçage
Certains systèmes de ponçage visent à réduire le nombre d'étapes du processus. Ils sont conçus de manière à ce que le réparateur ne doive passer aucune étape (100 puis toujours 200 et 300 …), si bien que le réparateur doit moins jouer sur son évaluation/expérience, ce qui favorise toujours le résultat.
Codes couleur
Une autre manière de faciliter les choses au réparateur consiste à harmoniser techniquement les abrasifs, les pads et les lingettes de nettoyage au moyen d'un code couleur spécifique.
Les matières en mousse se voient alors attribuer une couleur, qui correspond à une certaine taille de grain.
Le jaune indique les produits pour éliminer les rayures de ponçage, le noir pour éliminer les effets d'hologramme, le blanc pour créer une finition protectrice, … De cette façon, les réparateurs savent exactement quelles pâtes de polissage doivent être utilisées avec quels pads pour effectuer des corrections de peinture. Un système simple, visuel et excluant toute erreur qui augmente la sécuritédu processus (choix de l'abrasif adéquat) et l'efficacité (moins de voitures ramenées).
Technologie de répartition améliorée
Traditionnellement, on applique, pour la production d'abrasifs flexibles, la méthode d'épandage fermé par dispersion électrostatique. Une nouvelle technologie par épandage ouvert améliore le positionnement desgrains abrasifs. Avec une couche de stéarate optimisée (pas de zinc), on obtient unrendement de ponçage qui est 20 pour cent supérieur pour un encrassement minimal et une plus longue durée de vie.
Appareils plus ergonomiques
Des robots qui effectueraient tout le travail de ponçage dans l'industrie automobile … ce n'est pas pour demain. Ceci dit, les ponceuses manuelles traditionnelles pèsent très lourd, si bien que les fabricants de ponceuses misent sur l'aspect ergonomique avec des modèles plus légers. Les réparateurs qui travaillent de longues journées et qui doivent sans cesse effectuer les mêmes mouvements de ponçage sur une surface verticale, savent apprécier ces modèles à leur juste valeur!
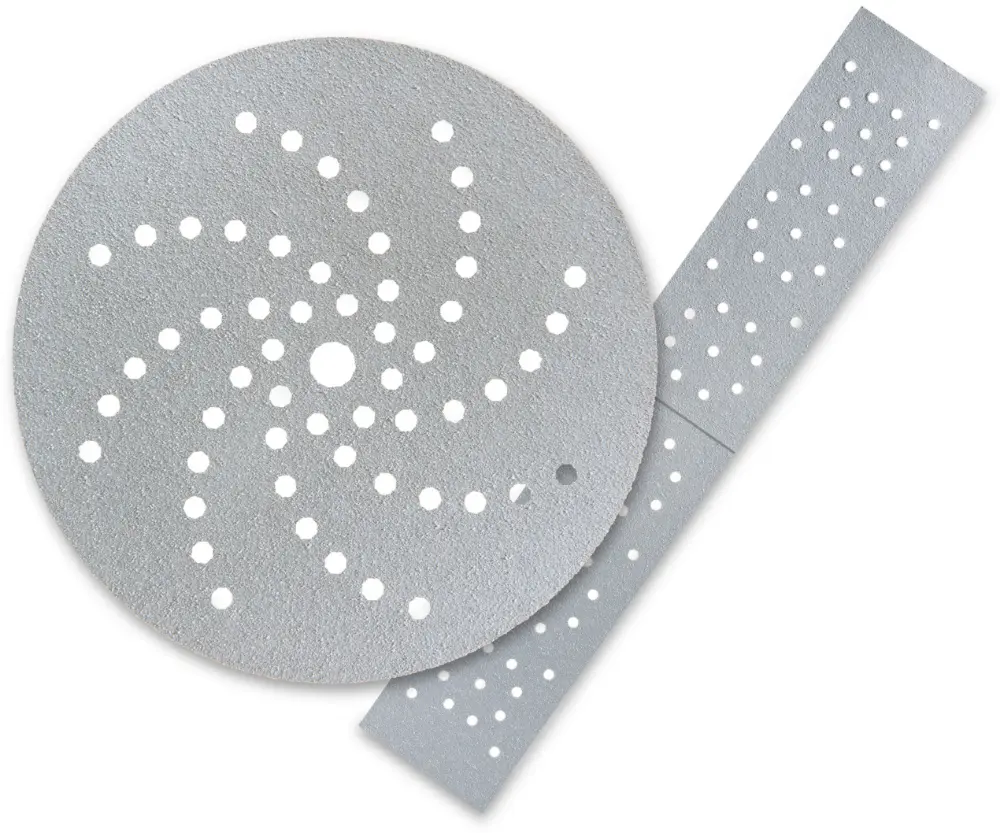
Meilleure aspiration
Une aspiration optimale est cruciale pour le résultat de ponçage. Si un abrasif est saturé avec de la poussière, non seulement cela provoque une obstruction de la machine, mais en plus, cela entraîne des dégâts sur la surface à réparer ainsi qu'une plus courte durée de vie de l'abrasif. Le réparateur a également tout intérêt à travailler dans un environnement sans poussière. Le nombre de trous, leur taille, leur position et leur forme déterminent la capacité d'aspiration. L'utilisation de la technique laser dans la production d'abrasifs permet de produire des disques abrasifs avec des trous très petits et plus nombreux. Aujourd'hui, cette technique est surtout utilisée pour la production de disques abrasifs multiperforés.
Matériel universel pour la facilité d'utilisation
De nos jours, les motifs de trous pour le papier abrasif sont conçus de manière à s'adapter sur tous les appareils du fabricant. Idem pour les bandes de papier abrasif préperforé que l'on peut découper en fonction de la taille des différents blocs manuels proposés dans l'assortiment.
Avec la collaboration de: SIA Abrasives