"Nous sommes relativement peu connus, mais omniprésents"
ZiggZagg a lui-même imprimé son prix Factory of the Future
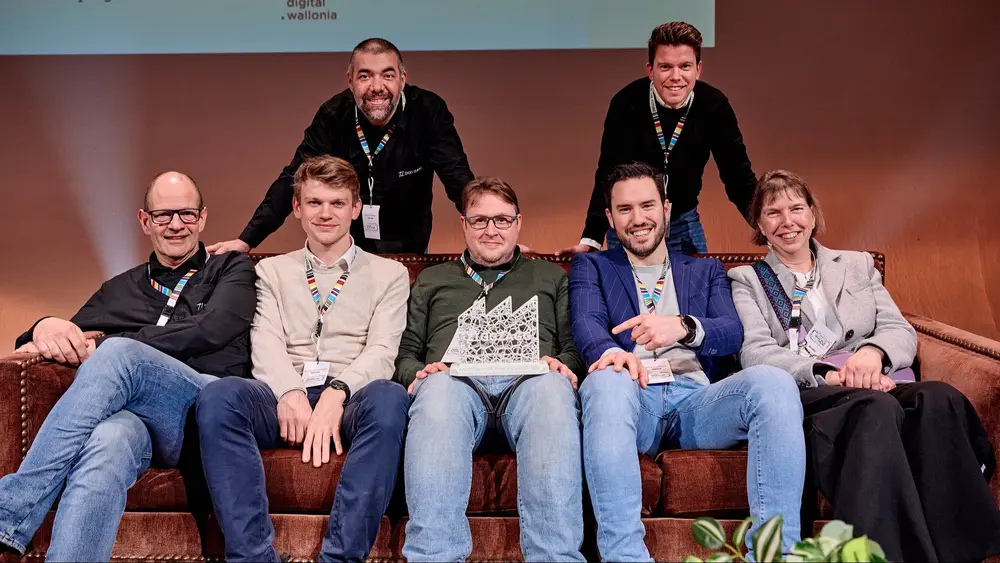
Ce printemps, les prix Factory of the Future ont été décernés pour la dixième fois déjà. Parmi les nouveaux lauréats figure l'entreprise ZiggZagg, basée à Aalter, qui utilise l'impression 3D pour fabriquer des pièces destinées à l'industrie, à la santé et à la défense. Avec seulement 15 collaborateurs, elle fait figure d'exception parmi les lauréats précédents, tels que Daikin, Alpro ou DAF Trucks. "Nous servons ainsi d'exemple à d'autres PME", déclare Stijn Paridaens, PDG de l'entreprise. Il voit dans ce prix une occasion de sensibiliser le grand public.
Production industrielle de pièces
ZiggZagg a été fondé en 2010 en tant que centre de R&D d'un fabricant de luminaires. Cinq ans plus tard, l'entreprise a été reprise par la famille Seynaeve, et en 2016, Stijn Paridaens a été recruté comme PDG par les nouveaux propriétaires. Aujourd'hui, l'entreprise compte parmi les plus grandes usines européennes d'impression 3D, avec des clients dans 23 pays différents.
Auparavant, nous nous occupions principalement de modélisme, mais après ma nomination, nous nous sommes détournés de ces joujoux coûteux et 'artisanaux' pour nous concentrer sur la production à grande échelle. Dans de nombreux cas, il s'agit encore de petites séries ou de pièces uniques, mais nous les fabriquons désormais sur des machines très rapides et à partir de poudre plutôt que de fil. Nous imprimons aussi bien du plastique que du métal, sur onze machines hautement automatisées et connectées", nous explique Paridaens lors de la visite.
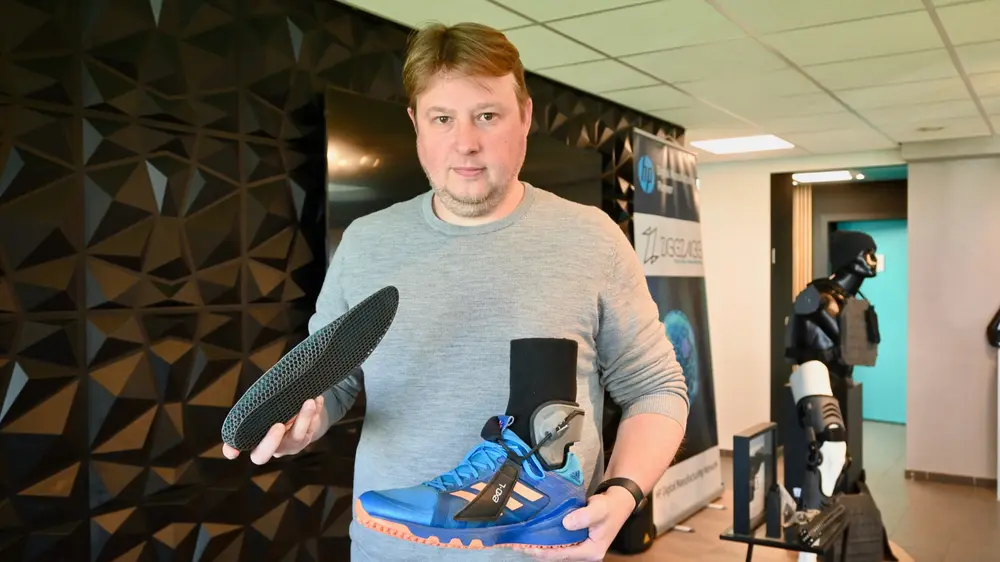
"Ainsi, nous fabriquons aujourd'hui des dizaines, voire des milliers de pièces par jour, en fonction de leur taille et de leur complexité. Soit nous recevons les fichiers de conception, soit nous développons les pièces nous-mêmes. Dans de nombreux cas, il s'agit de prototypes pour l'industrie automobile ou de pièces sur mesure pour les constructeurs de machines, et nous fabriquons également des pièces de rechange qui ne sont plus disponibles auprès du fabricant d'origine. Pour les applications médicales, il s'agit de toutes sortes d'appareils orthopédiques ou d'accessoires, et pour la défense, il faut penser aux composants des lunettes de vision nocturne ou aux cadres des gilets pare-balles."
Optimisation de la chaîne d'approvisionnement
À cet égard, la fabrication additive présente un certain nombre d'avantages par rapport à la fabrication soustractive classique, ou au moulage par injection.
"Tout d'abord, c'est un procédé qui permet non seulement la production, mais aussi la personnalisation sur mesure, grâce à un délai d'exécution très court. C'est un atout important, car de plus en plus d'entreprises font attention à leur stock dormant et ne se réapprovisionnent donc qu'en cas de réelle nécessité. En termes de coûts, cette méthode de production est particulièrement intéressante pour les petites séries ou les pièces uniques, car elle permet d'éviter la fabrication de moules coûteux. De plus, elle permet de réaliser les designs les plus complexes", explique le PDG.
"De nombreuses entreprises européennes souhaitent être moins dépendantes des importations non européennes"
Autre avantage: l'impression 3D est dans ce cas un processus de production très écologique, qui gagne également en importance. "Nous partons d'un bac rempli de poudre, extraite de graines de ricin naturelles, qu'un faisceau laser fusionne là où c'est nécessaire. L'excédent de poudre sert à soutenir la structure formée et peut être réutilisé à 100% pour une opération ultérieure. Chez nous, il n'y a donc pas de gaspillage de matériaux ni de lubrifiants réfrigérants polluants, comme c'est le cas avec l'impression 3D FDM ou l'usinage."
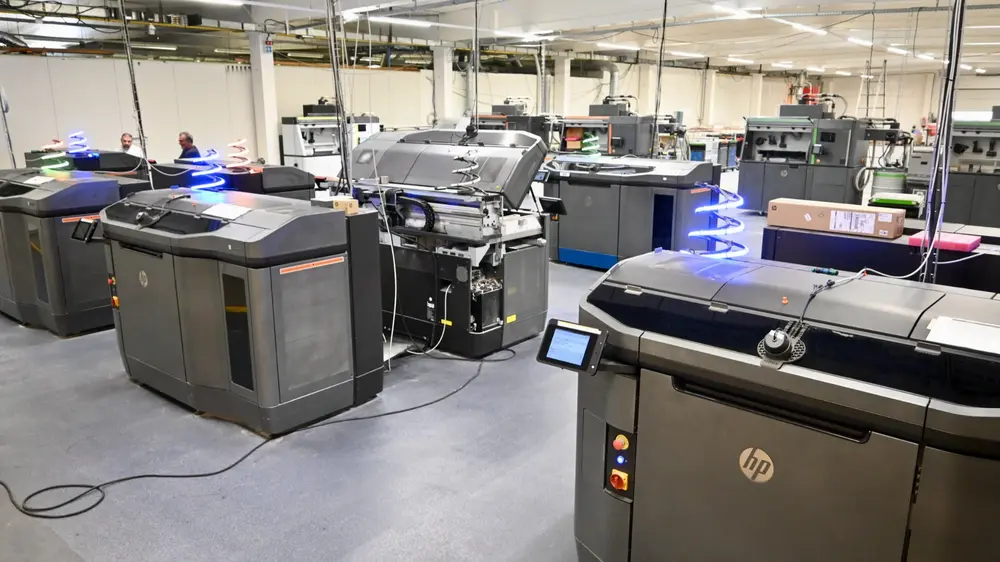
À cet égard, la PME flamande est souvent privilégiée par rapport aux fabricants d'outre-mer. "Tout d'abord, notre région située entre le nord de la France et le sud des Pays-Bas renferme beaucoup de connaissances en matière d'impression 3D. Ces dernières années, il y a eu beaucoup de problèmes dus au covid, à l'Ever Given, à la guerre... C'est pourquoi de nombreuses entreprises européennes souhaitent aujourd'hui être moins dépendantes des importations non européennes. Ce faisant, elles apprécient plus qu'avant notre communication fluide, nos délais de livraison courts, notre service après-vente, notre protection IP... Le 'Produced in Europe' est donc un label de qualité important, qui offre les garanties nécessaires."
Des postes vacants en permanence
Mais il y a aussi des inconvénients, en partie dus à la situation géographique. "Le personnel est sans aucun doute notre principale pierre d'achoppement, qui ralentit notre croissance. Il y a bien sûr les coûts élevés de la main-d'œuvre dans notre pays, qui pèsent sur notre compétitivité internationale. De plus, nous avons du mal à trouver des collaborateurs adéquats, en raison de nos activités spécifiques. Nous travaillons dans un secteur en vogue avec des clients de premier plan, mais en raison des nombreux accords de confidentialité, nous ne sommes pas toujours autorisés à communiquer à ce sujet. En outre, il n'est pas possible d'étudier pour les emplois que nous offrons", explique Paridaens.
"Chaque entreprise est un client potentiel pour nous"
"Nous sommes un employeur exigeant, car nous avons besoin d'opérateurs de machines ou de développeurs de produits intelligents, qui ont également le bon état d'esprit. J'entends par là une attitude flexible et la capacité de sortir des sentiers battus pour faire face à la grande diversité des clients et à l'évolution rapide des marchés sur lesquels ils opèrent. Chaque entreprise est un client potentiel pour nous. Nous ne leur vendons pas des produits off the shelf, mais le service nécessaire pour optimiser leurs processus par le biais de nouvelles pièces, de re-conceptions ou de la gestion des pièces de rechange. Cela leur permet d'économiser des coûts considérables."
Un exemple pour d'autres PME
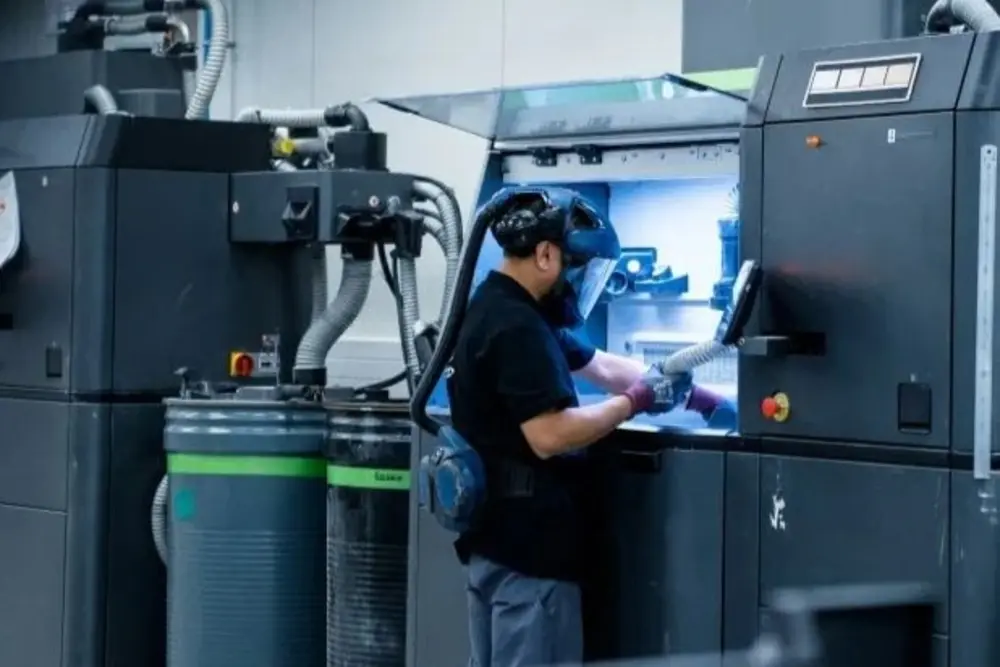
Les nombreux trophées imprimés par cette entreprise de Flandre orientale sont également soumis au secret. "Presque tous les trophées brandis par les e-sportifs du monde entier viennent de chez nous. Nous fabriquons également les prix Factory of the Future depuis des années, et nous savons donc toujours à l'avance qui sont les gagnants", explique Paridaens.
Cette année, ZiggZagg a donc imprimé son propre prix. "Sur les conseils de Sirris et d'Agoria, qui connaissent bien notre entreprise grâce aux projets de recherche auxquels nous participons, nous avons procédé à notre première évaluation en 2022. À l'époque, nous avions encore quelques lacunes concernant l'organisation centrée sur l'humain, mais lors de la deuxième tentative, l'année dernière, nous avons obtenu des résultats satisfaisants pour toutes les transformations clés prédéfinies concernant la technologie, la durabilité et les employés", déclare le PDG.
L'entreprise a ainsi rempli toutes les conditions pour recevoir le prix. "Nous sommes la plus petite entreprise dans l'histoire des prix Factory of the Future et nous sommes un exemple pour les autres PME. Nous profitons donc particulièrement de l'attention de la presse, afin de gagner encore un peu plus de visibilité auprès du grand public et des nouveaux employés potentiels."
Poursuite de la croissance
Que réserve l'avenir, après cette étape importante? "Par gratitude pour le soutien obtenu de VLAIO et de nos actionnaires flamands, nous voulons à tout prix conserver nos connaissances et notre production ici. Nous avons l'ambition de multiplier notre entreprise par trois ou cinq, juste en doublant le nombre de nos employés. Par conséquent, dans les années à venir, nous devrons continuer à travailler sur l'automatisation et l'efficacité afin d'évoluer vers une factory lights-out", ajoute le PDG.