La champignonnière choisit une installation hybride à l’ammoniaque
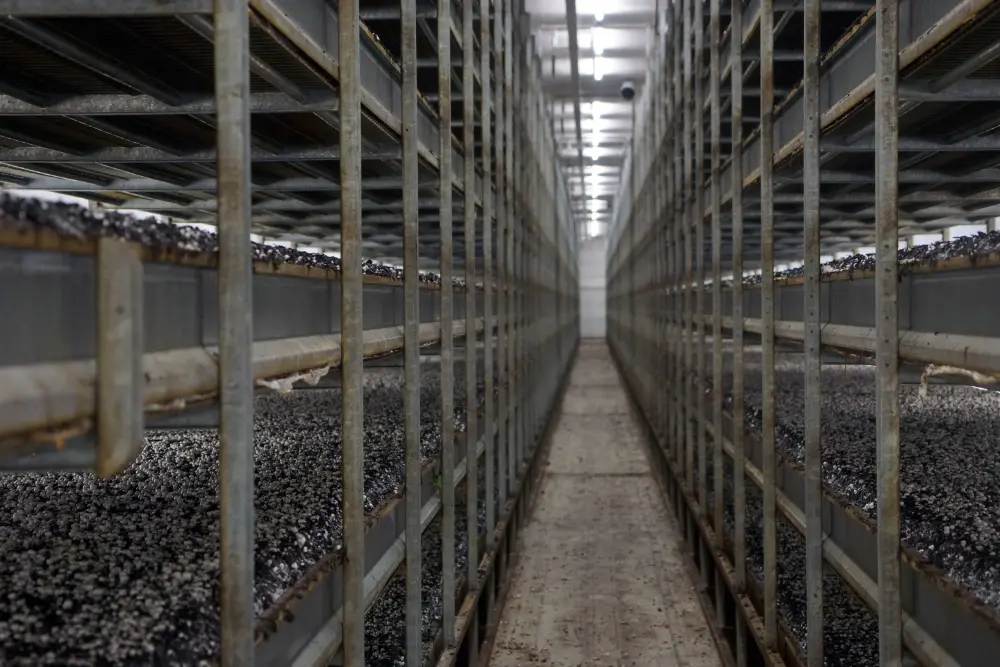
Température, humidité de l’air et taux de CO2 précisément adaptés aux champignons
Après un grand incendie en 2018, qui a ravagé une grande partie du hall de production, la champignonnière Gemert a immédiatement commencé la reconstruction. Dans les six mois, la production a été rétablie, en partie grâce à la construction rapide des nouvelles installations de refroidissement et de traitement de l’air, qui doivent garantir le climat idéal pour la culture du champignon.
Exigences élevées pour l’installation de refroidissement
La construction d’un système de refroidissement dans une champignonnière est un processus complexe, impliquant plusieurs parties (voir encadré). Pour commencer, naturellement le maître d’ouvrage, van den Boomen, qui pose des exigences en matière d’humidité de l’air et de température dans les chambres de culture des champignons, de variation maximale admise et de coût. Essentiels dans le processus de refroidissement sont un compresseur (BITZER), un échangeur de chaleur, des pompes et autres appareils (livrés par ECR) et un installateur qui dimensionne et construit l’installation (Verbrugge). Tout doit coïncider parfaitement, la communication et la concertation entre les parties est essentielle.
Guus Verbrugge (Verbrugge Koeltechniek):
“En un clin d’œil, toutes les donnees importantes sur le climat de culture par chambre sont controles”
Lois et règles
Mais le monde extérieur joue aussi un rôle. Frans van Laarhoven (BITZER) déclare à ce propos: “Il y a naturellement la législation environnementale, mais également les règles dans d’autres domaines. Depuis 2015 est entré en vigueur le règlement sur les gaz F, censé limiter l’utilisation de gaz à effet de serre fluorés et qui donne des directives quant au facteur GWP (Global Warming Potential) maximal du réfrigérant. Ceci explique notamment le choix de Verbrugge d’un réfrigérant naturel – ammoniaque – au lieu d’un gaz synthétique. Naturellement, d’autres facteurs ont influencé le choix de l‘installation complète: le prix d’achat, les coûts d’entretien, la consommation d’énergie – en fait le TCO, Total Cost of Ownership. Comme l’ammoniaque exige un autre traitement que les réfrigérants traditionnels, et afin d’exploiter pleinement les avantages de l’utilisation (optimisation énergétique et faible facteur GWP), Bitzer à Gemert a installé un nouveau produit, l‘ACP (Ammonia Compressor Package), un package complet comprenant un compresseur, un refroidisseur d’huile, des opérateurs d’huile et une commande pour utiliser l’ammoniaque, Il y a quelques années encore, Bitzer vendait surtout des éléments séparés pour une installation.”
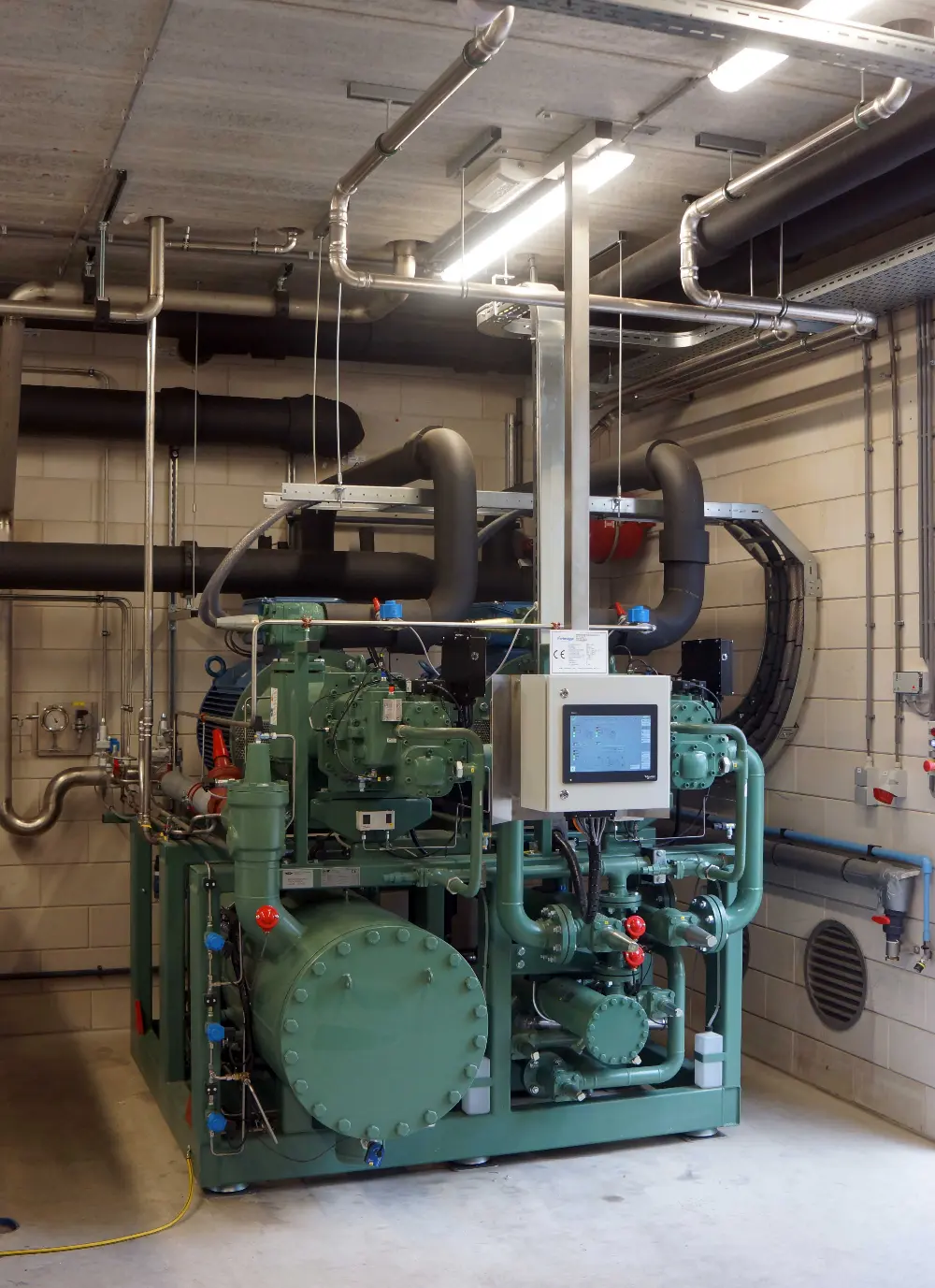
avec lequel les cellules de culture sont refroidies
Choix d’une installation hybride
Mais la catastrophe qui a précédé ce business case, a compliqué la situation. Puisque deux machines frigorifiques (utilisant encore le réfrigérant R134a, un gaz fréon) ont été épargnées et parce que la pression du temps était forte, on a décidé de construire une installation hybride. “Concevoir, dimensionner et construire une installation complète avec l’ammoniaque comme réfrigérant expansible dans les chambres de culture (expansion directe) aurait duré trop longtemps”, confie le technicien frigorifique, Guus Verbrugge. “Nous avons choisi un système qui transmet le froid produit dans un échangeur de chaleur sur un mélange eau/glycol qui refroidit les chambres. Nous pouvons vite recommencer et encore compter sur une ancienne machine dans les premiers mois (d’hiver), quand la demande de froid serait faible. Avant le début de l’été, le nouveau compresseur à ammoniaque est placé.”
Avantages et désavantages
“Ceci n’est peut-être pas la solution la plus efficace”, affirme van Laarhoven. “Car les pertes sont immédiates dans l’échangeur de chaleur. De l’autre côté, l’ammoniaque est toxique et vous avez naturellement affaire à des denrées alimentaires. Il est notamment possible de construire des solutions sûres, mais cela prend du temps. Et des investissements dans la sécurité.” Verbrugge: “L’utilisation uniforme de l’ammoniaque signifierait la présence de conduites d’ammoniaque aux greniers où se trouvent toutes les armoires de traitement de l’air. Là, la détection des fuites et la protection devraient aussi se placer. Maintenant, l’ammoniaque ne se trouve que dans la chambre de compresseur. Si de l’ammoniaque se libère, il ne peut pas atteindre la production.” Van Laarhoven conclut: “Aux Pays-Bas, des entreprises utilisent le système total avec des dérivations vers les chambres où il se dilate. Nous y avons réfléchi, mais avons décidé de ne pas le faire ici, parce qu’on n’avait pas le temps.”
Pieter van den Boomen (Champignonnière):
“En moyenne, la temperature doit se situer autour de 17, 18 °C, avec une humidite relative de 90 a 92%”
Puissance
La nouvelle installation fournit env. 800 kW, tandis que les anciens compresseurs au fréon fournissent encre respectivement 600 kW et 350 KW. “Donc, une puissance totale de 1.750 kW”, précise Verbrugge. “Alors que la puissance requise théorique pour les 8 chambres de culture s‘élève à 1.600 kW. Maintenant, nous économisons déjà 100 kW, mais on peut encore faire mieux. Le but est aussi de remplacer à l’avenir les machines au fréon par une installation à l’ammoniaque.”
“Et une extension n’est pas un problème,” confie Frans van Laarhoven, “dans des conditions de -10/35 °C, BITZER peut fournir 3 MW de refroidissement avec nos systèmes, à l’aide de trois compresseurs. C’est naturellement nettement plus que ce qui est ici nécessaire, pour l’instant.”
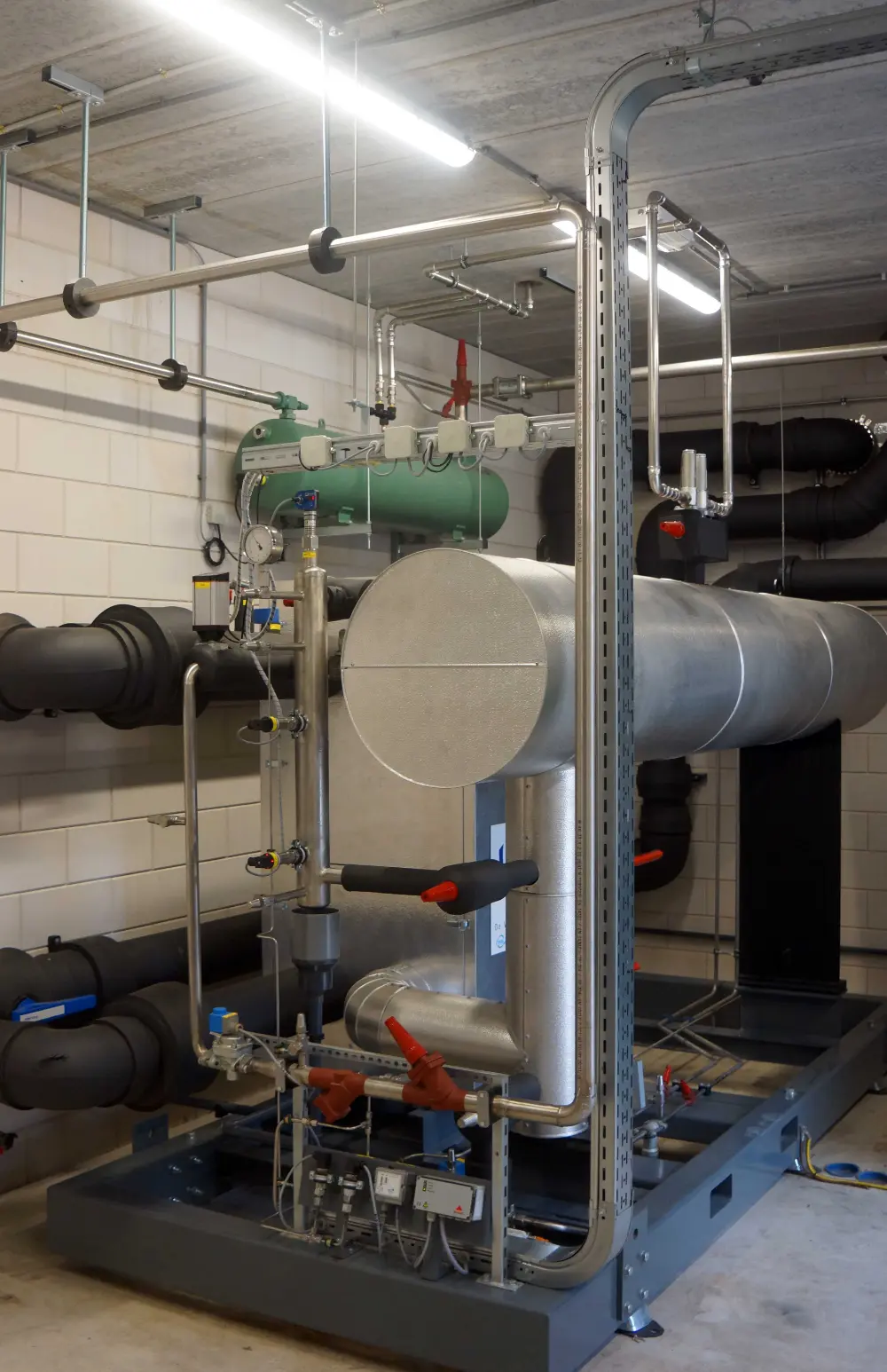
Climat précis
“Cette puissance est importante”, confirme l’éleveur et maître d’ouvrage, Pieter van den Boomen. “En raison des étés de plus en plus chauds, nous pouvions à peine y satisfaire avec l’ancienne installation. Surtout si l’humidité de l’air était élevée dehors.” Grâce à la meilleure isolation, à la plus grande puissance et aux plus grandes armoires de traitement de l’air (deux par chambre de culture), cela ne pose plus de problèmes. Par ailleurs, la précision est très importante – hormis la température, l’humidité de l’air et le taux de CO2 sont adaptés avec précision à la phase de croissance des champignons. Van den Boomen: “En moyenne la température doit se situer autour de 17, 18 °C, avec une humidité relative de 90 à 92%. Au début d’une culture,il y a une grande activité biologique dans le soI, puis nous refroidissons vers 17 °C, cela doit à nouveau augmenter pendant la croissance et redescendre vers la fin.
Nous déterminons le nombre de champignons par mètre carré surtout par la température de l’air. La vitesse de croissance est aussi déterminée par la température de l’air. Nous voulons toujours récolter le même jour, et les champignons doivent avoir atteint le bon format.”
Entrepreneuriat minutieux
Lors de la visite guidée dans le complexe industriel, on note la finition et la bonne accessibilité des installations. Pieter van den Boomen déclare à ce sujet: “Naturellement, tout est passablement neuf, mais nous faisons aussi de notre mieux pour travailler avec le plus grand soin tant pour l’environnement que pour les salariés et le produit.” C’est ainsi que la champignonnière a acquis une certaine notoriété avec le propre système de ‘recyclage valorisant’ des déchets biologiques du processus de culture. Cela est transformé dans une installation séparée en une culture améliorante, un compost sec pour l’agriculture et l’horticulture, et une chaleur durable. La chaleur est utilisée dans l’entreprise, mais aussi livrée à l’éleveur d’asperges voisin. Le système procure de solides économies, sans émission de CO2, ce qui est typique de l’exploitation soignée de cette entreprise moderne.
Champignonnière Gemert
La champignonnière a été fondée à Pelle (Brabant) en 1986 par Hans et Maria van den Boomen. L’entreprise se concentre sur la culture de champignons blancs et châtaignes pour la transformation dans l’industrie alimentaire (comme dans des pizzas et de la soupe). L’entreprise est dirigée par (le fils) Pieter van den Boomen.
Verbrugge Koeltechniek
Une entreprise familiale qui existe et est spécialisée depuis plus de 25 ans dans le montage et l’entretien d’installation en technique du froid et traitement de l’air, notamment pour l’industrie alimentaire. Bien que l’entreprise soit ancrée en région brabançonne (Boekel), elle a construit des installations jusqu’en Amérique et en Australie.
BITZER
BITZER est un spécialiste indépendant du refroidissement et de la climatisation. Dans quasi tous les pays du monde – Bitzer possède 65 établissements dans 34 pays – la société livre la technologie, les produits et les services dans le domaine du refroidissement, du traitement de l’air, du refroidissement de processus, du transport et du contrôle climatique dans les bâtiments. L’économie d’énergie et la qualité priment toujours.
ECR-Nederland
ECR est spécialisé depuis les années 50 dans la technique du froid, à savoir la construction d’unités de refroidissement industrielles au niveau national et international.