Meettasters: klassieke technologie, nog steeds actueel
Sinds de eerste schakelende meettaster een halve eeuw geleden op de markt kwam, is er veel veranderd en heeft de meettaster zich ontwikkeld tot een onmisbaar gereedschap in de verspanende industrie. De meettaster is hét gereedschap om nauwkeurig de positie van het werkstuk in de opspanning te bepalen of om op de coördinatenmeetmachine (CMM) bepaalde features van het werkstuk of de nauwkeurigheid in beeld te brengen.
Meettasters
De klassieke meettaster werkt in principe nog altijd op dezelfde manier als toen de eerste exemplaren op de markt kwamen: de punt van de stylus maakt contact met het werkstuk en meet zo de positie. Drie gelijkmatig verdeelde staven in deze weerstandssonde rusten op zes kogels, waartussen een elektrische stroom vloeit. Zodra de kogel op de stylus contact maakt, ontstaat er een kracht op deze constructie, en dat zorgt ervoor dat het veermechanisme doorbuigt.
De contactvlakken worden kleiner, waardoor de elektrische weerstand toeneemt. Zodra het contact weg is, keert de taster in de uitgangspositie terug. De verandering in de elektrische weerstand wordt gebruikt om de exacte positie te bepalen; dit is het triggersignaal en vandaar de naam schakelend tasten.
Er zijn ook alternatieve concepten, zoals een scharnierconstructie. Deze zijn echter minder nauwkeurig doordat de stylus geen unieke positie heeft en de grotere krachten de stylus kunnen doorbuigen. Het gaat hier om drukmetingen per punt: voor elk punt dat men wil meten, moet de stylus contact maken met het werkstuk. Dit levert een nauwkeurigheid op die bij de meest nauwkeurige systemen op submicronniveau ligt. En de nieuwste drukmeettasters werken met extreem geringe kracht (minder dan 0,1 N), zodat beschadigingen aan het te meten oppervlak praktisch uitgesloten zijn.
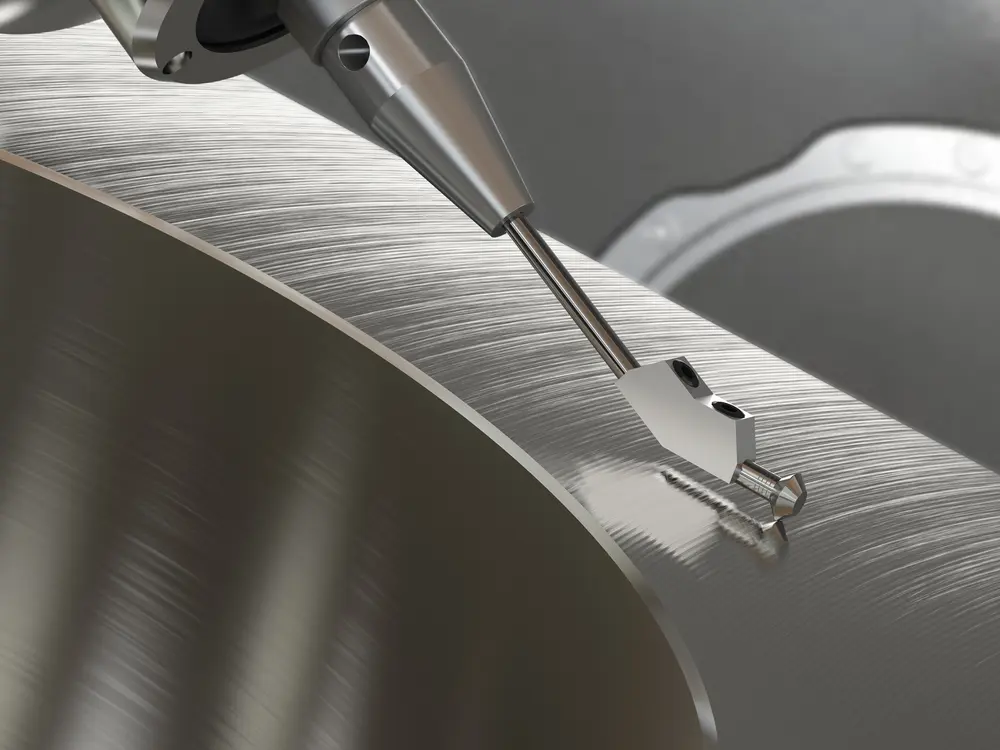
Tactiel of contactloos
Tegenwoordig zijn er naast de drukmetingtasters, tactiele tasters (of optische taster) met wit of blauw licht (zoals in een scanner) en scannende tasters. De optische tasters met scanners werken contactloos; de scannende tasters maken wel contact, maar kunnen veel meer data in korte tijd verzamelen dan een tactiele taster.
Deze optische tasters hebben als voordeel dat ze snel veel meetdata verzamelen van complexe oppervlakken. Voor typische freesstukken met een gekromd oppervlak leent deze oplossing zich beter dan een tactiele scanner, omdat de meetcyclus korter is. Hier staat tegenover dat de nauwkeurigheid iets lager is. De herhaalnauwkeurigheid in een richting van een tactiele taster ligt bij de standaard uitvoeringen rond de 1 µm, bij de nauwkeurige versies zelfs rond de 0,25 µm.
Deze hogere nauwkeurigheid gaat echter samen met een langere meetcyclus. Elk punt dat men wil meten, moet immers door de taster aangetikt worden, terwijl men met een optisch systeem een gebied van enkele vierkante centimeters in één keer volledig meet, dus met veel meer meetdata.
Bij een tactiele meettaster loopt men daarnaast tegen de beperking van de lengte van de stylus aan. Deze mag slechts een bepaalde lengte hebben omdat anders de doorbuiging de nauwkeurigheid beïnvloedt. Doordat de behuizing van de taster een minimale omvang moet hebben om de elektronica in te kunnen bouwen, kan dat bij sommige toepassingen een nadeel zijn. Verder slijt de stylus: iets waar de contactloze meettasters die scannend meten geen last van hebben.
Een voordeel is dan weer dat een tactiele taster geschikt is voor vrijwel elk oppervlak, ook als het reflecterend is. Of als men sleuven wil meten, dan is optisch meten uitgesloten. Tactiele tasters zijn de juiste keuze voor toepassingen die een snelle en eenvoudige meting vereisen, bijvoorbeeld voor het meten van afmetingen, afstanden, hoeken of diameters. Optische tasters kunnen worden gebruikt op materialen die gevoelig zijn voor beschadiging door contact, zoals zachte, flexibele of kwetsbare oppervlakken.
Toepassing doorslaggevend
Tegenwoordig bestaan er eveneens hybride tasters, die schakelend tasten en lasertasten combineren. Het voordeel hiervan is dat men geen tasters hoeft te wisselen als men beide technieken in een meetcyclus inzet. Uiteindelijk zal de toepassing, de machine en de gewenste nauwkeurigheid de keuze bepalen voor het type taster.
Hoe complexer het product, des te sneller zal men naar een contactloze meting toe willen. Ook het materiaal kan een rol spelen, net als de investeringskosten. Deze liggen bij schakelende tasters gemiddeld lager dan bij een scannende taster. De klassieke meettasster is, ondanks dat de stylus een slijtdeel is, minder onderhoudsgevoelig.
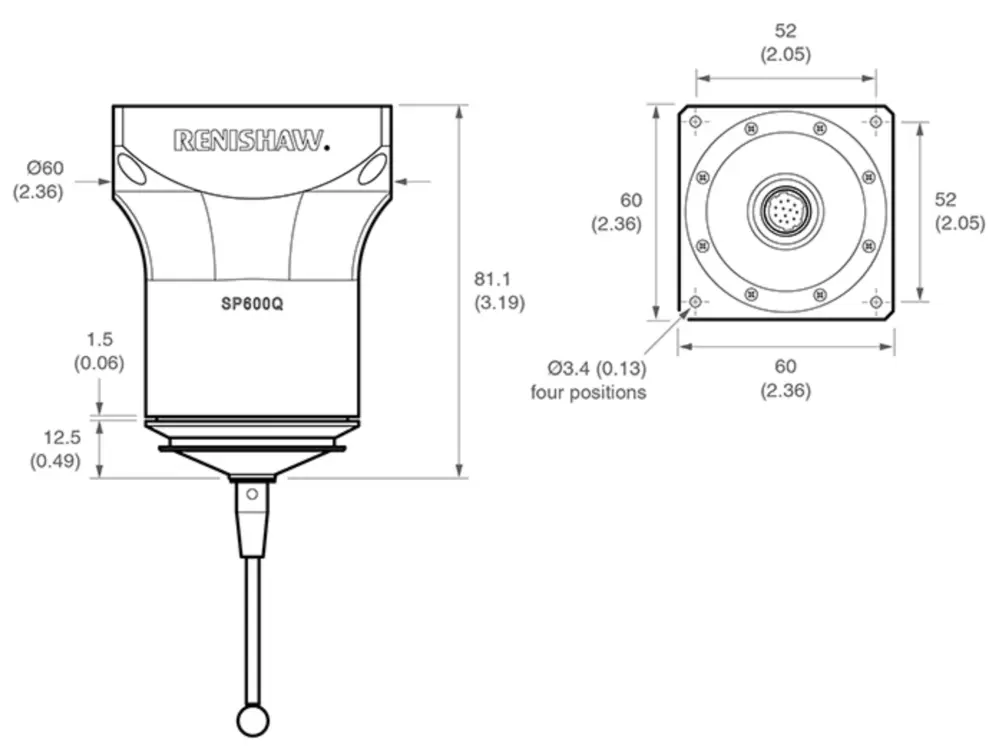
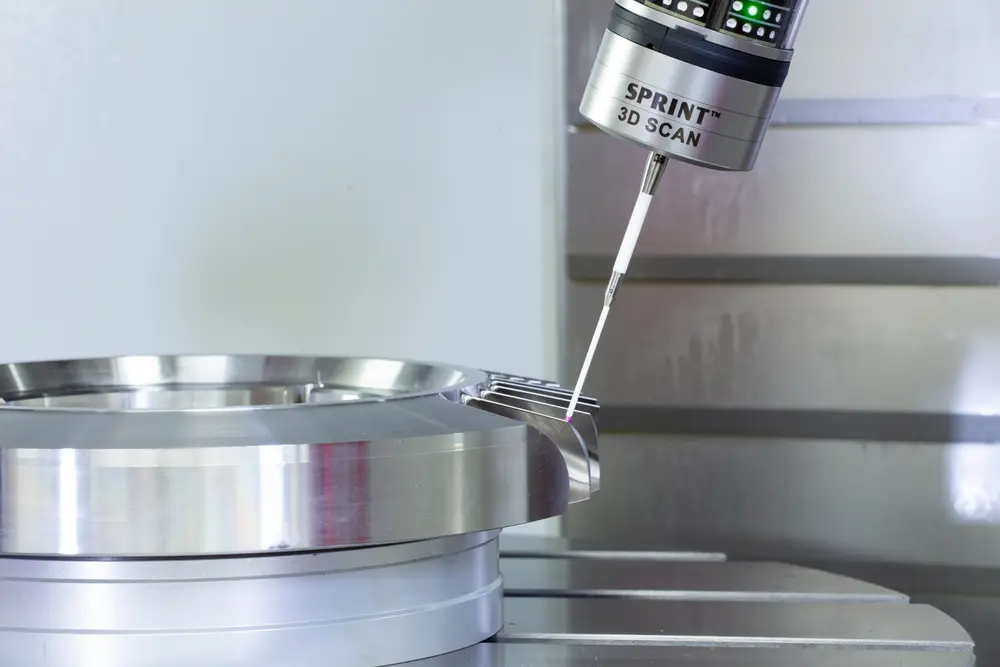
Stabiele datatransmissie
Een tweede aspect dat een rol speelt bij de keuze voor een bepaald type meettaster is de manier waarop de meetgegevens naar de CNC-besturing of de meetsoftware worden gestuurd. Optische (infrarood) en radiotransmissie zijn de gangbare methoden, omdat bekabelde tasters te veel nadelen hebben naast het voordeel van hoge betrouwbaarheid.
Bij optische transmissie wordt infraroodlicht gebruikt. Het nadeel hiervan is dat er een directe zichtlijn moet zijn tussen de taster en de ontvanger. Ook is infrarood gevoeliger voor interferentie van andere lichtbronnen of reflecties. In de nieuwste tastersystemen onderdrukken de fabrikanten dit met verschillende technieken, zoals gemoduleerde optische transmissie. Dikwijls is deze oplossing geschikt voor kleinere CNC-bewerkingscentra.
Dataoverdracht via radiotransmissie is met de hedendaagse technologie eigenlijk de voor de hand liggende oplossing. Deze systemen hebben een groot bereik en zijn dus geschikt voor grotere CNC-machines of als er grote, complexe werkstukken gemeten moeten worden. Meestal werkt het systeem op verschillende frequenties die het zelf kiest, om hiermee interferentie met andere systemen zoals een WLAN-systeem te voorkomen. Hierdoor vermijdt men "dode punten" in de machine. Met de nieuwe generatie ontvangers kan men meerdere tasters combineren op één ontvanger.
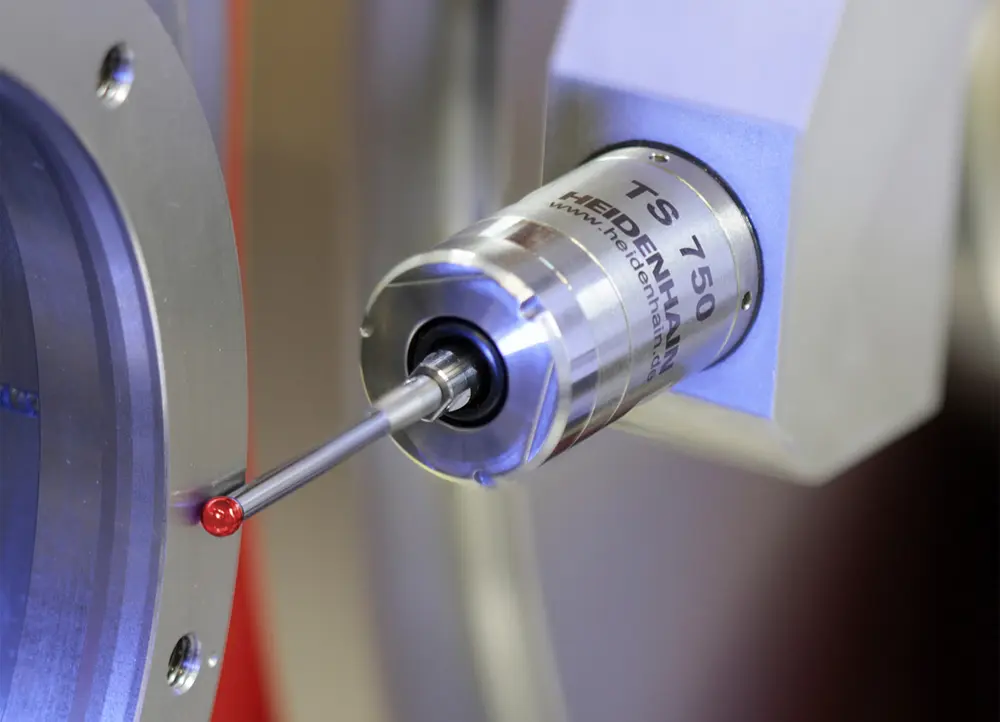
Meten op de machine
Meettasters kom je zowel op CMM's in de meetkamer tegen als (steeds vaker) op CNC-machines in de productieafdeling. De toepassingen op een CNC-machine zijn legio, zeker met de recente ontwikkelingen van de besturings- en meetsoftware. Bij gebruik in de machine is het wel belangrijk erop te letten dat de warmte van de spindel niet wordt doorgegeven aan de taster. Bij langere meetcycli zou dit de nauwkeurigheid kunnen beïnvloeden.
Een voorbeeld van de toepassing in de machine is het uitlijnen van het werkstuk. In plaats van handmatig klokken kan de machine met een meettaster de exacte positie van het werkstuk bepalen. Met best fit-opties in de software wordt het programma automatisch hierop aangepast.
Soms kiezen verspaners er ook bij een gerobotiseerde CNC-machine voor om eerst de positie van het werkstuk te bepalen voordat het freesprogramma automatisch start. Hiermee verhoogt men de nauwkeurigheid, omdat een kleine afwijking in de positie van het werkstuk in de klem zo gecorrigeerd wordt. Met beide toepassingen vermindert men de tijd dat de operator fysiek aan de machine moet staan om het proces op gang te brengen.
In proces meten
Een toepassing die minder gangbaar is, is het op de machine meten van werkstukken en hiervoor eventueel corrigeren in de besturing. Critici wijzen er telkens op dat meten op een CNC-machine betekent dat je de fout in de machine kopieert. Daarnaast is een CNC-machine minder nauwkeurig dan een CMM, die bovendien vaak in een geklimatiseerde ruimte staat en geen last heeft van thermische uitzetting zoals bij een CNC-machine wel het geval is als men freest.
In principe hebben deze critici een punt. Maar met de huidige stand van de technologie én een goede aanpak kan men ook zeer nauwkeurig werkstukken frezen én meten op de machine. En vergeet niet dat het uit het nulpuntspansysteem halen van de opspanning met daarin het werkstuk om te gaan meten op een CMM op zich ook al tot een afwijking kan leiden, hoe klein ook.
Door in proces te gaan meten, verzamelt men tijdens het proces veel meer meetdata die geanalyseerd kunnen worden en waarna men een trend kan gaan herkennen. Zo ontstaat er zicht op hoe het freesproces zich ontwikkelt binnen vooraf bepaalde toleranties. Aangevuld met steekproefmetingen op een CMM bouwt men zo een betrouwbaar onbemand proces, waarbij de operator tijdig kan ingrijpen voordat er afkeur wordt geproduceerd.
Een andere minder bekende toepassing is het meten van oppervlakteruwheid met een taster. Deze meting kan in het programma worden opgenomen zodat ze volledig geautomatiseerd kan worden uitgevoerd. Hiermee verzamelt men zowel gegevens over de Ra-waarde alsook de Rz, Rmax en Wt en andere waarden die iets zeggen over de oppervlakteruwheid.
De meettaster blijkt nu een gereedschap te zijn dat de productiviteit verbetert en de reëel beschikbare machinecapaciteit vergroot. De meettaster verhoogt effectief de ROI (return on investment) van een CNC-machine. Bovendien wordt de productie minder manafhankelijk, wat bij de huidige schaarste aan vakmensen een uitkomst is.