Overzicht van projecten
Het Belgisch Instituut voor Lastechniek (BIL) speelt een toonaangevende rol in de ontwikkeling van innovatieve lastechnologieën. Door middel van fundamenteel en toegepast onderzoek draagt het bij aan de verbetering van de efficiëntie, duurzaamheid en veiligheid van gelaste constructies. Als onafhankelijke onderzoeksorganisatie initieert en voert het BIL diverse projecten uit binnen het vakgebied van de lastechniek. In deze lasspecial van Metallerie krijgt u een overzicht van enkele actuele onderzoeksprojecten. Voor meer informatie over deze projecten kunt u terecht bij dr. ir. Koen Faes (koen.faes@bil-ibs.be, +32 (0)92921403)
AILEEN - Centres of Vocational Excellence (CoVe) in Aerospace & Defence for Advanced Manufacturing
Met het AILEEN-project zet Europa een ambitieus netwerk op poten om het nijpende tekort aan technische profielen in de productieprocessen van de lucht- en ruimtevaart- en defensiesectoren aan te pakken. In deze sectoren groeit de vraag naar vakmensen met expertise in high-end fabricagetechnologieën zoals lassen, solderen, additive manufacturing en inspectie.
Binnen AILEEN bundelen 18 partners uit 7 landen de krachten om een transnationaal platform van Centres of Vocational Excellence (CoVE's) op te richten. Het doel is het ontwikkelen van innovatieve methodologieën en praktische instrumenten die inspelen op de noden van zowel huidige als toekomstige professionals in geavanceerde productie, door gespecialiseerde sectorale training en kennisoverdracht binnen het beroepsonderwijs en -training (VET) te waarborgen.
Het project mikt op een brede Europese impact. Niet alleen worden de resultaten actief gedeeld, ook externe VET-aanbieders kunnen aansluiten bij het netwerk. Zo ontstaat een dynamisch ecosysteem waarin kennisdeling, sectorgerichte training en best practices centraal staan.
AILEEN is een vierjarig project dat wordt gefinancierd door het ERASMUS+ programma (projectreferentie: 101103507). Verdere info op www.aileencove.eu of via ir. Wim Verlinde (wim.verlinde@bil-ibs.be) van het Belgisch Instituut voor Lastechniek.
COAMWELD - Lassen van additief vervaardigde materialen: een cruciale stap voorwaarts
De voortdurende vooruitgang in Additive Manufacturing (AM) technologieën, zoals Wire Arc Additive Manufacturing (WAAM) en Laser Powder Bed Fusion (PBF-LB), biedt belangrijke voordelen vergeleken met traditionele productieprocessen, vooral bij het maken van grote of complexe metalen onderdelen. Voor complexe eindproducten is echter vaak een combinatie van additieve en conventionele fabricagemethoden nodig. Een cruciale uitdaging hierbij is de lasbaarheid van 3D-geprinte onderdelen, vooral wanneer deze verbonden moeten worden met traditioneel geproduceerde werkstukken. De dichtheid en microstructuur van AM-materialen vormen hierbij een aanzienlijk obstakel.
Om deze uitdaging te onderzoeken, heeft het Belgisch Instituut voor Lastechniek het COAMWELD-project uitgevoerd. Dit project was gericht op het ontwikkelen van verbindingsconcepten voor het lassen van 3D-geprinte metalen onderdelen, waarbij systematisch experimenteel onderzoek werd uitgevoerd naar de factoren die de laskwaliteit beïnvloeden. Verschillende lastechnieken - waaronder MIG/MAG, TIG, laser, plasma en friction stir lassen - werden getest om hun toepasbaarheid te beoordelen, de resulterende verbindingseigenschappen te vergelijken en om de mogelijkheden van deze verbindingsprocessen in kaart te brengen.
Het lassen van additief gefabriceerde PBF-aluminiumonderdelen
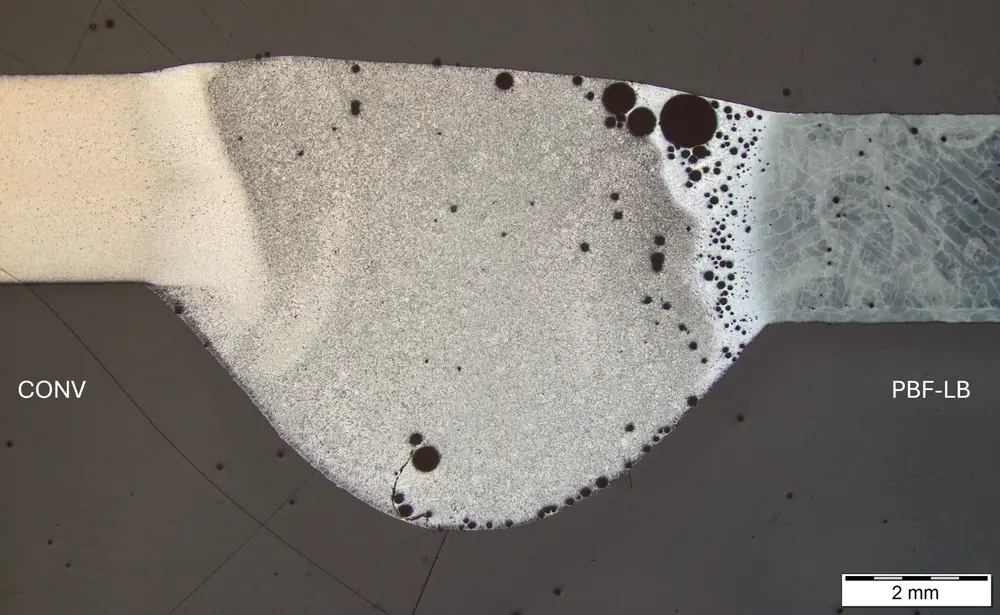
Het lassen van additief gefabriceerde PBF (Powder Bed Fusion) aluminium onderdelen met behulp van booglastechnieken brengt aanzienlijke uitdagingen met zich mee, voornamelijk door de hoge porositeit in de lassen. Deze porositeit ontstaat door waterstof die tijdens het stollingsproces wordt ingesloten, aangezien aluminium een hoge waterstofoplosbaarheid heeft in de gesmolten toestand, maar een lage in vaste toestand. Daarnaast verergert de vorming van aluminiumoxide op het oppervlak de defecten door het insluiten van oxidefilms in het smeltbad. Gerecycleerd poeder dat in PBF-processen vaak wordt gebruikt, draagt verder bij aan de problemen met de porositeiten door oppervlakte-oxidatie en verontreiniging van het poeder. Deze factoren leiden tot lassen met verminderde mechanische eigenschappen en een lage kwaliteit.
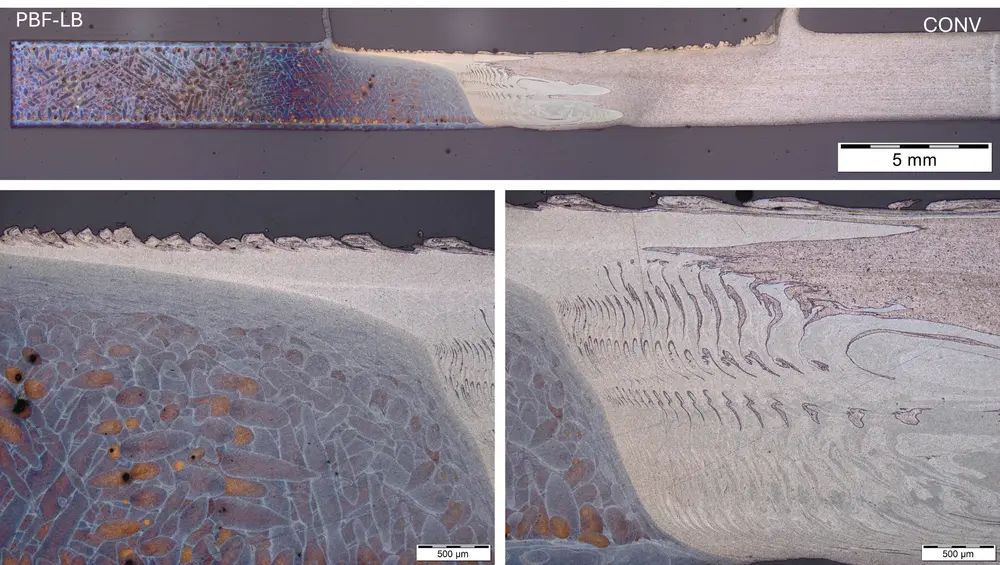
Solid-state lasprocessen bieden een duidelijk voordeel. Doordat deze processen plaatsvinden onder het smeltpunt van de legeringen, verandert het lassen de porositeitsgraad niet. De verminderde porositeit zorgt voor een sterkere verbinding tussen de materialen, wat de algehele sterkte en integriteit verbetert. FSW leverde uitstekende resultaten op voor alle materiaalcombinaties, zonder dat er onvolkomenheden in de lassen werden aangetroffen.
Uit de vergelijking tussen solid-state lasprocessen en booglasprocessen voor het verbinden van PBF additief gefabriceerde onderdelen kunnen we concluderen dat solid-state lastechnieken significante voordelen bieden. Deze processen verdienen de voorkeur voor het verbinden van PBF-gefabriceerde aluminium onderdelen, vooral wanneer structurele integriteit en consistente laskwaliteit cruciaal zijn. De microstructurele verbeteringen en afwezigheid van defecten maken deze methoden uitermate geschikt voor hoogwaardige toepassingen waar betrouwbaarheid essentieel is.
COAMWELD is een project met steun van het Agentschap Innoveren & Ondernemen (VLAIO) - Project nr. HBC.2020.2994. Meer informatie is te vinden via www.bil-ibs.be, dr. ir. Koen Faes (koen.faes@bil-ibs.be) of ing. Rafael Nunes (rafael.nunes@bil-ibs.be).
FlexWind - Verlenging van de levensduur van offshore windturbines
Het Belgisch Instituut voor Lastechniek (BIL) werkt momenteel aan een innovatief project dat de toekomst van offshore windenergie kan veranderen. In samenwerking met OCAS, Universiteit Gent, Universiteit Luik voert het BIL het FlexWind-project uit, gericht op het verlengen van de levensduur van verouderde offshore windturbinefunderingen.
Offshore windturbines en hun funderingen zijn ontworpen voor een levensduur van 20 tot 30 jaar. De huidige standaardprocedure voor levensduurverlenging is beperkt tot situaties waarbij aangetoond kan worden dat de belasting lager was dan aanvankelijk verwacht. Het FlexWind-project gaat verder en onderzoekt de mogelijkheid dat de constructies een grotere levensduur bereiken dan in de huidige normen wordt aangenomen.
Geavanceerde testmethoden
Voor het onderzoek zijn samples met twee lasprocessen geproduceerd: MAG (Metal Active Gas) en OP (onderpoederdeklassen). Deze lasverbindingen zijn uitgevoerd onder omstandigheden die vergelijkbaar zijn met die van echte offshore windturbinefunderingen, met als doel mechanische karakteristieken te verkrijgen die nauw aansluiten bij de praktijk.
Het BIL zet de laserscanningtechnologie in voor de nauwkeurige opmeting van de lasnaadgeometrie. Deze technologie levert gedetailleerde beelden voor de detectie van lasfouten, kwaliteitscontrole en een verhoogde efficiëntie bij inspecties. Geavanceerde analysesoftware converteert deze lasermetingen naar kwantitatieve data, die vervolgens gecorreleerd wordt met vermoeiingsgegevens. Deze aanpak maakt een veel nauwkeurigere voorspelling mogelijk van de structurele integriteit van offshore-constructies.
Huidige voortgang
De MAG-lassen werden onderworpen aan diverse statische testen, waaronder trekproeven, buigproeven en macroscopisch onderzoek. De volgende fase bestaat uit vermoeiingstesten op vijf verschillende belastingniveaus. Bijkomend worden twee testseries uitgevoerd op gecorrodeerde samples en twee series met een PIT behandeling (Pneumatic Impact Treatment) rond de lassen, een techniek die de vermoeiingsweerstand kan verhogen.
Dit innovatieve project wordt gesteund door de FOD Economie via het Energie Transitiefonds, en vertegenwoordigt een belangrijke stap voorwaarts in het optimaliseren van de levensduur van offshore windenergie-infrastructuur. Meer informatie via ing. Ben De Brouwer (ben.debrouwer@bil-ibs.be).
STWIN - artificiële intelligentie toegepast voor de optimalisatie van lasprocessen
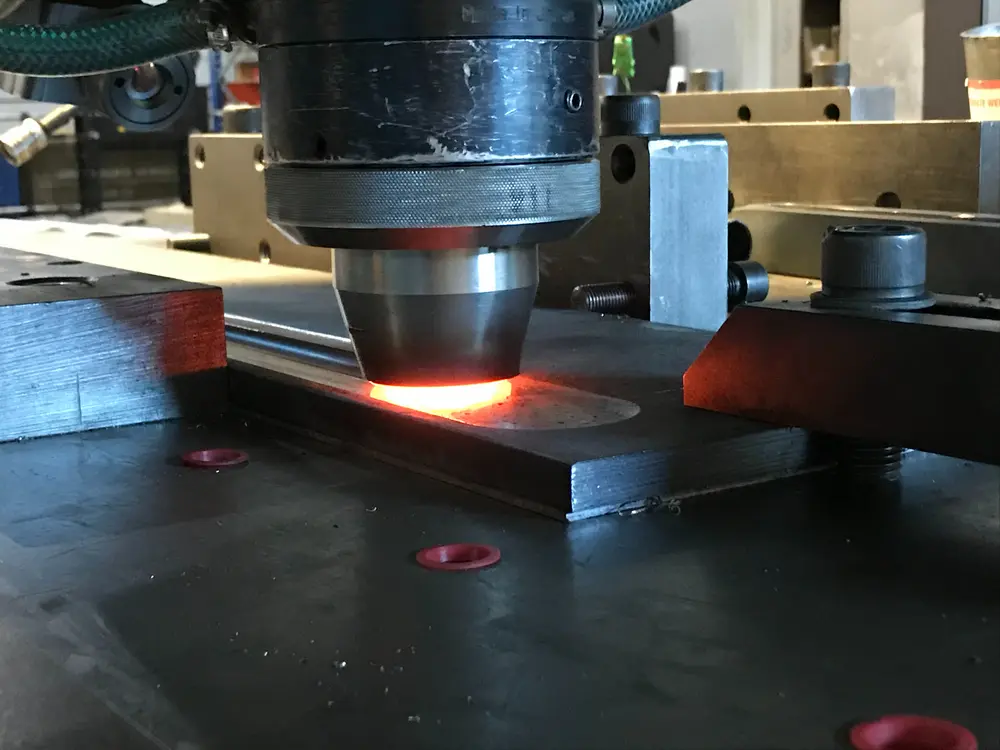
De intrede van artificiële intelligentie (AI) in verschillende industriële sectoren heeft geleid tot een ongekende transformatie, en de laswereld vormt hierop geen uitzondering. In tegenstelling tot conventionele lasmethoden waarbij het basismateriaal wordt gesmolten, maakt wrijvingsroerlassen (Friction Stir Welding of FSW) gebruik van een roterend gereedschap om wrijvingswarmte te genereren en het materiaal plastisch te vervormen, wat resulteert in een verbinding zonder het materiaal te smelten. Deze techniek vermindert aanzienlijk het risico op defecten zoals porositeit en vervorming.
Hoewel deze methode tot hoogwaardige lassen in aluminiumlegeringen leidt, kent het proces voor staal beperkingen. Het STWIN-project, gecoördineerd door CIDAUT in Spanje, onderzoekt de mogelijkheden van AI om de kwaliteit van FSW-verbindingen in staal te garanderen door ervoor te zorgen dat de procesparameters, ongeacht het type materiaal, altijd optimaal zijn. Hiervoor maakt het project gebruik van niet-destructieve inspectiemethoden zoals akoestische emissiemonitoring en thermografie.
De implementatie van machine learning in de lastechniek
De reductie van defecten in lasverbindingen is van cruciaal belang voor het waarborgen van de productiviteit en duurzaamheid in diverse sectoren. AI, met het vermogen om grote hoeveelheden gegevens te analyseren en patronen te herkennen, wordt ingezet om de precisie van lasprocessen aanzienlijk te verhogen.
De methodologie is gericht op het integreren van inline inspectiemethoden, zodat AI voorspellende analyses kan uitvoeren over de factoren die laskwaliteit beïnvloeden. Het doel van de implementatie van deze technologieën is het verminderen van materiaal- en energieverspilling, wat leidt tot een duurzamere bedrijfsvoering. Bovendien stelt de voorspellende capaciteit van AI bedrijven in staat om proactief de optimale procesparameters te bepalen, waardoor de kwaliteit van het laswerk aanzienlijk wordt verhoogd.
Vooruitgang in het wrijvingsroerlassen van staal
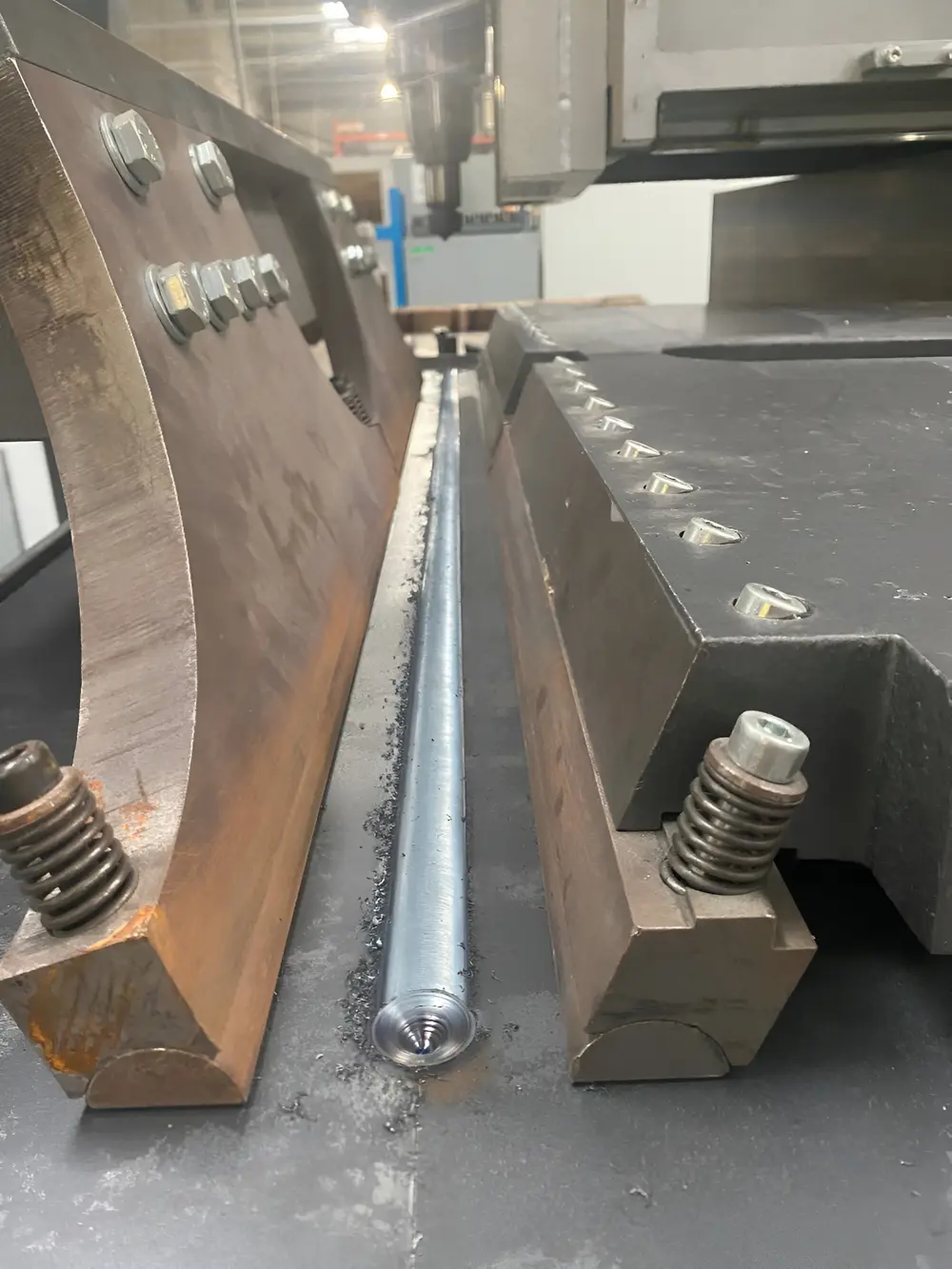
Het STWIN-project verlegt de grenzen van het wrijvingsroerlassen van staal, met bijzondere aandacht voor hoogsterkte staalsoorten (S700/S960) met diktes variërend van 6 tot 10 mm, ontwikkeling van nieuwe gereedschapsgeometrieën om verbindingseigenschappen en gereedschapslevensduur te optimaliseren, het lassen van ongelijksoortige staalverbindingen en platen met verschillende diktes en het verbinden van aluminium met staal.
Het project heeft al aanzienlijke vooruitgang geboekt bij het lassen van hoogsterkte staalsoorten. Voor S700MC-staal tonen de resultaten goede laseigenschappen, hoewel verdere optimalisatie nodig is om worteldefecten te voorkomen. Er wordt momenteel gewerkt met S960MC-staal om de laskwaliteit te optimaliseren
AI-modellen
Het STWIN-projectteam werkt aan de ontwikkeling van AI-modellen voor de automatische voorspelling van procesvariabelen die de laskwaliteit optimaliseren. De modellen transformeren ruwe data van inline inspectiemethoden in bruikbare inzichten, zoals het voorspellen van defecten en de optimalisatie van procesparameters. Op deze manier opent AI nieuwe horizonten voor het wrijvingsroerlassen in de industrie in het algemeen.
Het STWIN-project brengt een consortium van organisaties samen: CIDAUT (Spanje) voor projectcoördinatie en artificiële intelligentiemodellen; het Belgisch Instituut voor Lastechniek voor lasbaarheidsonderzoek en niet-destructieve testmethoden; STIRWELD (Frankrijk) voor de productie van lasapparatuur; ISEND (Spanje) voor expertise in eddy current testen; SSAB (Zweden) voor de levering van hoogsterkte staal; Element Six (Ierland) voor de ontwikkeling van FSW-gereed; en HIAB, HORSE en GRANALU (Zweden / Spanje) voor industriële demonstratoren.
Het onderzoek dat tot deze resultaten heeft geleid, heeft financiering ontvangen van de Programma's van het Fonds voor Onderzoek voor Kolen en Staal (RFCS) van de Europese Commissie onder subsidieovereenkomst 101112504. Meer informatie via dr. ir. Koen Faes (koen.faes@bil-ibs.be).