Convergentie OT en IT geen luxe, maar noodzaak
Systeemscheiding is rem op datagestuurde productieprocessen
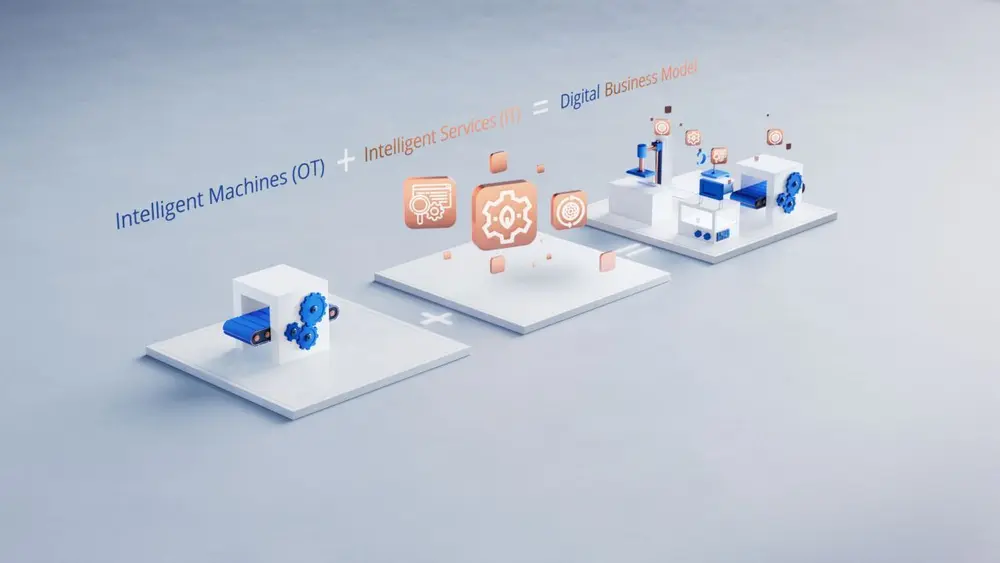
Door de ontwikkelingen op het gebied van data-integratie en data-interoperabiliteit wordt de OT/IT-convergentie – de samenwerking’ tussen operationele technologie (OT) en bedrijfsmatige informatietechnologie (IT) − steeds belangrijker. Die maakt het mogelijk realtimegegevens van productiemachines te combineren met geavanceerde data-analysetools. Dit leidt tot optimalisatie van zaken als productie-efficiëntie, kwaliteitscontrole en energiebeheer, vandaar ook dat er continu wordt gewerkt aan innovaties op dit gebied.
Gegevensverwerking
Operationele technologie (OT) en bedrijfsmatige informatietechnologie (IT) groeien steeds meer en steeds sneller naar elkaar toe. Die verregaande integratie heeft alles van doen met de stroom aan digitale ontwikkelingen waaronder cloud en edge computing, Internet of Things (IoT) en Industrie 4.0. Het hoge tempo hangt samen met de ontwikkeling van de benodigde tools en platforms, de verbeterde connectiviteit (bijvoorbeeld 5G) en de noodzaak om uit efficiëntie- en kostenoverwegingen nieuwe technologieën sneller te omarmen.
Begrippenkader
• Bandbreedteverbruik: de mate van data-uitwisseling via het netwerk in een zeker tijdvak, uitgedrukt in MB.
• Interface-apparatuur: apparaten die communicatieprotocollen van oudere OT-systemen vertalen naar protocollen die gangbaar zijn binnen moderne IT-systemen.
• Latentie: de hoeveelheid tijd die verstrijkt tussen een verzoek en de bijbehorende respons.
• Middleware: software die gegevens van oudere systemen verzamelt, normaliseert en doorstuurt naar IT-systemen in een compatibel formaat.
• Virtualisatie: technologie waarmee meerdere virtuele machines op één fysieke server draaien, wat de efficiëntie en flexibiliteit verhoogt.
Datagestuurd
De geschetste ontwikkelingen leveren veel voordelen op, maar ook uitdagingen. Alvorens hierop in te gaan een korte ‘opfriscursus’.
OT
OT verwijst naar de hard- en software die wordt gebruikt om fysieke processen, apparaten en infrastructuren aan te sturen en te monitoren. De OT begon zich in de jaren zestig en zeventig te ontwikkelen, en groeide gedurende enkele decennia uit tot een reeks van geavanceerde digitale infrastructuren die productieomgevingen en hun infrastructuur betrouwbaar laten functioneren. Het accent ligt daarbij op de realtimeverwerking van informatie afkomstig van bijvoorbeeld sensoren, actuatoren, PLC’s of industriële netwerksystemen.
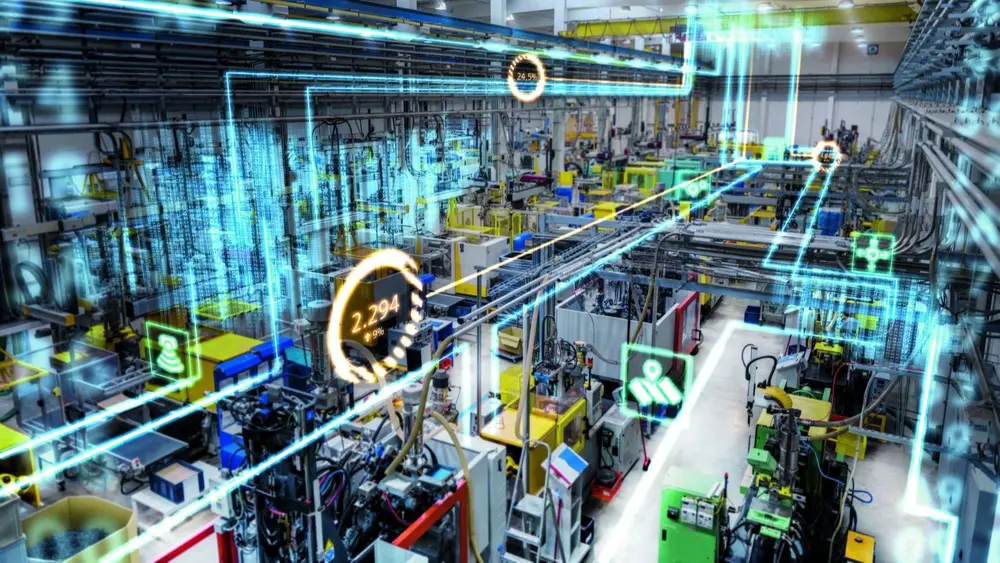
IT
IT is gericht op het verwerken, opslaan, beveiligen en verzenden van informatie binnen een organisatiestructuur. In de jaren vijftig en zestig gebeurde dit met de eerste generatie mainframes, logge apparaten met weinig geheugencapaciteit die gebruikmaakten van ponskaarten en magneetbanden. Sinds de (op)komst van minicomputers, pc’s en interne netwerken kwam een en ander eind vorige eeuw in een stroomversnelling, en sinds begin deze eeuw is de rol van IT behalve ondersteunend ook sturend en innoverend.
Strikt gescheiden
Rond eeuwwisseling opereerden OT en IT nog strikt gescheiden, en met reden. Met een zogeheten ´air gap´, een ICT-infrastructuur die fysiek gescheiden is van andere netwerken (zie ook de tabel) trachtte men het risico op digitale dreigingen te minimaliseren. Wat niet hielp was het feit dat OT- en IT-systemen verschillende beheerders kenden: OT werd beheerd door technici en engineers, IT door IT-specialisten.
Niet alleen verschilden hun uitgangspunten − in OT draait het om availability (de productie mag niet stoppen), bij IT om confidentiality (data en dataverkeer moeten veilig zijn) – ook de communicatie verliep moeizaam: men sprak elkaars taal niet. Ook konden en kunnen systemen onbedoeld stilvallen wanneer IT-processen als updates of authenticatieprotocollen naar OT worden gebracht zonder daarbij rekening te houden met de noodzaak van continuïteit. Een robuuste OT-Backbone (zie kader) maakt tegenwoordig een veilige en gecontroleerde koppeling tussen OT en IT mogelijk.
OT-Backbone
Een OT-Backbone zorgt binnen de OT-omgeving voor betrouwbare en snelle communicatie tussen fabriekslijnen, servers en controlekamers; zaken als betrouwbaarheid, lage latentie en beschikbaarheid hebben daarbij prioriteit. De hoogwaardige netwerklaag is gebouwd met behulp van industriële ethernet-switches, redundantie (dubbele verbindingen zodat een storing geen impact heeft), realtimedataverwerking-ondersteuning en cybersecuritymaatregelen specifiek voor OT waaronder segmentatie, firewalls en monitoring. Behalve voor betrouwbare OT-communicatie zorgt het systeem ook voor de separatie van IT- en OT-data en OT/IT-werkzaamheden, dit laatste middels netwerksegmentatie en beveiligingsarchitecturen.
Rem op datasturing
Als gevolg van de ontwikkelingen binnen de data-integratie en -interoperabiliteit is er steeds meer behoefte aan OT/IT-convergentie. Sterker nog: de scheiding van OT- en IT-systemen kan zelfs een rem vormen op datagestuurde productieprocessen.
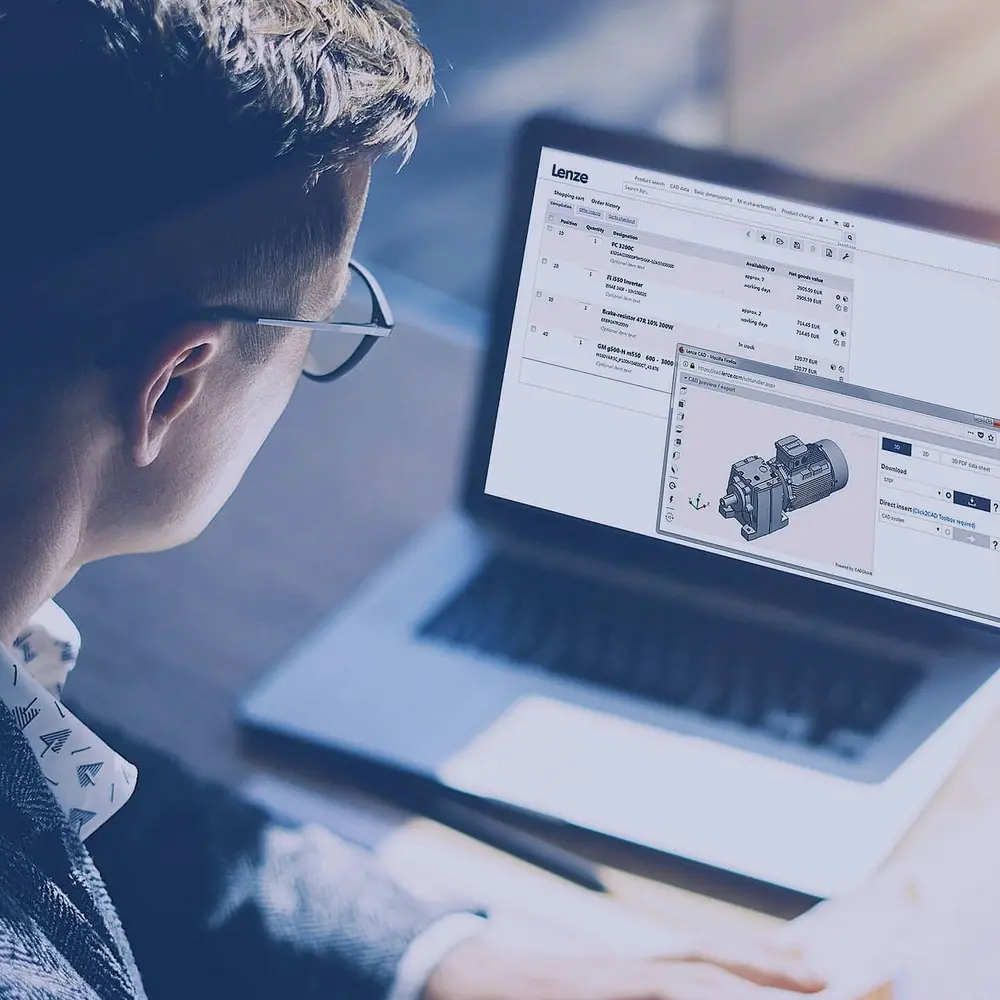
Gegevensuitwisseling en integratie
In een IoT-omgeving worden enorme hoeveelheden gegevens verzameld ter analyse. Wanneer IT- en OT-systemen gescheiden opereren, zijn deze niet centraal beschikbaar. Niet alleen gaat dit ten koste van de end-to-end visibility, ook zal de gegevensanalyse suboptimaal verlopen (datasilo's).
Schaalbaarheid en flexibiliteit
Gescheiden domeinen bemoeilijken de invoering van schaalbare, flexibele oplossingen, wat het lastig(er) maakt snel te anticiperen op digitale veranderingen. Integratie maakt de implementatie van nieuwe technologieën als AI, machine learning, en cloud en edge computing bovendien eenvoudiger.
Als gevolg van de ontwikkelingen binnen de data-integratie en
-interoperabiliteit is er steeds meer behoefte aan OT/IT-convergentie
Cybersecurity
Beveiligingsproblemen treden met name op wanneer OT-systemen zijn aangesloten op een verouderd, gesloten netwerk en de IT-systemen zijn verbonden via internet. Integratie maakt geavanceerde beveiligingsprotocollen en monitoringtools real time toepasbaar, wat de beveiliging op een hoger plan brengt.
Besluitvorming
IT-systemen kunnen real time gegevens verwerken en inzichten bieden, maar als de OT-systemen niet goed zijn geïntegreerd, leidt dit tot vertraging bij de dataverzameling en -analyse. In een productieomgeving, waar snelle besluitvorming essentieel is, zal dit tot problemen leiden.
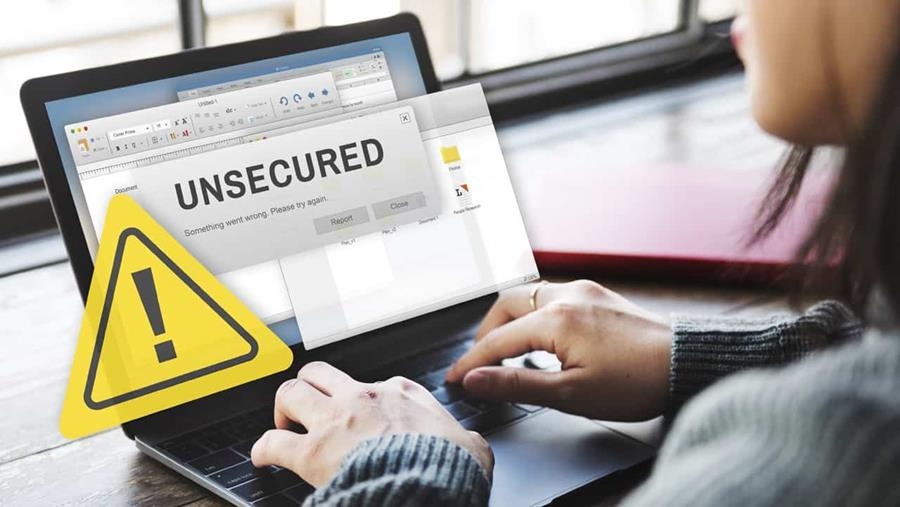
Verenigde netwerkarchitectuur
Gezien het voorafgaande is de overstap naar een geïntegreerde OT/IT-structuur een volstrekt logische. Hier komen systemen, gegevens en processen samen in een verenigde netwerkarchitectuur, leidend tot verbetering van:
- de productie-efficiëntie, door het sneller (kunnen) traceren en optimaliseren van performance bottlenecks en een efficiënter gebruik van middelen (resourcebeheer), resulterend in lagere kosten;
- de kwaliteitscontrole, doordat continue monitoring van de productkwaliteit mogelijk wordt en trends en patronen kunnen worden geïdentificeerd die duiden op kwaliteitsproblemen;
- het energiebeheer, door patronen in energieverbruik te identificeren en op basis daarvan – al dan niet automatisch − te komen tot optimale machine-instelling.
Daar komt nog bij dat OT/IT-convergentie producenten toegang geeft tot nieuwe technologieën als edge en cloud computing en virtualisatie (zie Begrippenkader).
Procedure
Na te hebben geconstateerd dat de (steeds sneller verlopende) convergentie van OT en IT een feit is, is de voor de hand liggende vraag: hoe komt deze nu daadwerkelijk tot stand? Het antwoord is: door een combinatie van technologische integratie, organisatorische afstemming en beveiligingsmaatregelen.
OT/IT-convergentie geeft producenten toegang tot nieuwe technologieën als edge en cloud computing en virtualisatie
Technologische integratie
OT-systemen worden via industriële communicatiestandaarden als OPC UA of MQTT gekoppeld aan IT-systemen waarbij controllers een intermediaire rol vervullen (zie kader Controllers). Een probleem kan zijn dat industriële installaties nog draaien op oude(re) besturingssystemen die moeilijk matchen met moderne IT-infrastructuur. De remedie daartegen zijn middleware- en interface-apparaten (zie Begrippenkader).
Organisatorische afstemming
IT- en OT-specialisten werken samen aan projecten en infrastructuur. Bedrijfs- en productieprocessen worden op elkaar afgestemd via systemen als MES en ERP waarbij nadrukkelijk is vastgelegd wie waarvoor verantwoordelijk is.
Cybersecurity en betrouwbaarheid
Netwerken worden beveiligd zodat beide domeinen veilig kunnen communiceren. Om dreigingen vroegtijdig te kunnen detecteren worden systemen zowel op OT- als op IT-niveau bewaakt onder gebruikmaking van gemeenschappelijke protocollen en normen als ISA/IEC 62443.
Controllers
Een controller fungeert als een intelligente interface die procesdata omzetten in voor IT-systemen toegankelijke en bruikbare informatie. Ze vervullen als het ware een intermediaire rol tussen het deterministische, realtimedomein van OT en het flexibele, datagedreven domein van IT. Juist omdát controllers aan beide domeinen raken zijn ze te beschouwen als een high-value target binnen de beveiligingsarchitectuur. Beveiligingsmaatregelen als zero trust-architectuur, gelaagde beveiliging (defense-in-depth), netwerksegmentatie en strikte toegangscontrole en logging zijn derhalve aangewezen.
Trends
Bedrijven die OT/IT-convergentie hebben omarmd kunnen sneller anticiperen op veranderingen in de markt, komen tot kostenbesparing en kunnen hun concurrentiepositie versterken. Er wordt dan ook volop gewerkt aan innovaties op dit gebied.
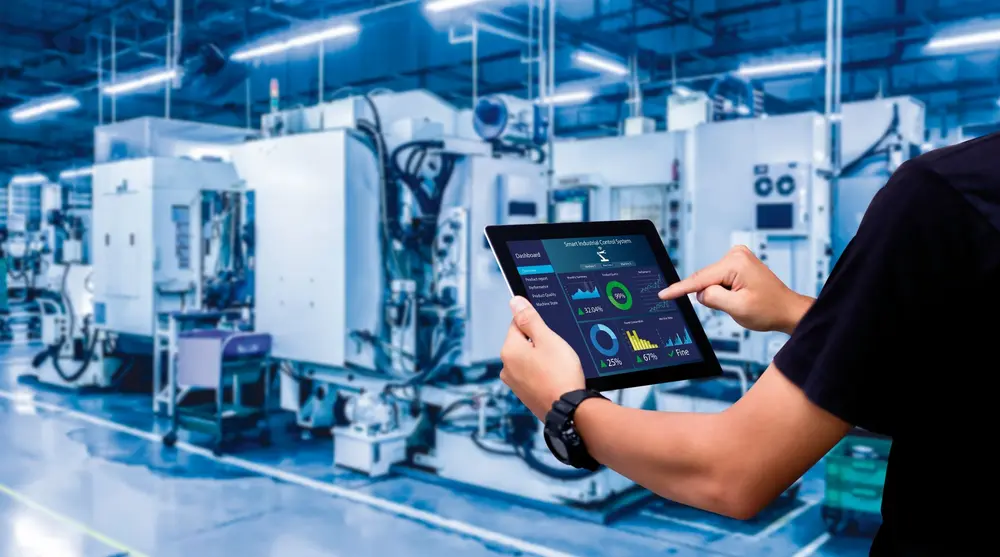
Data-analyse en AI
De integratie van OT- en IT-systemen creëert enorme hoeveelheden data. De analyse daarvan kan worden aangescherpt met behulp van artificial intelligence (AI) en machine learning, een subveld daarvan. Deze technologieën bieden bedrijven de mogelijkheid processen (verder) te optimaliseren en de productie te verbeteren door inzichtgestuurde beslissingen te nemen.
Edge computing
Hierbij worden gegenereerde gegevens lokaal verwerkt dan wel in een nabijgelegen server. Deze benadering vermindert de latentie en het bandbreedteverbruik (zie Begrippenkader). Ook de kans dat gevoelige informatie onderweg verloren gaat of wordt onderschept is aanzienlijk kleiner. Het feit dat in principe elk edge-apparaat een toegangspoort is voor cyberaanvallen maakt robuuste authenticatie- en toegangscontroles en endpoint-beveiliging een must.
Low-code- en no-code-platforms
Een low-code-platform is een ontwikkelomgeving waarin applicaties kunnen worden gebouwd met minimale handmatige codering. Optioneel is het gebruik van visuele interfaces, drag-and-drop-componenten en -sjablonen om de ontwikkeling te versnellen.
No-code-platforms zijn ontworpen voor een brede toegankelijkheid van de softwareontwikkeling. Ze worden doorgaans ingezet voor het snel automatiseren van processen of het bouwen van eenvoudige bedrijfsapplicaties.
Met medewerking van Cebeo, Lenze en Prokorment