meer doen met minder
Gas Solid Vortex Reactor: procesintensificatie in al zijn facetten
Wat is er nodig voor procesintensificatie bij wervelbedreactoren? Het was de vraag die prof. dr. ir. Geraldine Heynderickx zich begin jaren 2000 stelde en die de bal aan het rollen bracht. Het resultaat is vandaag drie varianten van de gas solid vortex reactor, die door de uitstekende warmte- en massaoverdracht de deur opent voor een meer duurzame procesindustrie.
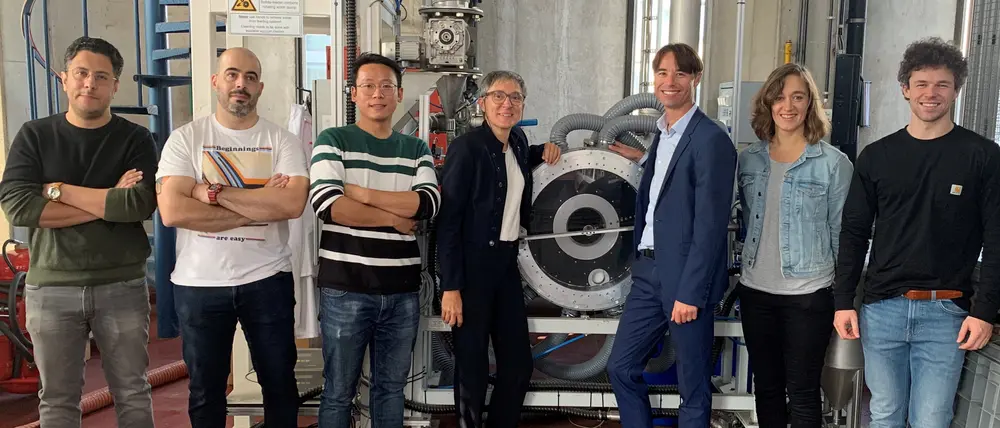
Centrifugaalkracht als uitgangspunt
Werveldbedreactoren zijn populair voor het uitvoeren van meerfasige chemische reacties omdat ze garant staan voor een meer uniforme menging van partikels en meer uniforme temperaturen. Maar ze hebben ook hun beperkingen zoals trage warmte- en massatransfer tussen fases. Zomaar het voedingsdebiet opschroeven is niet mogelijk, vaak moeten het dan bijzonder grote reactoren worden. Maar hoe kan het dan wel ‘meer met minder’ worden?
Prof. dr. ir. Geraldine Heynderickx en haar team vonden het antwoord in centrifugaalkracht. “De uitdaging bestond erin om centrifugaalkracht te genereren zonder een bewegende reactor nodig te hebben. Door gassen in een zelf ontworpen reactor te injecteren via tangentieel gerichte inlaatgleuven zijn we erin geslaagd een roterend bed aan deeltjes te realiseren.” De hoge centrifugale versnelling van meer dan 30 g genereert hogere slipsnelheden, meer uniformiteit in de pakking van bed, en dus intensere warmte- en massaoverdrachten tussen fasen.
Naar een mooi gestructureerd wervelbed
De eerste niet-bewegende gas solid vortex reactor met wervelbed werd in 2010 aan de wereld voorgesteld. Maar daar gingen wel jaren van berekeningen aan vooraf. “Door de toepassing van numerieke stromingsleer (CFD) hadden we 36 mogelijke varianten berekend. We hebben er de zes meest veelbelovende uit geselecteerd voor een eerste publicatie om dan uiteindelijk tot één ontwerp te komen”, aldus Heynderickx. Die cilindrische setup werd ook effectief gebouwd. Met 0,5 m diameter en 10 cm mantelhoogte was die flink uit de kluiten gewassen met een grote compressor naast zich om de hoge gasdebieten te genereren. Met de hulp van Particle Image Velocimetry (PIV) werd de beweging van deeltjes gevolgd.
“Er ontstond een mooi gestructureerd wervelbed, waarmee we het bewijs hadden dat het idee praktisch werkt. Vervolgens was het zaak om dit grondwerk verder te kunnen uitbreiden naar hogere temperaturen. We hadden het vermoeden dat we met onze reactor een betere warmteoverdracht zouden kunnen realiseren dan in klassieke wervelbedreactoren. Een tweede, eenvoudiger, ontwerp van de gas solid vortex reactor bevestigde dat: uniforme temperatuurprofielen werden gemeten met een infraroodcamera.”
Driemaal is scheepsrecht
Intussen werd ook al een derde reactor gebouwd, complementair aan de eerste twee, om reacties bij hoge temperaturen mogelijk te maken. “Deze hebben we ontworpen en getest met pyrolyse van biomassa en een nog meer compacte opstelling voor ogen.”
Aan het woord is Prof. dr. Kevin Van Geem die de onderzoeksgroep enkele jaren geleden kwam versterken. “De grote vraag was hoe het biomassamateriaal eruit zou komen? Het resultaat was bijzonder: naast goede omzetting vormde de lichtere ‘char’ een separate laag: segregatie werd vastgesteld waarbij dit nevenproduct gemakkelijk kon worden afgescheiden. Typische opbrengsten voor dit soort toepassingen liggen maximaal op 65%. Onze reactor zette een opbrengst van 75% neer of meer. Dat verschil lijkt misschien weinig, maar voor bijvoorbeeld raffinageprocessen is dit een gigantische stap vooruit. De grote kracht van de technologie is dat we materiaal kunnen omzetten met een zeer goede warmteoverdracht en een mooie vermenging van de fasen en segregatie van verschillende vaste materialen. Je kan op die manier eigenlijk perfect de condities instellen die je wil. Dat we er al van bij de eerste poging zo een mooie opbrengst uit halen doet dan fantastisch deugd. Bovendien hebben we ook veel tijd gestoken in het ontwerpen van modellen. Rekenresultaten worden gevalideerd met meetresultaten. Ik krijg er nog altijd kippenvel van”, vertelt Van Geem enthousiast.
Blijven verrassen
“De gas solid vortex reactor verrast ons steeds opnieuw”, vult Heynderickx aan. “Het ontwerp kan makkelijk aangepast worden. Waar we bij de eerste twee reactoren uitgingen van een octopusachtig ontwerp, waarbij de gasinvoer verdeeld werden over verschillende zij-ingangen, gebeurt de gastoevoer in het derde model via een enkele ingang. Dat dit evengoed kan werken, heeft ermee te maken dat we, wederom door uitvoerige CFD-berekeningen, ook andere punten in het ontwerp veranderden. Zo bleek het profiel van de bodemplaat cruciaal om minder afzettingen en nog betere stromingspatronen binnenin de reactor te realiseren. Daarnaast is de ring met inlaatgleuven een cruciale ontwerpparameter om een mooie verdeling van het gas te verkrijgen. In functie van de applicatie kan het ontwerp van de volledige reactor aangepast worden.”
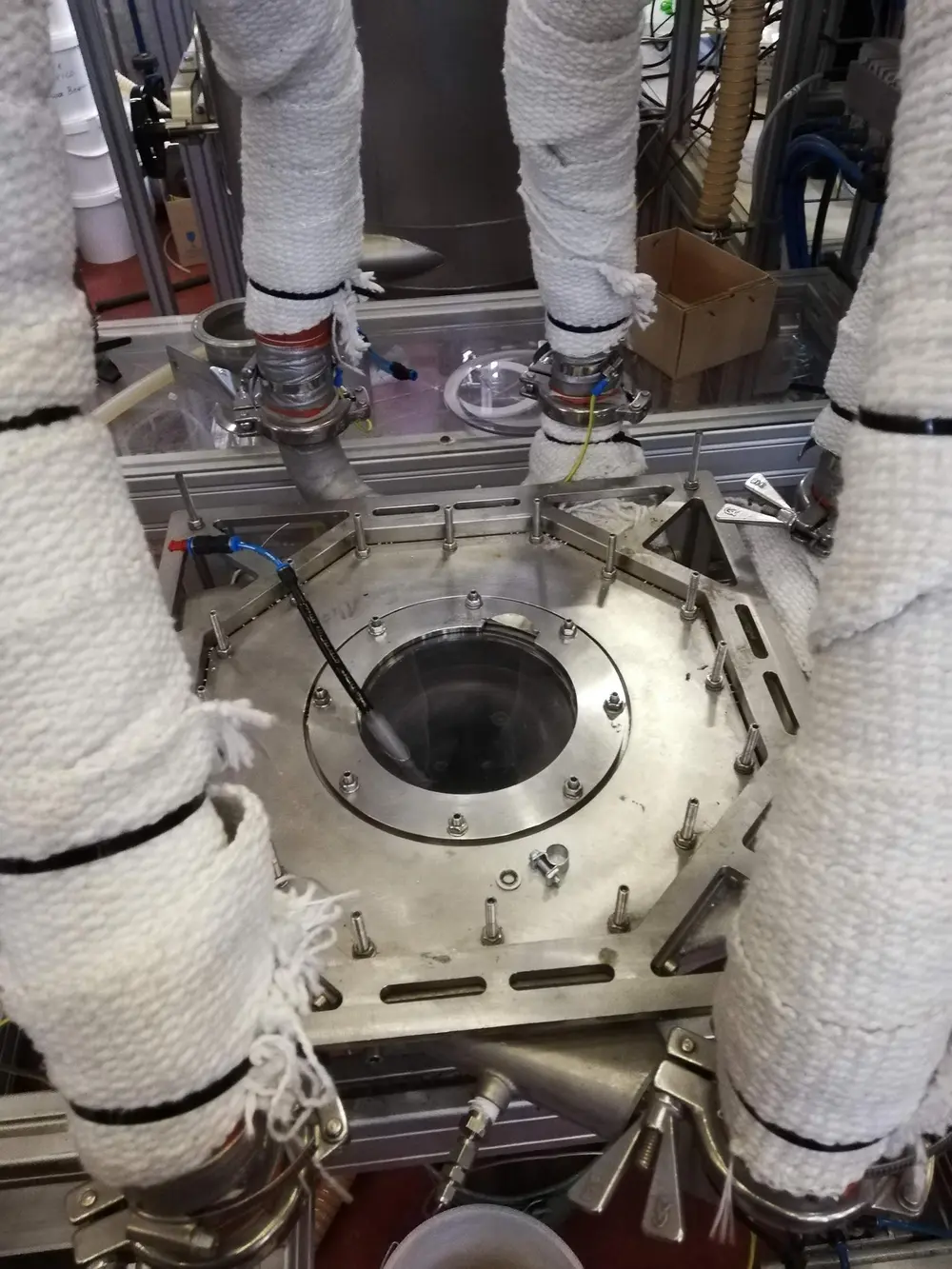
Klaar voor de procesindustrie
Met deze drie ontwerpen willen Heynderickx en Van Geem nu op zoek gaan naar concrete toepassingen in de industrie voor ‘hun’ gas solid vortex reactor. Ze hopen dat hij binnen vijf jaar die stap gezet heeft. In eerste instantie wordt gedacht aan pyrolyse van biomassa en verwerking van plastics (chemische recyclage), aan het drogen van poeders tot extreem lage vochtgehaltes, maar ook in de voedingsindustrie liggen er veel mogelijkheden. “Bij de verwerking van cacaobonen bijvoorbeeld kunnen we drie afzonderlijke stappen tegelijk combineren in een proces in onze reactor: uit de schil halen (deshelling), uniformisering en roosteren. Er is dus nog heel veel moois mogelijk. Zijn compacte afmetingen, de hoge warmte- en massaoverdracht, waardoor een korte verblijftijd in de reactor mogelijk is, en de hoge efficiëntie van omzetting zijn alvast onmiskenbare troeven. Het blijft natuurlijk een grote investering, maar door onze onderbouwing met onder andere CFD kunnen we wel heel sterke bewijzen voorleggen dat de gas solid vortex reactor toegevoegde waarde kan brengen. Wij kunnen technology readiness level 5 voorleggen, maar de industrie vraagt om 9. Voor die sprong zoeken we dus fondsen.”
“We hopen op termijn te kunnen bijdragen tot de oxidatieve koppeling van methaan (OCM),
een veelbelovend proces waarbij methaan als grondstof voor ethyleenproductie gebruikt wordt”
Zoeken naar meer variatie
Toch blijft men ook binnen de universiteit van Gent hard werken aan de gas solid vortex reactor. De bedoeling is om te onderzoeken waar in de procesindustrie hij nog een meerwaarde kan zijn.
Van Geem: “We hopen op termijn met de gas solid vortex reactor te kunnen bijdragen tot de oxidatieve koppeling van methaan. Dit is zo een beetje de heilige graal voor de chemische industrie, waar men een alternatieve manier zoekt om uit goedkoop aardgas, ethyleen te maken, de basisgrondstof voor polyethyleen en vele andere kunststoffen. Ethyleen wordt nu geproduceerd door ruwe aardoliefracties te kraken in gasgestookte ovens aan hoge temperaturen waarbij bijzonder veel CO2 in de atmosfeer terechtkomt. Oxidatieve koppeling van methaan (OCM) is een veelbelovend proces waarbij methaan als grondstof voor ethyleenproductie gebruikt wordt. De enorme warmte die vrijkomt tijdens het proces (dit in tegenstelling tot de enorme warmte-input die nodig is voor klassieke ethyleenproductie), vormt een van de belangrijkste uitdagingen die getrotseerd moeten worden vooraleer OCM op industriële schaal kan toegepast worden. Daar kan de gas solid vortex reactor een oplossing voor bieden.”
CO2 uit de lucht halen
Een andere piste die nog verkend wordt, is in plaats van een gas en een vaste stof tot een perfecte mix te brengen, het vizier te verruimen naar gassen en vloeistoffen.
Heynderickx: “In de vermelde tweede eenheid zijn we er al in geslaagd om water en lucht samen te laten bewegen met als resultaat een sprayflow of een bubbly flow. We willen hierop verder bouwen en kijken of we CO2 uit de lucht kunnen extraheren met behulp van geschikte vloeistoffen in kader van het Moonshot project van de Vlaamse overheid.” Dat blijft voorlopig toekomstmuziek. “We hebben niet de gewoonte erin te vliegen, maar brengen eerst alles zo goed mogelijk in kaart, ook met het oog op validatie van simulatieresultaten. Om hierin te slagen zullen we eerst de gas/vloeistof hydrodynamica in de eenheid op punt stellen met variërende lucht/waterdebieten. Pas daarna wordt de CO2-extractie zelf onderzocht, met een vloeistof met geschikte extractie-eigenschappen. We controleren dus eerst of de hydrodynamica goed zitten, om dan ook de bijkomende massatransfer te bestuderen. Pas als we er echt van overtuigd zijn dat het met de gas vloeistof vortex reactor CO2-extractie beter en efficiënter kan, willen we de toepassing verder ontwikkelen. En dat de vortex reactor voor verschillende combinaties van fases een bijdrage kan leveren tot duurzaamheid en intensificatie in de procesindustrie, is drijfveer genoeg om zijn verdere mogelijkheden te blijven onderzoeken. Zoals gezegd, de vortex reactor weet ons altijd weer te verrassen”, besluit Heynderickx.
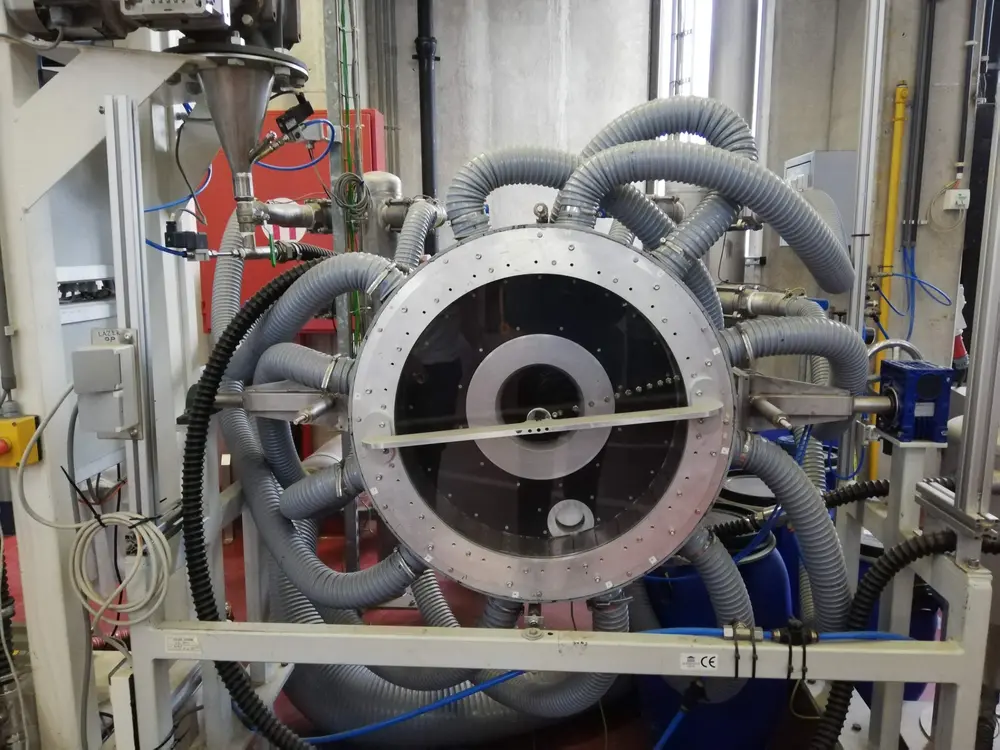