DES SYSTEMES DE PRODUCTION
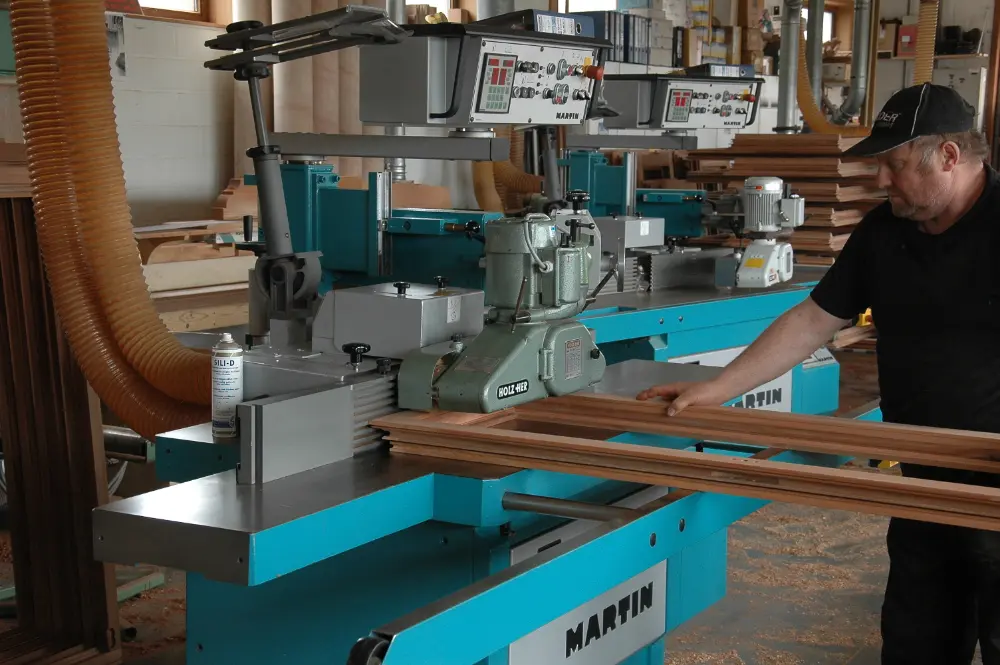
TOUPIE ET TENONNEUSE CONVENTIONNELLES
Ici, on utilise uniquement des outils en version 'MAN'. Les outils sont réglés à l'aide d'une bague de mise à zéro sur les machines: le réglage en hauteur comme la profondeur de la butée de fraisage. Par profil, on utilise un jeu d'outils sur une bague fixe. La flexibilité de profil (par ex. différentes épaisseurs de bois) est obtenue avec une simple transformation des jeux d'outils, en dévissant les outils ou en utilisant des bagues séparées au préalable. Chaque système a ses avantages et ses inconvénients. Capacité de production de ce système: env. 5 à 10 châssis par équipe. Ici, on ne compte que le travail à la machine sur la toupie et la tenonneuse. Le travail à la machine supplémentaire pour les perçages ou fraisages de ferrure n'est pas compris. Il peut varier fortement et dépend notamment du système de ferrure utilisé et des perceuses et fraiseuses disponibles. L'aspect fraisage d'ébauche n'est pas compris non plus.
CENTRE D'USINAGE A CHASSIS
Un centre d'usinage à châssis permet une production just-in-time sans empilement intermédiaire des pièces sortant de la tenonneuse. Toutes les pièces sont tronçonnées, les fraisages de tenon et mortaise et les profilages longitudinaux sont réalisés en continu. Avec la même machine, les vantaux collés (éventuellement les cadres) sont fraisés autour. Les outils sont placés sur des arbres pouvant être positionnés verticalement par des sauts fixes ou par commande CN. Si les profilés sont trop diversifiés, il faut, selon le nombre d'axes et leur longueur, ou non changer les outils de la machine, à nouveau avec des jeux fixes ou des bagues séparées. Pour monter et démonter facilement les outils, des adaptateurs spéciaux sont idéaux. Cela évite une détérioration prématurée des axes et des bagues à outils. Capacité de production de ce système: env. 60 à 80 châssis par équipe. Ici, on ne compte que les usinages à la machine, tombant sous le centre d'usinage à châssis. Avantages supplémentaires: cette capacité permet, s'il y a suffisamment d'axes, de réaliser un fraisage d'ébauche. Outre le gain de temps vu qu'il n'y a pas d'empilement intermédiaire entre l'usinage longitudinal et transversal, on gagne aussi de la place. Lors du fraisage autour, un arbre suivant fraise sans cassure. On atteint sur ces machines la capacité de production maximale lorsque tous les profilés prévus peuvent être fraisés en un seul passage et sans changements d'outils. En cas de profilés trop diversifiés, il faut effectuer une transformation et/ou un changement sur cette machine, ce qui réduit la capacité.
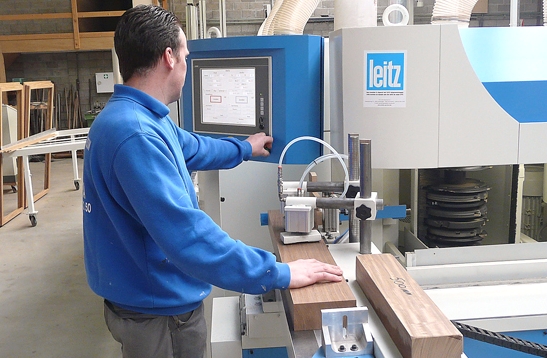
CENTRE D'USINAGE A CHASSIS AVANCE
Les centres d'usinage à châssis plus gros ont plusieurs arbres successifs. Il ne faut donc plus transformer la machine ni les outils. Ces installations sont destinées au splitting. La présence de plusieurs arbres l'un derrière l'autre permet de réaliser le fraisage d'ébauche et de finition en un seul passage. Des types de châssis variables peuvent être produits avec les mêmes outils, et donc sans changements. Il n'y a, dès lors, plus d'arrêts pour transformation. Ces machines permettent également de produire selon la fabrication de pièce finie. Une exigence importante en matière de précision: comme différents arbres doivent se positionner correctement pour fraiser un profil, la précision de re-positionnement des arbres ne peut pas excéder le faux-rond de rotation des outils (max. 0,05 mm). Les arbres peuvent se positionner de manière axiale et radiale. Capacité de production de ce système: env. 60 à 80 châssis par équipe mais avec des planifications de configuration spéciales, ces capacités peuvent être accrues. Un centre d'usinage à châssis à arbres (changeables) amovibles fait en sorte que la machine reste compacte comme un centre d'usinage à châssis conventionnel, mais offre aussi une grande flexibilité en permettant une transformation rapide via les arbres. Les centres d'usinage à châssis avec des composants CNC, par ex. un magasin à outils pour un changement d'outils automatique, tirent leur flexibilité de ces composants. Si de nouveaux profils se présentent après l'investissement, ils peuvent être intégrés dans la machine facilement via les échangeurs CNC. Aligner un magasin rotatif (échangeur) à moteur de fraisage avec des arbres conventionnels accroît à cet endroit la capacité pour le positionnement de l'outil. Un échangeur abrite plus d'outils qu'un arbre et on peut aussi les changer plus facilement. Un échangeur supplémentaire au niveau des arbres de tenonnage permet par ex. de fraiser aussi pendant le profilage transversal des onglets de parcloses, de percer des trous pour des postes intermédiaires et des lattes, de percer/fraiser des trous de poignée ou éventuellement de fraiser des palastres… Ici, il faut tenir compte du fait que les usinages de ce type peuvent ralentir la machine et donc réduire la capacité.
MACHINES RELIEES
Dans le cas de nombres de production plus élevés (niveau industriel), des machines individuelles sont reliées par des convoyeurs. Les versions initiales de bancs de profilage et de doubles tenonneuses sont configurées indépendamment de la longueur. L'usinage conjoint des pièces est réalisé en continu, par pièce.
MACHINE CNC SIMPLE A COL-DE-CYGNE
Pour pouvoir produire des châssis sur une machine CNC simple, il faut tout de même prendre quelques points en considération.
- Assemblage angulaire à réaliser? Tenon et mortaise ou contre-profilage avec goujons et vis? Selon le choix de l'assemblage, il sera parfois impossible de travailler avec certaines machines CNC. Pensez ici aux diamètres, poids et régimes maximaux que les outils doivent avoir pour ce travail.
- Le moteur de fraisage a-t-il suffisamment de puissance (kW) et est-il assez stable pour supporter les lourds usinages?
- Le serrage des pièces est-il suffisant? Nous pensons surtout ici aux éléments de serrage au lieu de ventouses. En plus d'empêcher les pièces de glisser, les éléments de serrage doivent veiller à ce qu'elles restent sans vibrations sur la machine pendant l'usinage. Des pièces mal fixées ont des conséquences néfastes: elles entraînent des cassures d'outil ou des profilages inégaux, des outils à coupes se chevauchant devant donner un résultat lisse présentent à la place des lignes (horizontales), les vitesses d'avance souhaitées ou nécessaires pour l'outillage ne peuvent pas être atteintes, etc.
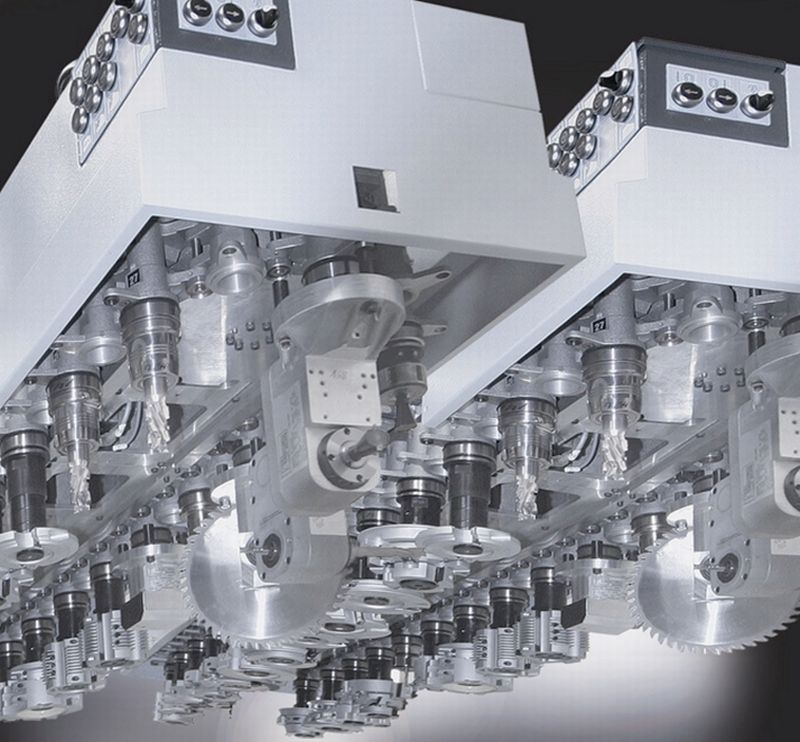
Pour toutes ces raisons, on peut dire que les centres d'usinage CNC uniquement conçus pour la tôlerie ne conviennent pas pour la production de châssis en bois.
EQUIPEMENT DE LA MACHINE CNC
Lorsqu'on travaille avec un seul moteur de fraisage, il faut tenir compte du fait que tous les usinages doivent être réalisés avec. Le splitting d'outils est possible dans ce cas mais prend énormément de temps (il faut changer après chaque usinage). Un deuxième moteur de fraisage ou groupe permet de fraiser avec splitting sans changement d'outil. Cela est le cas lorsqu'on peut travailler avec les deux moteurs en un passage. Sur ce type de machines, deux moteurs sont plutôt rares. Un magasin à outils rotatif et suivant le moteur a l'avantage de permettre des changements plus rapides mais est limité en termes de poids et de diamètre d'outils. En général, seule la moitié des places pour outils indiquées peut être utilisée. Les autres places peuvent être complétées avec des outils de perceuse ou défonceuse (petits diamètres). L'avantage des magasins à outils linéaires, c'est qu'ils permettent des diamètres d'outils plus grands et prennent moins de place dans la machine. Lors du choix de la capacité du magasin, on doit faire en sorte que le nombre de places dans ce dernier soit suffisant pour pouvoir fabriquer un type de châssis sans changements manuels.
Lorsqu'il n'y a pas de moteurs à cinq arbres, tous les usinages horizontaux comme les trous de goujons, le perçage et le fraisage pour la ferrure,… doivent être effectués avec des groupes de report d'angle. Ces groupes ne coûtent pas rien et sont limités au niveau de la puissance, de la continuité (durée de fonctionnement sans pause de refroidissement) et prennent beaucoup de place dans le magasin à outils.
En plaçant plusieurs profilages dans un jeu d'outils les uns en dessous des autres, on évite dans le cas de ces machines d'importants temps de changement. Pour cela, la machine a besoin d'un axe z suffisamment haut, d'une grande hauteur libre sous le plan de serrage et d'un poids d'outil admissible élevé.
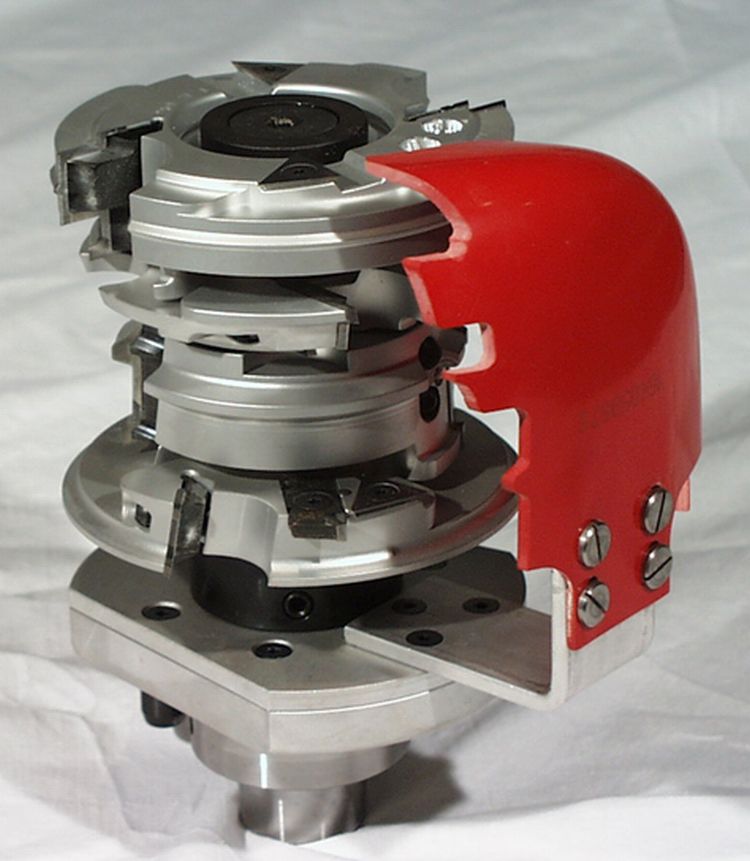
Les éléments de serrage automatiques permettent une production selon la fabrication de pièce finie. En raison de la précision exigée, il n'est pas recommandé pour ce type de production de positionner les pièces plusieurs fois contre les butées. Ici, une fabrication lors de laquelle les pièces sont serrées pendant tout le processus est conseillée. La reprise automatique du profilé par les éléments de serrage est donc nécessaire.
Une machine à système de chargement automatique peut fonctionner un certain temps de manière autonome.
Le codage par puce des outils garantit leur utilisation correcte et réduit le risque de graves dommages dus à des collisions d'outils. Sur cette puce, le fabricant d'outils consigne notamment les données suivantes: tous les paramètres de l'outil, les données de départ, la représentation, les corrections dans le cas d'outils pouvant éventuellement être ré-affûtés, le nombre de mètres courants,…
Des guide-copeaux sur l'outillage sont possibles sur les machines pour lesquelles le fabricant ne propose pas de solution intégrée. Tous deux améliorent l'évacuation des copeaux vers l'aspiration de poussière. La capacité de production possible de ce type de systèmes de production se situe autour de 15 à 25 châssis par équipe.
MACHINES CNC COMME INSTALLATION A PASSAGE CONTINU
Ici, un ou plusieurs moteurs à plusieurs arbres ou non, des broches de perçage, des groupes de fraisage, des groupes de sciage,… sont accrochés à un portique (pont) ou à plusieurs portiques alignés. Les pièces sont posées sur une table d'amenée ou introduites automatiquement, des pinces de serrage emmènent ces pièces dans la machine et les déplacent dans le sens x au-delà de l'arbre/des arbres de fraisage et de perçage. Les arbres effectuent les mouvements en y et z et, le cas échéant, les mouvements en c, a et/ou b. Nous appelons l'interpolation entre l'axe a, b et c les moteurs à cinq arbres. La manière dont les pinces de serrage se déplacent avec la pièce, sur l'axe x et/ou y, dépend de la fabrication de la machine.
Si, en raison de l'exécution ou de la construction de la machine, on ne peut fraiser qu'avec des pinces de serrage conduisant la pièce, il est uniquement possible de fabriquer via la fabrication de pièce finie. Un certain nombre de fabricants de machines proposent dès lors en guise d'option une table intégrée (comme dans le cas d'une machine CNC ordinaire). On peut donc par ex. ici fraiser une porte ou des châssis ronds avec un petit rayon moyennant une transformation éventuelle de la machine. Pour pouvoir usiner toutes les faces de la pièce, les pièces peuvent être reprises sans problème par des pinces de serrage se trouvant à l'opposé. Il va de soi que plus il y a de moteurs ou groupes pouvant travailler en une ligne, plus la machine sera efficace (rapide). Le concept peut également être étendu avec des doubles tables ou rangées de pinces de serrage. Plusieurs pièces peuvent de cette manière être usinées simultanément sur la machine et on peut tout de même commencer à penser en termes de travail en série avec cette machine flexible, ce qui est souhaitable pour un usage industriel. Contrairement à la production par cadre de fenêtre, on peut ainsi retenir des pièces similaires ensemble et les finir successivement sur la machine. A la sortie, les pièces doivent à nouveau être triées. Cela peut se faire via un code-barres gravé ou imprimé sur les pièces. Des tampons peuvent également trier les pièces automatiquement. Un deuxième portique peut doubler la capacité. La capacité de production possible de ce type de machines varie fortement car leur construction est adaptée aux attentes de l'acheteur. En alignant plusieurs unités, on peut facilement produire jusqu'à plus de cent châssis par équipe. En moyenne, on peut fabriquer par portique avec deux moteurs env. 25 à 35 châssis par équipe.