Scanloos werken: het magazijn van de toekomst
Innovatiedrang bij Atlas Copco loont
Bij Atlas Copco Airpower in Wilrijk zit men duidelijk niet stil. Continu innoveren is daar het devies en dat werpt zijn vruchten af. Zo is men bezig met een significante efficiëntieslag in het magazijn. Dankzij een systeem met allerlei sensoren en camera's kan men de vorkheftrucks én de pallets met het nodige materiaal perfect traceren zonder herhaaldelijk te scannen. Er zit bovendien nog rek op het initiatief: zo oogt de toekomst wellicht volledig scanloos.
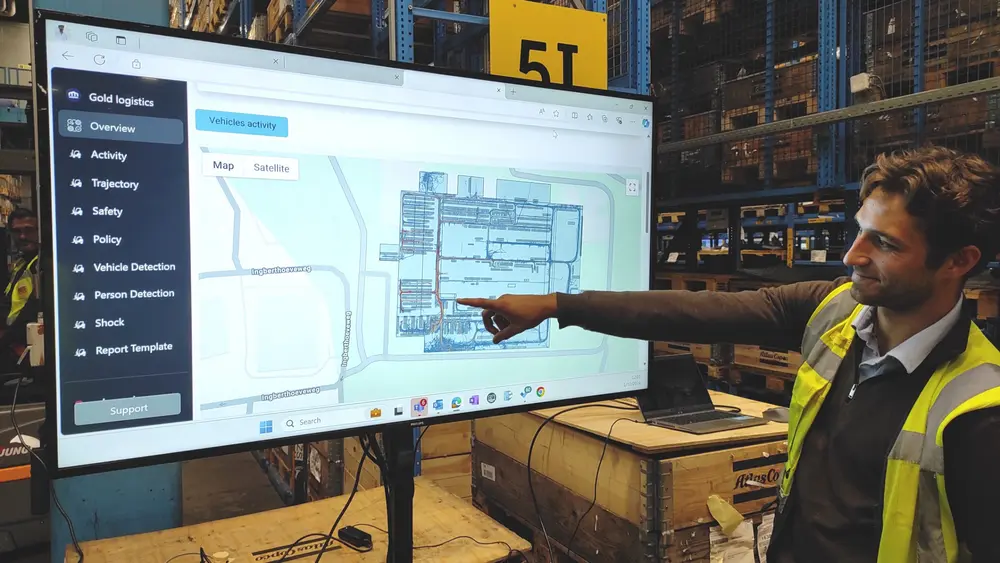
Minder scannen, vlotter werken
Stroomlijnen magazijn
We worden rondgeleid in het magazijn van Atlas Copco Portable Air in Aartselaar, ook wel liefkozend de 'supermarkt' genoemd. Hier speelt zich een van de nieuwste innovatieprojecten van de specialist in compressoren af: het scanloos verhandelen van pallets met onderdelen voor de productielijnen. Het is dan ook een drukke zone, met in totaal bijna 40 voertuigen die hun ding doen.
Het project kadert binnen het principe van smart vision, waarbij camerabeelden worden geanalyseerd en verwerkt met artificiële intelligentie. Alle vorkheftrucks zijn uitgerust met camera's en sensoren die in real time de positie van de voertuigen en de vervoerde pallets monitoren. Het doel is om zo de pallets – en dus de nodige onderdelen – te kunnen traceren, zonder dat men daarbij moet scannen.
Vroeger moest een pallet in het magazijn minimaal drie keer gescand worden. Bovendien bestond dit scannen vaak uit een vrij onergonomische handeling, wat het comfort van de bestuurders niet ten goede kwam. Met het nieuwe systeem wordt dus heel wat tijd bespaard, maar er is ook minder kans op menselijke fouten. Dit alles zorgt uiteindelijk voor een vlottere productie met minder stilstand.
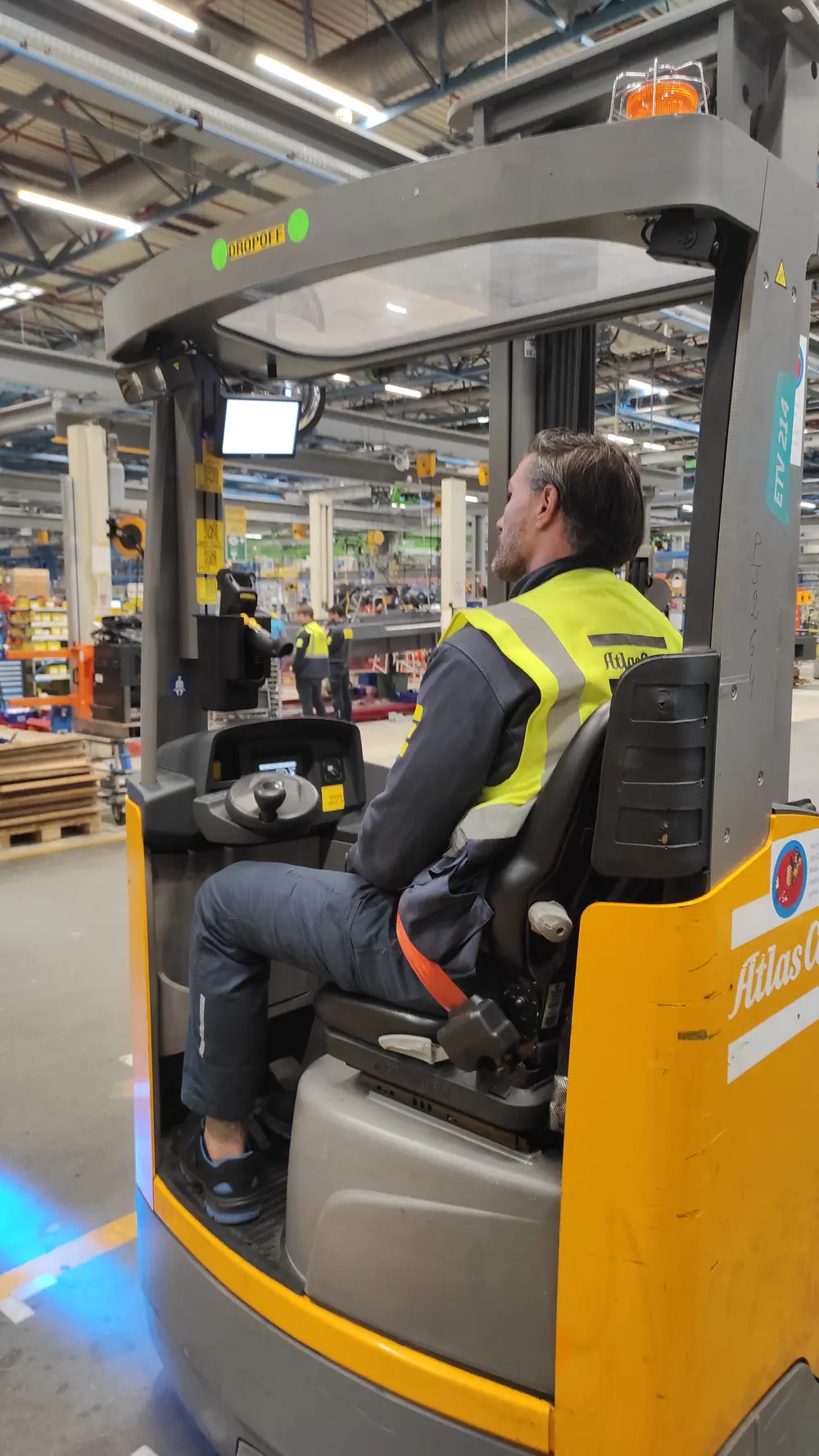
Werkingsprincipe
Hoe werkt dit alles nu? Een camera op het dak van de vorkheftruck scant continu het dak van het magazijn, waarbij het dankzij een deep learning-model zeer gedetailleerd weet waar het voertuig zich bevindt. Het volledige gebouw is immers in kaart gebracht door middel van een digital twin, waarin je in real time de vorkheftrucks ziet rijden. Deze technologie is een stuk preciezer dan gps.
Vervolgens zijn er heel wat sensoren aangebracht op de vorkheftrucks. "Naast de sensoren die instaan voor de veiligheid, zijn er twee die van bijzonder belang zijn: één die de hoogte van de lippen aangeeft en één die weet of de lippen beladen zijn of niet. De camera op het dak zorgt voor de x- en y-coördinaten, terwijl een van de sensoren op de lippen de z-as monitort. Zo weet het systeem exact waar een pallet wordt neergezet, zonder dat de nieuwe locatie moet ingescand worden om zo manueel een link te maken tussen de pallet en de nieuwe bestemming", geeft Rik Van de Velde, vice president Operations voor de Portable Air divisie, duiding bij het project.
Elke stap in het proces – bijvoorbeeld het plaatsen van een pallet in het rek – wordt apart geregistreerd. Aan het einde van de rit beschikt men over een uitgebreid logboek met data over de rijtrajecten en ook hoe men zich verplaatste: met lege of volle lippen.
Blijven innoveren
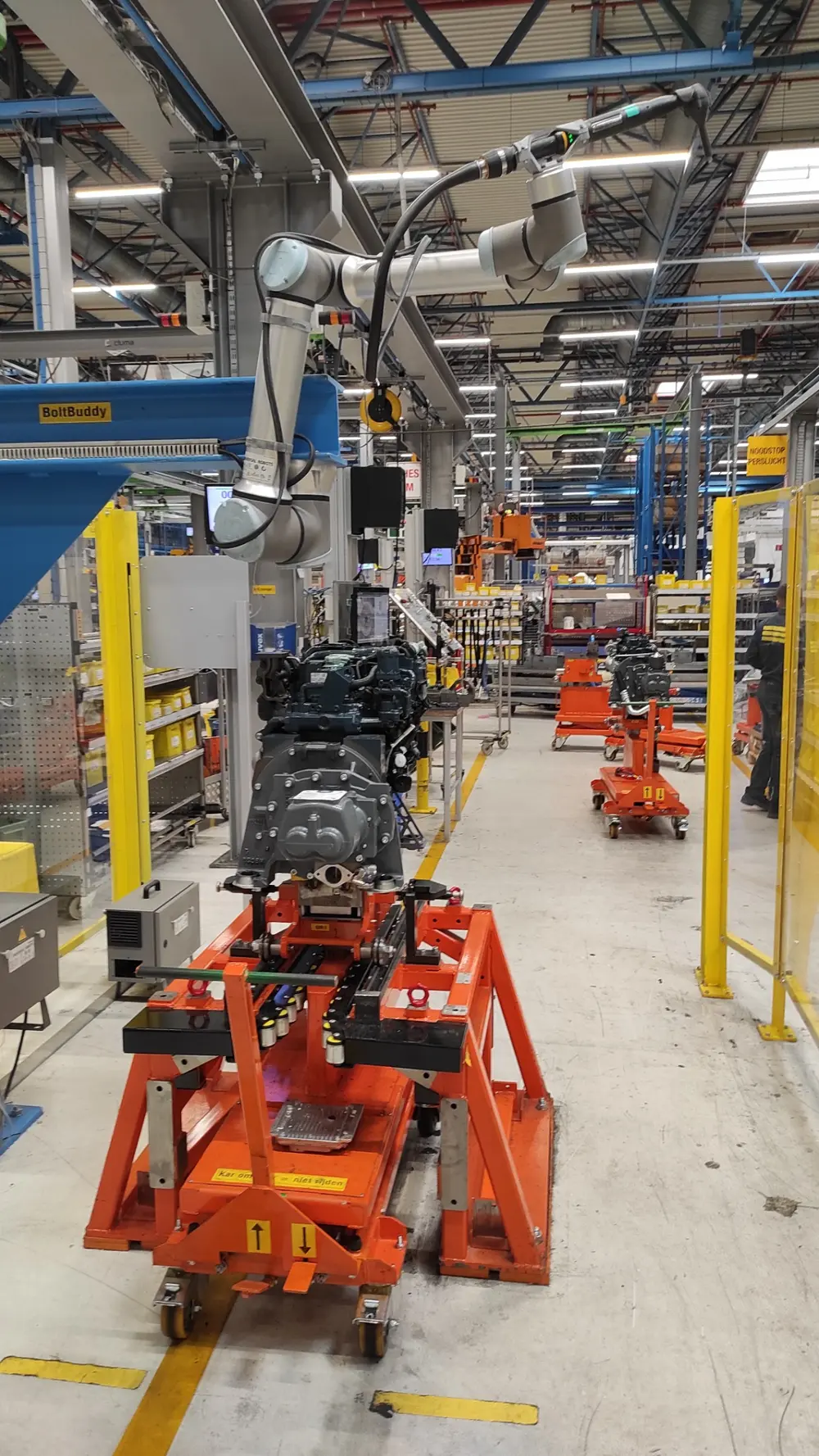
Even terugspoelen. Doorgaans ontstaan dergelijke initiatieven uit een bepaalde concrete noodzaak, maar in Aartselaar ligt het wat anders. "Wij zijn continu op zoek naar manieren om niet alleen onze producten, maar ook onze processen te verbeteren. Zo gebruiken we nu camera's met AI voor kwaliteitsinspectie en hebben we enkele cobots staan in de productielijnen. Innoveren staat centraal bij ons en we zijn dan ook bereid om nieuwe technologieën uit te proberen, zeker wat efficiëntie en duurzaamheid betreft. Atlas Copco Airpower is hierbij vaak een pilootsite, waar projecten uitgewerkt worden en vervolgens vaak elders worden uitgerold", gaat Rik verder.
Het nieuwste project, dat men nu volop aan het uitrollen is naar alle voertuigen in de werkplaats, is in verschillende fasen tot stand gekomen. "In 2020 kwam ik in het kader van een postgraduaat Smart Logistics deze technologie tegen en ik zag meteen het potentieel voor onze toepassing. Na wat doorontwikkeling voerden we in 2022 een feasibility studie uit met de hulp van twee studenten. Uiteindelijk zijn zij hier ook komen werken", geeft Anja Van Steen, teamleader Supply Chain & Production Logistics, meer duiding.
Bowout Broucke, logistics engineer, was een van die studenten. "Mijn thesis ging na hoe de smart vision-technologie concreet kon worden toegepast binnen het kader van pallet tracking bij Atlas Copco. Gewone trackers en RFID (Radio Frequency Identification) bleken immers niet de geschikte oplossing te zijn. Bij het project hadden we aanvankelijk twee pijlers in gedachten: kwaliteit en efficiëntie. Na verloop van tijd kwam ook het veiligheidsaspect daarbij. Door dit te onderzoeken ben ik eigenlijk op organische wijze nauw in contact gekomen met Atlas Copco, waar ze me dan ook een job hebben aangeboden."
Met het nieuwe systeem wordt heel wat tijd bespaard, maar is er ook minder kans op menselijke fouten
Veilig gevoel
Ondanks de vele vorkheftrucks is het toch bijzonder veilig in het magazijn. De helft van de vloot is namelijk uitgerust met verschillende sensoren, die helpen om personen aan de bestuurder te signaleren. Ze projecteren bovendien een blauw licht op de vloer, dat ook zij die naar een apparaat of blad staren meteen verwittigt van het potentiële gevaar. Gecombineerd met een vaste camera die extra informatie over voetgangers doorgeeft en een systeem dat de vorkheftruck bij nakende botsingen automatisch doet vertragen, voelt het magazijn als een aangename plek om te werken.
"Ons innovatieproject heeft belangrijke verbeteringen op het vlak van veiligheid teweeggebracht. Dit is een bijkomend voordeel, dat we aanvankelijk eigenlijk niet op het oog hadden", stelt Rik. "Het is gaandeweg wel uitgegroeid tot een van de drie centrale pijlers van het project. Daar zijn we best trots op, aangezien veiligheid toch fundamenteel blijft."
Concrete verbeteringen
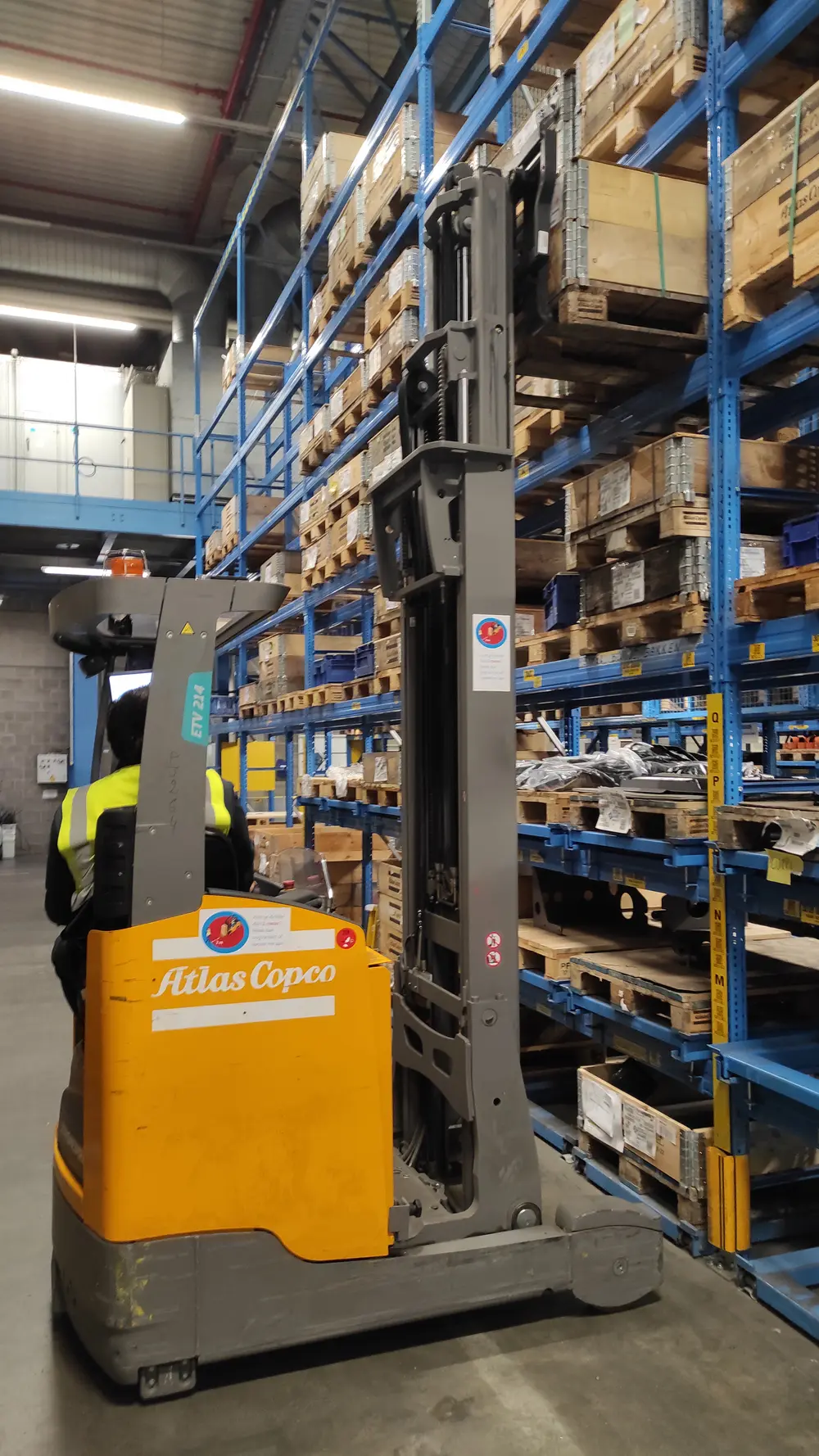
"Het tracken van de voertuigen biedt heel wat voordelen. Zo is er de verbeterde veiligheid, maar ook het locatiemanagement verloopt gestroomlijnder en met minder fouten. Ten slotte laat het verzamelen van al deze data toe om de rijtrajecten en de opslaglocaties te optimaliseren en indien opportuun het magazijn te herorganiseren. Op termijn biedt dit veel mogelijkheden om efficiënter en sneller te werken", stelt Bowout.
Het systeem heeft nog heel wat potentieel om door te ontwikkelen. "De volgende stap is het verbinden van de digital twin en de vorkheftruckbewegingen met het Warehouse Management System (WMS), om zo de instructies die bestuurders krijgen over het plaatsen van pallets te integreren in de display van het smart vision-systeem. Zo zien onze werknemers niet alleen welke stap ze juist gezet hebben, maar geeft dezelfde interface meteen ook aan wat de volgende stap moet zijn. Daarbij zal AI ook aanbevelingen geven. Deze integratie willen we volgend jaar al realiseren", aldus Rik.
Uiteindelijk is het de bedoeling om volledig scanloos te werken. Nu moet er nog eenmaal gescand worden wanneer een pallet aan de receptie binnenkomt. Dit laat toe om de pallet binnen te brengen in het magazijnsysteem, waardoor het vervolgens mogelijk is om de toegewezen pallet overal te volgen. "Er bestaan technologieën om ook die eerste scan te elimineren en het geheel nog meer te stroomlijnen. We zijn volop bezig met het evalueren van die opties, om zo te kijken wat het beste kan werken voor ons. We blijven in ieder geval innoveren en perfectioneren", sluit Anja af.