Wat als de druk op de meetkamer te groot wordt?
De meetkamer in een verspanend bedrijf kun je met recht het hart van de productie noemen. Hier vinden namelijk de vrijgave voor de productie van precisiecomponenten en de eindcontrole plaats. Zowel aan de hardwarekant van de meetkamer, als aan de softwarekant, zijn er ontwikkelingen die met name de efficiëntie van het meetproces moeten verbeteren. We bespreken ze meer in detail in dit dossier over de meetkamer.
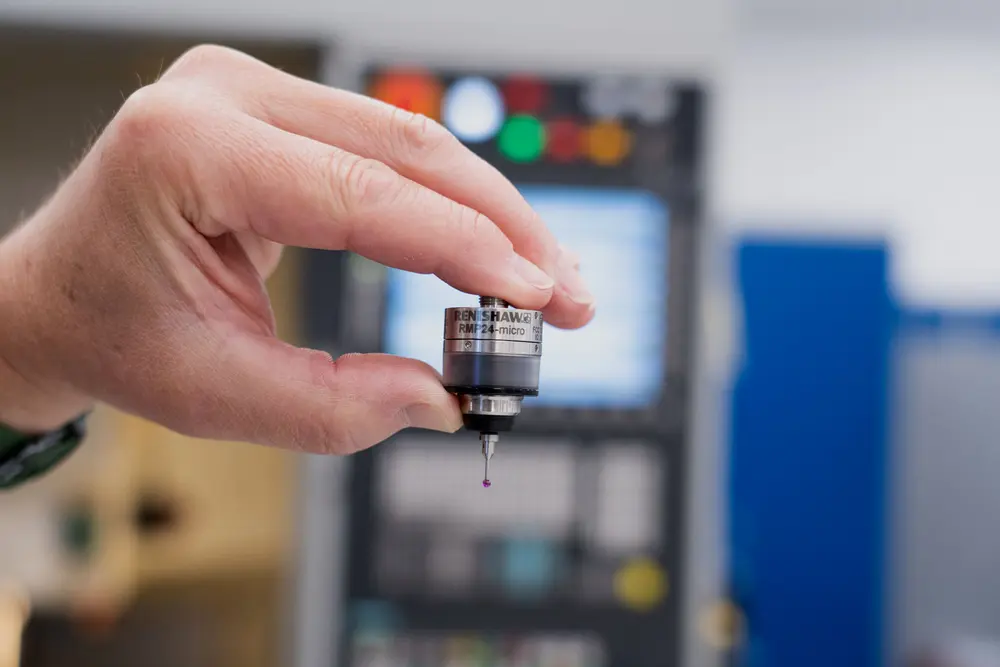
Belang van de meetkamer
Het aantal metaalbedrijven dat een eigen meetkamer heeft, groeit. Dit heeft alles te maken met de toenemende complexiteit en nauwkeurigheid van componenten én de toename van onderdelen die 100% kwaliteitscontrole vereisen. Verschillende onderzoeksbureaus verwachten dat de wereldwijde markt voor coördinatenmeetmachines (CMM) tot 2030 jaarlijks met zo’n 8 tot 9 procent zal groeien. Ook voor Europa geldt dit.
Er zijn eigenlijk maar twee factoren die de groei afremmen: de hoge investeringskosten en het gebrek aan vakmensen met kennis van metrologie. Bij de investeringen spelen niet alleen de initiële investering in een CMM een rol, ook de bijkomende kosten voor tasters, bijhorende software en niet te vergeten de geklimatiseerde ruimte.
Beide belemmeringen kun je overwinnen met een hogere efficiëntie van de meetsystemen. Dit onder andere door digitalisering. Zowel wat het programmeren betreft, als het meten zelf, zie je de laatste jaren ontwikkelingen om de doorlooptijden in de meetkamer te verkorten. Een kortere meetcyclus betekent immers dat je méér producten kunt meten in dezelfde tijdspanne.
Tactiel meten
De coördinatenmeetmachine (CMM) is de klassieke meetmachine. Het meest gekend zijn de gantry meetmachines, waarbij de meetkop aan de brug is bevestigd. Er bestaan ook CMM's in horizontale versie en arm-type CMM, evenals een meetarm, de meest flexibele oplossing. De keuze wordt vooral bepaald door het type werkstuk dat men wil meten, evenals de nauwkeurigheid die men zoekt.
CMM's voor tactiel meten zijn in de regel 3-assige meetmachines. Sinds enkele jaren kan men deze opwaarderen naar een 5-assige meetmachine, om daarmee de cyclustijd van een meting sterk te reduceren. Dit gebeurt met een speciale meetkop waarin een extra draai- en zwenkas zitten.
Het belangrijkste voordeel van 5-assig meten is dat de cyclustijd sterk verkort wordt. Afhankelijk van de afmetingen en complexiteit kan men tot drie keer zo snel meten. Daarnaast zijn de 5-assige meetsystemen nauwkeuriger, zowel absoluut als wat betreft de herhaalnauwkeurigheid. Bestaande meetmachines kan men vaak retrofitten naar de nieuwe 5-assige meetoplossing.
Een CMM wordt in principe gebruikt als men de hoogste nauwkeurigheid wil. Voor sneller meten en meer veelzijdigheid, lenen zich veel meer de optische meetsystemen (zie verderop).
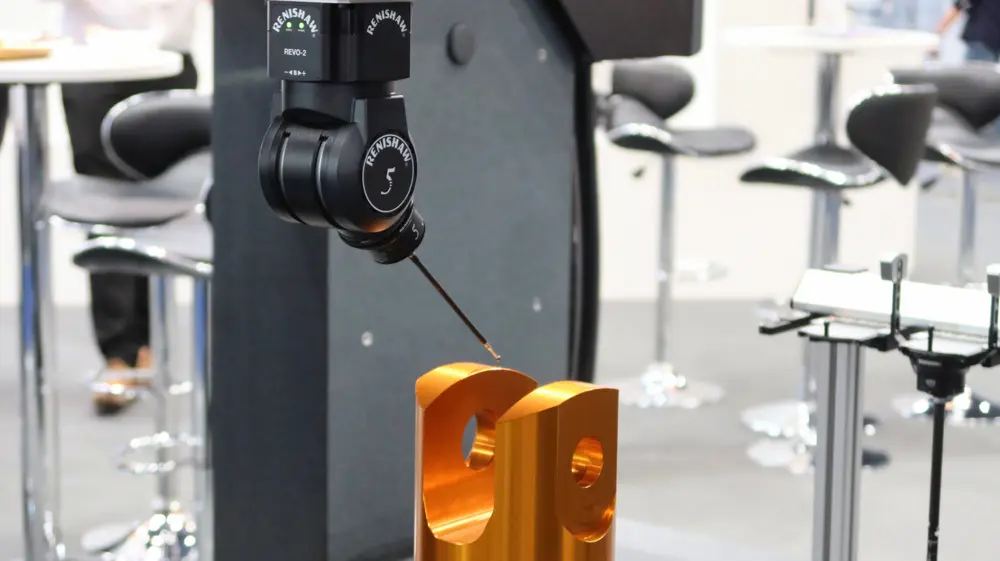
Schakelende meettasters
Van oudsher is de CMM voorzien van schakelende meettasters met stylus. De klassieke schakelende meettaster is een uitvinding van inmiddels ruim een halve eeuw geleden; een elektromechanisch systeem.
Een veer drukt de stylus tegen metalen staafjes, de kinetische contactpunten. Wanneer de kogel van de stylus het werkstukoppervlak aanraakt, ontstaat er een tegenkracht. Vlak voordat de stylus het contact met een of twee van de drie punten verbreekt, wordt er een signaal getriggerd dat de positie bepaalt. De stylus keert, zodra die van het werkstukoppervlak af beweegt, terug naar de uitgangspositie met een nauwkeurigheid van 1 µm.
De huidige generatie meettasters werkt nog steeds volgens dit principe en heeft een meetafwijking van hooguit enkele tienden van een micron.
Belang van de stylus
De nauwkeurigheid van een CMM hangt mede af van de gekozen stylus. Een kwalitatief minderwaardige of versleten stylus kan tot 10% van de meetnauwkeurigheid van een CMM kosten.
De vormnauwkeurigheid van de kogel (de mate waarin deze perfect bolvormig is) wordt uitgedrukt in graden; hoe lager de graad, hoe perfecter de bolvorm is. Het probleem is dat men de verschillen met het blote oog niet kan zien. Daarom is het aan te raden om liever een graad 5 te kiezen dan graad 10, omdat met die laatste de foutkans hoger wordt. De kogel is meestal van robijn.
De lengte van de stylus is een tweede factor die van invloed is op de nauwkeurigheid. De meeste tasters worden niet direct na contact met het werkstuk geactiveerd. Dit betekent dat naarmate de lengte van de stylus toeneemt, de foutkans groter wordt, doordat de stylus licht doorbuigt. De doorbuiging van de stylus is daarom eveneens een factor die men goed moet bewaken.
De temperatuur is de derde factor die het meetresultaat beïnvloedt. Meetkamers zijn doorgaans geklimatiseerd, maar het materiaal van de stylus is desalniettemin van belang. Materialen met een zo laag mogelijke uitzettingscoëfficiënt hebben de voorkeur.
Scannende meettasters (en de combinatie)
Naast de klassieke tactiele meettaster, is de laatste jaren de scannende taster in zwang geraakt. Hierbij glijdt de bol van de stylus over het oppervlak en worden er in korte tijd veel meer meetpunten gemeten. De scannende tasters werken met een lijnscanner die tot 75.000 punten per seconde kunnen meten.
Er bestaat ook een combinatie, de tactiele-optische tasters. De stylus wordt alleen gebruik om de tastkogel te positioneren. Met een optische sensor meet men de doorbuiging. Deze techniek leent zich onder andere goed voor het meten van boorgaten. Voor kleine boorgaten (< 0,5 mm), zijn er speciale fibertasters met kogels die een diameter hebben van kleiner dan 20 µm.
Optisch meten
We haalden het al kort aan, maar naast tactiel meten bestaat er ook optisch meten, met laser of met een vorm van licht. De belangrijkste voordelen van optisch meten zijn dat de meting contactloos is en men snel veel datapunten meet. Optisch verzamelt men in korte tijd veel meer meetgegevens, zonder risico op beschadiging. Hierdoor is ook de opspanning minder van belang, omdat er geen enkel contact plaatsvindt.
Optisch meten leent zich uitstekend voor de controle van plaats- en vormtoleranties van grote aantallen onderdelen in de productie. Of van complex gevormde werkstukken, met veel diepe gaten. De snelheid ligt namelijk veel hoger dan bij de CMM’s. Het grote nadeel van tactiel meten ten aanzien van optisch meten is dat het tijd kost. Immers elk punt dat je wilt meten moet door de taster worden aangetikt. Bij grote werkstukken of producten met veel kritische punten kost dat tijd, omdat de taster elk punt afzonderlijk moet afgaan.
Hier staat wel tegenover dat een tactiele meting nog altijd nauwkeuriger is, mede omdat deze meettechniek minder gevoelig is voor verstorende omgevingsfactoren, zoals licht, stof en andere vervuilingen. Ook harde materialen kun je het beste tactiel meten. Bij zachte materialen, die snel vervormen, is optisch meten dan weer een voordeel. Een optische 1D-meting wordt uitgevoerd met een nauwkeurigheid van 1,6 µm + l/200 µm; bij een 3D-meting ligt deze nauwkeurigheid op 2,4 µm + l/150 µm. Ter vergelijking: bij tactiel meten ligt de nauwkeurigheid rond 0,9 µm + l/350 µm.
Omdat optisch meten een digitaal proces is, kan men dit relatief eenvoudig automatiseren. Optisch meten wordt regelmatig in een CMM gecombineerd met tactiel meten. Hierdoor neemt de efficiënte bezetting van de meetmachine toe en kan men bij complexe werkstukken de beste oplossing inzetten, zonder dat het werkstuk op meerdere machines opgespannen moet worden.
3D-scannen: witlicht of blauwlicht
Eén van de technieken voor optisch meten is 3D-scannen. Deze oplossing is met name interessant als er grotere oppervlakken gemeten moeten worden. Bij 3D-scannen zijn twee technieken te onderscheiden: scanners met witlicht en met blauwlicht. De eerste techniek komt men vaak tegen in goedkopere scanners. De lichtbron is namelijk goedkoper dan die voor blauwlicht.
Deze laatste techniek levert een hogere nauwkeurigheid. Een blauwlicht scanner werkt met een golflengte tussen 405 tot 450 nanometer. Het golflengtebereik is veel smaller, waardoor een blauwlichtscanner minder last heeft van interferentie en ruis, wat in de nauwkeurigere meetdata resulteert. Ook is dit type scanner beter geschikt om reflecterende oppervlakken te meter. Tot slot zijn deze 3D-scanners sneller dan een witlichtscanner, die het hele zichtbare spectrum bestrijkt.
Scanners die met gestructureerd licht werken, zijn de derde variant. Deze belichten het te meten oppervlak met een specifiek patroon, waarna een camera de afwijkingen in het patroon vastlegt. Aan de hand van de afwijkingen berekent de software de vorm en maten.
3D-scannen gaat veel sneller dan tactiel meten. Zowel de witlicht- als blauwlichtscanners zijn geschikt om fijne details vast te leggen. Daarnaast kan men deze scanners eenvoudiger automatiseren. Sommige fabrikanten bieden hiervoor turnkey oplossingen aan. In andere situaties kan men het laden van het werkstuk automatiseren met een cobot. Als er grote aantallen producten gemeten moeten worden, is dit wel een oplossing om de efficiëntie te verbeteren.
Softwareontwikkelingen
Veel ontwikkelingen op het vak van meten, gebeuren momenteel aan de softwarekant. Aan de ene kant is dat software om de meetresultaten automatisch te vergelijken met bijvoorbeeld een CAD-model, wat men vooral bij optisch meten ziet. Hier kan men deze stap automatiseren, omdat met 3D-scannen een compleet beeld van het werkstuk ontstaat. Aan de andere kant zijn er softwareontwikkelingen als het gaat om het programmeren van klassieke meetmachines.
Merkonafhankelijke software
Opvallend bij dit laatste is dat een aantal nieuwe partijen hardware-agnostische software ontwikkelt. Deze werkt met de CMM’s van verschillende merken, mits voorzien van de juiste interface. Net als bij CAM-programmeren van een CNC-machine is het voordeel hiervan dat men niet meer afhankelijk is van de leverancier van de hardware.
Bedrijven die al een grote bibliotheek met meetprogramma’s hebben opgebouwd, zijn minder snel genegen om over te stappen naar een andere leverancier, omdat men dan de meetprogramma’s opnieuw moet maken. Of men werkt met verschillende programma’s naast elkaar. Merkonafhankelijke software voorkomt dit.
Deze partijen leggen vooral veel nadruk op het eenvoudiger en sneller programmeren van een CMM of een optisch meetsysteem. Dit doen ze bijvoorbeeld door ballooning en GD&T-extractie aan te bieden, waarmee men veel handmatige programmeerstappen vermijdt.
Daarnaast leggen ze vaak de nadruk op het snel genereren van een kwaliteitsrapport op basis van grote hoeveelheden data. Het combineren van meetdata van verschillende bronnen, zelfs als die van verschillende merken meetmachines komen, wordt dan mogelijk. Ze spelen ook sneller in op de digitalisering door standaardkoppeling naar bijvoorbeeld een ERP-systeem aan te bieden.
Automatisch programmeren
In Nederland kiezen steeds meer grote OEM's voor Model Based Definition (MBD). Hierbij worden alle belangrijke productiedata, zoals vorm- en plaatstoleranties, als PMI-data aan het 3D-model toegevoegd. Daarmee zou men machines en ook CMM's voor een groot deel automatisch kunnen programmeren. De fabrikanten van CMM's lopen op dit vlak voorop.
In de praktijk zal hierdoor de vraag naar meetkennis in de ontwikkelfase van componenten toenemen. De constructeur zal kennis moeten hebben van welke toleranties tegen een acceptabele prijs haalbaar zijn in de productie om niet te over-tolereren; ook zal de design engineer moeten weten hoe te controleren. En vooral zal er aan de engineeringkant zorgvuldig moeten worden omgegaan met toleranties, omdat men de controlestap uitschakelt die nu nog in het maakbedrijf wordt gezet. Dit punt maakt sommige meetexperts in maakbedrijven dan ook kritisch over de doorbraak van automatisch programmeren van een CMM. Wie is immers verantwoordelijk als het fout gaat?
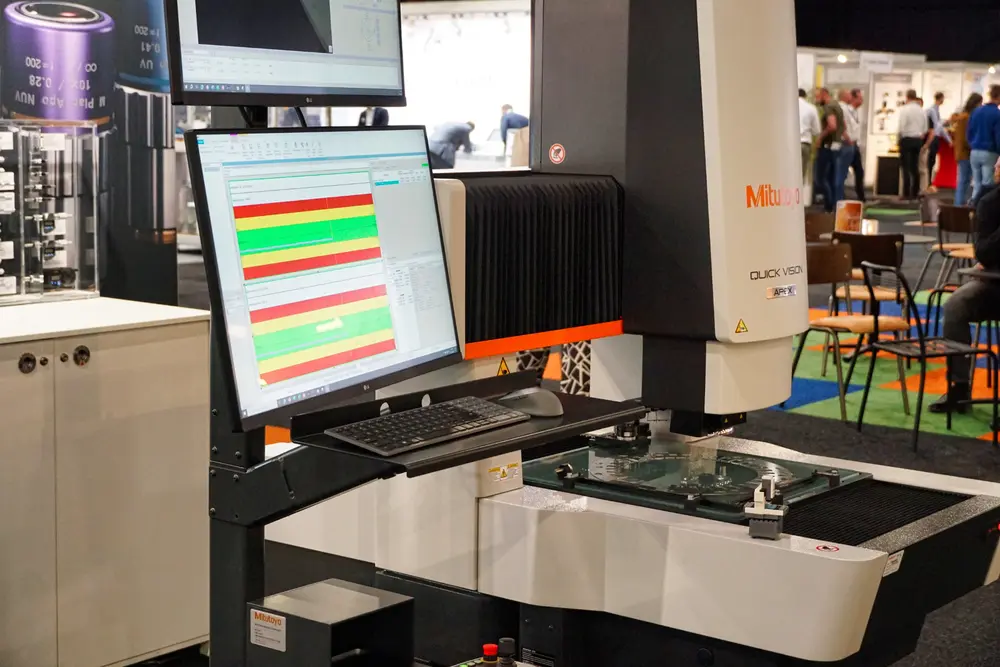