Economical design approach for an industrial steam heat pump
potential for high temperature mechanical vapour recompression (MVR) as electrification investigated
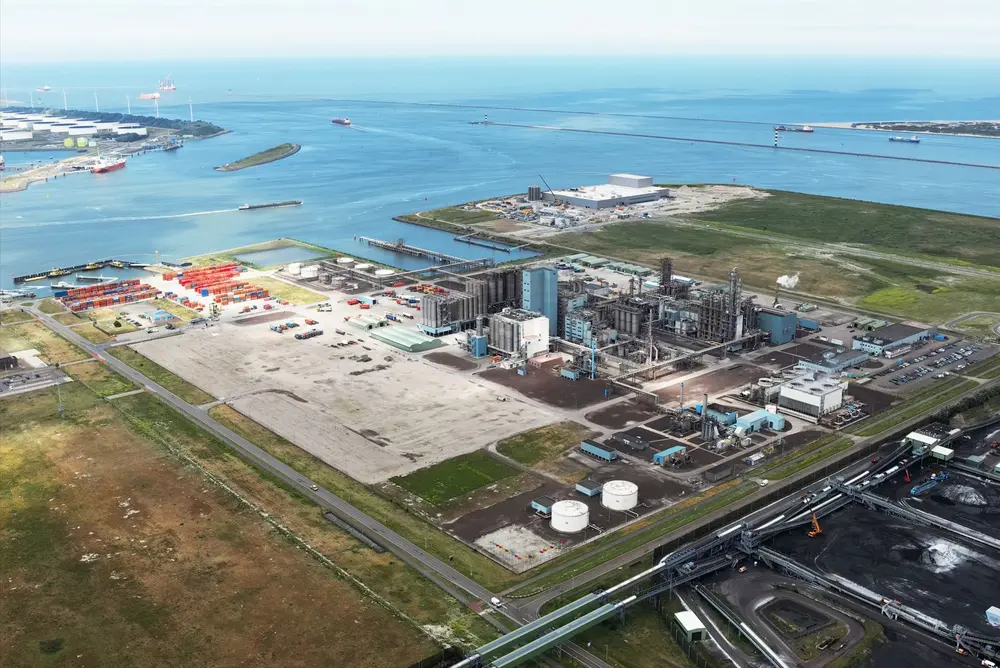
Recently Indorama Ventures Europe B.V. and BlueTerra Energy Experts B.V. have performed a study to investigate potential for Mechanical Vapor Recompression (MVR) as electrification and (partial) replacement for natural gas-fired utility steam generation. The interesting findings of this study show how a design for high-pressure steam MVR may become feasible.
The cases presented in this study are fiction, but using the steps for design as presented here, could be of benefit to many industrial companies that have waste heat available of sufficient amount and temperature, and want to decarbonize their steam supply on site. Due to rising CO2 emission costs the high-temperature open steam heat pump faces a positive trend in better payback.
Background and conceptual improvements
Mechanical Vapor Recompression as heat pump
Mechanical Vapor Recompression is the compression of a vapor, by means of a mechanical compressor. MVR of steam is an industrial technology for the recovery of heat energy and steam, applied at lower pressures for decades.
This study shows how higher pressures of steam may become feasible. By compressing a vapor, the density, pressure and temperature rise. This enables the reuse of the heat at a required temperature level.
The compression energy needed to upgrade an amount of heat is expressed as the coefficient of performance (COP).
In which:
QH is the heat output of the heat pump
W is the work needed to drive the compressor
As a result of the compression, the temperature rises. Then, the superheated steam is quench-cooled by water injection.
In Figure 1 it becomes clear how relatively small the part of compression work is, compared to the latent heat of evaporization. The evaporization from point 1-2 crosses the most isenthalp lines, and the desuperheating from 3-4 recovers heat by converting degrees superheating to more steam from quench water, so the net compression work is only a part of the isenthalps crossed during compression line 2-3.
Conventional applications of MVR have smaller compression ratios. At these compression ratios and efficiencies some typical COPs of MVR applied with a small temperature lift have higher efficiencies. Typically, when the temperature lift is low, higher COPs can be achieved. For a HT-heat pump to have a better COP and high delivery temperature it is important to have a waste heat source of a higher temperature.
In comparison with compression heat pumps, existing MVR applications show a higher performance and MVR can reach higher output pressures when using waste steam as a heat source. Where closed compression heat pumps are able to reach outlet temperature up to 160 °C supply temperature [1].
Current state-of-the-art Stirling closed cycle heat pump reaches steam conditions of 10 bar was reported by [2], MVR is capable to reach end pressures of 40 barg or higher, with a corresponding end temperature of about 260 °C, even at an acceptable COP when the design approach in this paper is adopted.
Steam grid cascading
In chemical industry, it is common that a steam boiler produces steam at the highest pressure and temperature that is necessary. Then other processes that require lower temperatures are supplied with steam that is expanded by a reducing station (a letdown valve).
After the use of the steam, condensate of high pressure is reduced in pressure in a flash vessel for each pressure level, whereby extra steam of lower pressure is created. By reducing the steam to several pressure levels, and flashing condensate, a cascade of steam grid pressures is created.
Multi-stage heat pump concept
In general, when a heat pump is applied, it consists of a compressor with fixed input and output pressure level. When the heat pump produces higher compression ratios the COP also decreases.
However, the cascading of steam grids in industry implicates that not all steam has to be compressed to the highest pressure. Therefore, the compressor may be split up in several compressors that each have their own dedicated end pressure. The compression to lower pressures is beneficial for power consumption and therefore the overall COP will increase.
Decrease temperature lift
A compression heat pump that uses the ambient air as a heat source is, in general, limited in delivery temperature, because the coefficient of performance decreases with the increase of the delivery temperature. The temperature lift and the absolute delivery temperature level is dependent on the working fluid used in the compression/expansion cycle. When considering the possibilities for the implementation of a MVR heat pump, it is important to look for waste heat sources in the plant to feed the heat pump.
Interstage condensate cooling
Usually compressors for dry gases, for example an air compressor, need interstage cooling. Conventionally, the gas streams are cooled by means of a heat exchanger that operates with cooling water or air. In the case of a multi-stage steam compressor, the interstage cooling is realized by injecting boiler feed water. This water vaporizes and becomes steam, mixed with the compressed steam. This way, the compression heat is not lost, but converted into steam as a product.
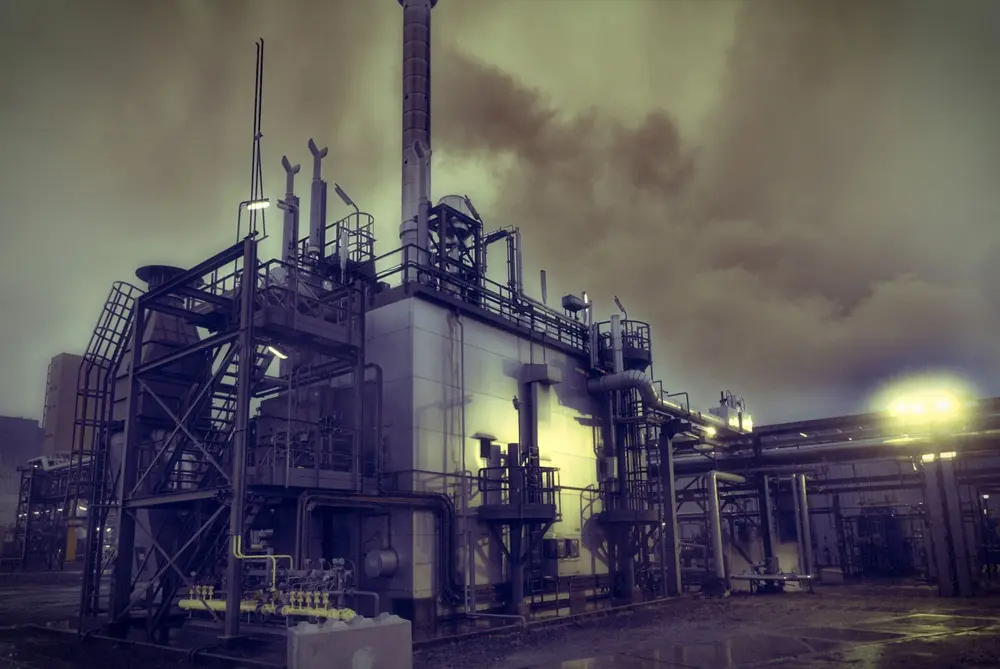
Technical design approach
Introduction
This chapter describes an ASPEN+ simulation of a multi-stage heat pump mass balance for a cascaded steam grid.
In the simulation, the grid pressure is 40 barg. Two ASPEN simulations were performed. One simulation with steam produced with a MVR heat pump where all steam is compressed to the highest pressure. In the second simulation, the steam is divided over several pressure grids, lower than 40 bar and one with 40 bar.
40 barg MVR-concept
In the 40 bar scenario the total steam demand of 60 t/h is produced at one pressure level; the consumers receive steam at the required pressure level via pressure reducing stations. The total steam production is defined here as the sum of all consumed steam by consumers.
The annual expenses for natural gas are derived based on conservative gas prices so the MVR advantage will also be conservative. In this case a gas price of 45 euro per MWh for industrial plants is adopted. For the annual CO2 costs a CO2 price of 90 euro per ton is adopted. Electricity is considered to be around 105 euro per MWh.
If all the steam of 60 ton per hour is compressed to 40 bar from the same starting pressure in one step, and the steam is distributed by pressure reducers like as in a conventional boiler system, the coefficient of performance is low, due to high average temperature lift and pressure ratio.
The following situations were simulated in Aspen and show the electricity consumption in such a case.
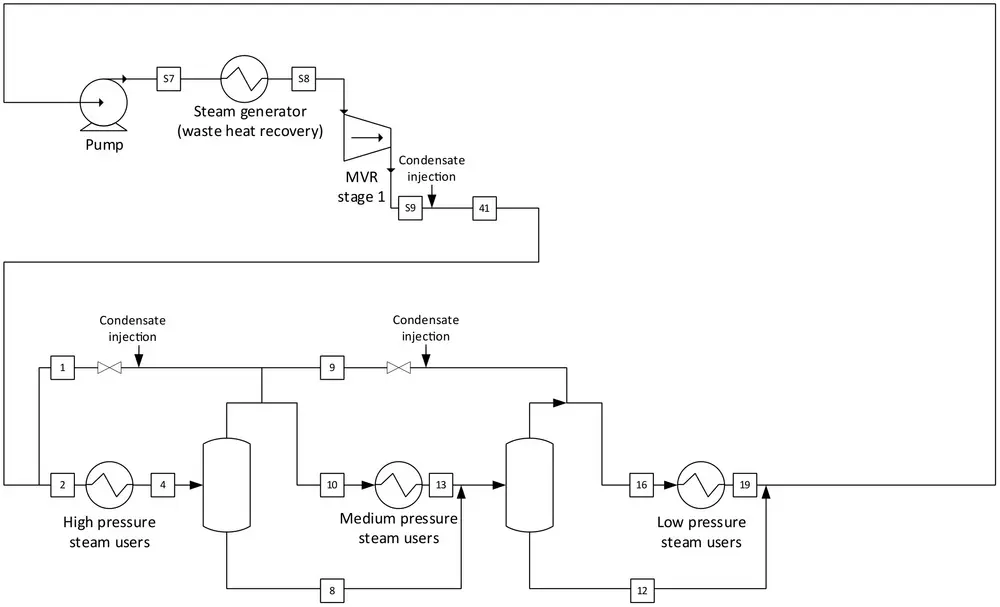
The process conditions are shown in Table 1:

Alternatively the steam is not generated at the highest pressure level only, but at several grid pressure levels. This is depicted in the following flowsheet. The highest grid pressure is also 40 bar and the total amount of steam remains the same as in the first case. A part of the total flow of steam is not compressed all the way to 40 bar and delivered at the pressure of each individual steam user grid.
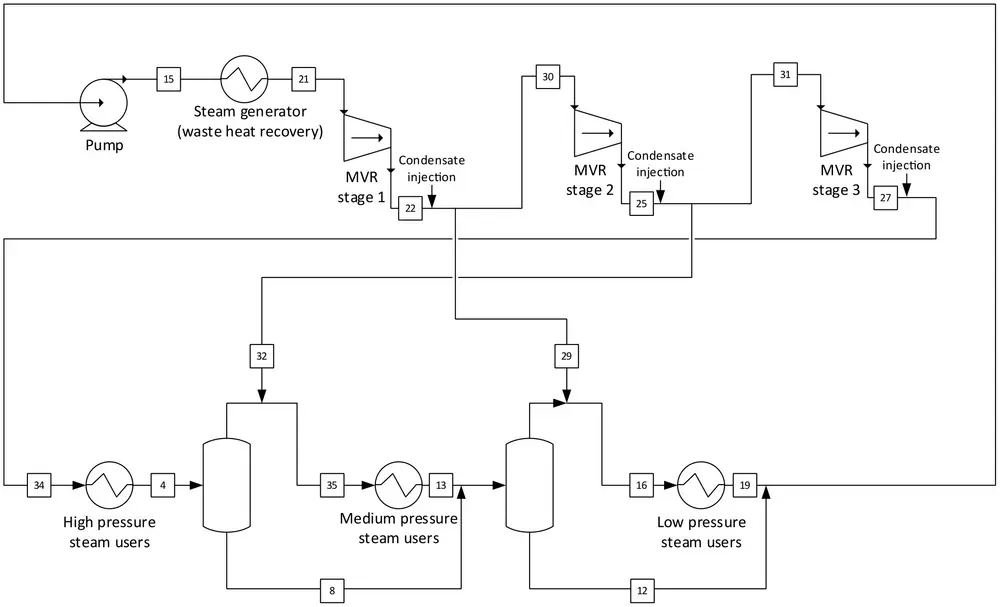
The process conditions are shown in Table 2:

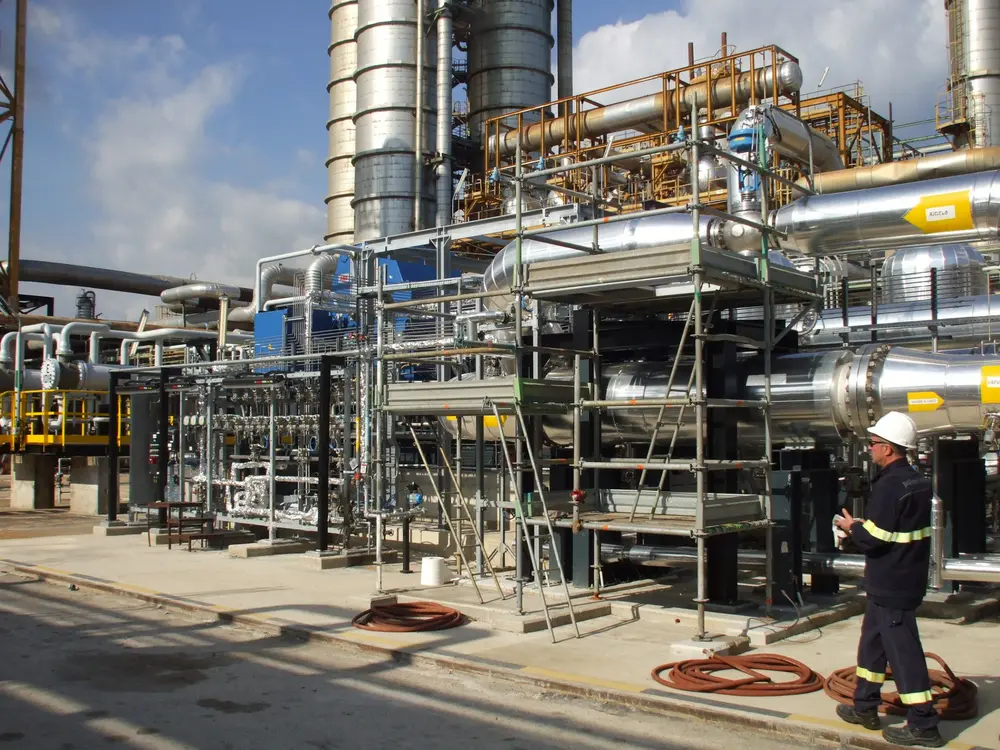
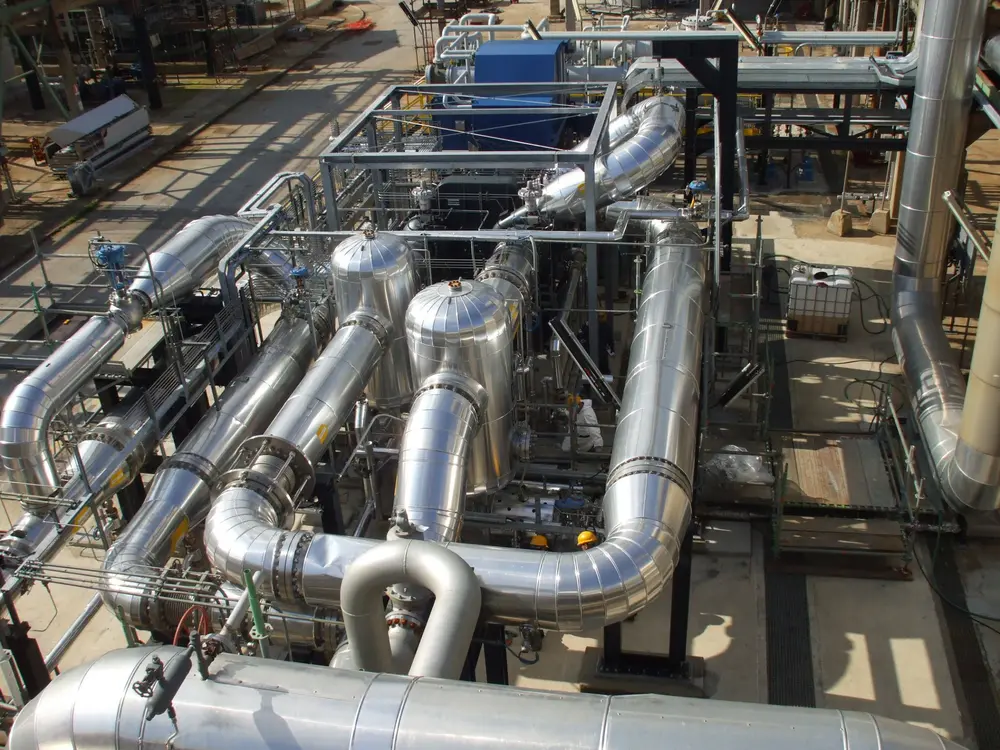
Economical feasibility analysis
MVR Capex
The capital expenditures (CAPEX) of the MVR heat pump project were estimated using the Lang factor cost estimation method [3] and indicative equipment costs. The Lang factor is an average database factor of similar projects. The Lang factor formula is as follows.
In which:
Capex = the total project cost
Cprocess eq = the sum of all indicative process equipment costs
fL= Lang factor
For these types of processes to quickly investigate feasibility in a brownfield environment, the factor 5.2 is common. This factor is a sum of subfactors described by [5]. The factor was obtained from table 6.1, chapter 6 of [5]. The result of the estimate of the capex is summarized in Table 3.
The Capex for both options (refer to par. '40 barg MVR-concept') is at the same level. For multi-stage compression the same multi-stage turbocompressor can be applied as for the concept with one high (40 barg) end pressure.

MVR feasibility comparison
In this chapter, we present feasibility analyses for compression to one high pressure and pressure divided scenario of 40 bar end pressure. For the calculations, we used conservative, low energy prices and these do not represent the actual prices.
The following table presents an overview of annual costs of the 'all to high pressure' and 'pressure divided'. The compressor is the same for both situations, however the pressure divided has several side streams in between the stages. Total cost of equipment consists of steam generators, pumps, compressor, desuperheaters and knock-out drums.
Cost effectiveness of CO2 reduction
In order to be able to compare technologies on their effectiveness in terms of abatement costs, below formula is used.
A standard way to define cost effectiveness for CO2 abatement technologies is to calculate all annual costs, minus all annual benefits of the technology, and subsequently divide by the avoided CO2 emission per year. Doing so, the annual costs per ton of CO2 are calculated. As will be shown, MVR will have negative costs and is therefore actually saving money per ton of CO2 as compared to continue emitting CO2. Usually, for such projects the capex may be a loan, where a discount rate should be applied. A capital recovery factor (CRF).
In which:
kd is the annual real debt interest rate usually (8-10%)
kinsurance is the annual interest rate (1%)
n is the depreciation period (20 years)
The levelised cost of abatement (LAC) of CO2 emissions is expressed in the same manner as levelised cost of electricity [4]. The annual costs for the evaluated technology are divided by the abated amount of tonnes:
In which:
CRF*Cinv the annual costs for the investment
CO&M the annual operation and maintenance cost
Ce the annual electricity cost (mainly to operate the MVR-compressor).
Ssteam the annual savings on steam (being indirectly reduced natural gas costs when MVR is applied)
SCO2 the savings on CO2 tax
CO2net the annual abated tonnes of CO2.
The cost effectiveness for the 40 bar ‘one end pressure’ case B is as follows using the data from Table 4:
Annual investment costs = 4.9 M euro
Annual operation and maintenance = 0.6 M euro
Annual electricity cost = 4.7 M euro
Annual steam / natural gas savings = 8.0 M euro
Annual CO2 savings (60 euro per ton tax) = 3.8 M euro
Annual scope 1 CO2 mitigated = 63.8 kT CO2/yr
Using the formula above this yields 44 euro savings per ton saved CO2 as compared to business as usual and paying tax for emitted CO2. This means that the MVR technology is competitive and more attractive than paying EU-ETS carbon taxes. The same conclusion applies for CCS-technology based on amine sorbent in comparison with MVR; the cost per ton CO2 is approximately Euro 80, whereas MVR technology results in savings for every ton CO2 emission.
Conclusion
In this paper we described a design approach to realize industrial heat pumps for steam generation (MVR) with exceptional high temperatures (>260 °C) and acceptable payback. The scenario’s have high carbon reduction potential.
The high temperature MVR concept has, contrary to most carbon capture technologies, a strong benefit in comparison with EU-ETS (depending on local parameters) per ton CO2 reduced. The COP and feasibility depend on several factors, that vary for each individual situation.
Also the pressures used in this study can be reached by compressors on the market, but as of yet no references above 17 bar end pressure are known to the authors which may hamper further deployment in industry. The results of this study may therefore provide insight to take next steps needed for MVR in order to become a more widely accepted industrial decarbonisation technology.
Key elements for the design approach in order to achieve short paybacks are the following:
- Limiting the temperature lift (by for instance using a waste heat source to boost the inlet temperature of the MVR)
- Distribute the total steam amount over several required pressure levels, in order to increase the COP
- The open heat pump construction saves a condenser and therefore the efficiency and capex are improved to closed cycle heat pumps.
- The open heat pump makes use of proven technology and therefore the investment costs are lower compared to closed cycle heat pumps.
- The injected quench water boost the steam output.
Waste heat valorisation by means of MVR is a powerful tool for carbon emission reduction, even in brownfield application. Secondly, thermal pollution to the environment (water, air) is reduced.
Disclaimer
The presented business case in this article is purely hypothetical, and has no reference to the situation at Indorama. The hypothetical feasibility study as described here has the sole purpose of demonstrating a design approach, to be able to explore opportunities and become aware of the potential of MVR technology.
References
[1] Verdnik, M., Rieberer, R. Influence of operating parameters on the COP of an R600 high-temperature heat pump. International journal of refrigeration 2022
[2] Olvondo high lift 2022 HighLift | HighLift by Olvondo Technologydownload 10/18/2022
[3] H. J. Lang, “Simplified approach to preliminary cost estimates,” Chemical Engineering, vol. 55, pp. 112-113, 1948.
[4] Straatman, P. van Sark, W. A new hybrid ocean thermal energy conversion-offshore solar pond (OTEC-OSP) design: a cost optimization approach. Solar energy, volume 82, issue 6, june 2008, pages 520-527.
[5] R.K. Sinnott Coulson & Richardson’s Chemical Engineering, Chapter 6 Costing and Project Evaluation Elsevier (2005) Google Scholar
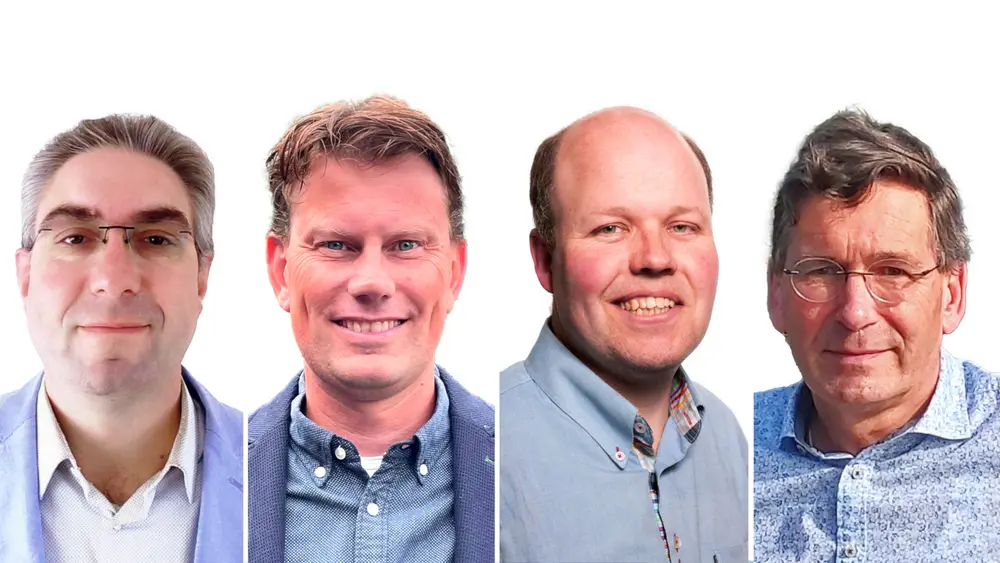