Ontwikkelingen lasersnijden gaan door
technologische innovatie en procesbeheersing zijn 'hot'
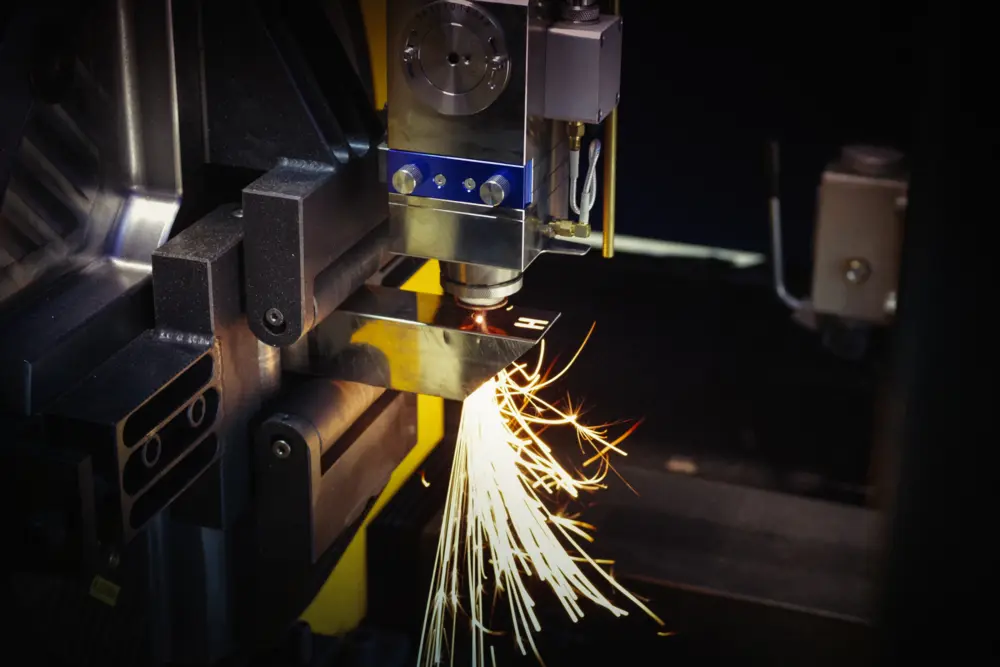
Lasersnijden heeft sinds de introductie in 1965 als techniek een groot aantal ontwikkelingen doorgemaakt en is nog altijd volop in beweging. Enerzijds zijn er de snijtechnologische innovaties, anderzijds ontwikkelingen op het gebied van procesondersteuning en -integratie, met als ultiem doel de autonome plaatwerkfabriek. Tijd voor een tussenbalans met Kurt van de Collie (LVD), Luc Creemers (Yamazaki Mazak), Matthieu Deram (Haco), Marc Leeman (Metanox), Hans van de Meerakker (Bystronic) en Karel Vincke (V.A.C. Machines).
Technologische innovaties
Fiberlaser
De fiberlaser wint steeds meer terrein ten opzichte van de CO₂-laser. Volgens sommigen zal die techniek gaandeweg verdwijnen terwijl die volgens anderen voor bepaalde toepassingen toonaangevend zal blijven. De tijdens het gesprek genoemde percentages variëren weliswaar – 90 om 10%, 95 om 5% −, maar vallen allemaal uit in het voordeel van de fiberlaser. Haco en LVD zijn al enkele jaren gereden volledig gestopt met de verkoop van machines met CO₂-lasers en dat geldt ook voor Metanox. Bij Mazak is de CO₂-variant nog altijd beschikbaar, maar de verwachting is dat dat niet lang meer zal duren. Bij Bystronic worden alleen nog de nog bestaande producten uitgefaseerd.
Deram (Haco) onderkent de leidende positie van de fiberlaser, maar merkt op dat de CO₂-laser nog een groot aandeel heeft in toepassingen als het snijden en lassen van organische materialen. Karel Vincke (V.A.C. Machines) rekent zichzelf tot de ‘believers’ in de CO₂-technologie: “Beide technologieën hebben hun sterke punten, maar bij CO₂ is de snijkwaliteit bij sommige toepassingen nog altijd hoger dan bij fiber.” LVD bekleedt een uitzonderingspositie. Van Collie: “Voor zover ik kan inschatten is 95% van de verkochte lasers een ‘solid state laser’. We praten over solid state aangezien Trumpf vooralsnog de voorkeur geeft aan de disklasertechnologie.”
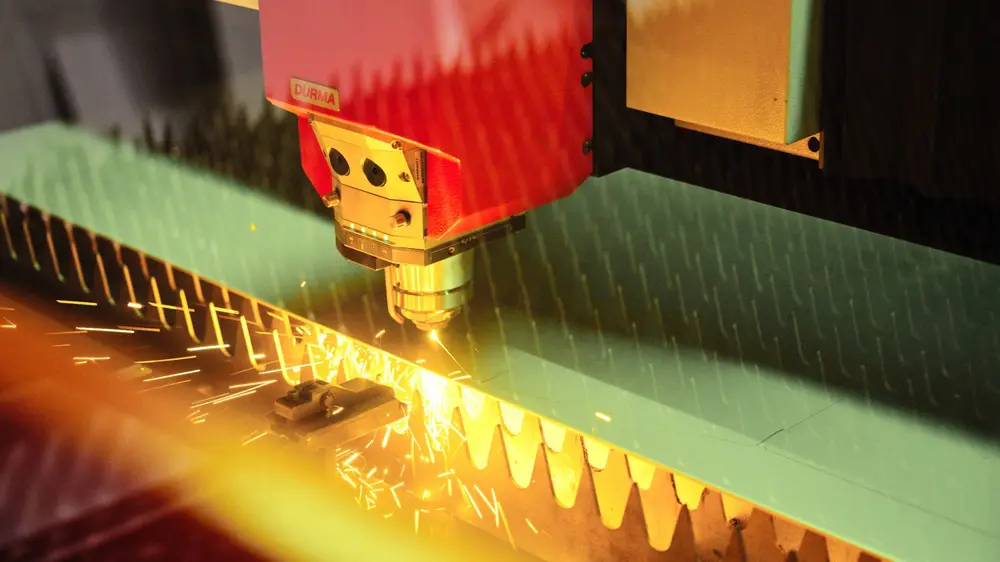
Wat is lasersnijden?
Lasersnijden is een thermische snijtechniek voor het snel en precies bewerken van metaal. De laserstraal wordt opgewekt in de laserbron − een CO₂-, een diode-, een disk- of een fiberlaser – en via spiegels of een vezelkabel naar de snijkop van de machine geleid. Daar aangekomen, wordt die sterk geconvergeerd met behulp van de focusoptiek. Het plaatmateriaal smelt lokaal waardoor het mogelijk wordt uiterst nauwkeurig te snijden met een op de laserkop bevestigd mondstuk. Een gasstraal zorgt voor de uitdrijving van het gesmolten materiaal en voor een beperkte oxidatie van de snedekanten. Afhankelijk van de materiaalsoort, de plaatdikte en nabewerkingen is dat snijgas stikstof, zuurstof, perslucht of een mengsel daarvan. De warmte-beïnvloede zone is bij lasersnijden gering, de snede zeer fijn en het materiaalverlies beperkt.
Hogere vermogens
De roep om hogere vermogens zal gezien de daaraan verbonden voordelen voorlopig nog wel blijven bestaan. Van Collie (LVD): “Een Chinese constructeur zit bij mijn weten al op 40 kW, diverse anderen op 30 kW en een groot aantal op 20 kW.” Deram (Haco) denkt dat als het gaat om plaatmateriaal van geringe(re) dikte de grens met 15 kW nog niet is bereikt, maar dat dat bij materialen boven de 25 mm toch wel anders ligt. Zij bieden reeds vermogens aan tot 20 kW. Leeman (Metanox), Creemers (Mazak) en Van Collie (LVD) verwachten dat de prijs steeds belangrijker wordt. Van Collie: “In mijn ogen is de factor cost/part doorslaggevend, en die daalt drastisch bij hogere vermogens: in dik roestvast staal snijdt de 20 kW twee tot tweeënhalf keer sneller dan een 10 kW laser, en dat met dezelfde hoeveelheid stikstof.”
Creemers (Mazak) plaatst daarbij wel een kanttekening: “Hogere vermogens zijn voornamelijk interessant bij massa-/seriewerk waarbij een gepaste automatisering en een grote opslagcapaciteit inherent zijn aan het behalen van het maximale rendement. De investering die dat vergt is voor lang niet elk metaalbedrijf op te brengen.” Ook Van de Meerakker (Bystronic) zit op die lijn: “Bij een hele dag dik rvs snijden is een hoger vermogen zinvol, bij een dikte van 1 mm totaal niet. Daarom moet steeds in overleg met de klant worden beslist over zaken als vermogen, belaadsystemen softwareoplossingen en automatisering.”
Vincke (V.A.C. Machines vraagt zich af of het niet beter is te focussen op de (automatisering van) processen rondom het snijproces in plaats van op vermogen. “Een machine met een lager vermogen kan door automatisering meerdere shifts manloos doorwerken en dus toch meer throughput hebben dan een machine met een groot vermogen.”
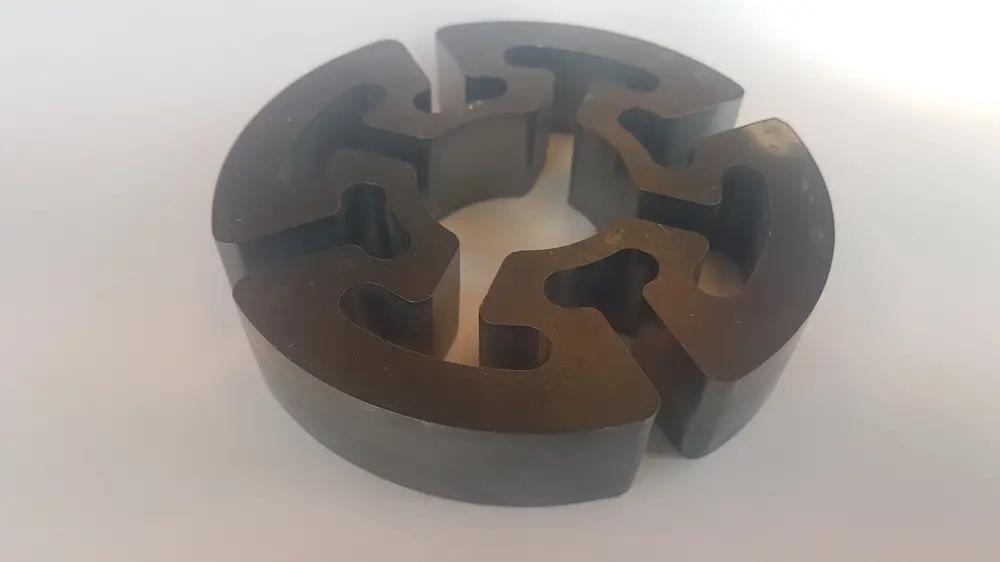
Verbeterpunten
Creemers (Mazak): “De snijkwaliteit in bepaalde materialen blijft een aandachtspunt − denk aan scherpe kanten en lichte braam- en korrelvorming − maar naarmate het vermogen stijgt en de snijsnelheid toeneemt, treden dergelijke verschijnselen minder op.” Deram (Haco): “Zeker het snijden van dikke platen met hoge vermogens kan beter: een van de weinige voordelen van de CO₂-technologie is nog de betere snijkwaliteit bij dik materiaal (20mm +).” Wat Van Collie (LVD) betreft zijn het vooral de hogere vermogens en betaalbare laserbronnen die de aandacht moeten krijgen. Vincke (V.A.C. Machines) noemt een tweetal voorbeelden van de reeds door Trumpf gerealiseerde verbeteringen: de BrightLine fiber die de straalkwaliteit van de machine kan aanpassen en de High Speed Eco waarbij het stikstofverbruik tot 70% lager ligt.
"Een van de weinige voordelen van de CO₂-technologie is nog de betere snijkwaliteit bij dik materiaal"
Van de Meerakker (Bystronic) geeft aan dat de snijtechnologie inmiddels wel op niveau is, en dat de inspanningen daar volledig zijn gericht op het autonoom kunnen draaien. Creemers meldt dat bij Mazak wordt gewerkt aan de double core technology, chiptechnologie waardoor taken in parallelle stromen kunnen worden uitgevoerd onder meer resulterend in kortere verwerkingstijd. Van Collie (LVD): “In het kader van de hogere vermogens houden wij ons bezig met de daarbij horende tendens om naast zuurstof en stikstof ook een mix van beide in te zetten, en dan vooral voor het snijden van dikke plaat.”
Vincke (V.A.C. Machines) houdt er de spanning nog even in: “Later dit jaar zullen we een nieuw snijproces introduceren waarover ik nog nu niets kan zeggen, behalve dat de mogelijkheid bestaat deze technologie te retrofitten. Deram sluit de rij met de mededeling dat er bij Haco wordt gewerkt aan ‘water guide laser cutting’, een techniek die kan worden toegepast daar waar hoge geometrische nauwkeurigheid gewenst is.
Handling laserparts
Gezien de ‘logistieke nachtmerrie’ die de handling van de laserparts vaak is, is er behoefte aan systemen die ervoor zorgen dat exact bekend is waar in de keten elk onderdeel zich op welk moment bevindt. Voor dit 'slim maken' van laserparts bestaan diverse mogelijkheden. Zo is men in een van de Japanse vestigingen van Mazak inmiddels zover dat elk onderdeel via een QR-code wordt getraceerd naar een volgend level, van snijden en kanten tot aan lassen en lakken. V.A.C. Machines helpt klanten met een audit stapsgewijs bij het smart maken van hun organisatie en Bystronic verkoopt al sorteerinrichtingen die 24 uur per dag doordraaien, en heeft daarmee volgens Van de Meerakker een voorsprong op de concurrentie.
Ten aanzien van de vraag welke van de beide coderingsmethoden de toekomst heeft, lopen de meningen enigszins uiteen. Vincke (V.A.C. Machines) en Creemers (Mazak) vinden dat beide voordelen hebben: een stuknummer is direct zichtbaar terwijl voor een 2D-code een scanner nodig is, maar het oproepen van het juiste vervolgprogramma is weer alleen met een scanner mogelijk.
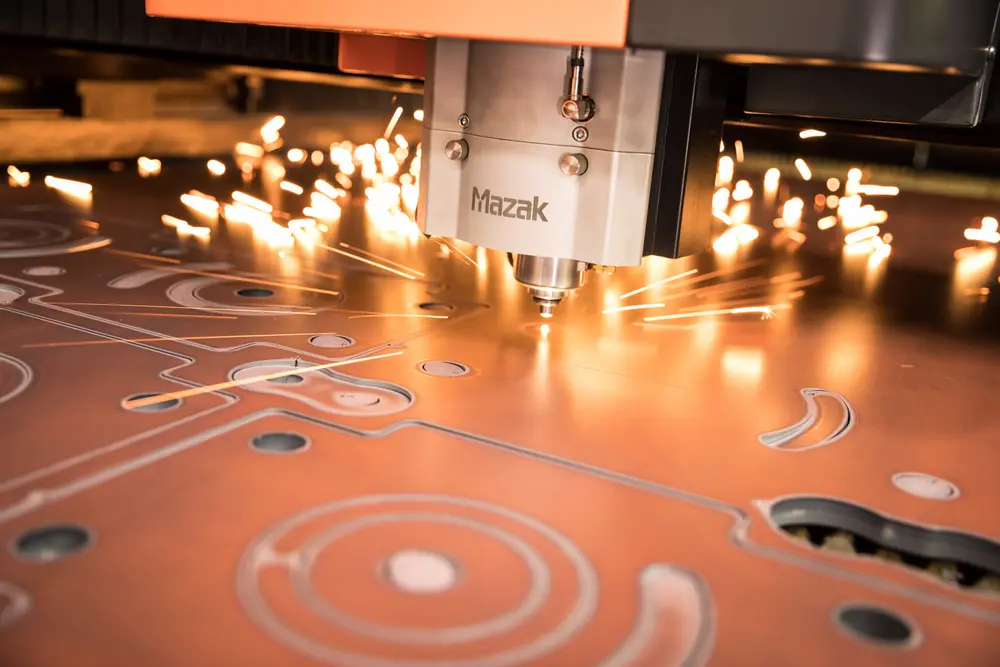
Deram (Haco) geeft aan dat de meeste klanten vooralsnog kiezen voor stukmarkering, maar denkt wel dat de codering in de toekomst aan populariteit zal winnen. Leeman (Metanox) deelt die mening: “Het voordeel van coderen is dat een QR-code zeer veel informatie kan bevatten.” Van de Meerakker (Bystronic) beaamt dat maar voegt daaraan toe dat er weliswaar veel coderingsmethoden zijn, maar dat een universele oplossing nog ontbreekt. “Het gebruik wordt bepaald door wat de klant ermee wil en wat het eindproduct is.”
Volgens Van Collie (LVD) is een QR-code qua uitlezing het meest betrouwbaar, maar niet bepaald snel. “Dat kan worden ondervangen door te graveren met een veel snellere, aparte laagvermogen laserkop waarbij de spiegel beweegt en de machineassen blijven staan.”
Procesbeheersing
Procesbeheersing is het plannen en regelen van een proces; procesondersteuning en procesintegratie zijn daarvan een onderdeel.
Procesondersteuning
De komende jaren zal de belangstelling voor procesondersteunende systemen groeien; ze helpen het proces efficiënter, veiliger en rendabeler te maken. Deram (Haco) daarover: “Intelligente bewaking van het proces helpt zicht te krijgen op de kwaliteit. Door automatisch monitoren kan bijvoorbeeld ook slijtage al in een vroeg stadium worden onderkend. Dat voorkomt machinestilstand en bevordert de algehele snijkwaliteit.”
Gevraagd naar concrete voorbeelden noemt Creemers (Mazak) dat controle van het snijbeeld bij hen momenteel plaatsvindt op basis van reflectiemeeting via sensoren in de snijkop. “Bij veranderende waarden wordt de snelheid aangepast tot deze terug zijn op hun normale niveau; lukt dat niet dan stopt de machine automatisch.” Metanox maakt volgens Leeman gebruik van een camerasysteem voor optimalisatie van de nesting, de positionering van de plaat en die van de stukken op de snijtafel.
"Intelligente bewaking van het proces helpt zicht te krijgen op de kwaliteit"
Van de Meerakker (Bystronic) noemt in dat verband de functie TiltPrevention: “Die maakt het mogelijk snijsequenties te creëren die het risico van uitstekende delen minimaliseert. Dat vermindert de verstoring van snijprocessen en de uitvaltijd veroorzaakt door botsingen met de snijkop.” Wat Vincke (V.A.C. Machines) betreft zijn dat Active Speed Control en Coolline. Eerstgenoemde zorgt er door monitoring via de koperen nozzle voor dat het snijproces van bovenaf realtime wordt gecontroleerd. Coolline is een procesondersteunend systeem dat met name bij dikke platen de warmte afvoert door middel van waterkoeling,
Van Collie (LVD) vindt het lovenswaardig dat er gewerkt wordt aan de proceszekerheid, maar ziet ook de ‘onmogelijkheden’: “Zoiets als smeltstroombewaking is natuurlijk mooi, maar met een sensor/camera zie je enkel en alleen de bovenkant van het smeltbad, en heb je verder geen zicht op wat daaronder gebeurt.”
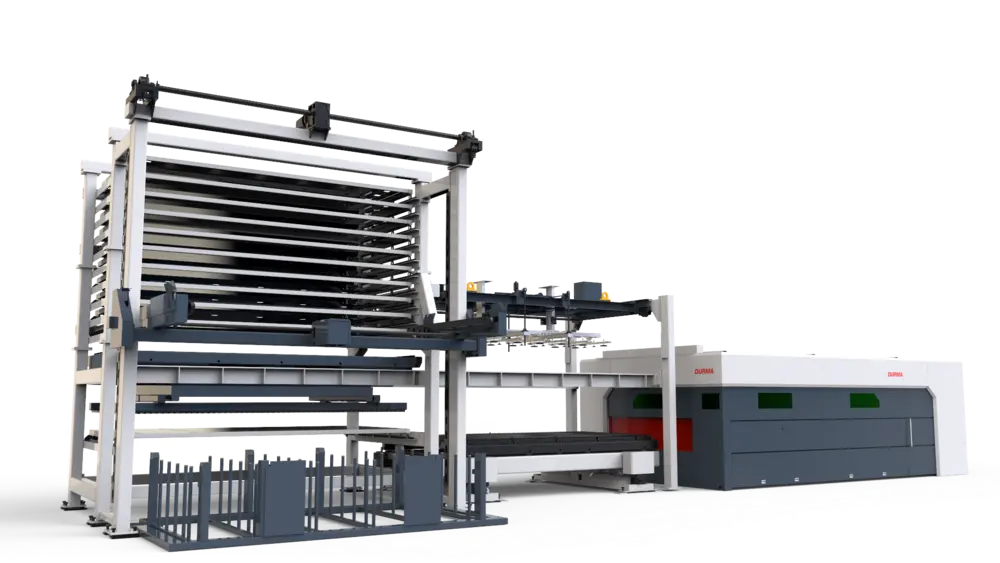
Procesintegratie
Naar verwachting zal het accent bij de metaalbewerking meer en meer komen te liggen op de integratie van de technologie. Dat vraagt behalve om verregaande automatisering ook om de integratie van bijvoorbeeld voorraadbeheer en procesondersteunende systemen. De deelnemers aan het gesprek zijn zich hiervan terdege bewust en bereiden zich daarop voor, waarbij samenwerking de rode draad vormt.
Van de Meerakker (Bystronic): “Wij creëren een ecosysteem waarbinnen we heel eenvoudig met externe partijen kunnen samenwerken, zowel hardware- als softwarematig. Ook bij LVD gaan ze niet over een nacht ijs. Van Collie: “Integratie is bij ons al meer dan 10 jaar een speerpunt. Koppeling met externe partijen is noodzakelijk en softwarematig zijn we al goed voorbereid om met andere machines/processen samen te werken.
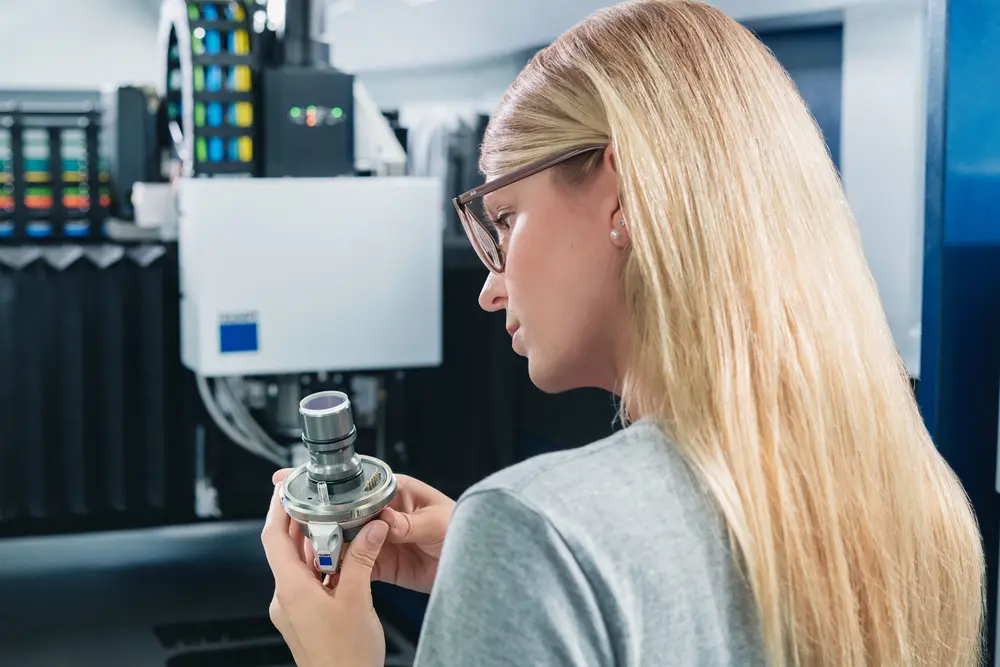
Dat geldt volgens Creemers ook voor Mazak: “Communicatie met diverse soorten machines en automatiseringssystemen en integratie van administratieve processen en stockbeheer zijn een must. Onze machines zullen worden uitgerust met de nodige interfaces om als integrator te kunnen opereren binnen een totaalconcept.” Haco werkt op het gebied van R&D en softwareoplossingen nauw samen met partners die absolute experts zijn op dit gebied. Al onze machines kunnen eenvoudig worden gekoppeld aan automatische aan- en afvoer systemen, wat resulteert in een optimaler plaat- en machinegebruik. Hierdoor worden het rendement en de concurrentiekracht van de plaatafdeling beter.”
Ook Metanox is er aldus Leeman klaar voor: “Wat ons betreft kan er bij wijze van spreken morgen al worden geleverd. Onze leveranciers Salvagnini en Durma beschikken over de daarvoor benodigde expertise en zijn volledig in staat hun bijdrage te leveren aan de integratie van de technologie.”
De factor mens
De techniek van het lasersnijden wordt weliswaar steeds geavanceerder, maar nog (te) vaak gaan er zaken fout door verkeerd menselijk handelen:
- fouten tijdens de werkvoorbereiding en/of het programmeren;
- het onjuist gebruiken, positioneren of vervangen van onderdelen;
- het gebruik van onvoldoende zuivere snijgassen;
- snelheid verkiezen boven proceszekerheid.
In veel gevallen is dat terug te voeren op gebrek aan kennis en/of het niet opvolgen van richtlijnen en/of instructies. Dit is alleen te voorkomen door een goede opleiding en training, een gedeelde verantwoordelijkheid van leverancier en gebruiker. De techniek staat voor niets, maar alleen als die goed wordt ingezet.
De autonome plaatwerkfabriek
Het uiteindelijk doel van de procesintegratie is volgens velen de autonome plaatwerkfabriek, maar niet voor iedereen is het bereiken van dat doel even vanzelfsprekend. Wat Creemers (Mazak) betreft bestaat dat concept feitelijk al als het gaat om repetitief en seriematig werk, en is veralgemenisering de volgende stap. “Ik vraag me echter af hoe snel dat zal kunnen gaan, aangezien er nu nog te veel variabelen zijn die een stabiel en autonoom proces ondermijnen.”
"Ik denk dat het nog wel een tijdje zal duren voordat er autonoom kan worden gewerkt zonder de tussenkomst van de mens"
Ook Deram (Haco) is gematigd optimistisch: “Het moet op zich mogelijk zijn in de komende 5 tot 10 jaar te komen tot een hooggespecialiseerde en min of meer volledig geautomatiseerd werkende fabriek. Veel van onze klanten geven er echter vooralsnog de voorkeur aan te investeren in bekwame, loyale medewerkers en willen of kunnen (nog) niet investeren in verregaande en kapitaalsintensieve vormen van ‘autonome’ automatisering.” Leeman, (Metanox) sluit zich daarbij aan: “Ik denk ook dat het nog wel een tijdje zal duren voordat er autonoom kan worden gewerkt zonder de tussenkomst van de mens.”
Van Collie (LVD): “In mijn ogen is ‘autonoom’ voor de meeste plaatwerkbedrijven een utopie. In onze visie is het een stap te ver; wij spreken liever van ‘operator-arm’. Voor repetitief en seriewerk is het in grote mate haalbaar, maar ook hier is de hamvraag: hoe zwaar weegt de extra investering door op de cost/part? Van een stap te ver wil Van de Meerakker (Bystronic) niet horen: “Wij investeren heel veel in de smart factory en werkt daarbij met en aan modulaire, schaalbare systemen. Er zijn echter nog veel praktische problemen om op te lossen, en degene die daartoe het best in staat is, gaat uiteindelijk die smart factory neerzetten.”
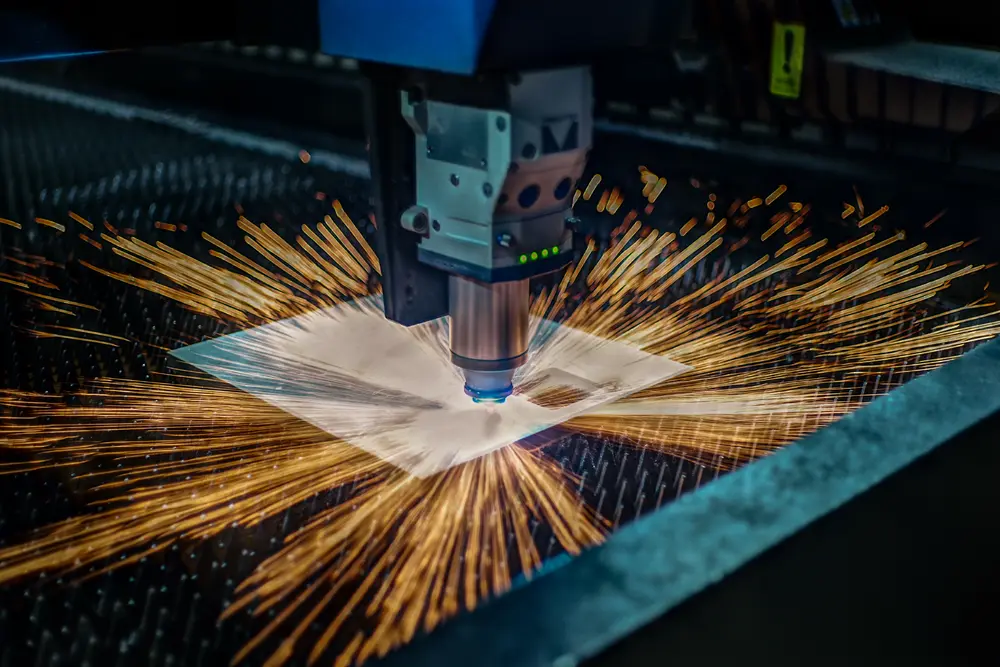