3D-PRINTEN WORDT AL MET LASROBOTS GECOMBINEERD
Wire+arc additive manufacturing
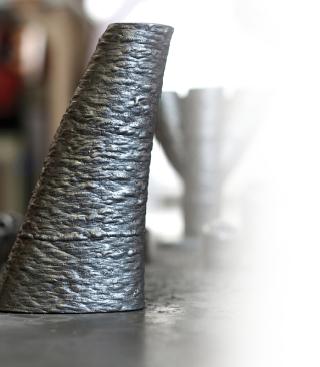
ADDITIVE MANUFACTURING (AM)
De volgende industriële revolutie
De 3D-printtechnologie voor metalen en non-ferro's staat niet meer in haar kinderschoenen en wordt wel eens de volgende industriële revolutie genoemd. In vele sectoren wint AM aan populariteit dankzij de mogelijkheid om complexe onderdelen te fabriceren met een redelijke precisie en een hoge vrijheidsgraad. Bovendien is er aanzienlijk minder materiaalverlies tijdens de verschillende fabricagestappen. Zo draagt AM bij tot enorme kostenbesparingen en verhoging van de productie-efficiëntie. Na de vliegtuigindustrie en de medische sector vindt AM nu ook haar weg naar andere sectoren zoals energie, maritieme toepassingen en zelfs burgerlijke bouwkunde.
Van rapid prototyping tot rapid manufacturing
AM omvat een veelheid van technieken die allemaal eenzelfde basis hebben: een bewegingssysteem, een warmtebron en een (toevoeg)materiaal. Het werkstuk wordt vervolgens opgebouwd door het op elkaar stapelen van dunne laagjes, aangestuurd vanuit een CAD-model. Zo kennen we vandaag technieken waarbij vooral metaalpoeders omgesmolten worden via laser (Selective Laser Melting) of een elektronenstraal (Electron Beam Melting). Hoewel AM allemaal heel nieuw en revolutionair in de oren klinkt, werd er al een eerste patent opgemaakt in 1920. AM maakt vandaag de evolutie door van de Rapid Prototyping-techniek naar volwaardig Rapid Manufacturing.
WAAM
Voordelen van alternatieve productievorm

Technologie
Wire+Arc Additive Manufacturing kan verdeeld worden in drie groepen, afhankelijk van welke energiebron gebruikt wordt. Deze energiebronnen kunnen zijn:
- een lasbron voor booglassen met een toevoegdraad. Denk dan aan MIG/MAG- of TIGlassen;
- een laserbron voor het oplassen met een extern aangevoerde draad of een aangevoerd poeder;
- elektronenbundel (EB)-lassen met een toevoegdraad.
Elk type energiebron heeft zijn voor- en nadelen qua efficiëntie, energieverbruik, oppervlakteruwheid, gebruik van materiaalsoort en de uiteindelijke mechanische eigenschappen van het product. Het WAAM-proces wordt uitgevoerd met een industriële robot. Dergelijke robots hebben een groot bereik en een hoge repeteernauwkeurigheid met steeds dezelfde toleranties. De productietijd is aanzienlijk korter.
TITAAN EN ALUMINIUM
Als alternatief voor aluminium

Nood aan nieuwe fabricagetechnologieën
Gezien de hoge kostprijs van titaan en het feit dat het materiaal ook zo moeilijk mechanisch te bewerken valt, is er nood aan alternatieve fabricagetechnologieën zoals WAAM om grote onderdelen zoals verstijvers en vleugelribben te vervaardigen, die tot vandaag worden gemaakt op basis van giet- en smeedstukken. Omdat het MIG-lassen van titaan een onstabiele vlamboog oplevert, kan dit vandaag enkel via TIG- en plasmalassen. Er mag ook niet worden vergeten dat zuurstof nogal heftig reageert met titaan, waardoor er oxidatie optreedt en mechanische eigenschappen worden aangetast. Voorzichtigheid is dus geboden en het lassen in een inerte atmosfeer is daarvan het gevolg. De volledige lasinstallatie moet afgeschermd worden van de omgevingslucht door middel van omkappingen. Ook aluminium is een zeer dankbaar materiaal voor de WAAM-technologie. MIG-lassen is hier uitermate geschikt. Omdat de draad coaxiaal met de lastoorts loopt, resulteert dit in een eenvoudig te programmeren traject waarbij er minder vrijheidsgraden nodig zijn op de robotinstallatie in vergelijking met het TIG-lassen, waar de draad haaks op de lastoorts wordt toegevoerd en dus voor een hindernis zorgt. Onderzoekers van de universiteit van Cranfield claimden in oktober 2016 het grootste 3D-geprinte stuk ooit te hebben gerealiseerd via WAAM: een 6 m lange en 300 kg zware balkvormige structuur uit aluminium.
UITDAGINGEN
Succes ligt in combinatie van parameters
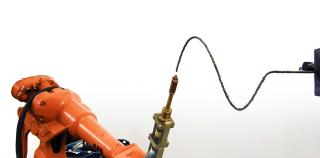
CONCLUSIE
Het succes van WAAM is enerzijds te danken aan de eenvoud en toegankelijkheid van de technologie en anderzijds aan de enorme en quasi ongelimiteerde mogelijkheden. Verdere ontwikkelingen lopen niet uitsluitend in onderzoekslaboratoria van universiteiten, maar ook de industrie en haar vele start-ups zijn intensief bezig met WAAM. Een volgende stap wordt ongetwijfeld het integreren van de WAAM-technologie in CNC-bewerkingscenters.