Nieuwe variaties op de combimachine
Van additive manufacturing tot vezelversterkte kunststoffen voor de plaatbewerking
Bij de combimachines voor plaatbewerking is de combinatie ponsen en lasersnijden de meest voor de hand liggende. Dat is het type machine dat de voordelen van beide technieken combineert. Bedenken de machinebouwers geen andere combinaties van technieken die ze in één machine integreren, zoals dit bij de verspanende machines wel meer en meer gebeurt?
Om met het antwoord op de laatste vraag te beginnen: ja en nee. Sommige machinebouwers integreren specifieke technologieën om een bestaand proces te verbeteren. Een bekend voorbeeld is warm omvormen (hot forming), waarbij hogesterktestalen in de matrijs tot 200 à 600 graden verwarmd worden en dan pas geperst. Hierdoor zijn ze beter te vormen. In zeker zin is dit ook een gecombineerde technologie. Minder bekend is de combinatie van dieptrekken met vibratie. Door de plaat in de onderste matrijs aan een trilling bloot te stellen met een frequentie van 20 Hz, vloeit het materiaal beter en laat zich de plaat nauwkeuriger en gemakkelijker vormen. De laag frequent trillingen verminderen de wrijvingskracht, wat een zichtbaar effect heeft op de kwaliteit van het uiteindelijke werkstuk. Zo kan men diepere vormen produceren en is er minder kracht nodig.
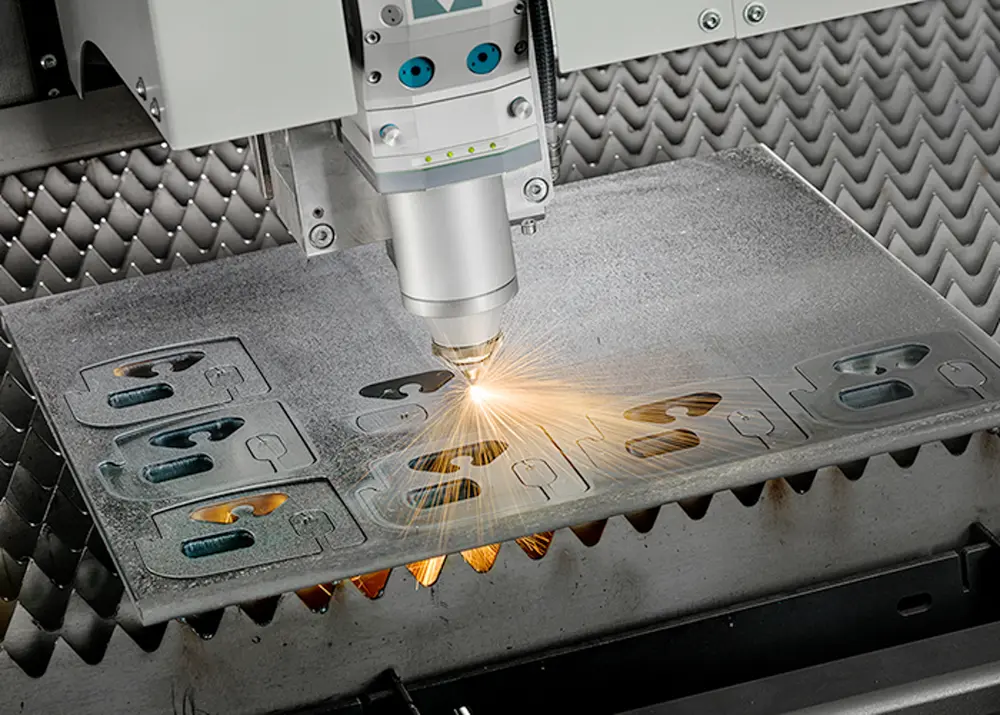
AM met plaatbewerking
Meestal wordt met een combimachine iets anders bedoeld: het combineren van bewerkingen die doorgaans op twee standalone machines plaatsvinden. Volgens deze definitie van combimachines is er een nieuwe combinatie in ontwikkeling, namelijk omvormen gecombineerd met additive manufacturing. Hiervoor zijn meerdere varianten in ontwikkeling. De drijfveer is de vraag naar lichtere constructies, met name in de transportmiddelenindustrie omdat men daar gewicht wil reduceren om de CO2-emissie omlaag te brengen. De automobielindustrie gebruikt al decennia de zogenaamde tailored blanks. In feite worden deze geproduceerd door de combinatie van dieptrekken waarna met dezelfde slag het materiaal precies gestuurd wordt. Zo ontstaan verdikkingen in het materiaal, doorgaans 1 tot 5 mm dik. Op die manier hoeft niet een heel onderdeel van dikkere plaat te zijn omdat men op een bepaald punt een minimale dikte nodig heeft.
De belangrijkste beperking van tailored blanks is dat de materiaalstroom zijn grenzen kent. Men kan niet onbeperkt materiaal naar een bepaalde punt in het onderdeel laten vloeien, de geometrie is hier een belangrijke factor in. En die hangt ook weer nauw samen met de vorm van het eindonderdeel. Bovendien is het een relatief kostbaar proces, vanwege de speciale gereedschappen die nodig zijn. Daarom wordt het vooral in de automobielindustrie toegepast, omdat hier de series groot zijn en de dure gereedschapskosten over veel onderdelen kunnen worden geamortiseerd. Onderzoekers van de universiteit in Erlangen (Duitsland) zijn daarom bezig om additive manufacturing als technologie aan de productie van de tailored blanks toe te voegen.
De belangrijkste beperking van tailored blanks is dat de materiaalstroom zijn grenzen kent
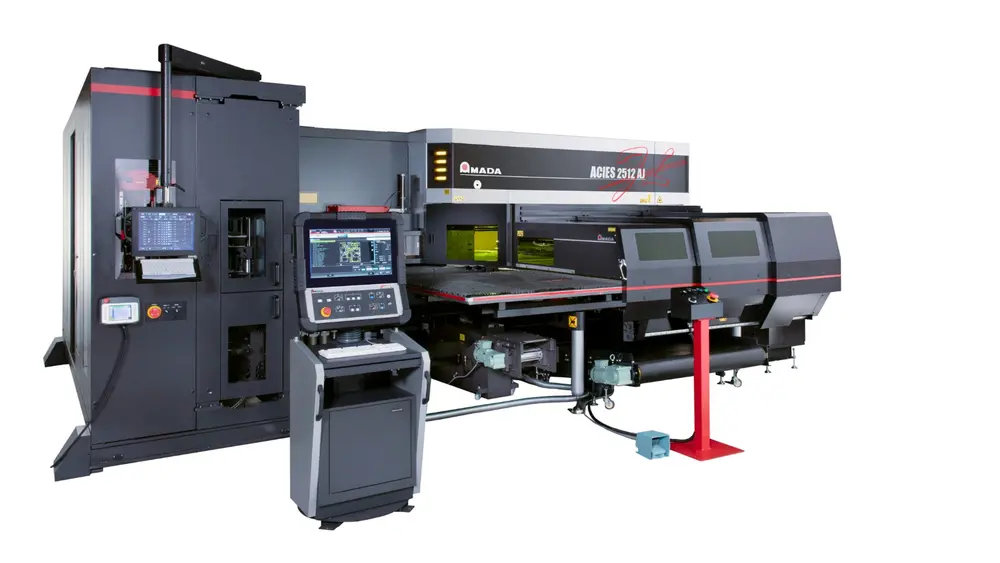
Minder gereedschappen nodig
Daarmee kan men de plaatdikte – ergo gewicht – tot het minimum beperken en waar nodig versterkingen aanbrengen met additive manufacturing, oftewel 3D printen. Bovendien zijn er geen kostbare gereedschappen meer nodig waardoor de combinatietechnologie wellicht ook toepasbaar is bij kleinere series.
Als additive manufacturing technologie wordt de laserpoederbedtechnologie gebruikt. Op de vlakke plaat wordt op de plaats waar uiteindelijk méér materiaal nodig is, extra materiaal aangebracht. De Duitse onderzoekers gebruiken een dunne plaat die de afmetingen heeft van het bouwplatform van de 3D-metaalprinter. Nadat het extra materiaal is aangebracht, snijdt men met een laser de juiste vorm uit en wordt het onderdeel gevormd zoals dat gebruikelijk is bij de productie van tailored blanks. Het eindproduct heeft dan op de plek waar dit nodig is aanzienlijk meer materiaal dan zonder de toevoeging van additive manufacturing. Het onderzoek heeft zich gericht op het creëren van een vertanding, die ontstaat door het materiaal te dieptrekken. Deze technologie is nog niet direct inzetbaar, omdat er door het additief aanbrengen van materiaal verschillen in hardheid ontstaan waardoor het risico op scheuren in het materiaal toeneemt. Toch zijn de onderzoekers optimistisch en zien ze voordelen in deze combitechnologie omdat de vorm van de vertanding – of een andere geometrie - eenvoudig aangepast kan worden, omdat additive manufacturing verder geen gereedschappen vereist.
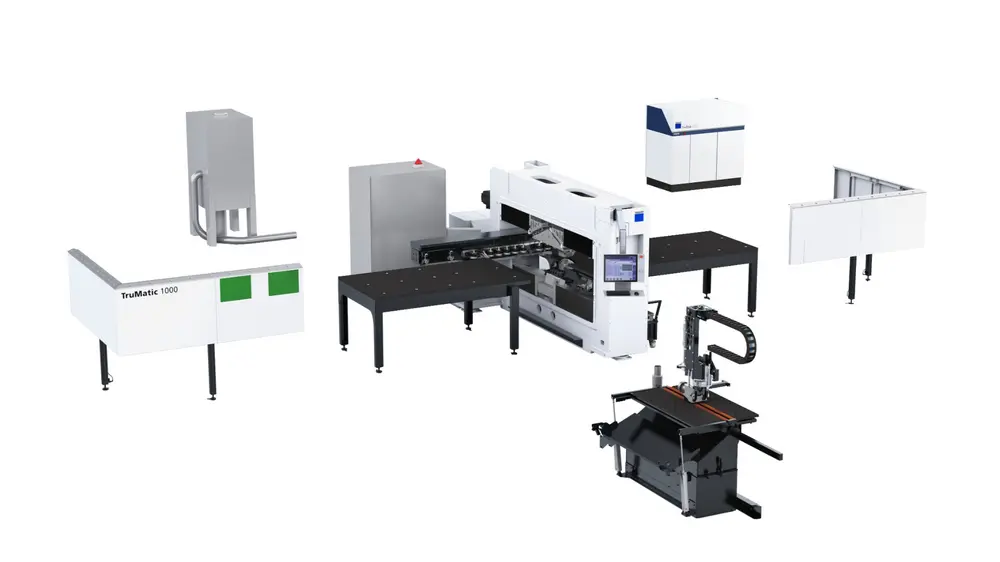
Flens als versterking van gat
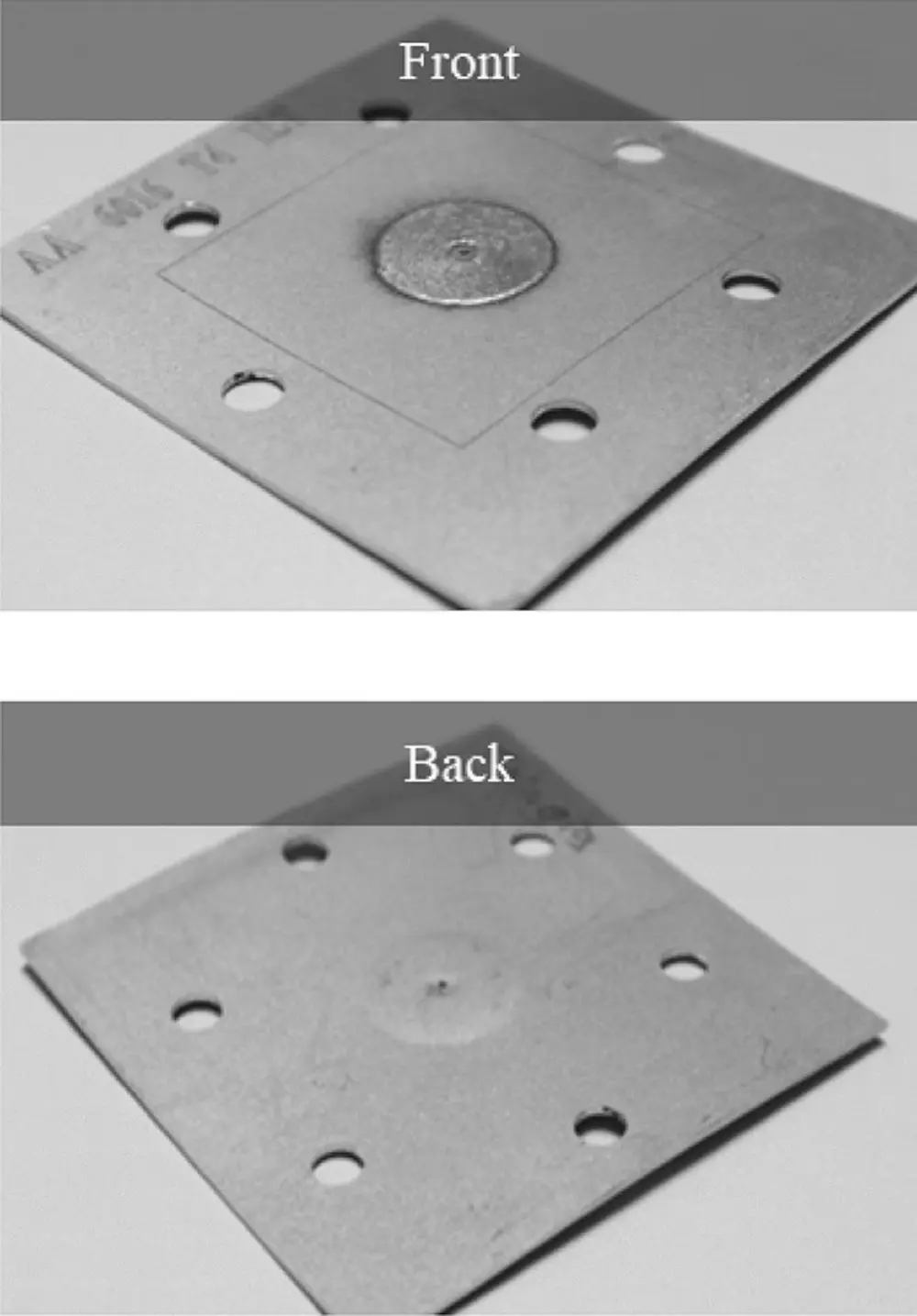
Zo ziet de additief aangebrachte gatflens er uit zoals de onderzoekers van de ETH Zürich hebben getest
De Duitse onderzoekers zijn niet de enige die additive manufacturing willen combineren met dieptrekken of een andere omvormtechnologie voor dunne plaat. In Zwitserland onderzoeken wetenschappers van het ETH in Zürich hoe ponsgaten in dunne plaat, waarin een functie-element zoals een tap geperst wordt, versterkt kunnen worden met additive manufacturing.
Met laser metal deposition (LMD) bouwen de onderzoekers rond een gat van 6 mm in een aluminiumplaat (6061, een in de auto-industrie veel gebruikte aluminiumlegering) een flens op. Dit kost relatief weinig tijd: in 20 seconden heeft men een laag materiaal neergesmolten. In het onderzoek gaat het om een verdikking van 0,3 tot 0,4 mm. Deze versterking vertoont geen porositeit en de vervormbaarheid van het materiaal verschilt slechts minimaal ten opzichte van het standaard 6061 aluminium.
Hierna wordt het functie-element ingeperst. Het geheel ondergaat nog een warmtebehandeling om spanningen uit het materiaal te halen en de sterkte te verbeteren. In het gat is een 7/16 UNF schroeftap geperst, passend op het flensgat met een diameter van 10 mm en wanddiktes tussen 1 en 1,5 mm. Hoewel de mechanische eigenschappen tijdens het proces veranderen, blijft alles binnen de marges. Met 1 laag materiaal aangebracht rond het gat verbetert de afschuifkracht al met 14% en na de warmtebehandeling zelfs met 196%. Bij 3 lagen (in totaal dus 1 minuut extra cyclustijd) zijn deze percentages respectievelijk 164 en 380% volgens de onderzoekers in Zürich.
Dunne plaat versterken met kunststof vezels
Een ander Duits team wetenschappers zoekt de innovatie in een andere richting: het combineren van metaal met kunststof in één processtap. Met het MultiForm-principe hebben de onderzoekers een hybrideproces ontwikkeld voor de productie van lichte structuurdelen voor onder andere mobiliteitstoepassingen. Het hybrideproces is een combinatie van metaalomvormen met het vloeipersen van Polyamide voor 40% gevuld met lange vezels. Tot nog toe worden dit soort hybride componenten in meerdere processtappen geproduceerd: eerst wordt de dunne plaat gevormd in een pers; daarna wordt een coating aangebracht die voor een betere hechting van de kunststof zorgt, waarna het metalen onderdeel met kunststof wordt omspoten, in-mold assembly. Het alternatief is dat de twee onderdelen los van elkaar worden geproduceerd en dan worden verlijmd, post-molding assembly.
De onderzoekers van de universiteit in Siegen combineren alles in één processtap. Daartoe worden de lange vezels in een gesmolten toestand in een verwarmde matrijs geplaatst. Tussen de neerhouder en de matrijs wordt een dunne plaat gepositioneerd, die voorbehandeld is met een coating om de verbinding met de vezels te versterken. Dan sluit het systeem en drukt de stempel de plaat en de lange vezels in de matrijs. Door de druk verspreiden de gesmolten Polyamide vezels zich over de hele plaat waardoor het hybride werkstuk ontstaat. Dat wordt met waterstraalsnijden in de juiste vorm gesneden.
Wat dit betekent voor het gewicht blijkt duidelijk uit de vergelijking van de materiaalspecificaties van een langs- en dwarsdrager voor een auto. Met de nieuwe technologie volstaat een plaat van minimaal 2 mm dikte, terwijl zonder de vezelversterking er minstens plaat van 3,5 mm dik nodig zou zijn om dezelfde mechanische eigenschappen te realiseren. Vergeleken met een stalen component is de hybride langsdrager 20% lichter. De cyclustijd zou rond de 25 seconden per langsdrager uitkomen, wat volgens de onderzoekers kort genoeg is voor serieproductie.
Vergeleken met een stalen component is de hybride langsdrager 20% lichter
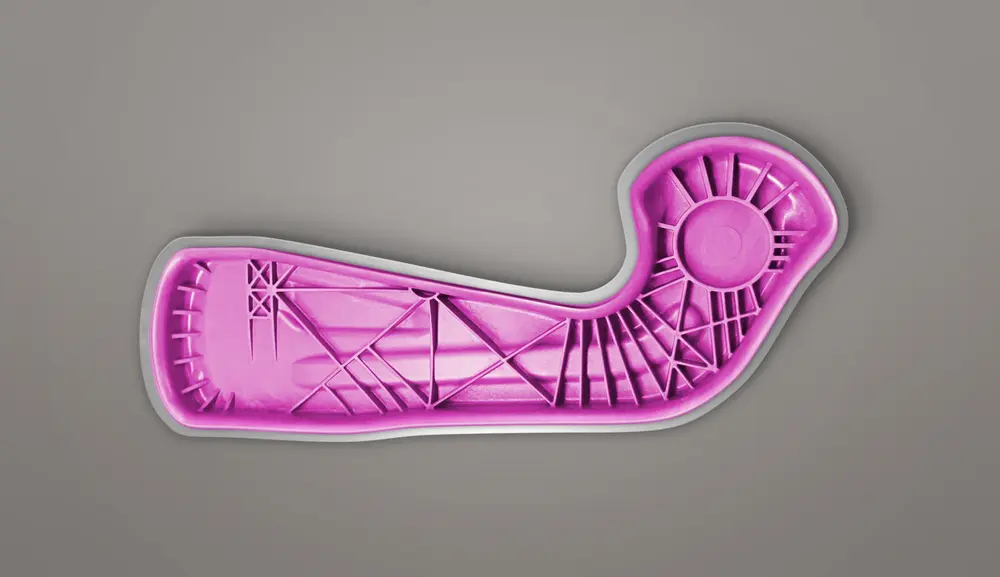
De demonstrator van de Multiform-technologie van de Universiteit Siegen. Deze langsdrager voor een wiel bestaat uit dunne plaat die met vezels is versterkt. Voor de combinatie van dieptrekken en persen zijn met Vestamelt Hylink van Evonik Polyamide 6, 12 en 610 voor 40% gevuld met lange vezels verbonden met een dunne plaat
Plaat- en buislaser in één
De drie voorbeelden van combimachines die hiervoor zijn beschreven, zitten nog in de ontwikkeling. Daarbij is het Multiform-project het verst. Concreter is de combinatie van buis- en plaatlaser in één machine, die sinds anderhalf jaar op de markt is. Helemaal geïntegreerd is dit weliswaar niet, maar de bedrijven die met een plaatlaser beginnen kunnen er naderhand een module voor het lasersnijden van buis aan toevoegen, zonder dat ze in een nieuwe laserbron moeten investeren. Hiermee kunnen ze de kostbare laserbron efficiënter benutten, alhoewel net als bij elke combimachine één technologie stilstaat. Dat vergt een afgewogen berekening.
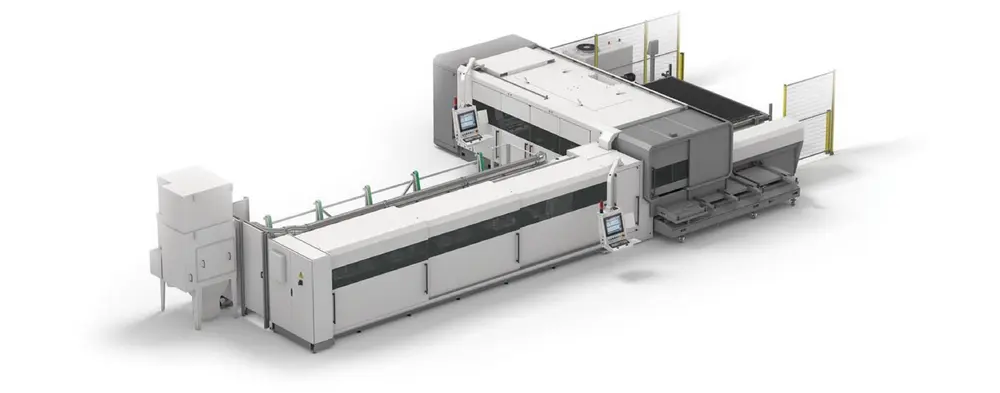
BLM Group biedt plaatbewerkers de kans om buis- en plaatsnijlaser in één systeem te integreren, de LC5. Hierdoor kan het systeem meegroeien met het bedrijf of is men flexibel in de orders die verwerkt moeten worden, zonder dat er geïnvesteerd moet worden. Het systeem is leverbaar met een fiberlaser van maximaal 6 kW