Hoe je sneller kan snijden met een buislasersnijmachine
Zijn er nog andere factoren om mee rekening te houden?
Een machine zo complex als een buizenlaser kan je vanuit verschillende perspectieven bekijken. In dit artikel kiezen we ‘snelheid’ als voornaamste insteek. Met andere woorden, welke factoren dragen ertoe bij dat je je buizen, kokers en profielen sneller kan snijden? Een combinatie van speciale cycli en andere opties zou immers tot een winst van wel 50% kunnen leiden. En daar willen we natuurlijk het fijne van weten. Behalve de factor snelheid raken we ook nog een paar andere aspecten aan die interessant kunnen zijn bij de keuze van een machine, zij het minder uitgebreid.
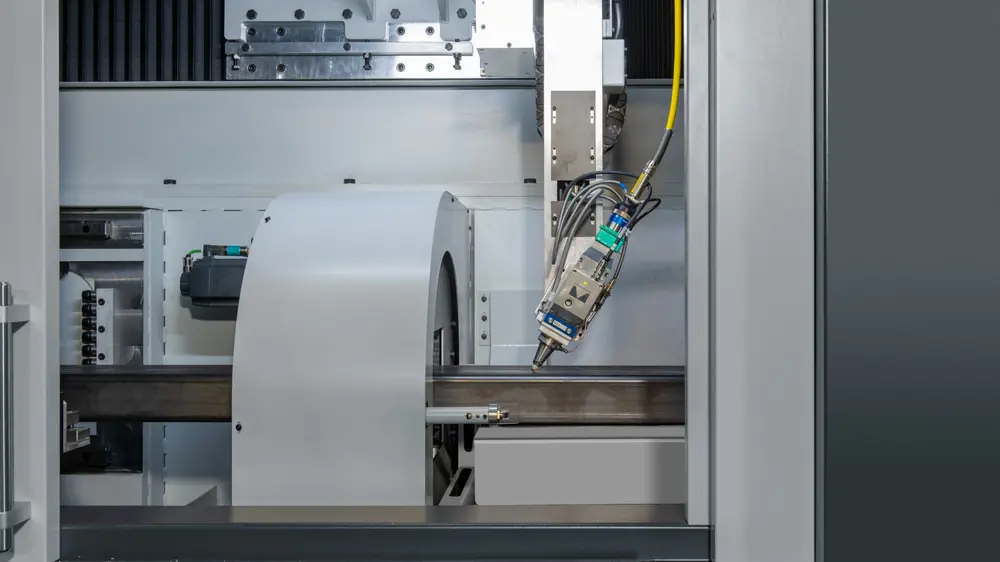
Waarom zijn buizenlasers interessant?
Vooraleer we de technische details met betrekking tot de bewerkingstijden aansnijden, toch nog even opfrissen wat dit type van machine zo aantrekkelijk maakt, met name voor sectoren als de meubelindustrie, de automotive en de machinebouw.
In de eerste plaats spaart een buizenlaser tal van extra handling en logistieke stappen uit. Daarmee verkleint de kans op fouten aanzienlijk. Een buizenlaser dient namelijk als vervanging van een zaag- en boorstraat. Bij die klassieke manier van bewerken, kwam typisch heel wat manipulatie van de buizen kijken.
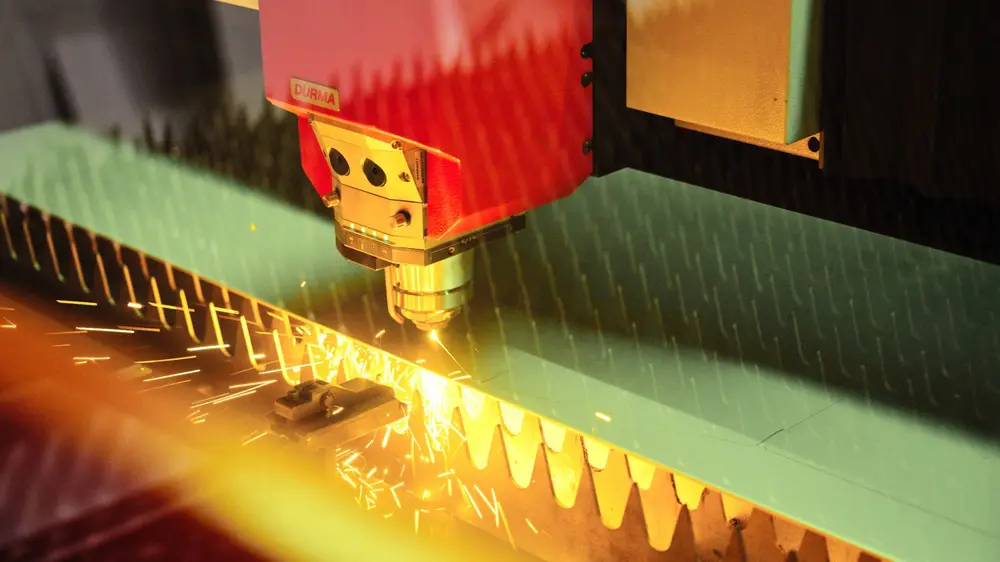
Een tweede troef is dat je sommige innovatieve buisverbindingen op geen enkele andere manier kan maken. En dergelijke slimme ontwerpen komen steeds vaker voor. Stukken die vroeger uit meerdere elementen bestonden, worden nu in één geheel vervaardigd of de afzonderlijke buizen klikken gewoon in elkaar. Dat biedt serieuze voordelen voor alle processen die erna komen: minder assemblage en laswerk, wat op zijn beurt resulteert in een reductie van de nabewerking.
Kijk naar de totale bewerkingstijd
Is het je opgevallen dat de inleiding het heeft over de factor snelheid maar nergens melding maakt van ‘snijsnelheid’? Een heel bewuste woordkeuze. Bij het buislasersnijden weegt de snijsnelheid namelijk veel minder door in de totale bewerkingstijd dan bij het vlakbedsnijden. Met bewerkingstijd bedoelen we het geheel van programmeren, beladen, meten, snijden en uitladen.
Bij het buislasersnijden weegt de snijsnelheid veel minder door in de totale bewerkingstijd dan bij het vlakbedsnijden
Snijsnelheid heeft kleiner aandeel
Om te beginnen neemt het eigenlijke snijden een kleiner aandeel in. Niet alleen zijn de snedes minder groot, aan het snijden gaan ook meer tijdrovende tussenstappen vooraf. De aanvoer van de buizen natuurlijk, via ofwel de kettinglader ofwel een bundellader (ook een combinatie van beide is mogelijk). Daarbij transporteert het automatisch klemsysteem de buizen naar het snijgebied, waar de klauwplaat tot tegen de buis of koker wordt geklemd. De klauwplaat zal de buis vervolgens centreren en gelijk ook de ingestelde afmetingen controleren, zodat de sturing eventuele afwijkingen kan compenseren, zolang ze niet te groot zijn. Gezien de vrij ruime toleranties bij kokermateriaal is centreren bij buislasersnijden een belangrijk aandachtspunt. In vergelijking met het vlakbedsnijden kruipt er daarom relatief veel tijd in het meten, of dat nu optisch gebeurt, capacitief via de snijkop of via meetsensoren in de klauwplaten. Voor speciale profielen zoals HOP, Foster of geëxtrudeerd aluminium bestaan er nog aparte meetopties. We moeten ook nog aanstippen dat afhankelijk van de klemmen die worden gebruikt en de eventuele aanwezigheid van ondersteuningen, de omsteltijden nogal variëren en zelfs helemaal kunnen worden geëlimineerd.
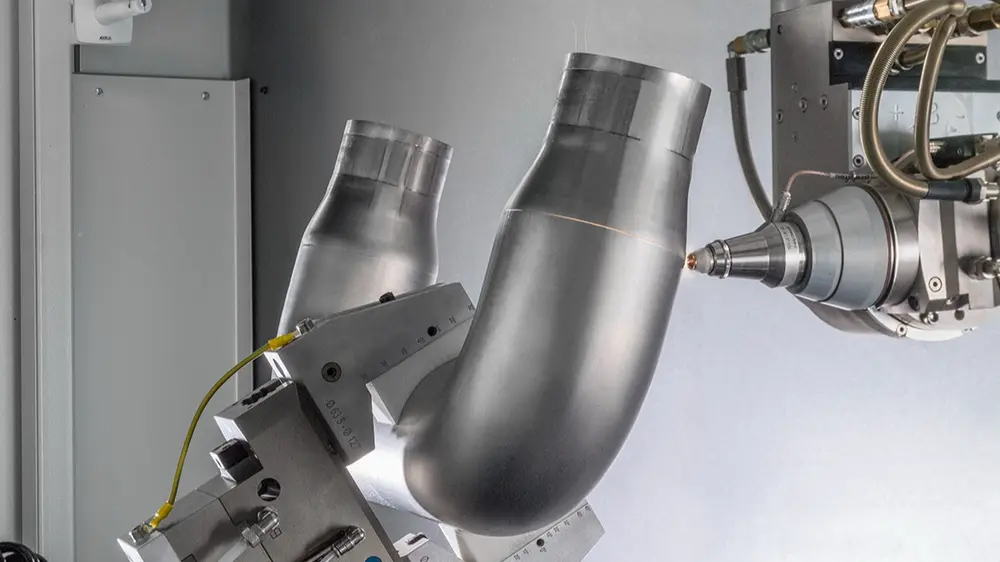
Hierbij een voorbeeld van een multi-assig laserssnijsysteem voor speciale profielen (foto: BLM Group)
De buizen bewegen evenzeer
Bij een buizenlaser beweegt niet alleen de snijkop, ook de buis of koker (die in extreme gevallen tot 300 kg/m kan wegen!) wordt voortdurend gemanipuleerd. Dat is een belangrijk verschil met het vlakbedsnijden. Tijdens het snijproces zorgen de kleminrichting en de ondersteuning samen voor het roteren en heen-en-weer bewegen van de buis over de x-as, terwijl de snijkop zelf in de y- en z-as kan bewegen en eventueel 45° kan inclineren, in het geval van 2,5 D snijden. Vandaar het belang van de algemene dynamiek van de machine. Om je een idee te geven van de verschillen op de markt: de basismodellen starten vanaf 0,3 G, terwijl andere machines vlot 1 G en meer aankunnen. Dat heeft onder meer te maken met de uitvoering van de motoren en de constructie van het machineframe, dat die zware belasting moet kunnen opvangen. Bovendien heb je twee soorten klauwplaten: elektrische en pneumatische. En ook dat maakt een verschil. Sommige bronnen spreken van een factor 3 sneller, in het voordeel van die laatste.
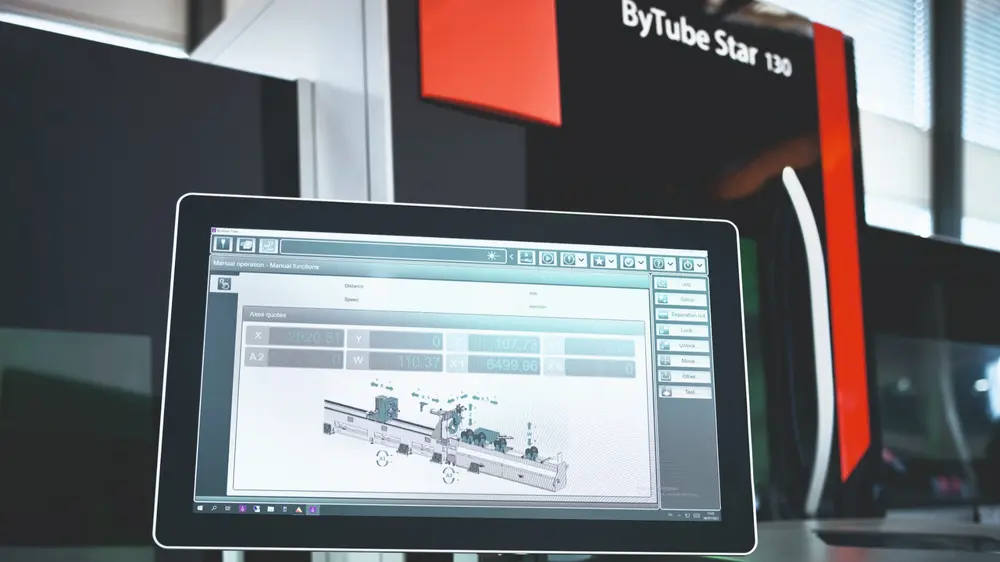
Aspecten die de snijsnelheid beïnvloeden
Hoewel dus minder doorslaggevend dan bij het vlakbedsnijden, kunnen we toch niet helemaal om de snijsnelheid heen. Verschillende aspecten hebben daar een impact op.
Verschillende aspecten hebben een impact op de snijsnelheid
Procesfactoren
Laat ons starten met een paar factoren die eigen zijn aan het proces zelf en die dus min of meer losstaan van de technische keuzes van de fabrikant. Zo spreekt het voor zich dat een grotere wanddikte een lagere snijsnelheid tot gevolg heeft. Wat evenmin zal verrassen, is dat de materiaalkeuze een rol speelt. Maar wist je dat je ook rekening moet houden met de locatie van de te snijden contour? In de hoek (radius) van een profiel zal de wanddikte meestal wat dikker zijn. Dat beïnvloedt overigens niet alleen de snijsnelheid, als je braamloos wilt snijden, zullen tevens de parameters licht moeten worden aangepast. Toegegeven, de invloed van deze en nog enkele andere procesfactoren is eerder gering.
Alternatieve snijmethodes
In tegenstelling tot de procesfactoren van daarnet, kunnen speciale snijcycli wel een serieuze hap van de snijtijd knabbelen. Tot zelfs 50% ten opzichte van de traditionele snijmethodes, als we de fabrikanten mogen geloven. Wat houden die dan in? Twee voorbeelden. Na het snijden van een snijvlak trekt de snijkop normaliter weer op naar zijn beginpositie, waarna de buis zich ofwel zal verplaatsen ofwel zal roteren zodat er opnieuw gesneden kan worden. In het bijzonder bij vierkante buizen resulteert dat in het herhaaldelijk op-en-neer bewegen van de snijkop. Als alternatief kan je ervoor opteren om die in een boog te laten bewegen. Op die manier minimaliseer je zijn pad tussen het snijden van twee patronen in. Een tweede voorbeeld is wat men ‘fly-cutting’ noemt. Ook dat is een methode om de efficiëntie van het snijproces te verhogen. Dit keer door het detecteren van rechte en circulaire lijnen binnen een patroon. We vertrekken opnieuw van opeenvolgende vierkantjes. In plaats van telkens in te steken of te piercen en daarna de volledige omtrek van een vierkantje te snijden – de klassiek manier – steekt men in de vlucht in, om vervolgens eerst alle horizontale lijnstukjes en daarna alle verticale te snijden.
Gaskeuze
Als derde element willen toch nog eens het snijgas onder de aandacht brengen. Kies je voor zuurstof, stikstof of perslucht? Niet onbelangrijk, want stikstof snijdt tot 3,5 keer sneller. Tevens zorgt het voor minder warmte-inbreng, waardoor fijne details makkelijker met stikstof dan met zuurstof te realiseren vallen. Daar staat wel tegenover dat je stikstof onder hoge druk moet gebruiken, wat een groter verbruik tot gevolg heeft. Ondanks de voordelen van stikstof zal je staal toch eerder met zuurstof associëren. Dat komt omdat stikstof in vergelijking met zuurstof veel beperkter is qua dikte. Maar een hoger vermogen van de laserbron kan dat deels compenseren. Vergeet dit aspect niet mee te nemen in je beslissing als je twijfelt tussen een 3 of 4 kW bron. In dit verband moeten we nog aanhalen dat onlangs een laserbron op de markt is verschenen die beide vermogens integreert, wat hem bij uitstek geschikt maakt voor het snijden van dik staal.
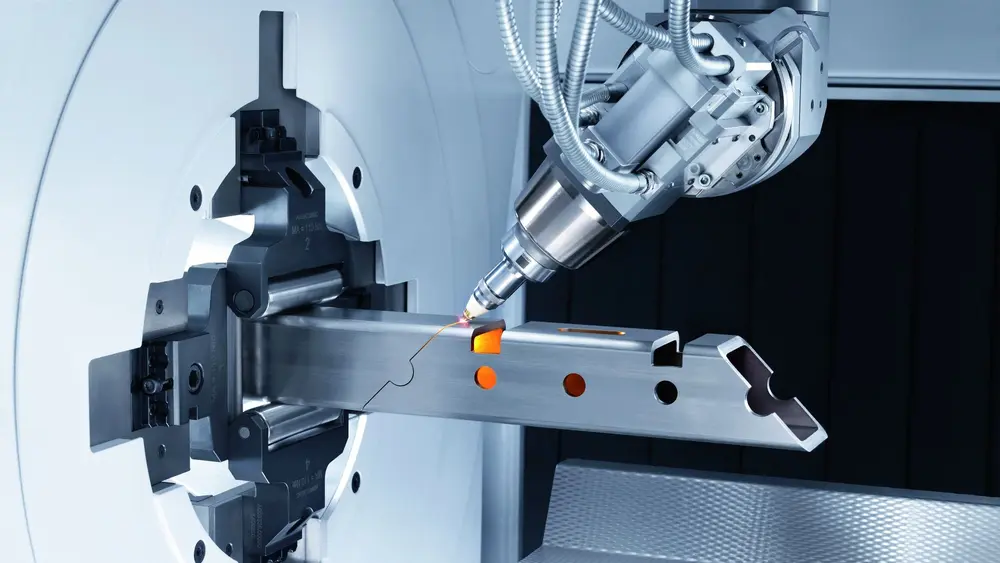
Andere elementen om mee rekening te houden
De totale bewerkingstijd is belangrijk, maar je mag je er ook niet op blind staren. Er spelen nog andere elementen, die een bepaalde machine minder dan wel beter geschikt maken voor jouw toepassingen. We bespreken er een paar om het artikel mee af te sluiten.
Extra bewerkingen
Is het nuttig om extra bewerkingen te integreren? Niet elke fabrikant kijkt daar op dezelfde manier tegenaan. Zij die de combinatie met het tappen, flowdrillen, inpersen van moeren en het boren van gaten aanbieden, verwijzen naar de bestaansreden van een buizenlaser: het elimineren van tijds- en arbeidsintensieve manipulatiestappen en handlingtijd als gevolg van het feit dat er slechts één machine bij de snijbewerking betrokken is. Dat je in één moeite bijvoorbeeld ook kan tappen op de buizenlaser, past naadloos in dat verhaal. Anderzijds – en dat is het argument van zij die deze mogelijkheid niet in het aanbod hebben – gaat het om twee relatief trage bewerkingen in vergelijking met het snijden, waardoor de snijkop moet wachten. En de effectieve snijtijd is al vrij beperkt. Het is dus een kwestie van visie, eerder dan van technische uitdagingen, want die zijn alles bij elkaar vrij beperkt.
Open profielen
Een ander aspect dat soms over het hoofd wordt gezien: niet alle buislasers kunnen open profielen snijden. Dat heeft in de eerste plaats met de software te maken. Sommige pakketten herkennen in een U-profiel, bijvoorbeeld, geen koker of buis omdat op geen enkel punt in de tekening de omtrek van de buis volledig is. De tekening voorzien van een extra brugje zou dat kunnen oplossen. Weet ook dat het risico op botsingen bij open profielen toeneemt. Voor sommige programmeersoftware wordt dat te complex om te verwerken. En er is nog een derde probleem, dat volledig losstaat van de uitdagingen op vlak van software. Open profielen zijn niet met alle types van klauwplaten compatibel. Hier zou een opvulkaliber een uitweg kunnen bieden.
Reststuk
Tot slot stellen we vast dat de lengte van het reststuk niet bij elke machine dezelfde is. Een afvalstuk ontstaat doordat je voor het inspannen van de buis een bepaalde lengte nodig hebt. Hoeveel materiaal je zo verliest, hangt af van fabrikant tot fabrikant, maar er bestaan machines waarbij dat tot ongeveer 200 mm per ingespannen lengte kan oplopen. Via speciaal daarvoor ontwikkelde reductiecycli kan het verlies sterk worden verminderd. Hoe werkt dat? In normale omstandigheden staat de ondersteuning of bril voor de snijkop. In reductiemodus is dat niet het geval. Met andere woorden, er wordt achter de bril gesneden. Een andere oplossing maakt gebruik van meerdere brillen. Daar schuilt het geheim in het overnemen van de buis. De lengte van het reststuk is daardoor nihil.
Met dank aan BLM Group, Bystronic, Haco, LVD en V.A.C. Machines
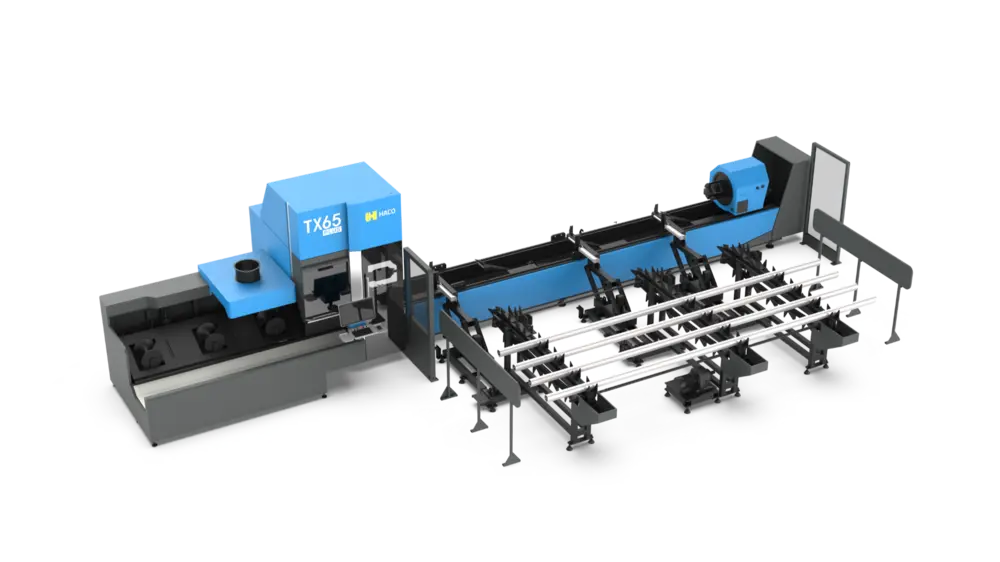