Duurzame automatisering gaat veel verder dan de aanschaf van een zuinige machine
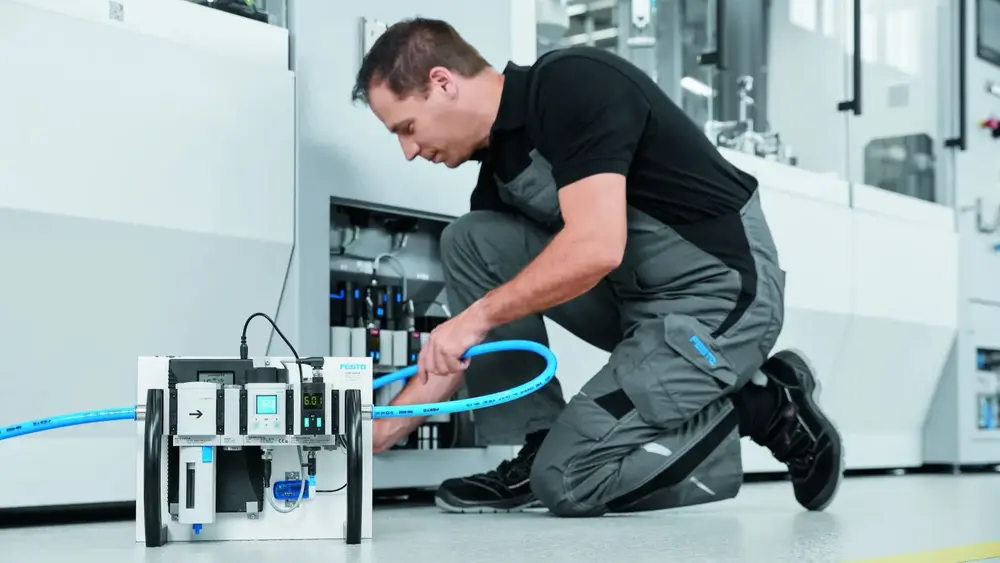
Bedrijven die duurzaam willen automatiseren, focussen doorgaans op individuele componenten. Zo koopt men bijvoorbeeld een zuinigere motor. Deze oplossing is vrij eenvoudig en behapbaar, maar een verregaande optimalisatie van het volledige systeem kan nog heel wat meer efficiëntiewinst opleveren. Hoe kan men door het vergaren van data en een holistische kijk op het systeem duurzamer automatiseren en energie besparen?
Wat is duurzame automatisering?
Het vervangen van een machine door een nog zuinigere machine is natuurlijk de meest voor de hand liggende manier om het energieverbruik te verminderen. Vandaag de dag hebben veel bedrijven deze relatief eenvoudige stap al achter de rug. Voor de overige grote verbruikers is het huidige verbruik niet gekend, zijn de investeringskosten te groot of is het verschil in efficiëntie te klein.
Minder bekend is het gegeven dat er op systeemniveau vaak veel meer winst valt te behalen dan op het niveau van de individuele component. Deze holistische kijk op systeemniveau noemt men duurzame automatisering - een mooi, maar ook een breed begrip. In het algemeen is een combinatie van drie zaken van belang:
- Hoe efficiënt draait de machine? Dit heeft te maken met het gebruik van energiebronnen, zoals gas, water, perslucht en stoom.
- Hoe effectief gebruikt een bedrijf de machine? Zorg ervoor dat een machine optimaal draait, want een stilstaande machine voegt niets toe aan het productieproces.
- Wordt de machine functioneel gebruikt? De inzet van machines kan medewerkers ontlasten van zware, gevaarlijke of repetitieve werkzaamheden, mits dit op de juist wijze gebeurt - dat wil zeggen vlot én veilig.
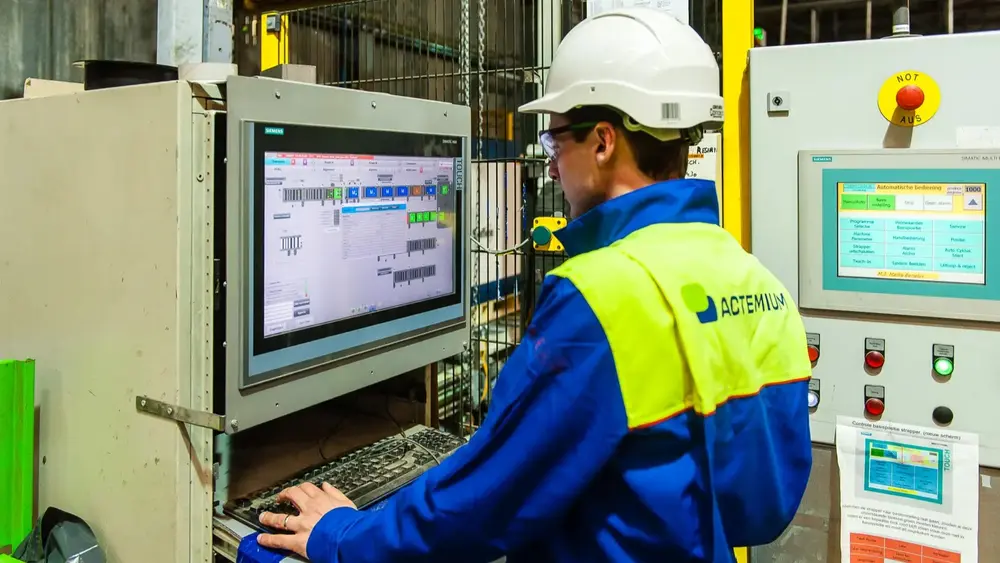
Digitale aanpak
Duurzame automatisering omvat dus meer stappen dan enkel het vervangen van niet-efficiënte verbruikers door meer efficiënte equivalenten. Een efficiëntere aansturing en controle kan veel meer impact hebben dan hetzelfde blijven doen met betere componenten.
Denk hierbij aan een regeling met frequentiesturing in plaats van een klepregeling van een pomp, het verminderen van de snelheid van een transportband bij een kleiner gevraagd debiet, of het uitschakelen van verbruikers als ze niet nodig zijn.
De uitvoering van deze aanpassingen zijn vaak al mogelijk met klassieke automatisering. Om te weten welke systemen geoptimaliseerd kunnen worden, op welke manier en wat de winst is, is vaak een digitale aanpak (met data of simulatie) nodig.
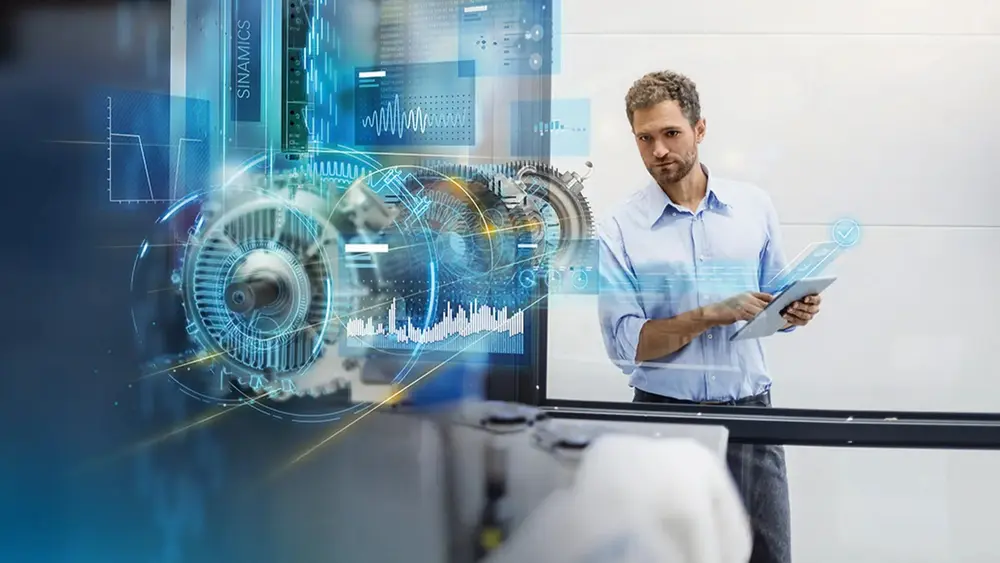
Voorbeelden van optimalisatie
Hergebruik
Het vervangen van een component door een efficiënter exemplaar brengt logischerwijs een nadeel met zich mee: een nog werkend toestel wordt uit dienst genomen, terwijl een nieuw toestel op zijn beurt ook voor uitstoot zorgt. Wat decarbonisatie betreft moet de vermindering in uitstoot in de productie dus de extra uitstoot van het nieuwe toestel verantwoorden. Het hergebruik van het toestel als spare part in stock of het gebruiken van refurbished parts kan de impact van het nieuwe toestel minimaliseren.
Een duurzaam alternatief voor een nieuwe machine is het reviseren of retrofitten van bestaande installaties. Door het vervangen van obsolete onderdelen en het toevoegen van bepaalde sensoren kan een machine terug 20 jaar zorgeloos werken. Bovendien zorgen deze sensoren voor meer feedback naar de gebruiker toe, die hierdoor de efficiëntie en dus de duurzaamheid kan verhogen.
Ideale timing
Een ander voorbeeld is het gebruik van predictief onderhoud om de levensduur van componenten te verlengen. Vandaag worden veel componenten (motoren, tandwielkasten en kleppen bijvoorbeeld) preventief vervangen op basis van de levensduur, zelfs als deze nog perfect in orde zijn. Predictief onderhoud laat een onderhoudsafdeling toe om de componenten te vervangen op exact het juiste moment. Dit maximaliseert de levensduur én vermindert het risico op ongeplande stilstand. Hierbij wordt gebruik gemaakt van AI.
Predictief onderhoud laat een onderhoudsafdeling toe om de componenten te vervangen op exact het juiste moment
Besparingen
Een verlaging van de werkdruk van een persluchtsysteem kan 14% energie besparen, zo blijkt uit onderzoek. Een fabriek met circa 90 kW vermogen aan compressoren kan al gauw 270.000 kWh per jaar besparen. Dat is het equivalent van bijna 80 huishoudens. Besparen kan ook bij vacuüm, dat veel wordt gebruikt bij het oppakken van producten. Door het toepassen van spaarregelingen kan tot 80% vacuüm bespaard worden. Voor een gemiddelde vacuümgenerator is dit ruim 600 kg CO2 per jaar.
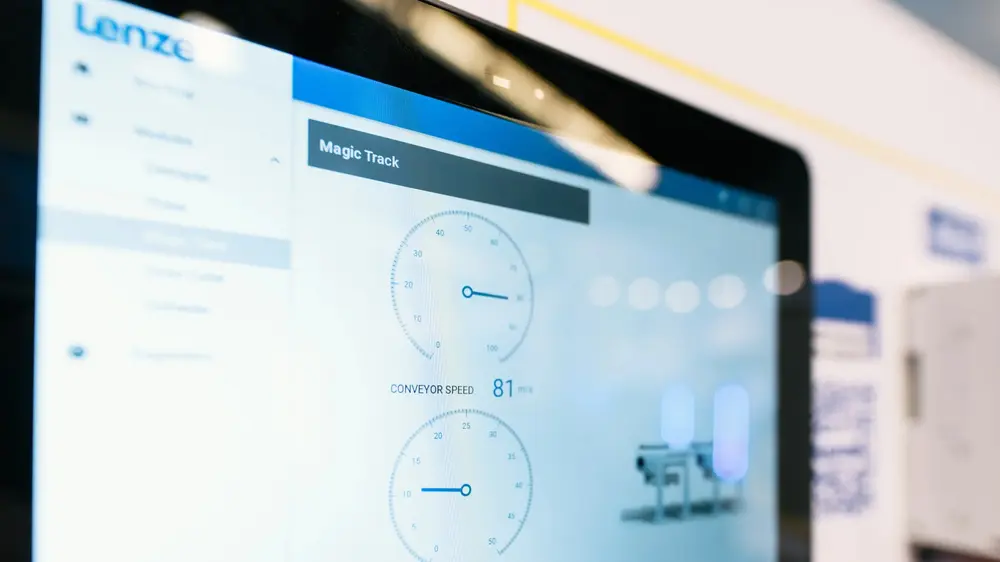
Een grote verandering is dat bedrijven nu veel vaker kijken naar het gebruik van de juiste energiebron per toepassing. Zo zijn servomotoren vaak zuiniger dan perslucht, maar niet in alle gevallen. Kies dus niet voor het een of het ander, maar stel per functie de vraag welke bron de meest geschikte is.
Uitdagingen bij optimalisatie
Ontdekken waar en hoeveel winst er te behalen valt: dat is een van de voornaamste uitdagingen bij duurzame automatisering. Data en simulatie zijn twee handige maar ook uitdagende tools die bedrijven hierbij kunnen inzetten.
Data
Dankzij data kunnen bedrijven ontdekken hoeveel energie door welke verbruikers op welk moment verbruikt wordt. In veel productieomgevingen wordt deze data echter niet naar een centrale plaats gebracht, waardoor bedrijven niet weten waar hun energieverbruik vandaan komt. Hierbij kan een energiemonitoringsysteem van pas komen. Met behulp van dit systeem wordt onderzocht hoe data bestaande meters (apart of geïntegreerd in bijvoorbeeld frequentiesturingen) naar een centrale plaats kunnen communiceren (cloud, Edge of bestaande server).
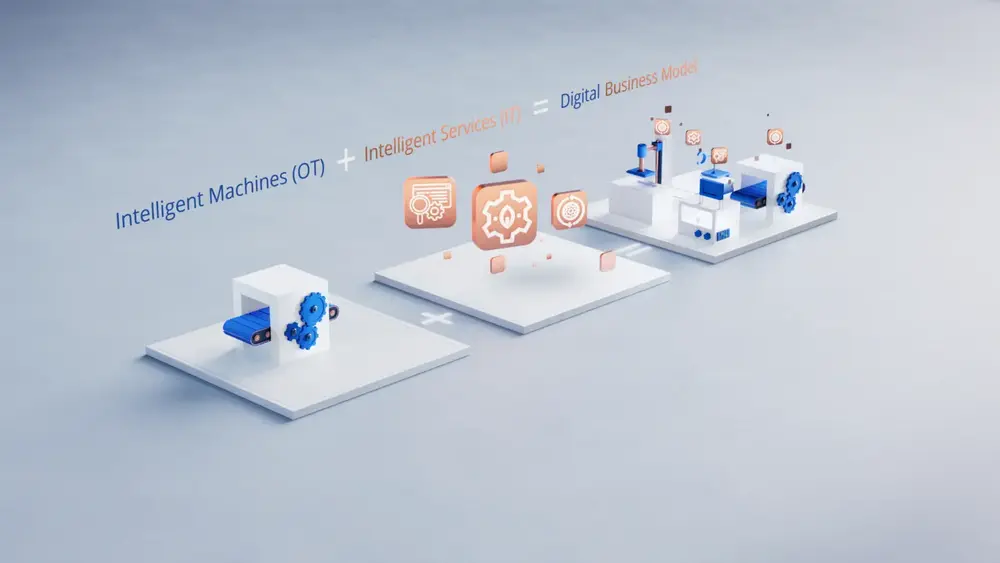
Simulatie
Bij nieuwe productielijnen is simulatie de eerste stap. Door energie op te nemen als KPI bij het digitale ontwerp van een productielijn, kan het ontwerp makkelijker worden geoptimaliseerd naar energieverbruik. Daarnaast heeft simulatie nog secundaire voordelen wat betreft duurzaamheid. Bijvoorbeeld een betere dimensionering van componenten en dus ook een efficiëntere werking en minder kans op beschadigingen tijdens de opstart.
Ook bij bestaande lijnen is simulatie nuttig: het kan gebruikt worden om what if-scenario's te testen. Het aanpassen van de controle heeft vaak invloed op het energieverbruik én op de kwaliteit van het product. Het eerst testen in een virtuele omgeving helpt om onvoorziene effecten te vinden en het risico op fouten te verminderen.
Door energie op te nemen als KPI bij het digitale ontwerp van een productielijn, kan het ontwerp makkelijker worden geoptimaliseerd naar energieverbruik
Mindset
Machinebouwers voelen vaak nog onvoldoende prikkels om zo energiezuinig mogelijk te produceren, omdat deze werkwijze de kostprijs verhoogt. Daardoor is de kans kleiner dat eindgebruikers de machine zullen kopen. Een andere, holistische mindset zorgt ervoor dat de kostprijs niet de belangrijkste drijfveer is bij de aanschaf van een machine, maar eindgebruikers minstens zoveel rekening houden met zaken als de output, het energieverbruik en het onderhoud ervan.
Zo is bijvoorbeeld een unit die een ongebruikte machine automatisch afsluit op zichzelf relatief duur. Maar door het positieve effect kan deze investering al binnen enkele jaren terugverdiend zijn, terwijl de machine vaak wel twintig tot dertig jaar meegaat.
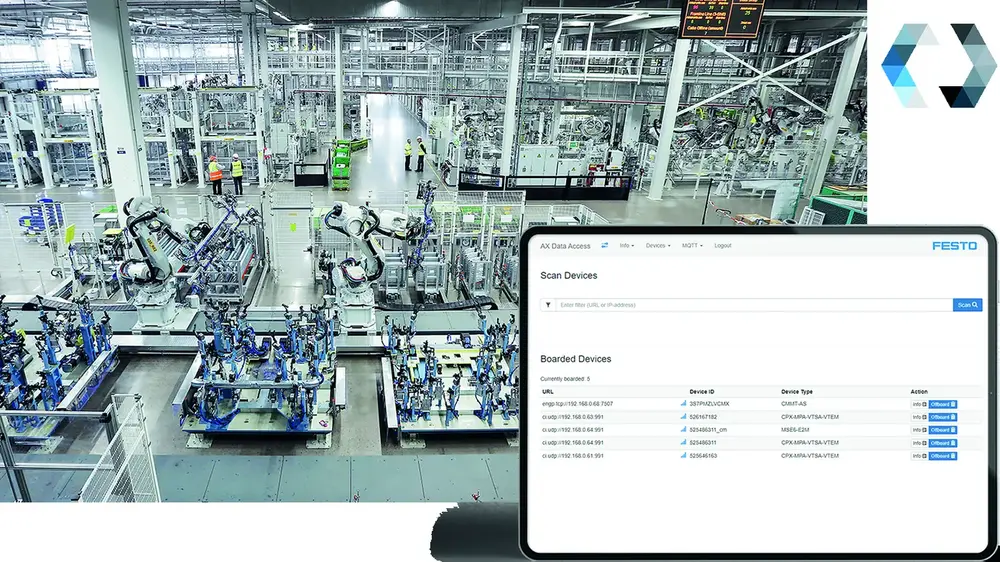
Wat brengt de toekomst?
In de toekomst zal de interactie tussen de systemen intelligenter worden. Een energiemonitoringsysteem gecombineerd met productiedata zal zelf afwijkingen detecteren en suggesties geven voor optimalisatie. Het achterliggende systeem zal eerst de suggestie testen op een digital twin om zeker te zijn dat er geen negatieve productie-impact is en automatisch de nodige aanpassingen doen in de PLC.
AI zal toelaten om data eenvoudiger te kunnen interpreteren. Het laat toe zonder kennis van programmeren de nodige info op te roepen en te vergelijken. Zo kunnen mensen met kennis van productie, maar met minder kennis van IT sneller optimaliseren. AI laat ook toe om energiemonitoringsystemen betere suggesties te laten geven.
Met medewerking van Actemium, Beckhoff Automation, Festo, Lenze en Siemens