Veilige en efficiënte opslag van platen en profielen
Dankzij automatische magazijnen VAN KASTO
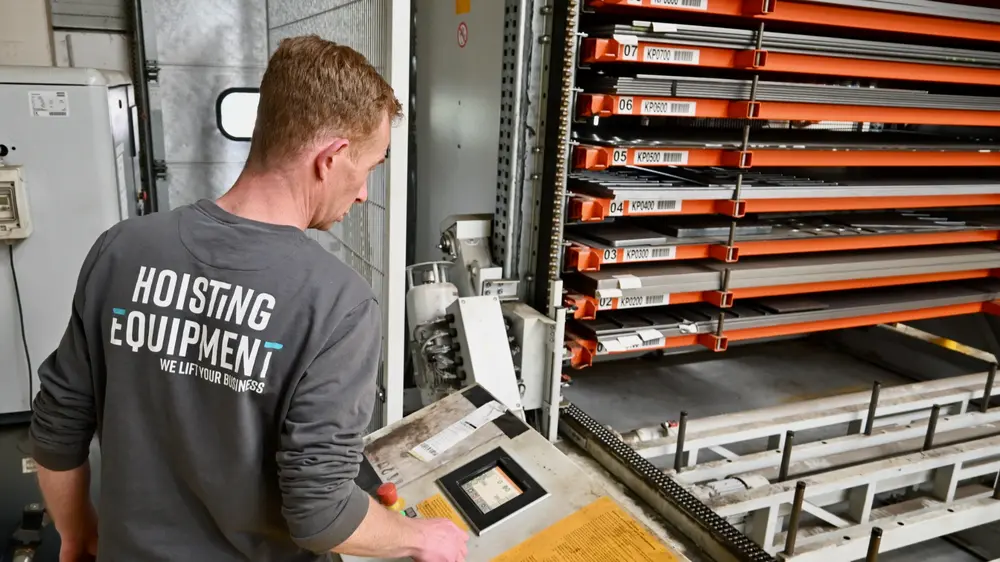
Hoisting Equipment NV uit Bornem verhandelt als hef- en hijsspecialist allerlei toestellen voor deze toepassingen, en ontwerpt en maakt ook eigen constructies. Daartoe heeft het bedrijf een grote stock aan stalen profielen, buizen en platen. Waar men die materialen voorheen vrij ongeordend en op een grote oppervlakte stapelde, bergt men die nu op in twee automatische magazijnen van Kasto. "Hierdoor kunnen we nu veiliger en efficiënter werken", stelt Dominique Leeman.
Heffen en hijsen
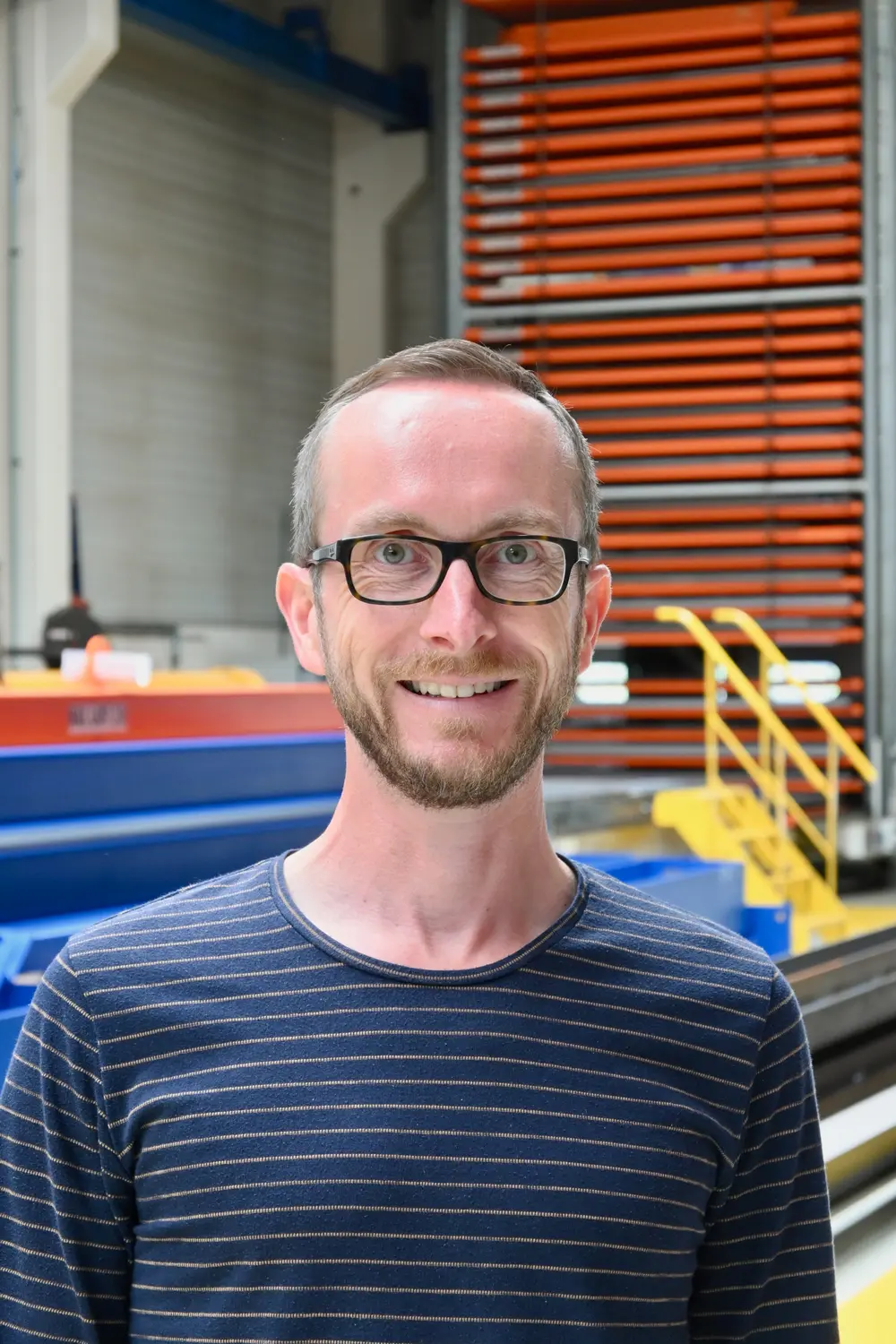
Hoisting Equipment NV uit Bornem is sinds 1976 actief op drie fronten. Vooreerst verdeelt en plaatst het bedrijf de rolbruggen, zwenkkranen, HB-systemen en takels van Abus in Vlaanderen, en verhandelt het ook allerlei hef- en hijsmateriaal via een heel dealernetwerk van gespecialiseerde vakhandels. Daarnaast ontwerpt en construeert het hijsjukken en diverse staalconstructies. Tot slot voert de onderneming ook onderhoud en herstellingen uit aan al deze producten.
"Tot tien jaar geleden borgen we de platen en profielen voor onze constructies op waar we er maar plaats voor vonden in ons atelier. Dat leidde tot onveilige situaties, er was geen overzicht waar zich welk materiaal bevond en bovendien verloren we zo veel tijd met het continu verleggen en herstapelen via heftrucks", zegt Dominique Leeman van de dienst engineering.
"Al deze bekommernissen deden ons uitkijken naar automatische magazijnen. Door hiermee meer in de hoogte te werken, konden we bovendien veel ruimte besparen."
Platen en profielen
In die zoektocht kwam het bedrijf uit bij de Duitse fabrikant Kasto, die in Nederland en Vlaanderen vertegenwoordigd wordt door Van Hoorn Machining. Voorheen had Hoisting Equipment NV al geïnvesteerd in een zaagmachine van diezelfde producent, waardoor ze reeds overtuigd waren van de Duitse kwaliteit van deze machines.
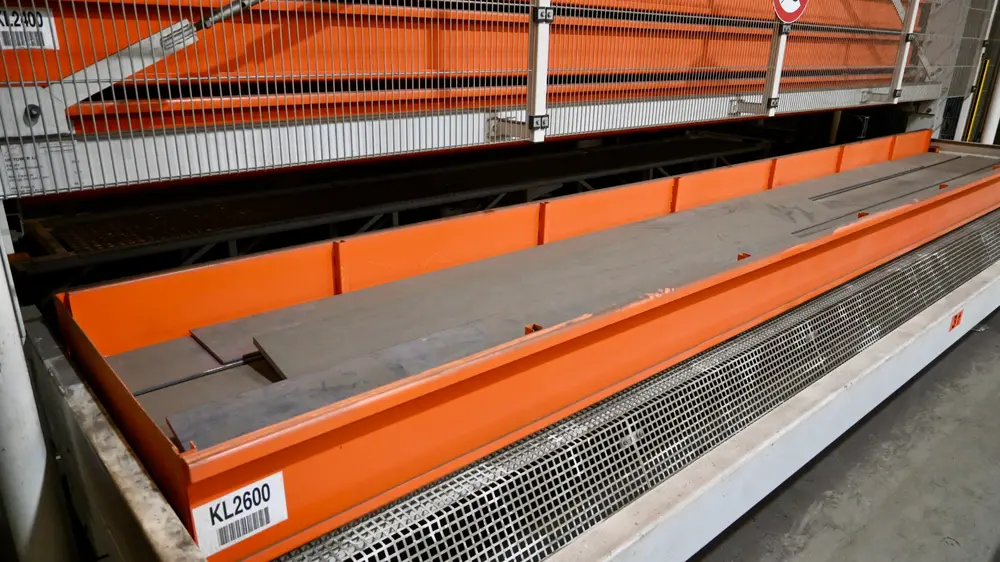
"Concreet kozen we voor de opslag van ons langgoed voor een Kasto Unitower-opslagsysteem. Die toren telt in totaal 43 cassettes van 6,2 m bij 840 mm, die elk een capaciteit van 3 ton hebben en in een dubbele rij zijn opgesteld. 36 daarvan zijn 200 mm hoog, de overige 7 cassettes meten 350 mm. Hierin bergen wij voornamelijk profielen en buizen op van S235- of S355-staal", zegt Leeman.
"Voortaan kunnen we hier veiliger, sneller en makkelijker werken"
Bij de aanbouw van een extra productiehal en de investering in een plasmasnijmachine plaatste het bedrijf hier later ook een platentoren bij uit hetzelfde Kasto Unitower-gamma. "Die is dan weer enkelvoudig opgesteld en telt 31 cassettes met onze standaardafmetingen voor platen: 3 bij 1,5 m. Ook die hebben allemaal een capaciteit van 3 ton. De twee bovenste cassettes zijn hoger, waardoor we hier andere zaken dan platen kunnen stockeren. De andere cassettes liggen vol met S355-staal", toont hij.
sERVICE NA VERKOOP
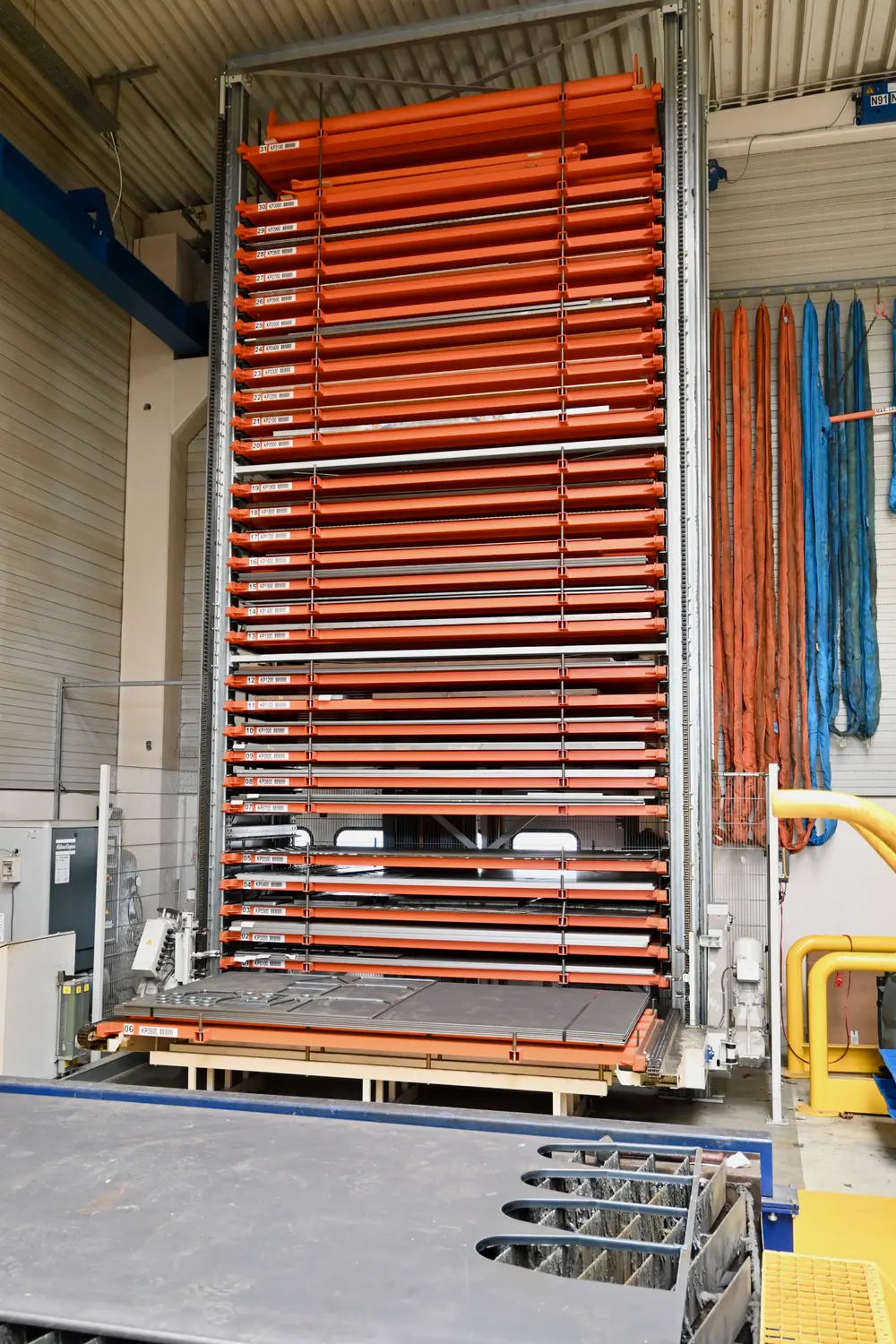
"De voordelen van deze investering zijn duidelijk: sinds de komst van de automatische magazijnen kunnen we hier veiliger, sneller en makkelijker werken, waardoor we kosten besparen", stelt Leeman.
"De Duitse makelij blijkt overigens niet alleen een troef qua kwaliteit, maar ook wat de snelle levering van wisselstukken betreft. Van Hoorn Machining heeft zelf veel wisselstukken op stock liggen en kan die anders binnen de 24 uur ter plaatse hebben voor ons. Daarbij garandeert Kasto overigens van elke machine dat de onderdelen tot 25 jaar na einde productie beschikbaar blijven."
Voor eventueel onderhoud heeft Van Hoorn Machining vier technici in dienst, die ofwel telefonisch storingen verhelpen of ter plekke komen om de machine snel weer aan de praat te krijgen. "Zware pannes hebben wij hier gelukkig nog niet gehad, maar in ieder geval zit ook de service na verkoop dus helemaal goed", aldus Leeman.
Barcodes scannen
Voorlopig hebben de profielen een vaste plaats in de toren volgens een eigen codesysteem en is er een manuele opvolging van het verbruik hiervan. "Het is evenwel de bedoeling om dit in de nabije toekomst flexibeler aan te pakken en de opslag via het scannen van barcodes te koppelen aan ons ERP-systeem. Dan is dit volledig traceerbaar en weten we dus te allen tijde wat waar ligt, en kunnen we dit snel terugvinden in het magazijn. Dit verbeterproces zijn we momenteel aan het doorvoeren en moet resulteren in een nog hogere efficiëntie", klinkt het nog.