La convergence de l'OT et de l'IT n'est pas un luxe, mais une nécessité
La séparation des systèmes est un frein aux processus de production basés sur les données
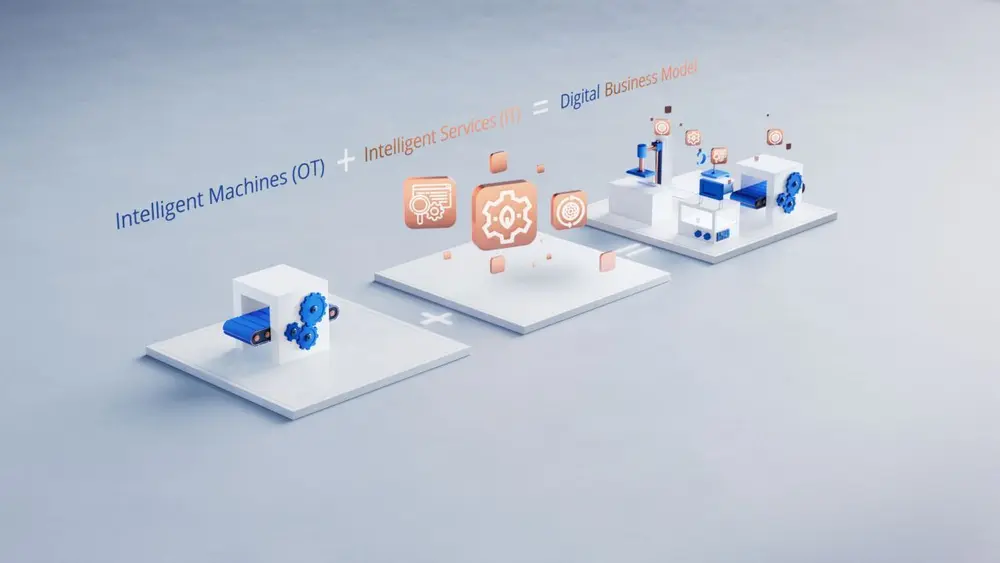
Avec les évolutions en matière d'intégration et d'interopérabilité des données, la convergence OT/IT - la 'collaboration' entre la technologie opérationnelle (OT) et la technologie de l'information (IT) - devient de plus en plus importante. Elle permet de combiner les données en temps réel des machines de production avec des outils d'analyse de données avancés. Cela permet d'optimiser des aspects tels que l'efficacité de la production, le contrôle de la qualité et la gestion de l'énergie. Voilà pourquoi on travaille constamment à des innovations dans ce domaine.
Traitement des données
La technologie opérationnelle (OT) et la technologie de l'information (IT) se rapprochent de plus en plus. Cette intégration poussée a tout à voir avec l'avalanche de développements numériques, notamment le cloud computing, l'edge computing, l'internet des objets (IoT) et l'Industrie 4.0. Ce rythme rapide est lié au développement des outils et des plateformes nécessaires, à l'amélioration de la connectivité (par exemple 5G) et à la nécessité d'adopter plus rapidement les nouvelles technologies pour des raisons d'efficacité et de coût.
Glossaire
- Consommation de bande passante: le degré d'échange de données sur le réseau au cours d'une période donnée, exprimé en Mo.
- Dispositifs d'interface: dispositifs qui traduisent les protocoles de communication des anciens systèmes OT en protocoles courants dans les systèmes informatiques modernes.
- Latence: temps qui s'écoule entre une demande et la réponse correspondante.
- Middleware: logiciel qui collecte, normalise et transmet les données des anciens systèmes aux systèmes informatiques dans un format compatible.
- Virtualisation: technologie qui permet à plusieurs machines virtuelles de fonctionner sur un seul serveur physique, ce qui accroît l'efficacité et la flexibilité.
Basé sur les données
Les développements décrits ci-dessus présentent de nombreux avantages, mais aussi des défis. Avant d'entrer dans le vif du sujet, il convient de faire un bref rappel.
OT
L'OT désigne le matériel et les logiciels utilisés pour contrôler et surveiller des processus physiques, des appareils et des infrastructures. L'OT a commencé à se développer dans les années '60 et '70 et s'est transformé, au fil des décennies, en un ensemble d'infrastructures numériques avancées qui permettent aux environnements de production et à leurs infrastructures de fonctionner de manière fiable. L'accent est mis sur le traitement en temps réel des informations provenant de capteurs, d'actionneurs, d'automates ou de systèmes de réseaux industriels, par exemple.
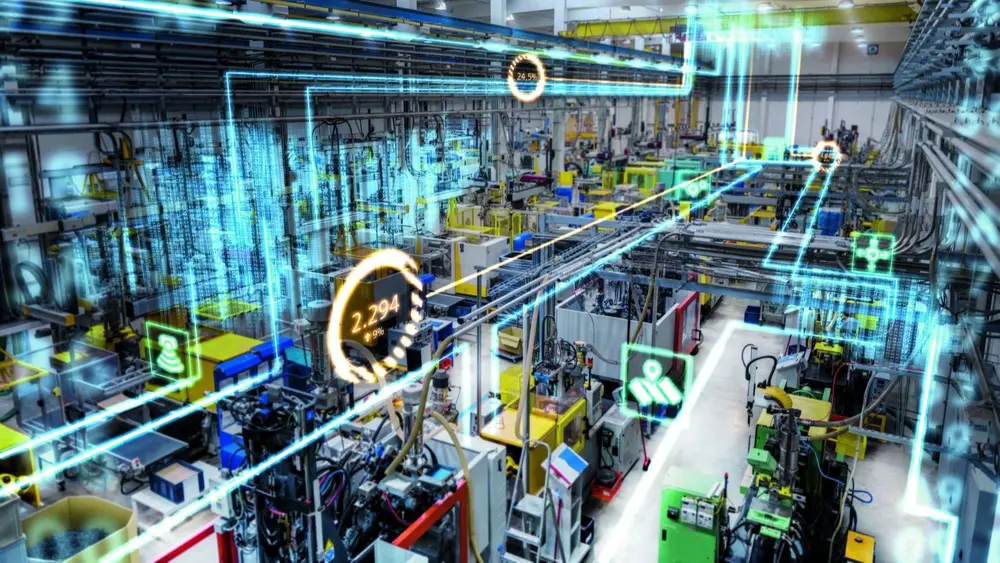
IT
L'IT se concentre sur le traitement, le stockage, la sécurisation et la transmission d'informations au sein d'une structure organisationnelle. Dans les années '50 et '60, cela se faisait avec la première génération de mainframes, des appareils peu maniables et à faible capacité de mémoire qui utilisaient des cartes perforées et des bandes magnétiques. Depuis l'arrivée (et l'essor) des mini-ordinateurs, des PC et des réseaux internes, les choses se sont accélérées à la fin du siècle dernier et, depuis le début de ce siècle, le rôle de l'IT n'est plus seulement de soutenir, mais aussi de guider et d'innover.
Strictement séparé
Au début du siècle, l'OT et l'IT fonctionnaient encore de manière strictement séparée, et ce pour de bonnes raisons. Avec ce que l'on appelle un 'air gap', une infrastructure ICT physiquement séparée des autres réseaux (voir tableau), on tentait de minimiser le risque de menaces numériques. Ce qui n'aidait pas, c'est le fait que les systèmes OT et IT avaient des gestionnaires différents: Les systèmes OT étaient gérés par des techniciens et des ingénieurs, tandis que les systèmes IT étaient gérés par des spécialistes IT.
Non seulement les points de départ étaient différents - dans l'OT, il est question de availability (la production ne doit pas s'arrêter), dans l'IT, il s'agit de confidentiality (les données et le trafic de données doivent être sûrs). Et puis la communication était difficile: les gens ne parlaient pas la même langue. En outre, les systèmes pouvaient et peuvent s'arrêter involontairement lorsque des processus IT tels que des mises à jour ou des protocoles d'authentification sont transférés vers l'OT sans tenir compte de la nécessité d'assurer la continuité. Aujourd'hui, un solide OT-Backbone (voir encadré) permet d'établir un lien sécurisé et contrôlé entre l'OT et l'IT.
OT-Backbone
Un OT-Backbone assure une communication fiable et rapide entre les lignes de production, les serveurs et les salles de contrôle au sein de l'environnement OT; les questions de fiabilité, de faible latence et de disponibilité sont prioritaires. La couche réseau haute performance est construite à l'aide de commutateurs Ethernet industriels, de la redondance (doubles connexions pour qu'une défaillance n'ait pas d'impact), d'un support de traitement des données en temps réel et de mesures de cybersécurité spécifiques à l'OT, notamment la segmentation, les pare-feux et la surveillance. En plus d'assurer une communication OT fiable, le système garantit également la séparation des données IT et OT et des opérations OT/IT, grâce à une segmentation du réseau et des architectures de sécurité.
Freiner le contrôle des données
L'évolution de l'intégration et de l'interopérabilité des données se traduit par un besoin croissant de convergence OT/IT. En effet, la séparation des systèmes OT et IT peut même constituer un frein aux processus de production basés sur les données.
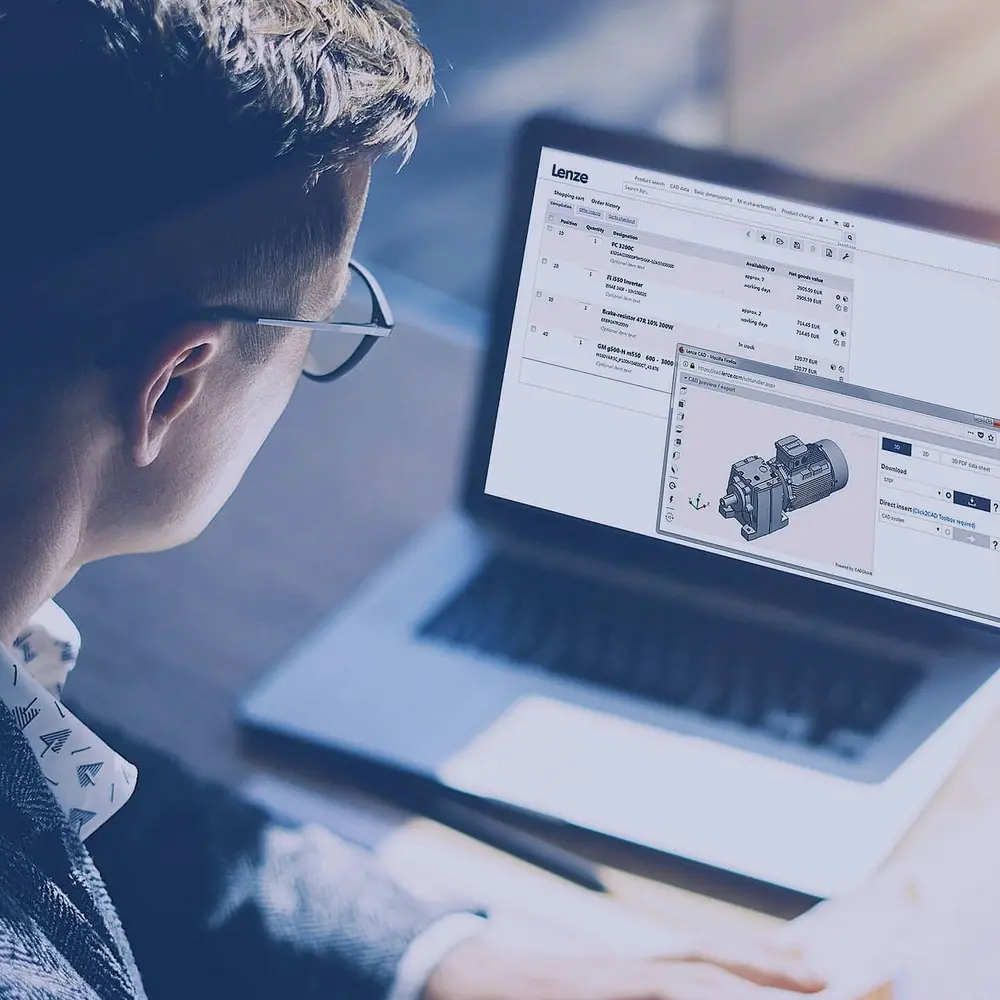
Échange et intégration de données
Dans un environnement IoT, d'énormes quantités de données sont collectées à des fins d'analyse. Lorsque les systèmes IT et OT fonctionnent séparément, celles-ci ne sont pas disponibles de manière centralisée. Non seulement cela se fait au détriment de la visibilité de bout en bout mais en plus, l'analyse des données sera également sous-optimale (silos de données).
Évolutivité et flexibilité
La séparation des domaines complique la mise en œuvre de solutions évolutives et flexibles, si bien qu'il est (plus) difficile d'anticiper rapidement les changements numériques. L'intégration facilite également l'implémentation de nouvelles technologies telles que l'IA, l'apprentissage automatique, l'informatique en nuage et l'informatique de périphérie.
Suite aux développements au sein de l'intégration et l'interopérabilité des données, le besoin de convergence OT/IT se fait de plus en plus sentir
Cybersécurité
Des problèmes de sécurité se posent en particulier lorsque les systèmes OT sont connectés à un réseau obsolète et fermé et que les systèmes IT sont connectés via internet. L'intégration permet d'appliquer en temps réel des protocoles de sécurité avancés et des outils de surveillance, ce qui porte la sécurité à un niveau supérieur.
Prise de décision
Les systèmes informatiques peuvent traiter des données en temps réel et fournir des informations, mais si les systèmes informatiques ne sont pas correctement intégrés, cela entraîne des retards dans la collecte et l'analyse des données. Dans un environnement de production, où une prise de décision rapide est essentielle, cela entraîne des problèmes.
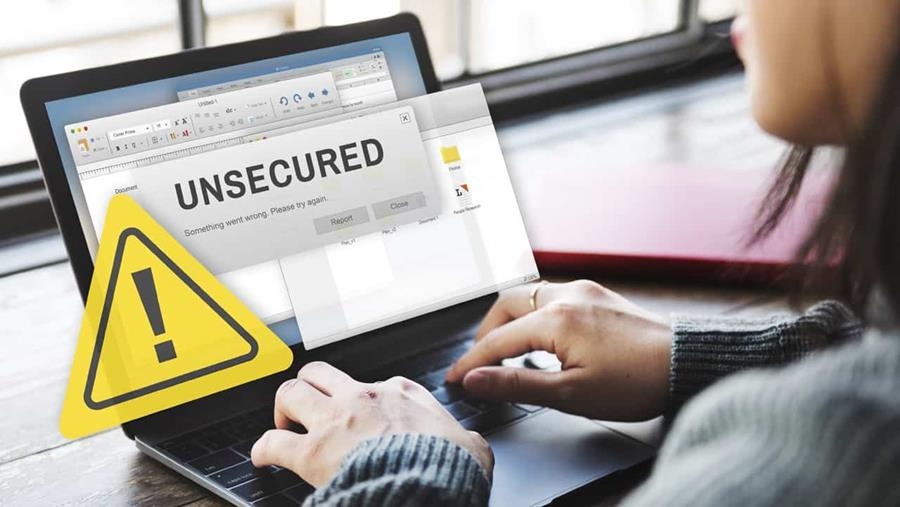
Architecture de réseau unifiée
Compte tenu de ce qui précède, le passage à une structure intégrée OT/IT est parfaitement logique. Ici, les systèmes, les données et les processus sont réunis dans une architecture de réseau unifiée, ce qui permet d'améliorer
- l'efficacité de la production, grâce à une localisation et une optimisation plus rapides des goulets d'étranglement et à une utilisation plus efficace des ressources (gestion des ressources), ce qui se traduit par une réduction des coûts;
- le contrôle de la qualité, en permettant une surveillance continue de la qualité des produits et en identifiant les tendances et les modèles indiquant des problèmes de qualité;
- la gestion de l'énergie, en identifiant des modèles de consommation d'énergie et, sur cette base, en parvenant - automatiquement ou non - à des réglages optimaux des machines.
En outre, la convergence OT/IT permet aux fabricants d'accéder à de nouvelles technologies telles que l'edge computing, le cloud computing et la virtualisation (voir le glossaire).
Procédure
Après avoir établi que la convergence (de plus en plus rapide) de l'OT et de l'IT est un fait, la question évidente est de savoir comment elle se concrétise. La réponse est: par une combinaison d'intégration technologique, d'alignement organisationnel et de mesures de sécurité.
La convergence OT/IT permet aux fabricants d'accéder à de nouvelles technologies telles que l'informatique en périphérie, l'informatique en nuage et la virtualisation
Intégration technologique
Les systèmes OT sont reliés aux systèmes informatiques via des normes de communication industrielle telles que OPC UA ou MQTT, les contrôleurs jouant un rôle intermédiaire (voir l'encadré Contrôleurs). L'un des problèmes peut être que les installations industrielles fonctionnent encore avec des systèmes de contrôle anciens qui sont difficiles à adapter à l'infrastructure informatique moderne. Pour y remédier, il existe des intergiciels et des dispositifs d'interface (voir le glossaire).
Alignement organisationnel
Les spécialistes IT et OT travaillent ensemble sur des projets et des infrastructures. Les processus d'exploitation et de production sont alignés grâce à des systèmes tels que MES et ERP, qui définissent explicitement les responsabilités de chacun.
Cybersécurité et fiabilité
Les réseaux sont sécurisés afin que les deux domaines puissent communiquer en toute sécurité. Pour détecter rapidement les menaces, les systèmes sont surveillés au niveau OT et IT à l'aide de protocoles et de normes communs tels que ISA/IEC 62443.
Contrôleurs
Les contrôleurs agissent comme une interface intelligente qui convertit les données de processus en informations accessibles et utilisables pour les systèmes informatiques. Ils jouent en quelque sorte un rôle d'intermédiaire entre le domaine déterministe et en temps réel de l'OT et le domaine flexible et basé sur les données de l'IT. C'est précisément parce que les contrôleurs touchent à ces deux domaines qu'ils peuvent être considérés comme une cible de grande valeur dans l'architecture de sécurité. Des mesures de sécurité telles que l'architecture zero trust, la sécurité en couches (defense-in-depth), la segmentation du réseau, le contrôle d'accès strict et l'identification sont donc appropriées.
Tendances
Les entreprises qui ont adopté la convergence OT/IT peuvent anticiper plus rapidement les changements sur le marché, réaliser des économies et renforcer leur position concurrentielle. Les innovations dans ce domaine sont donc en plein essor.
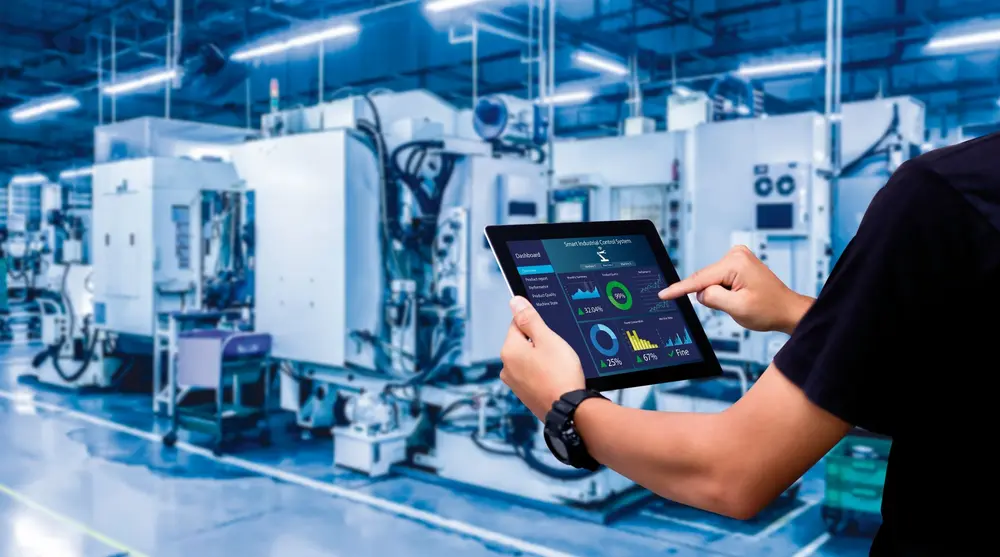
Analyse des données et IA
L'intégration des systèmes OT et IT crée d'énormes quantités de données. Leur analyse peut être affinée grâce à l'intelligence artificielle (IA) et à l'apprentissage automatique (machine learning), un sous-domaine de l'IA. Ces technologies permettent aux entreprises d'optimiser (davantage) les processus et d'améliorer la production en prenant des décisions fondées sur la connaissance.
Edge computing
Il s'agit de traiter les données générées soit localement, soit sur un serveur proche. Cette approche permet de réduire la latence et la consommation de bande passante (voir glossaire). Elle réduit également de manière significative le risque de perte ou d'interception d'informations sensibles en cours de route. Le fait que pratiquement chaque appareil edge soit une passerelle pour les cyberattaques rend indispensables une authentification et des contrôles d'accès robustes, ainsi qu'une sécurité des endpoints.
Plateformes low-code et no-code
Une plateforme low-code est un environnement de développement dans lequel les applications peuvent être créées avec un minimum de codage manuel. Elle utilise éventuellement des interfaces visuelles, des composants à glisser-déposer et des modèles pour accélérer le développement.
Les plateformes no-code sont conçues pour offrir un large accès au développement de logiciels. Elles sont généralement déployées pour automatiser rapidement des processus ou créer des applications d'exploitation simples.
En collaboration avec Cebeo, Lenze et Prokorment