invloed van CO₂ in argon op MAG-lassen van staal
Bij MAG-lassen van koolstofstaal wordt een actief binair gasmengsel van Argon en CO₂ gebruikt als hulpmiddel om het gesmolten materiaal tegen de inwerking van de omgevingslucht te beschermen. Zowel stikstof als zuurstof uit de omgevingslucht kunnen immers een zeer nadelige invloed uitoefenen op de kwaliteit van de lasverbinding door het veroorzaken van poreusheid, verbrossing of door afbrand van legeringselementen.
De hoeveelheid CO₂ heeft een invloed op de stabiliteit van het lasproces en de kwaliteit van de lasverbinding. De productiviteit van het MAG-lasproces hangt af van de manier waarop en de snelheid waarmee de lasdraad wordt afgesmolten.
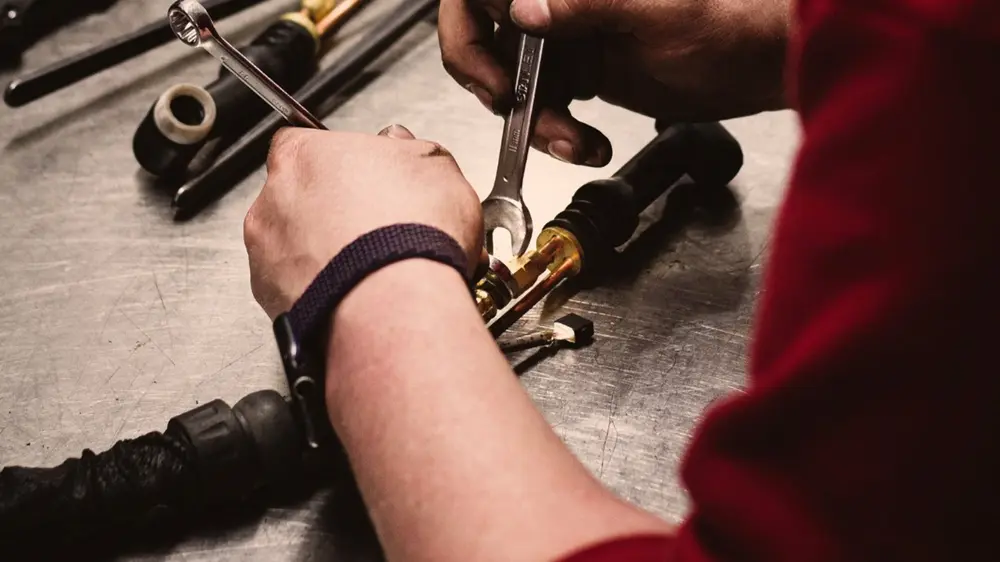
Samenstelling van het gas
De samenstelling wordt in eerste instantie bepaald door het te lassen materiaal en de laspositie. Maar ook andere factoren spelen een grote rol. Het beschermgas heeft namelijk een grote invloed op het gedrag van de elektrische vlamboog, de wijze van materiaaloverdracht, de hoeveelheid spatten, het aanvloeien en de geometrie van de las, de lassnelheid, de chemische analyse en de mechanische eigenschappen van het lasmetaal. Een juiste keuze van het beschermgas, in combinatie met een aangepast type lastoevoegmateriaal, is bepalend voor de technische en economische resultaten die kunnen worden verwacht.
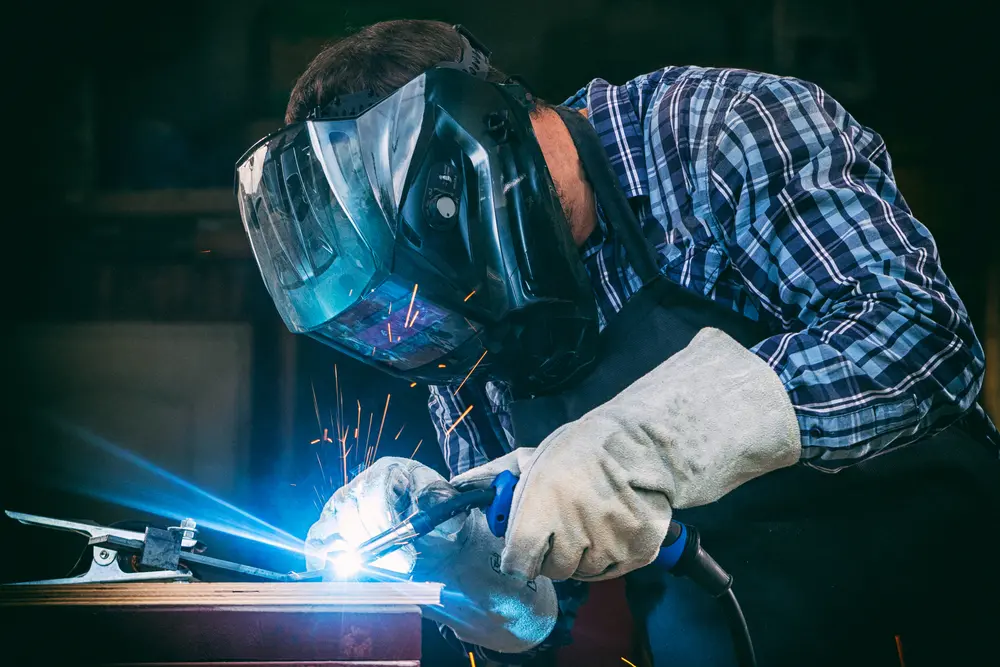
CO₂ in het beschermgas
Koolzuur (CO₂) wordt aan Argon toegevoegd om een combinatie te krijgen van het voordeel van Argon, een fijne druppelovergang, en de voordelen van CO₂, een goede inbranding en goede vloeibaarheid van het smeltbad. CO₂ heeft ook een stabiliserend effect op de elektrische vlamboog. Naargelang het aandeel CO₂ in Argon kunnen gasmengsels ingedeeld worden op basis van de EN ISO 14175:
- Groep M20 – licht oxiderend (5 < CO₂ ≤ 15)
- Groep M21 – matig oxiderend (15 < CO₂ ≤ 25)
- Groep C1 – sterk oxiderend (100 CO₂)
Oxiderende eigenschappen
De oxiderende werking van CO₂ is het gevolg van het feit dat een gedeelte van de CO₂-moleculen in de boogatmosfeer ontleedt tot zuurstof (O) en koolmonoxide (CO). De vrijgekomen zuurstofatomen kunnen in het vloeibaar lasmetaal oplossen en zullen vervolgens legeringselementen afbranden. Bij het lassen van koolstofstaal zijn dat in de eerste plaats mangaan (Mn) en silicium (Si), elementen die speciaal aan de lasdraad zijn toegevoegd om de nadelige effecten van oxidatie te neutraliseren. De gevormde oxiden komen uiteindelijk in de vorm van plaatselijke slakeilandjes op het lasoppervlak terecht. Bij een te laag gehalte aan Mn en Si kan de zuurstof met het aanwezige koolstof (C) zorgen voor gasvormig koolmonoxide (CO) dat in het stollende lasmetaal kan opgesloten raken en zo voor porositeit zorgt.
CO₂ heeft slechts de helft van het oxiderend vermogen van zuurstof en dat biedt een aantal voordelen
Het IIW definieert de oxidatiegraad van een menggas als volgt: oxidatiegraad = (0,5 x % CO₂) + % O₂
Daaruit blijkt dat CO₂ slechts de helft van het oxiderend vermogen van zuurstof heeft en dat biedt een aantal voordelen.
Ar/CO₂-mengassen voor staal
De toevoeging van CO₂ in argon heeft reeds een stabiliserend effect op de elektrische vlamboog vanaf 0,1%. Om ook nog eens een goede laskwaliteit te verkrijgen is minimaal 5% nodig. De hoeveelheid CO₂ beïnvloedt de inbrandingsdiepte en het inbrandingsprofiel. Lagere CO₂-percentages vertonen eerder een vingervormige inbranding, terwijl de hogere percentages een meer afgerond profiel hebben.
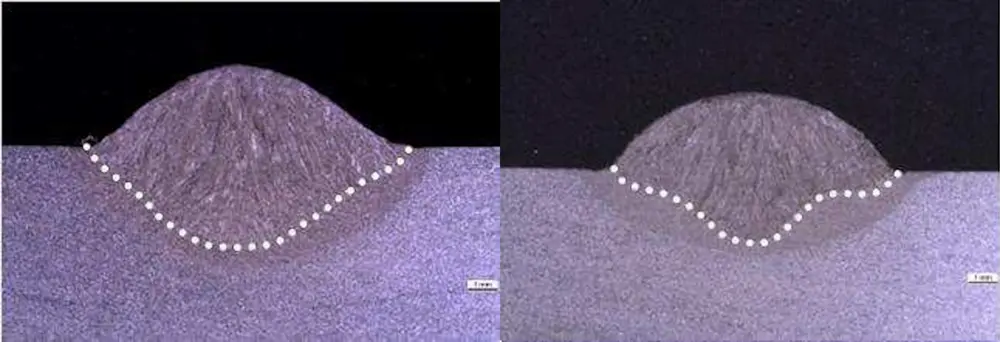
De toevoeging van CO₂ heeft ook een effect op de flexibiliteit van het lasproces en de tolerantie op de lasnaadvoorbereiding. Hogere CO₂ gehaltes zorgen voor een iets hogere boogspanning en een bredere elektrische vlamboog, waardoor variaties in de open stand (door een minder goede fit-up) kunnen worden overbrugd.
De eerste Ar/CO₂ gasmengsels voor het MAG-lassen van staal werden ontwikkeld in de jaren ’50 van de vorige eeuw. Europa en de Verenigde Staten hebben daarbij hun eigen koers gevolgd. Op basis van empirische data, lokale gebruiken en de opkomst van nieuwe toepassingen vinden we nu over de ganse wereld gasmengsels variërend van 8 tot 50% CO₂ in argon. Door het normatieve werk in die landen, zijn die mengsels ook terecht gekomen in sommige constructiecodes. Toch moet worden opgemerkt dat vanaf 20% CO₂ en meer de elektrische vlamboog minder stabiel wordt en dat zowel het aantal lasspatten als de vorming van lasrook aanzienlijk toenemen.
Waarom verschillende CO₂-percentages?
De ontwikkeling van stroombronnen voor het MAG-lassen evolueerde van diodetechnologie met bijhorende natuurlijke druppelafsplitsing van de draad, over thyristoren, transistoren, choppers en inverters tot software gestuurde bronnen die gebruik maken van een geforceerde druppelovergang, zoals het pulserend lassen. Bij lage draadsnelheden en bijhorende stroomsterktes zal een draad eerder in kortsluitboog (short arc) afsmelten. Bij hogere draadsnelheden gebeurt dat in een sproeiboog (spray arc). De overgang van de ene modus naar de andere gaat via een globulair gebied waarin de druppelafsplisting heel onregelmatig en instabiel is. Het pulserend lassen is het sluitstuk tussen deze 2 werkzame gebieden.
Het bijzondere aan Ar/CO₂ menggassen is dat ze vanaf 20% CO₂ tot 100% CO₂ bij hoge draadsnelheden en bijhorende stroomsterktes geen sproeiboog meer mogelijk maken op klassieke lasstroombronnen en uiteindelijk het afsmelten van de draad alleen mogelijk maken in het onstabiele globulaire gebied met veel spatten tot gevolg.
In 1993 publiceerde Prof. Ushio een werk over de druppelovergang van het MAG-lassen bij hoge stroomsterktes. Hij toonde aan dat het instabiele globulaire gebied 2 verschillende varianten van de druppelovergang heeft en dat het sproeiboog gebied wel 5 verschillende types kent.
GLOBULAIRE MODUS
- drop transfer: onregelmatige grootte, veel spatten, onregelmatig lasuiterlijk
- repelled transfer: zeer veel spatten door de afstotende manier van druppelafsplitsing
SPROEIBOOGMODUS
- projected transfer: druppels met regelmatige grootte
- streaming transfer: zeer stabiele sproeiboog
- repelled spray: de druppel wordt door elektromagnetische krachten uit de boog geduwd; veel spatten
- swinging spray: bij hoge stroomsterktes en afhankelijk van de samenstelling van het gas danst de boog in de richting van de lasnaad; verlies aan inbrandingsdiepte
- rotating spray: bij zeer hoge stroomsterktes en hoge spanningen (lange boog) zal de elektrische vlamboog beginnen ronddraaien ; toename van de inbranding en spatten
Dankzij high speed cameras (met 6000 tot 8000 beelden per seconde) en stroboscopische technieken konden deze fenomenen beter worden begrepen. Het werd duidelijk dat voor praktische lastoepassingen voornamelijk de kortsluitboogmodus en de axiale sproeiboog (projected transfer en streaming transfer) interessant zijn.
Het verband tussen druppelovergang en % CO₂
Wanneer Ar/CO₂-gasmengsels met verschillend % CO₂ worden getest over een breed stroombereik, kunnen een aantal vaststellingen worden gemaakt. Daarbij wordt steevast gekeken naar de sproeiboog omdat dit de meest productieve modus is bij het MAG-lassen van staal.
Een eerste vaststelling is dat laag oxiderende mengsels, type M20 met 8 tot 15% CO₂, allemaal vlot tot een axiale sproeiboog kunnen leiden bij stroomsterktes die beneden 300 A liggen. In het geval van 8% CO₂ wordt de sproeiboog bereikt bij amper 250 A. Dat maakt het mogelijk om productief te lassen met standaard stroombronnen en gasgekoelde pistolen. Het globulaire gebied bij deze samenstelling is heel beperkt (tussen 230 en 250 A).
Wanneer een niveau van 15% CO₂ wordt bereikt, gaat de vlamboog zich plots en over een breed stroombereik totaal anders gedragen, waarbij er een zeer breed globulair gebied ontstaat tussen het kortsluitbooglassen en het sproeibooggebied.
Boven 15% CO₂ spreken we van hoog oxiderende mengsels, type M21, waarbij de sproeiboog pas wordt bereikt vanaf 400 A. Dat maakt het gebruik van watergekoelde laspistolen en stroombronnen met een hoge inschakelduur op 400 A noodzakelijk.
Het beschermgas is een hoofdrolspeler in het MAG-proces, terwijl de samenstelling nauwelijks in vraag wordt gesteld
Bij 18% CO₂ is de axiale sproeiboog beperkt tot het gebied van 400 – 440 A. Bij hogere stromen gaat de boog ronddraaien.
Zodra 20% CO₂ wordt gebruikt, is er van een axiale sproeiboog geen sprake meer. De boog gaat bij stoenemende stroomsterktes over van globulair naar een dansende sproeiboog (swinging spray) waarbij het spatgedrag aanzienlijk toeneemt en waarbij de inbrandingsdiepte nog moeilijk kan aangestuurd worden.
Binaire gassen voor staal
Indien rekening wordt gehouden met de gedragingen van de elektrische vlamboog en de wijze waarop druppels worden afgesplitst van de lasdraad met moderne stroombrontechnologie, zijn de binaire Ar/CO₂ menggassen voor het MAG-lassen van staal als volgt onder te verdelen:
- Menggassen met een overgang naar de sproeiboog onder 300 A: deze gasmengsels bevatten minder dan 15% CO₂ en zijn tevens geschikt voor het pulserend lassen. Het meest gebruikte gas van dit type bevat 8% CO₂. Deze samenstelling leidt tot de laagste oxidatiegraad, een zeer stabiele elektrische vlamboog, extreem laag spatgedrag en de mogelijkheid tot het gebruik van eender welke stroombron en gasgekoelde pistolen.
- Menggassen met CO₂ gehaltes tussen 15 en 18% CO₂: deze gassen zijn universeel inzetbaar en zijn zowel geschikt voor massieve draden als gevulde draden. Het gas met 18% CO₂ presteert het beste in deze klasse. Deze samenstelling maakt een mooie axiale sproeiboog mogelijk op eender welke stroombron van 400 A bij 100% inschakelduur. Het gas is ook geschikt voor het pulserend lassen en is heel tolerant voor variaties in open stand (slechte fit-up) en vervuilde oppervlaktes.
- Menggassen met CO₂ gehaltes boven 18%: deze menggassen vertonen een sterk spatgedrag en leiden tot sterke oxidatie van de las. Tot 20% CO₂ worden deze gassen nog courant gebruikt. Indien echter rekening wordt gehouden met de totale laskosten, incl. het verwijderen van spatten, dan is dit niet altijd de beste keuze.
Conclusie
De fabrikanten van lasstroombronnen hebben de afgelopen jaren niet stilgezeten. De innovaties volgen elkaar op in snel tempo. Ook de fabrikanten van lasdraden sleutelen nog steeds verder aan zowel de samenstelling als de fabricagetechnologie (zoals de coating van de draad). Iedereen legt daarbij de focus op gebruiksgemak en productiviteit. Bij al die veranderingen wordt te weinig stil gestaan bij een aangepaste keuze van het gas. Het beschermgas is nochtans een hoofdrolspeler in het MAG-proces, terwijl de samenstelling nauwelijks in vraag wordt gesteld. Voor het MAG-lassen van staal met een binair gas, haal je het meeste economisch rendement met 8% CO₂ en 18% CO₂ in argon. Het loont de moeite om voor de Ar/CO₂-samenstelling te optimaliseren. In veel gevallen zijn deze veranderingen zelfs mogelijk binnen de bestaande gekwalificeerde lasprocedures.
BRONNEN
Effects of shielding gas composition on metal transfer phenomena in high current GMA welding; M.Ushio, K.Ikeuchi, M.Tanaka, T.Seto; JWRI, Vol.22 (1993), Vol.1
CO₂ content in argon for MAG welding – quality and productivity windows; J. Grundmann, F. Januard; 2012; Air Liquide CTAS