human-made climate change: is Co2 the problem?
Nova: the renewable carbon initiative
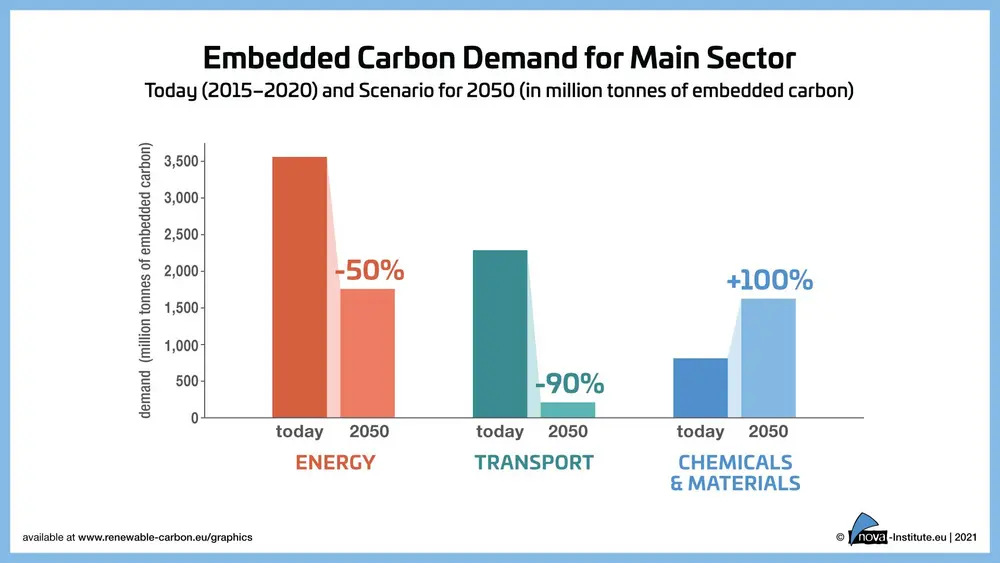
What is the primary cause of human-made climate change? The usual answer is: CO2 and other greenhouse gases. But is CO2 really the core of the problem? Recent climate data indicate that 72% of anthropogenic climate change stems from extracted fossil carbon from the ground, [1] while the other 28% comes from agriculture and forestry. [2] Presenting the first part of the new Intergovernmental Panel on Climate Change (IPCC) report in August 2021, UN Secretary-General António Guterres warned that fossil fuels are destroying the planet, and that the report "must ring the death knell for coal and fossil fuels". [3]
The core issue
CO2 is not at the core of the climate problem, it can actually be cycled between atmosphere, biosphere and technosphere. Instead, the core issue is the additional fossil carbon (oil, gas, coal) taken out of the ground, which is utilised in our technosphere and ultimately released in the atmosphere or environment. In order to mitigate climate change and achieve greenhouse gas emission reduction targets, the excavation of additional fossil carbon must be reduced as quickly as possible and in high volumes. For the energy and transport sector, this means a vigorous expansion of renewable energies, hydrogen and electromobility, the so-called decarbonisation of these sectors. But the chemical and material industries also have a high demand for carbon and are essentially only possible with carbon-based feedstocks. Unlike energy, these sectors cannot be "decarbonised". With decreasing carbon demand from energy and transport and increasing demand from the chemical and materials sector, the structure of carbon demand will change fundamentally – both sectors might be almost equal in 2050 (cf. Figure 1) based on foreseeable developments in the energy, transport and chemical & materials sectors.
The Renewable Carbon Initiative (RCI) was created end of 2020, and is today an interest group of roughly 40 well-known companies from the chemical and material value chains. The initiative aims to support and speed up the transition from fossil carbon to renewable carbon, which is carbon from biomass, direct CO2 utilisation or recycling, for all organic chemicals and materials. This way, the RCI addresses the core problem of climate change, which is extracting and using additional fossil carbon from the ground. An often-overlooked part of the carbon footprint of chemicals and polymers, the majority of the total carbon footprint often comes from the carbon bound in the molecular structure of the chemical or polymer (cf. Figure 2).
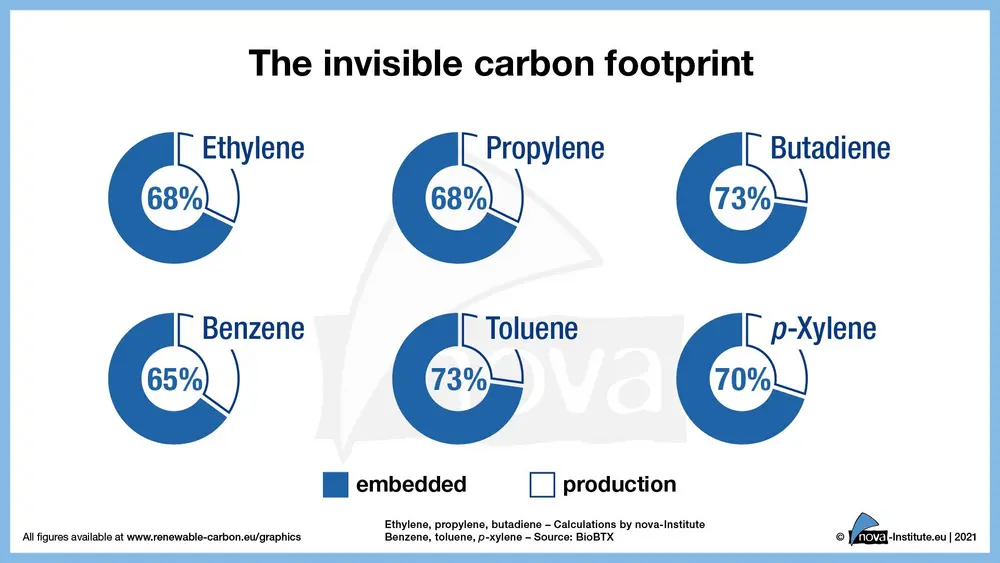
The vision of the RCI is that by 2050, fossil carbon shall be completely substituted by renewable carbon. The initiative is convinced that this is the only way for chemicals, plastics and other derived products to become more sustainable, more climate-friendly and part of the circular economy. The RCI aims at fostering networks among its members and building new value chains to replace fossil carbon with renewable carbon. Since its launch, the initiative has been busy raising awareness, preparing reports, fostering networks and reaching out to industry, policy and the public.
Global carbon demand today
Global demand for embedded carbon in chemicals and derived materials is around 450 million tonnes (Mt) per year (cf. Figure 3). 85% of this demand is today supplied by fossil-fuel-based resources, 10% by biomass and only 5% by recycling, meaning so far only 15% are renewable.
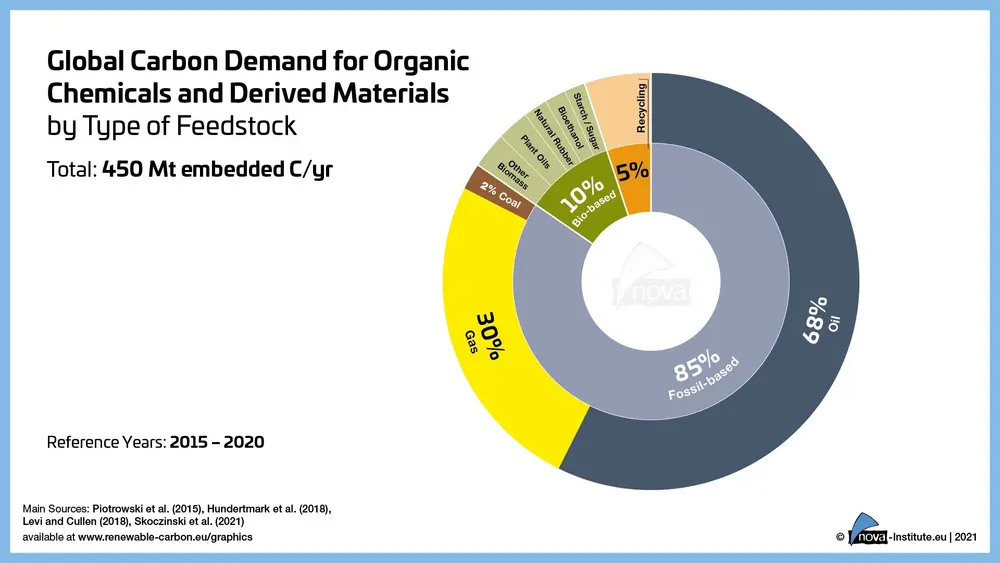
Increasing population, higher incomes and a growing middle class will drive the demand for products and thus also for carbon – already considering increased material efficiency and changes in personal behaviour. By 2050, demand for embedded carbon in chemicals and materials might increase to 1,000 Mt per year. The renewable carbon supply will have to be increased by a factor of 15 until 2050 to cover the needs of the chemical and material sectors without additional fossil carbon from the ground. This complex transformation will require cross-sector collaboration from industry, governments and consumers through a harmonised carbon management.
We must ring the death knell for fossil feedstocks – not only in energy and transport, but across all economic sectors
options to replace fossil solutions
The last few decades have given rise to multiple technological pathways that replace fossil carbon with sources of renewable carbon: biomass, direct CO2 utilisation (from industrial flue gases or the atmosphere), or mechanical and chemical recycling. The renewable carbon strategy unites these sources and provides companies with a framework for future investments by creating sufficient space to operate. For the first time since the industrial revolution, technology allows us to decouple chemical, plastics, fibre and other material industries from the use of fossil carbon. This is a fundamental game-changer, which inherits the potential for significant impact on climate protection since most of the embedded carbon in global commodities and consumer goods finds its way into the atmosphere. In the following, we want to provide some of the many existing examples of chemicals, materials and products from renewable carbon.
CCU-based fuels and chemicals
LanzaTech is a global leader in gas fermentation technology. The company provides novel and economic routes to ethanol, jet fuel and high-value chemicals from gas streams including industrial off-gases; syngas from any biomass resource and reformed biogas. The carbon recycling technology is like retrofitting a brewery onto an emission source, but instead of using sugars and yeast to make beer, pollution is converted by bacteria to fuels and chemicals. LanzaTech's unique microbial gas fermentation process provides a sustainable pathway to produce platform chemicals that serve as building blocks to products that have become indispensable in our lives such as rubber, plastics, synthetic fibers and fuels. The company's technology solutions mitigate carbon emissions from industry without adversely affecting food or land security.
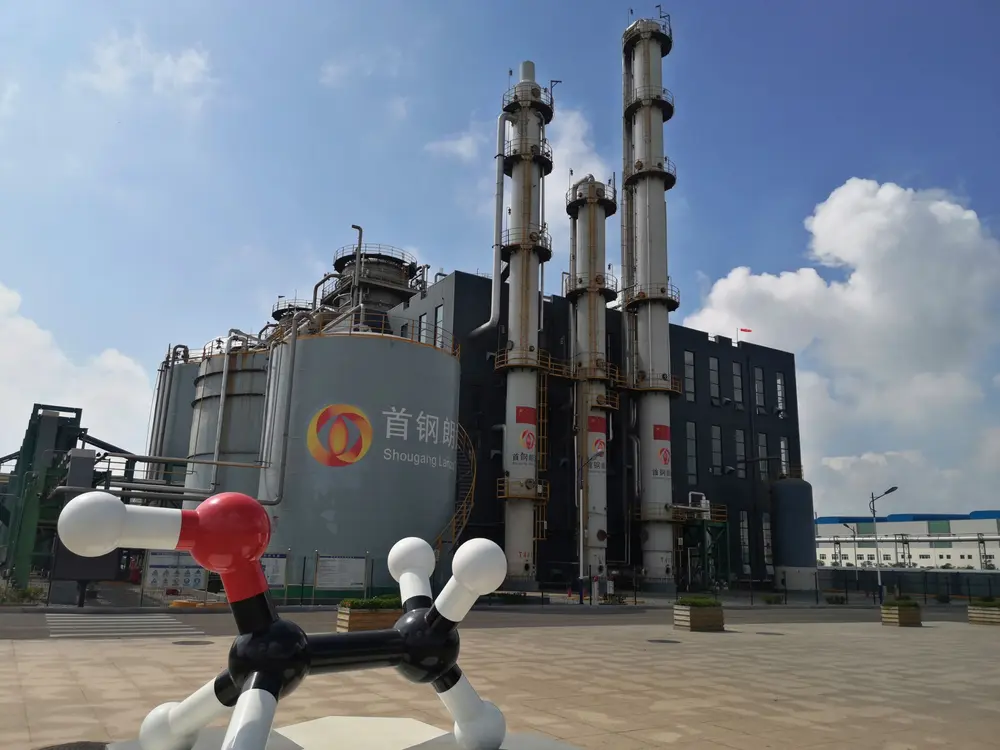
LanzaTech's technology has been demonstrated at five industrial sites with over 50,000 hours of operation using steel mill waste gases (BlueScope Steel, NZ; Shougang Steel, CN; BaoSteel, CN; China Steel, TW) and approximately 50,000 hours using syngas from industrial MSW gasification (Sekisui, JPN). LanzaTech has two commercial facilities operating in China with Shougang Steel and additional commercial facilities are in the pipeline globally using a range of feedstocks. Together with RCI member Unilever and India Glycols Limited, surfactants made from recycled carbon were used for the first time in a laundry capsule and dish soap launched in 2021. In addition, ethanol made from steel mill emissions was converted to monoethylene glycol and used to make PET for production of packaging for Mibelle and Migros in Switzerland and dm in Germany and was also spun into polyester for production of dresses by Zara.
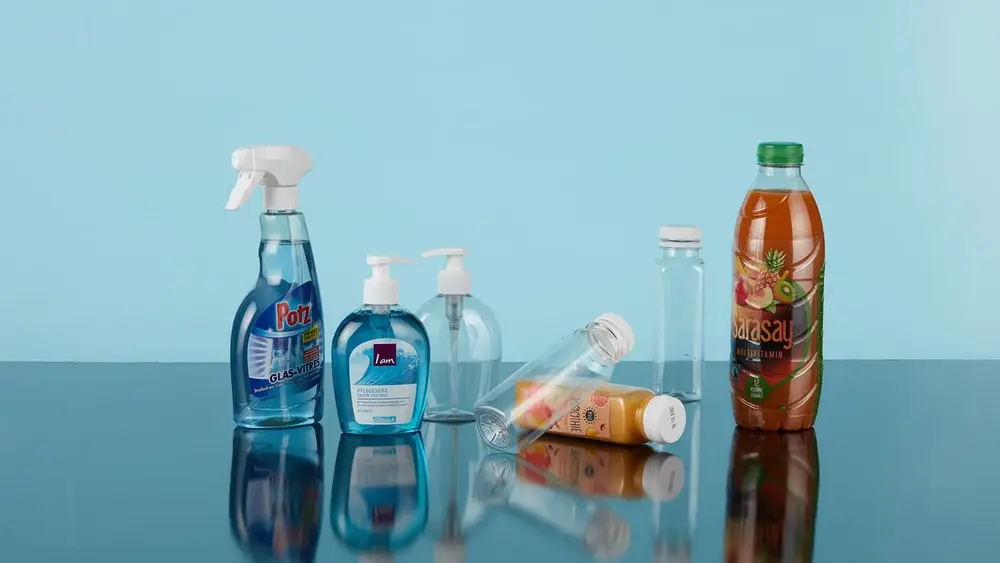
Wood-based biochemicals
UPM-Kymmene Oyj is a Finnish forest industry company, and one of the founding members of RCI. UPM has committed to innovate beyond its traditional stake in pulp, paper, plywood and timber to extend the forest value chain into renewable materials. After entering the advanced biofuels business with a biorefinery in Lappeenranta, UPM is now in the process of finalizing the world's first biorefinery to convert wood to renewable chemicals in Leuna, Germany. The chemicals produced at the Leuna biorefinery will enable a switch from fossil raw materials to sustainable alternatives in various consumer end-uses and the investment opens totally new markets for UPM with large growth potential for the future.
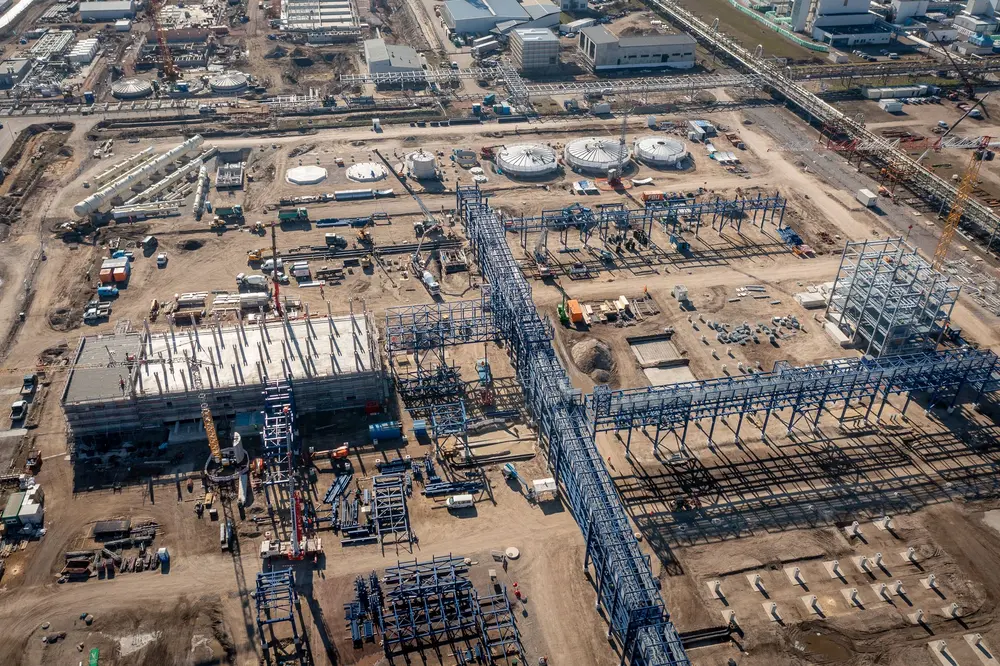
At its Leuna biorefinery, UPM Biochemicals will convert sugars taken from regionally sourced, certified beechwood to renewable monoethylene glycols (bMEG), ready to be used as a substitute for crude oil-based MEG in consumer products such as PET-packaging, Polyester based clothing or coolants for e.g. automotive end-uses. UPM's bMEG is ready to be used in existing recycling processes and helps taking the circular economy to the next level – renewable circularity.
The chemical industry is built on carbon – it can not be decarbonised, but instead needs to be defossilised
The beechwood's lignin, a 100% bio-based substance that can be found in the cell walls and which is the glue that provides compressive strength to wood and makes cell walls water repellent and durable, will be converted to renewable functional fillers (RFF) in Leuna. RFF are a complete new sustainable category of performance chemicals, replacing highly CO2-intense carbon black and precipitated silica in rubber and plastics applications such as hoses, seals or thermoplastics.
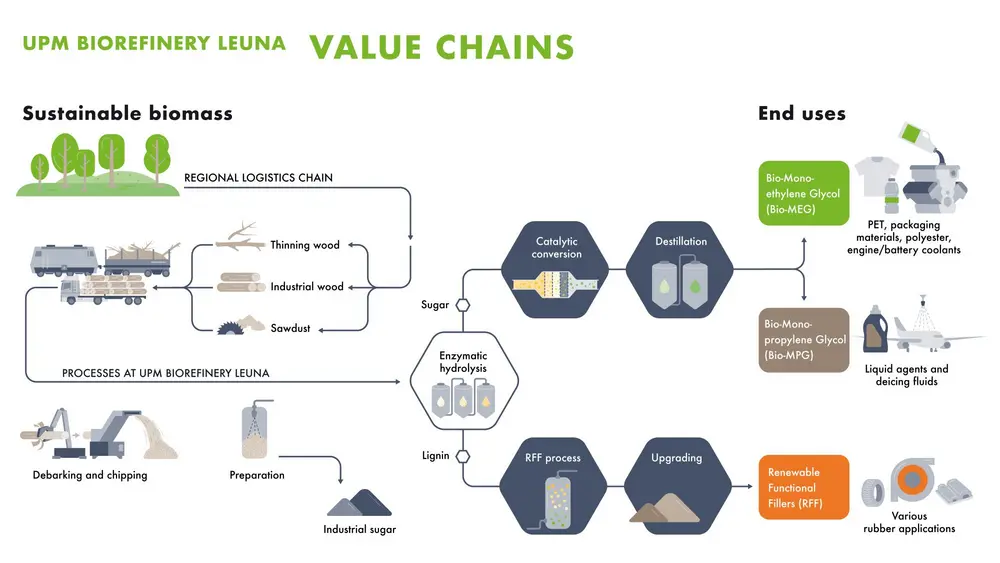
Leuna is the first industry scale biorefinery for second generation biochemicals. It's heavy focus on regional supply chains and a strong commitment to go beyond the CO2 negative feedstock and also optimize the environmental performance of the entire production process make it a lighthouse project for a renewable carbon economy.
PEF: A novel bio-based polymer with improved properties
Avantium, a Dutch pioneer in renewable and sustainable chemistry, has developed a technology to convert plant-based sugars into FDCA (furandicarboxylic acid), the building block of PEF (polyethylene furanoate). PEF is a 100% plant-based plastic material, made from sugars derived from plants. PEF has enhanced barrier, provides high recyclability, and has mechanical and thermal properties compared to today's widely used petroleum-based polymers. The barrier properties of PEF, which are approximately 10 times better for O2,15 times better for CO2, and 2.5 times better for water than PET, represent a revolutionary opportunity compared with traditional packaging solutions regarding performance, price, and sustainability when produced at scale 1.
The sugars (fructose) required to make FDCA can be produced from agricultural crops, such as wheat, corn and sugar beet. When fully technologically developed, PEF can also be produced from cellulose, which is abundant in non-edible biomass, such as agricultural and forestry waste streams. The current process utilises starch from European wheat. FDCA is polymerised with plant-based mono-ethylene glycol (MEG) to make a 100% plant-based PEF polymer. Avantium has successfully demonstrated this YXY® Technology in its pilot plant in Geleen, the Netherlands. In December 2021, Avantium has taken a positive investment decision concerning the construction of the world's first FDCA Flagship Plant in Delfzijl (the Netherlands), with construction planned to be completed by the end of 2023 and the aim to be operational in 2024.
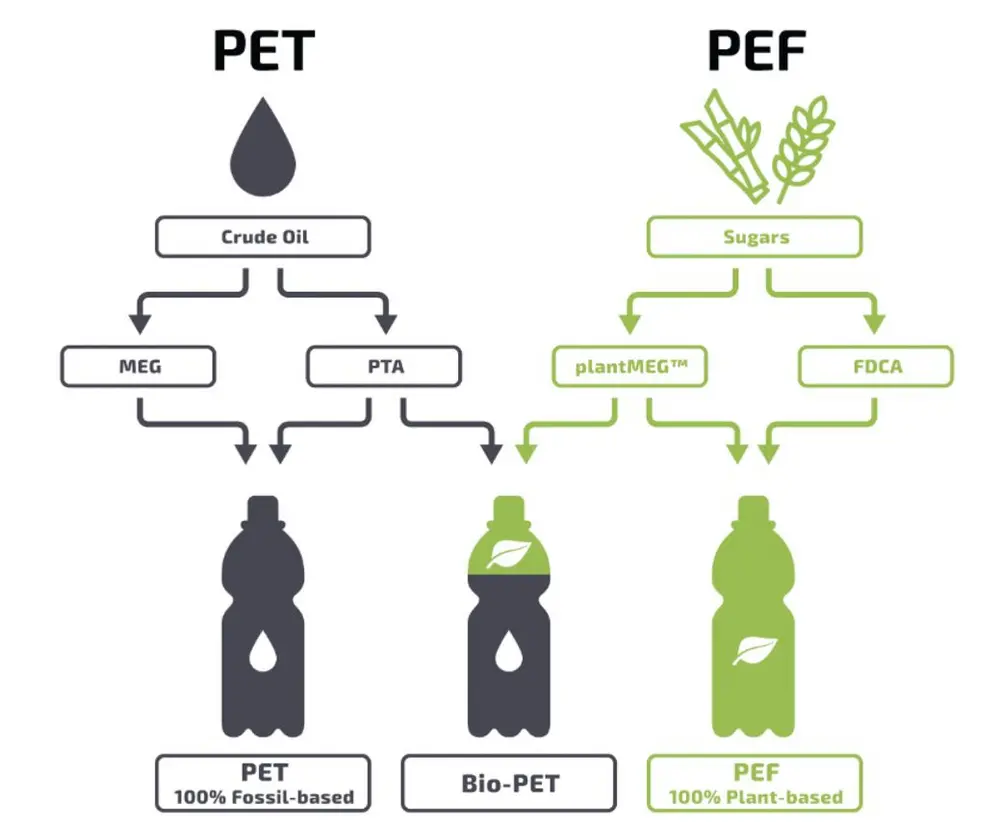
Textiles from chemical recycling
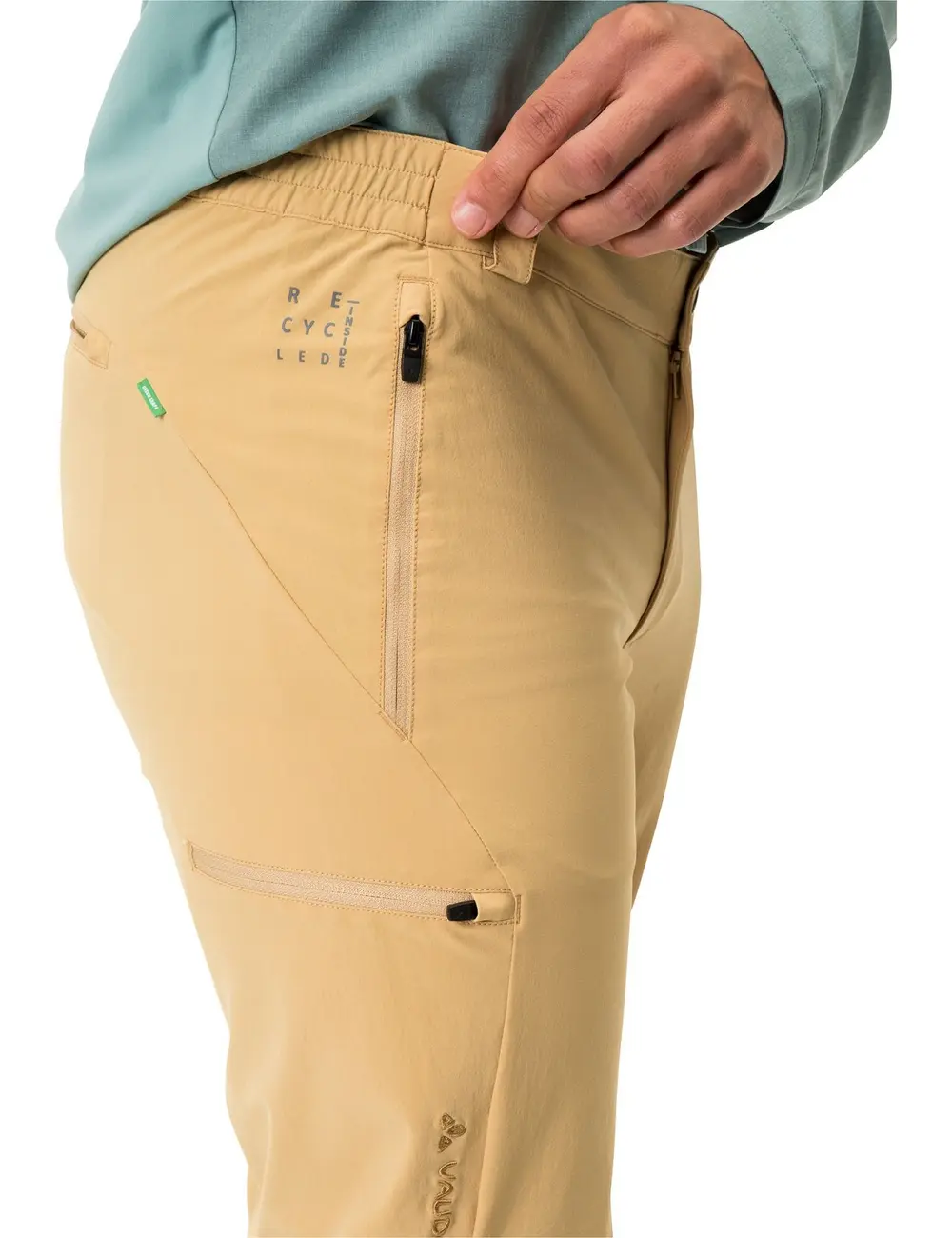
New pants based on recycled end-of-life tires: a new product line of pants from the outdoor apparel company and RCI member VAUDE will be available in stores from March 2022, made from chemically recycled material called Ultramid® CcycledTM. These pants are based on renewable carbon as they are derived from chemically recycled scrap tires used as a raw material. Working together with another RCI member, BASF feeds pyrolysis oil from end-of-life tires into its production Verbund in Ludwigshafen, and in doing so partially replaces fossil resources. The share of recycled raw material is assigned to certain products manufactured in the Verbund using a certified mass balance approach. As products with "CcycledTM" in their name have exactly the same properties as the equivalents made from fossil raw materials, customers can process them in the same manner and use them in their conventional processes. Accordingly, they can also be used in applications with high quality and performance requirements, such as in the textile industry. Vaude states that using "CcycledTM" products, they can reduce the carbon footprint by more than half, according to the HIGG Material Sustainability Index.
Renewable carbon is the concept that enables the chemical and material industries to become an important part of a sustainable future – and it can originate from biomass, CO2 utilisation and from recycling. As a guiding principle, renewable carbon enables the industry to think out of the box of established boundaries and stop the influx of additional fossil carbon from the ground. In February, the RCI published a fundamental strategy paper on the defossilisation of the chemical and material industry with eleven policy recommendations, which can be found here: https://bit.ly/3rqyejJ.
Are you interested to learn more about the RCI, their upcoming plans or how to join the initiative? Take a look at www.renewable-carbon-initiative.com or reach out directly to the executive managers Michael.carus@nova-institut.de or Christopher.vomberg@nova-institut.de.
[1] A glossary of many renewable carbon related terms can be found at https://renewable-carbon-initiative.com/renewable-carbon/glossary/
[2] Based on data from https://www.pbl.nl/sites/default/files/downloads/pbl-2020-trends-in-global-co2-and-total-greenhouse-gas-emissions-2019-report_4068.pdf
[3] https://www.un.org/press/en/2021/sgsm20847.doc.htm
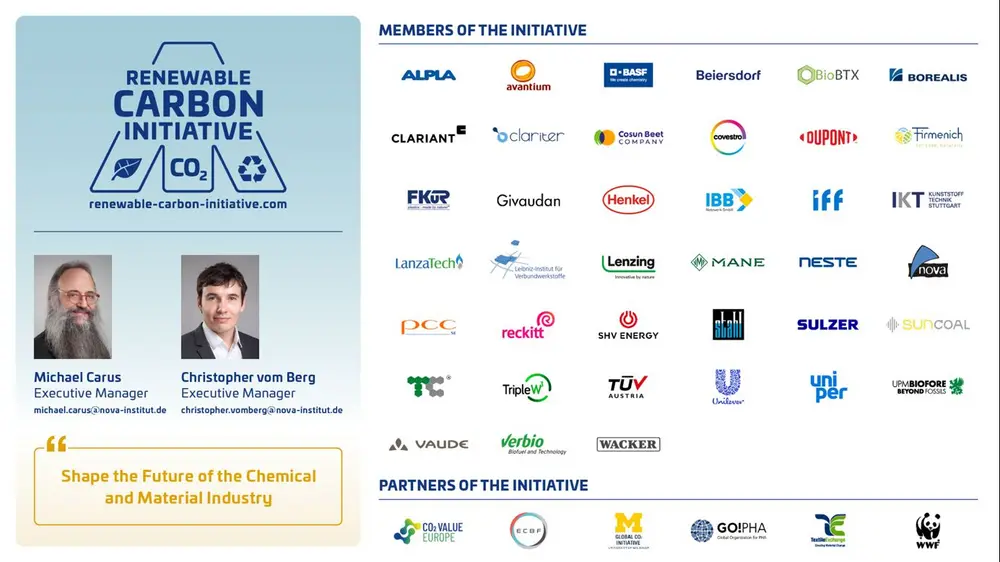