Rechercher la cause de la défaillance d'un matériau
La clé de l'amélioration et de la prévention
Les défaillances de matériaux se produisent malheureusement régulièrement dans divers secteurs: dans la construction de bâtiments, l'ingénierie mécanique, l'industrie,... La défaillance de composants critiques peut entraîner de graves pertes économiques, des interruptions de production ou même des blessures. La "Failure Analysis" ou recherche de la cause de la défaillance est donc cruciale dans le processus d'amélioration continue. Ce n'est que lorsque la cause est connue que les bonnes mesures peuvent être prises pour prévenir les défaillances futures.
Les matériaux défaillants contiennent plusieurs traces qui, une fois rassemblées, peuvent permettre de trouver la cause de la défaillance. Cela nécessite non seulement l'utilisation de techniques d'investigation appropriées, mais aussi l'intervention de chercheurs expérimentés. L'interprétation correcte des mesures, associée à l'expérience et aux connaissances des experts, permet de trouver la cause de la défaillance. Une fois la cause connue, des conseils peuvent être formulés pour éviter la défaillance dans les applications futures.
Sur la base de deux études de cas, cet article explique les techniques couramment utilisées dans l'examen des dégâts. Dans les exemples ci-dessous, les observations externes sont similaires: des fuites dan les conduites en acier inoxydable. Mais la cause est différente, ce qui implique des solutions différentes.
Cas: corrosion induite par des micro-organismes
Peu après l'achèvement d'un système de tuyauterie en acier inoxydable, des fuites ont été détectées. Une section de conduite a été retirée pour être inspectée et examinée à l'aide d'une combinaison de techniques.
Examen visuel
Dans un premier temps, les conduites ont été inspectées à l'intérieur à l'œil nu. Les points suivants ont été identifiés (voir figure 1): les fuites sont situées près des soudures, des vésicules de corrosion sont observées près des fuites et il y a une décoloration irisée de l'acier inoxydable, à partir de l'emplacement des fuites.

Microscopie optique
Des coupes transversales ont ensuite été réalisées sur plusieurs fuites. Pour ce faire, l'acier a été tronçonné, encastré, poncé, poli et attaqué à l'aide d'acides mélangés. La coupe transversale a été observée au microscope optique (voir figure 2): la zone de soudure présente plusieurs cavités sous-cutanées.
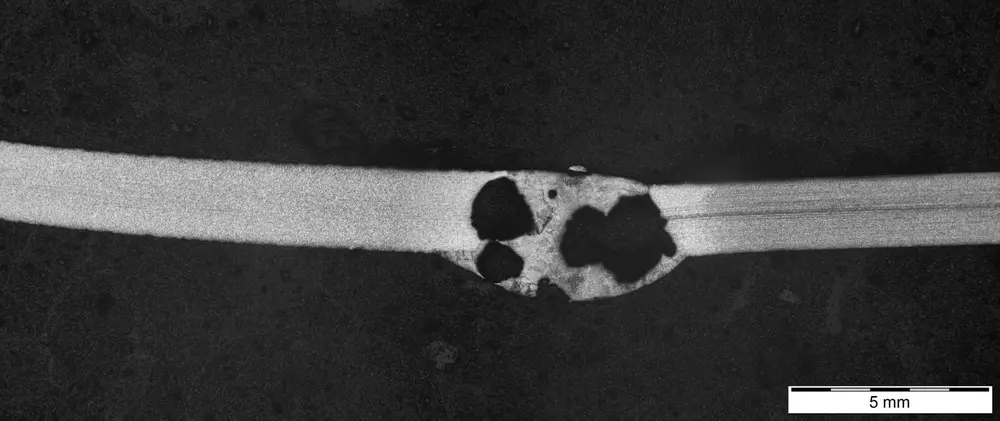
Microscopie électronique à balayage (Scanning Electron Microscopy,SEM)
Au niveau d'une autre fuite, la pustule a été enlevée. La surface du tube au niveau de la fuite a été examinée avec la SEM. Dans cette technique, un faisceau d'électrons frappe la surface. Celle-ci interagit avec les atomes, émet et détecte différents signaux. La détection des électrons secondaires permet de créer des images en 3D de la surface. L'une de ces images (voir figure 3) montre comment la corrosion affecte préférentiellement l'une des phases de la soudure: la phase dendritique est affectée, tandis que la phase interdentritique est laissée en place.
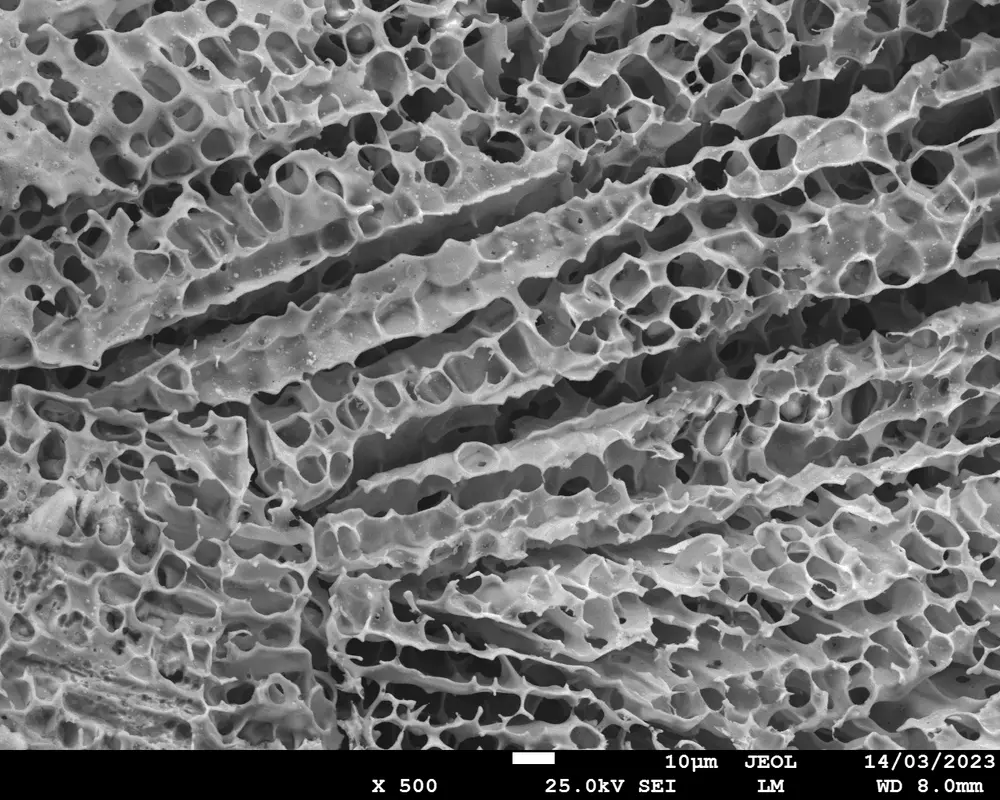
SEM-EDX: Spectroscopie de rayons X à dispersion d'énergie (Electron Dispersive X-ray)
Enfin, la composition des pustules a également été mesurée à l'aide du signal EDX de la MEB. En interagissant avec les électrons incidents de la SEM, les atomes de l'échantillon émettent une énergie spécifique. Sur la base de la valeur de l'énergie et de l'intensité du signal, la composition d'un matériau peut être déterminée de manière semi-quantitative. On a ainsi constaté un enrichissement en chrome au niveau des pustules: jusqu'à 30% en poids de chrome dans les pustules contre 19% dans l'acier inoxydable lui-même.
Cause de la défaillance
L'ensemble des observations ci-dessus indique une corrosion induite par les micro-organismes (CIM). Il s'agit d'un type de corrosion localisée dans lequel les bactéries sécrètent des substances corrosives, telles que des acides. Ces substances renforcent le processus de corrosion et, à leur tour, incitent les bactéries à se développer davantage. Le processus se poursuit en continu. Comme il se produit localement, il y a des fuites soudaines.
La vitesse de corrosion CIM dans l'acier inoxydable peut atteindre 0,5 à 1,5 mm/mois, selon les conditions. La CIM se produit généralement dans des eaux stagnantes ou à faible débit (polluées). En effet, cela permet aux bactéries d'adhérer à la surface. Plus la surface est rugueuse, plus il y a de points d'adhésion. Par conséquent, la CIM commence souvent au niveau des soudures, bien qu'elle puisse tout aussi bien se produire sur des surfaces lisses.
Pour prévenir la détérioration due à la CIM, il est important de vérifier la qualité de l'eau, d'éviter la stagnation ou l'écoulement lent de l'eau contaminée. La CIM est également souvent observée après un essai de pression avec de l'eau contaminée (par exemple l'eau du canal) et/ou un séchage insuffisant après l'essai.
Cas: fissuration par corrosion sous contrainte (stress corrosion cracking)
Chez un autre client, la tuyauterie en acier inoxydable présentait également des fuites, mais la cause n'était pas la même que dans le cas précédent. Une combinaison de techniques a de nouveau été utilisée.
Microscopie optique
Une coupe transversale de la conduite (voir figure 4) montre comment plusieurs fissures apparaissent sur la surface intérieure. Une fissure passe de la surface intérieure à la surface extérieure, ce qui entraîne des fuites. À un plus fort grossissement (voir figure 5), on peut voir que les fissures proviennent d'une attaque par piqûres sur la surface intérieure et que les fissures présentent un fort degré de ramification. Après la gravure et à un grossissement encore plus important (voir figure 6), on peut voir que les fissures traversent les grains. On parle alors de fissures transgranulaires.
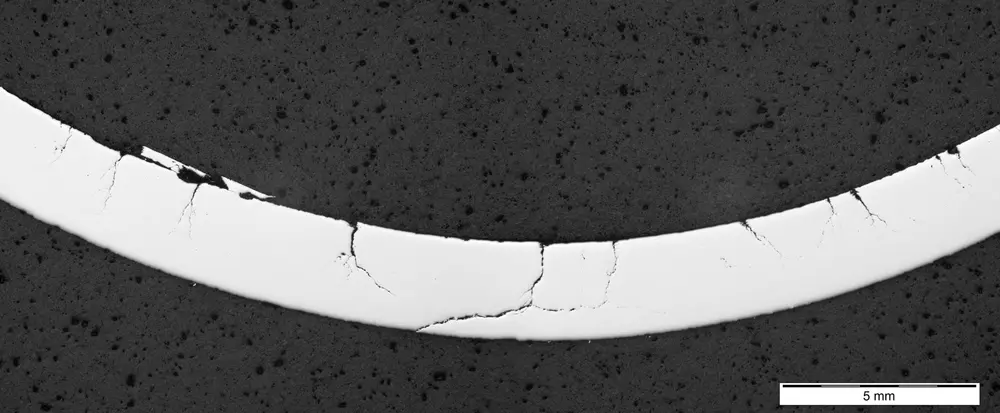
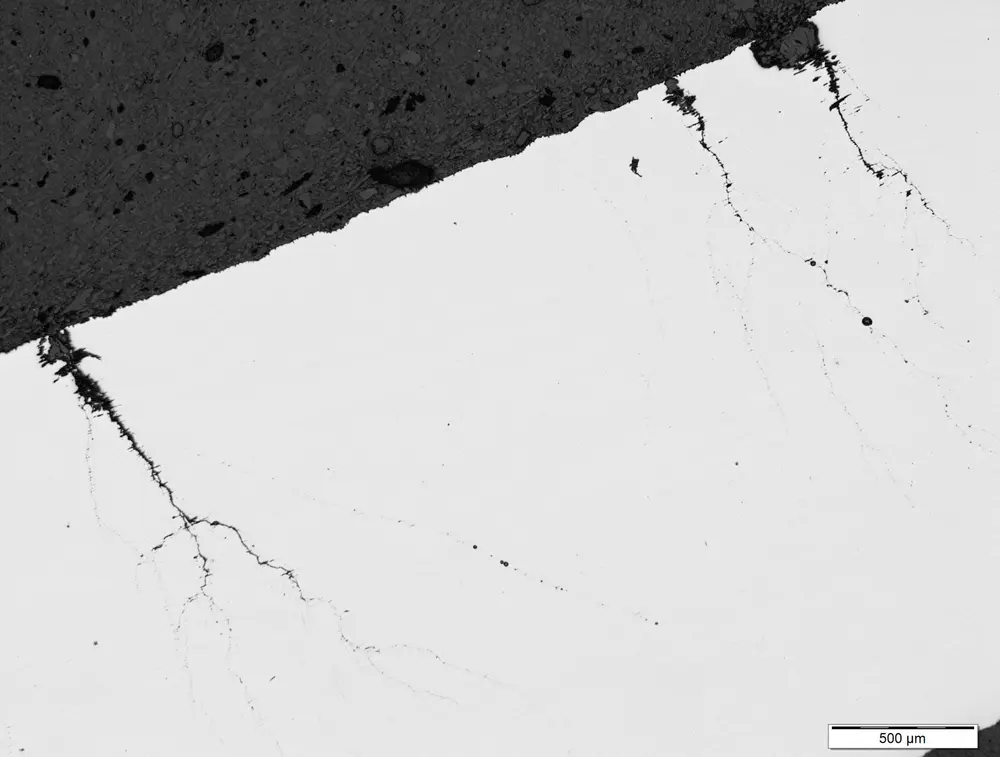
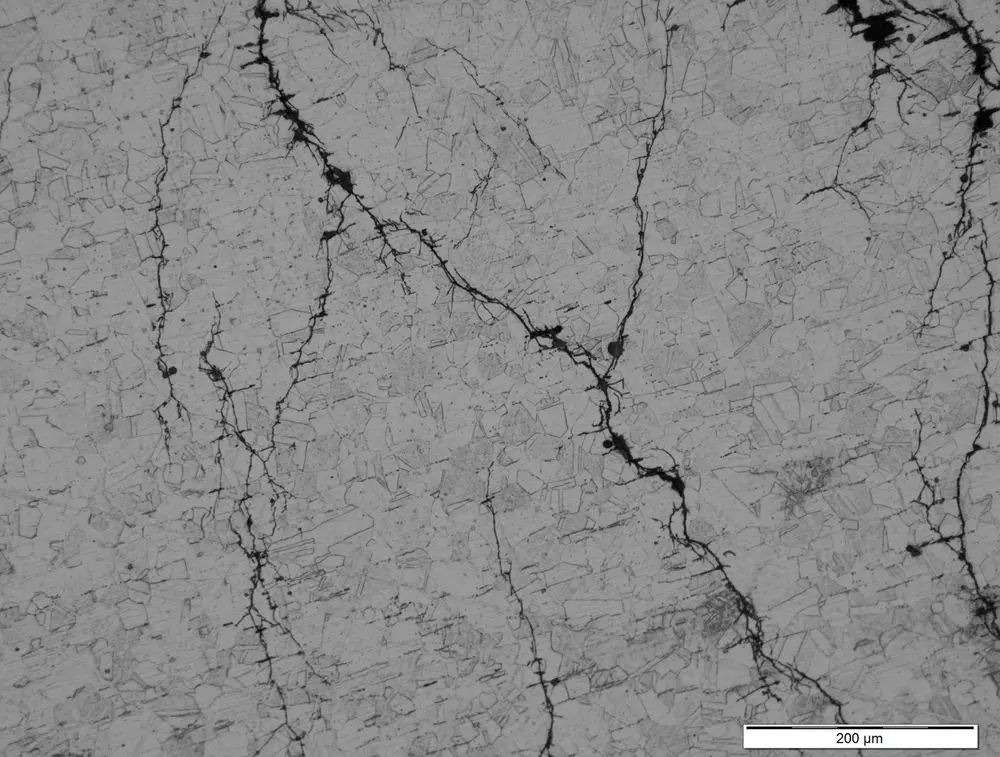
SEM et SEM-EXD
Une autre fissure dans le tube a été ouverte afin d'observer la surface de la fissure avec la SEM. La surface de la fissure présente un aspect de clivage (voir figure 7).
Enfin, la composition des matériaux à la surface de la fissure est mesurée à l'aide de la SEM-EDX. Le spectre est donné dans la figure 8: l'axe x montre l'énergie du signal et l'axe y l'intensité. Dans un premier temps, les éléments de l'acier inoxydable sont détectés: fer (Fe), chrome (Cr), nickel (Ni), molybdène (Mo), manganèse (Mn) et silicium (Si). En outre, on note principalement la présence de carbone (C) et d'oxygène (O). Enfin, on trouve également du phosphore (P) et du chlore (Cl), du sodium (Na), de l'aluminium (Al), du potassium (K) et du vanadium (V).
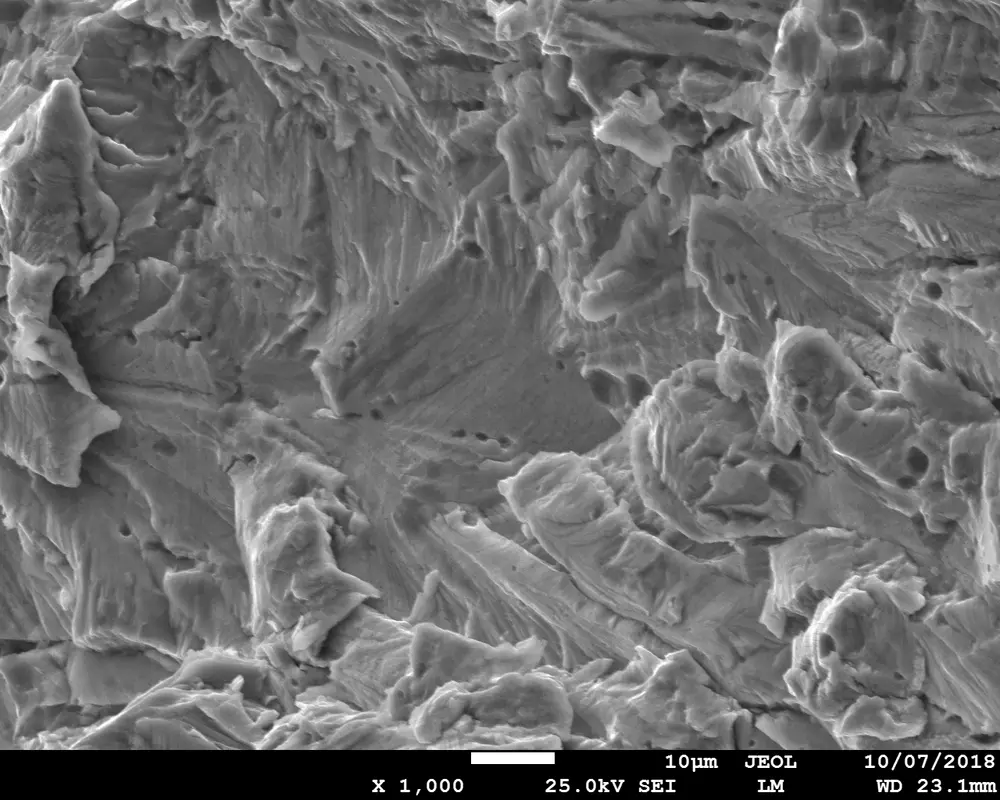
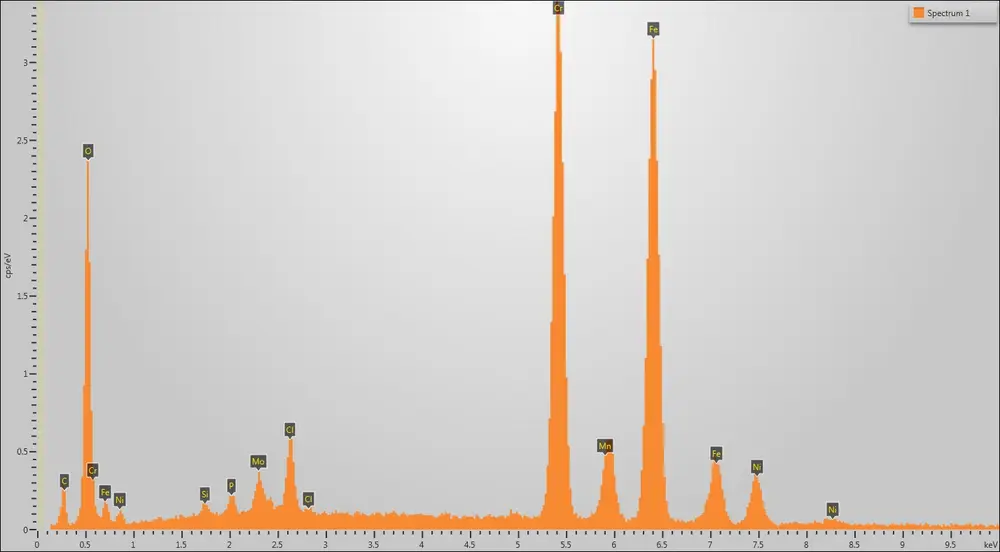
Cause de la défaillance
L'ensemble de ces observations indique une détérioration due à une fissuration par corrosion sous contrainte (SCC), avec une initiation à l'intérieur de la conduite.
Pour que la SCC se produise, trois conditions doivent être réunies: le matériau doit être sensible à SCC, des contraintes doivent être présentes dans le matériau et le matériau doit se trouver dans un milieu corrosif. L'acier inoxydable est susceptible de subir une CSC en présence de chlorures à des températures supérieures à 60 °C. Des contraintes peuvent être présentes en raison des conditions du processus ou en tant que contraintes résiduelles de la fabrication.
Pour éviter la SCC, l'une des trois conditions doit être supprimée. Comme il n'est pas possible de changer de milieu dans ce cas, il est recommandé d'opter pour des aciers inoxydables duplex ou des aciers inoxydables contenant plus de 25% de nickel. Ces alliages offrent une meilleure résistance à ce type de corrosion sous contrainte.