Process Systems Engineering – A transformative revival at TU Delft
PSE driven innovation in sustainable process technology at TU Delft
Process Systems Engineering (PSE) is about making informed decisions at all levels and scales, by understanding complex (chemical) systems and interactions of their parts. The transformative revival of PSE at TU Delft PSE reflects the strong academic, industrial, and societal interest in this field.
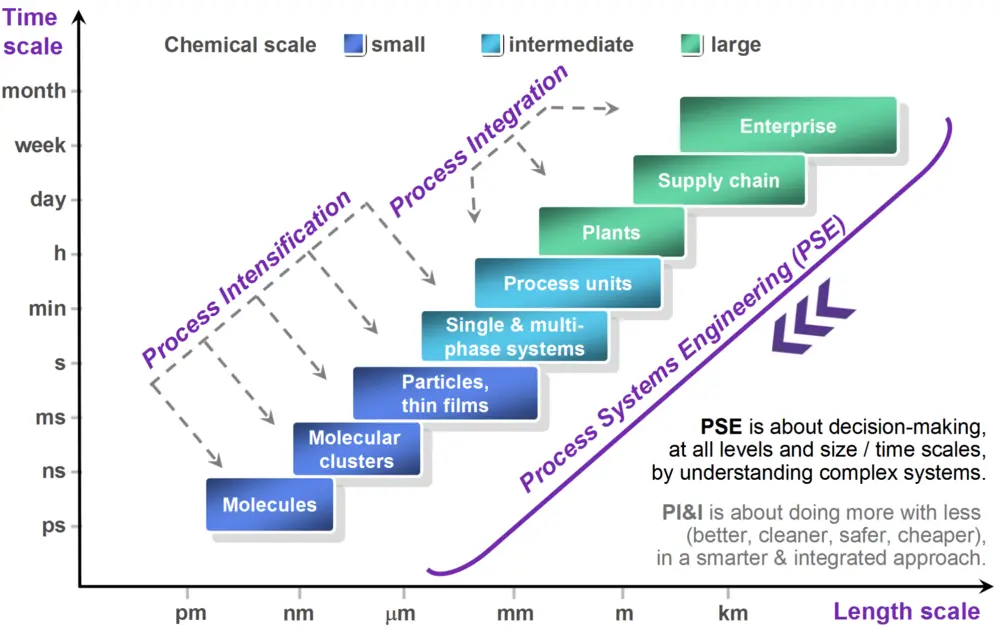
Process Systems Engineering (PSE) is vital for academia and industry, as it enhances efficiency, promotes sustainability, fosters innovation, and supports decision making at all scales (see Figure 1)1. Its interdisciplinary nature and focus on system integration is essential for addressing the complex challenges faced by industries and society. PSE helps in delivering better performance (e.g. profit, sustainability metrics) in shorter time, along all phases: RD&D, engineering, process control and optimization, operation, etc (see Figure 2)2. In this respect, PSE plays a key role in new research development as well as the education of the next generations of chemical engineers.
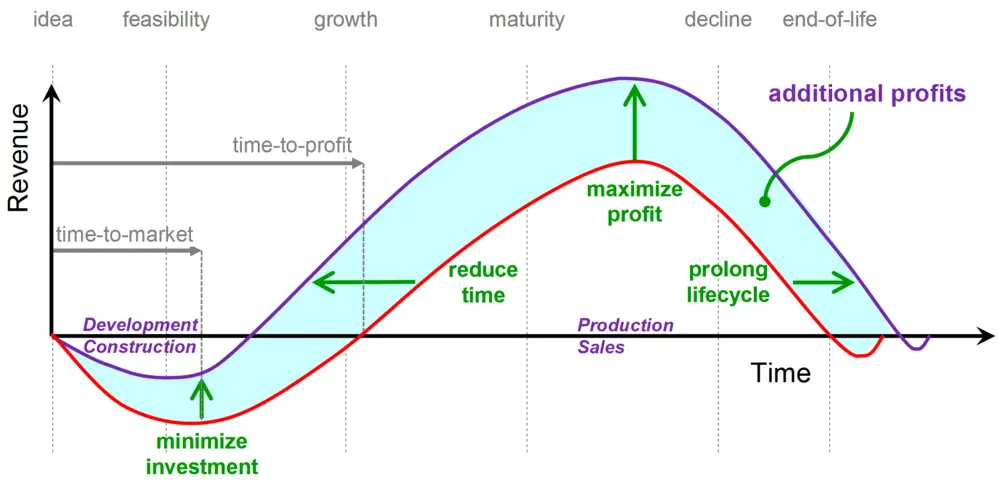
A history of PSE in Delft (NL)
PSE is an important branch on the tree of chemical engineering in the Netherlands. The roots of PSE in NL can be traced back to academic institutions and industrial R&D. The ancestors of PSE are process development, mathematical modeling & computing, control engineering and operations research (optimization). The PSE field at TU Delft developed over sixty years along three phases.
1) From process design to CAPE
Past chairs of process technology at TUD (J.C. Vlugter, P.J. van den Berg, J.A. Moulijn) considered conceptual process designs as a relevant final stage of process development. In 1968 a chair was established for process design & integration (A. G. Montfoort) to supervise all capstone process design projects. Computing manually the mass and energy balances, doing proper equipment selection and sizing, and making economic evaluations required much effort.
Distributed computing increased substantially in 1980’s, allowing the use of process flowsheeting programs (ChemCAD, Aspen, SuperPro) by students. In early 1990’s a suite of computer programs for process engineering became available, their use collectively labeled as Computer-Aided Process Engineering (CAPE). CAPE development was successively driven by C. van Leeuwen, J.C. Goebel, P.J.T Verheijen.
2) Evolution from CAPE to PSE
In 1992 TUD appointed J. Grievink (ex-Shell) as chair of Process Integration, who was responsible for courses in process modeling & simulation, process design, control & operations. A part-time chair for Process Dynamics & Control (P.J. de Jong, DSM) dealt with process dynamics & control. These two chairs were combined into a new section, called Process Systems Engineering, which was heavily involved in chemical engineering education, mainly in the MSc and EngD programs. The supervision (by C.P. Luteijn and later G. Bierman and P.L.J. Swinkels) of educational process design projects was a major activity.
The R&D focus of the PSE section was on improvements and structuring of the (conceptual) design approaches. The increasing effectiveness of process modeling, simulation and optimization gave room to more conceptual, systemic thinking for better performing processes and products. The process dynamics & control were covered (by C.S. Bildea) with attention to the various operational phases such as process start-up, shut down and mode switches. Research applications were focused on processes for liquid energy carriers (e.g. Fischer-Tropsch), on reactive distillation design, on the manufacturing of structured products with distributed properties (e.g. crystals and food products).
Long-term collaboration emerged with the P&E Lab on solution crystallization processes (G.M. van Rosmalen, H.J.M. Kramer and P.J. Jansens), as well as with the control engineering group (O. Bosgra and P. van den Hof) and the group Process & Energy Systems (M.P.C. Weijnen, P.M. Herder), all within TU Delft. The emergence of the process intensification (PI) field required a distinction between PI and PSE and an analysis on how to exploit synergies for an effective collaboration.3
3) Loss and recovery of PSE
Around the year 2000 a severe decline in the number of (chemical) engineering students started, requiring in 2006 a cost-driven downsizing by recombining chemical engineering chairs in Delft. The sections on reactor engineering, particle technology and PSE were integrated into a single new section for Product & Process Engineering (PPE), led successively by J. Grievink, M. T. Kreutzer and J. R. van Ommen.
Increasing the recruitment of international talent for the MSc, EngD and PhD programs, kept the education, research, and design activities in the chemical product & process engineering fields going. Afterwards, the situation reversed with a steady growth in the number of students, faculty members and research efforts. At the same time, the chemical process industry observed a lack in PSE skilled starters and required more graduates with strong PSE skills. This context allowed establishing a PSE section in 2024, headed by A.A. Kiss.
New horizons of PSE at TU Delft
Decades ago, the chemical manufacturing world was simpler with ample and reliable supplies of fossil resources both as a feedstock and as source of (cheap) energy. Commercial competition was on basis of manufacturing costs and the quality of products. In the academic world, the focus was almost exclusively on the development and design of active agents (e.g. catalysts, membranes, packing) for chemical processes. Academic interests went up to the design of a process for an application validation of their research, but there was little interest in actual process operation in practice, let alone in the operation of dynamic supply chains.
Understanding and control of complex physical and chemical phenomena was deemed to be more interesting than optimal use of resources in processes and supply chains, as the topic of PSE was not linked to a class of phenomena (biological, chemical, or physical) that would occur in nature. Nowadays that has largely changed, as the world moves away from fossil fuels. The industry, academia, and society focus currently on the energy transition, sustainability and circular economy4. – which are at the upper level of PSE and strongly supported by the PSE field (Figure 3)2.
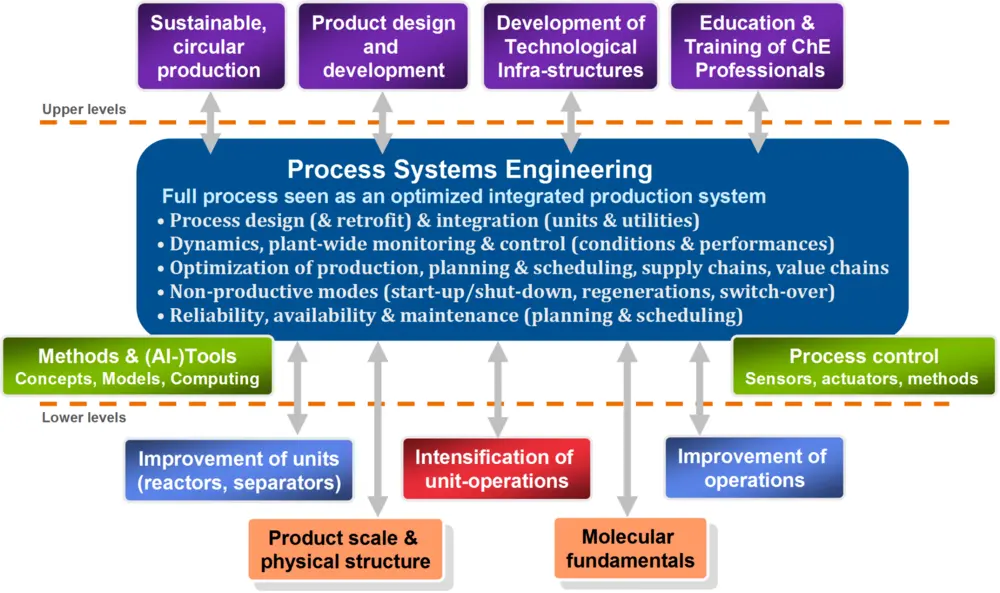
PSE is all about making educated decisions at all size and time scales, implying out-of-the-box thinking and design going from molecule to value chain, while having a sound basis in natural sciences with mathematical rigor. PSE methods and tools are used in all stages going from idea to implementation (Figure 4) and support the process scale-up in an industrial setting (Figure 5).
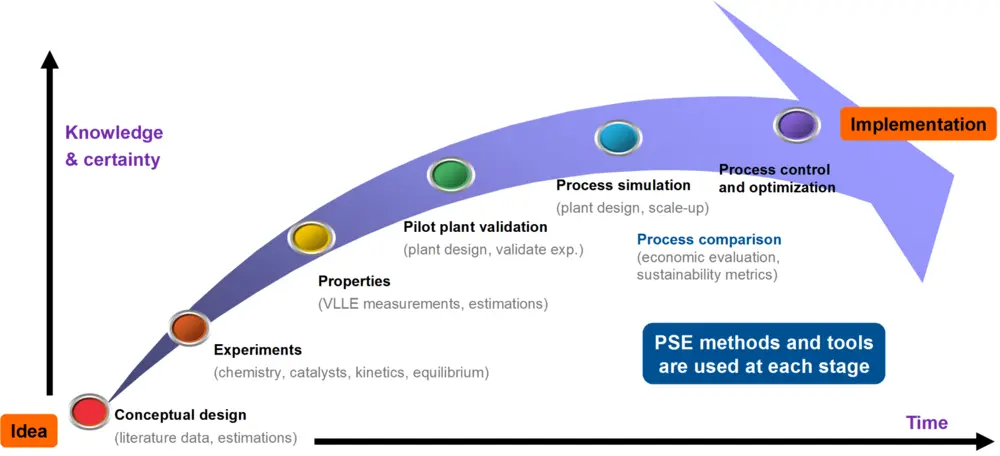
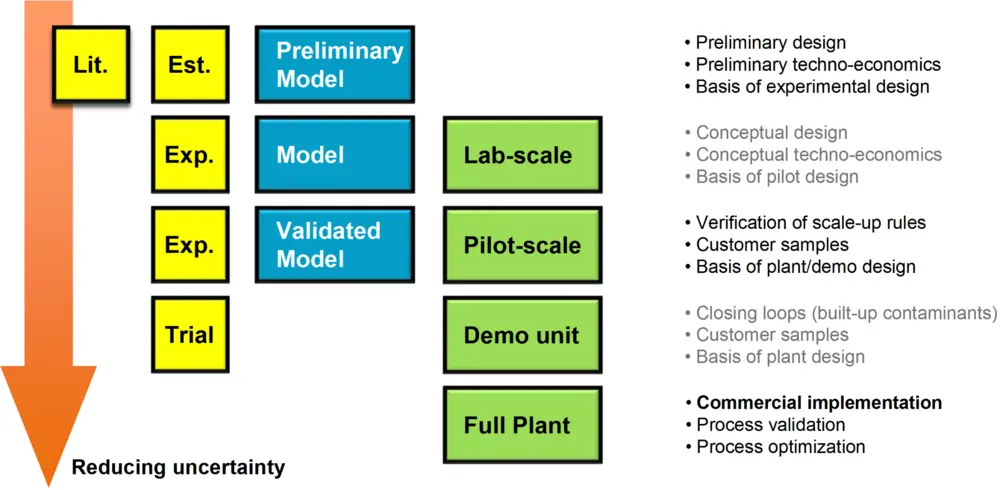
The newly created PSE section at TUD aims to create viable solutions for sustainable chemical processes that are low-carbon, energy efficient and cost effective. The PSE section consists of several principal investigators (A.A. Kiss, A. Ramírez Ramírez, A.B. de Haan, A. Schweidtmann, A. Somoza Tornos), a number of affiliated staff from other parts of TUD (P.L.J. Swinkels, F. Mousazadeh, J. Posada, J. Grievink, S. Safavi Nic, M.D.M. Pérez-Fortes), as well as over 25 PhD students and PostDocs (more details are available on: www.tudelft.nl/cheme/pse).
This professional team works on advanced computational research, with a focus on advancing the PSE field to bring new insights and sustainable developments, while contributing significantly to the field of chemical engineering and reinforcing TU Delft's position as a leader in ChemE research and education. Here is a partial list of research topics that we work on at various scales (Figure 6), linked to many opportunities for PSE (Figure 7), with applications in many areas such as bio-based chemicals / fuels, chemical recycling, carbon capture and utilisation, thermo/bio/electro-chemical conversion:5.
- PSE methods and tools expanded to new fields
- Process modeling/simulation, surrogate models
- Process synthesis, conceptual process design
- Process dynamics and plantwide control
- Process optimization and new techniques
- Global mixed integer optimization
- (Ex-ante) Techno-economic assessment
- Value chain analysis and design
- Uncertainty analysis and quantification
- Life cycle assessment (LCA), Ex-ante LCA
- Social-LCA and sustainability metrics
- Machine learning, artificial intelligence (AI)
- Molecular property prediction, product design
- Process intensification technologies
- Product and process design methodology
- Design thinking and design project execution
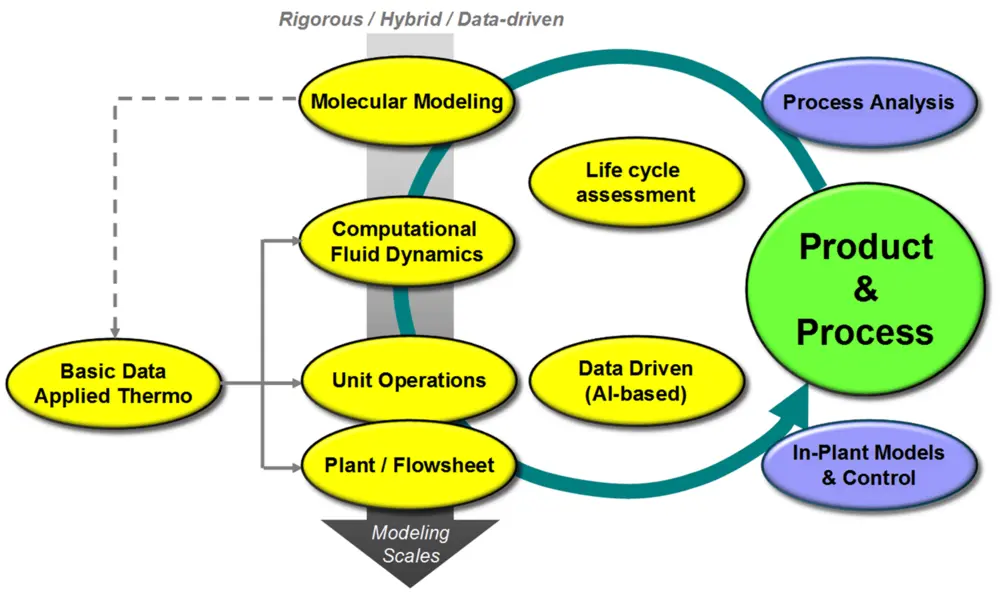
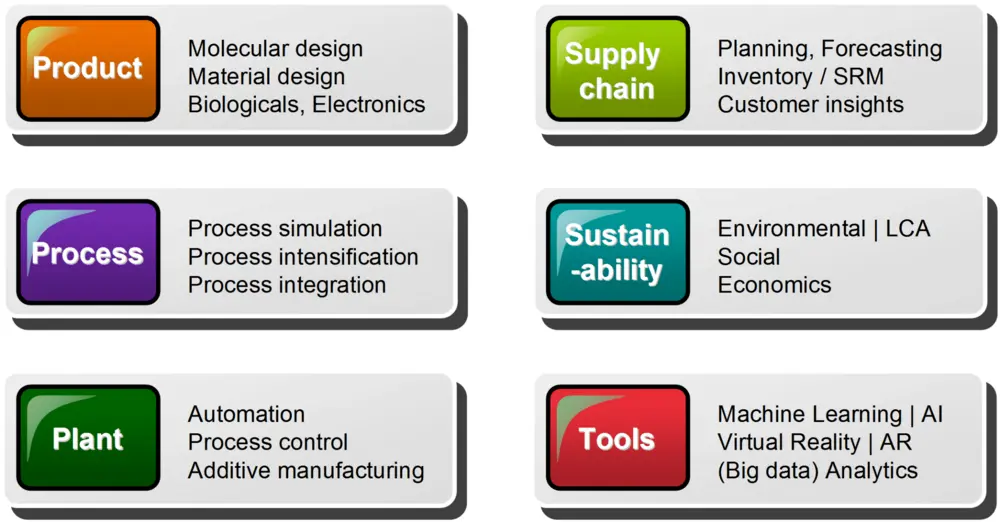
In addition to research, the PSE section strongly contributes to education at MSc and EngD levels (e.g. Conceptual Design Methodologies and Project, Process Dynamics & Control, Process Intensification, Sustainable Supply Chains, Chemical Process Technology, Artificial Intelligence in Chemical Engineering), thus ensuring a great career span for PSE professionals (Figure 8).
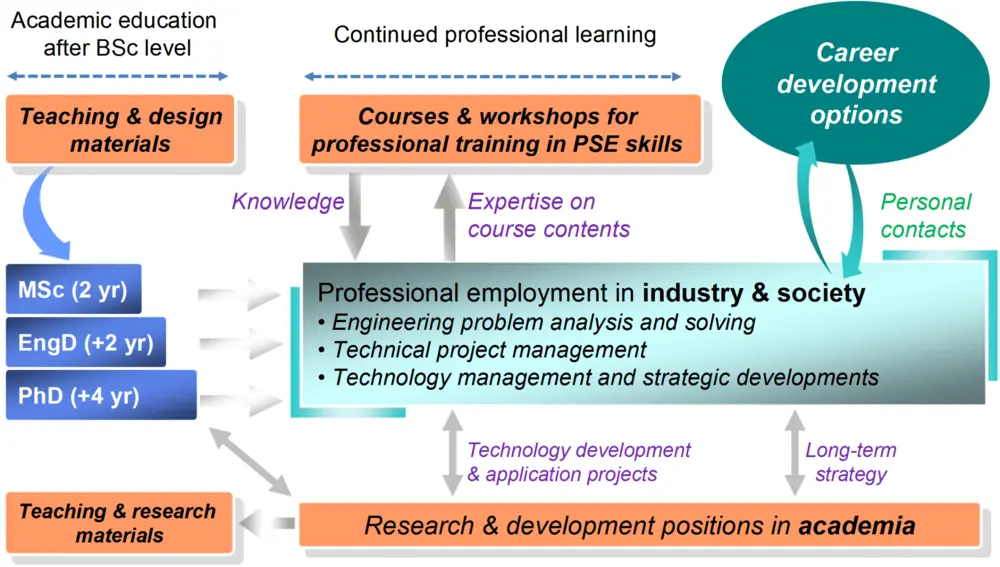
Concluding remarks
The new Process Systems Engineering (PSE) section at TU Delft (TUD) addresses the major societal challenges and opportunities related to energy transition (e.g. flexible e-production) and the transition from a linear to a circular supply chain in all industrial sectors. The development of tools and methods from PSE include multi-scale modeling (powered by AI techniques), process integration and intensification, ex-ante techno-economic and sustainability assessment.
Using a PSE approach has a large impact on the understanding, analysis, and optimization of supply and value chains, and the convergence of different disciplines towards a common vision.
At TU Delft there are several clusters of projects (e.g. energy with recent emphasis on heat, pharma engineering and food, circular water processing, advanced materials) within Pro2Tech that benefit from a strong PSE contribution at all scales. Besides research, the education of chemical engineers in the PSE domain gains from the new developments, adapting to match the new industrial and societal needs.
References
1. Kiss A. A., Grievink J., Rito-Palomares M., A systems engineering perspective on process integration in industrial biotechnology, Journal of Chemical Technology and Biotechnology, 90, 349-355, 2015.
2. Kiss A. A., Grievink J., Process Systems Engineering developments in Europe from an industrial and academic perspective, Computers & Chemical Engineering, 138, 106823, 2020.
3. Stankiewicz A.I., Moulijn J.A., Grievink J., Gorak A., Process intensification and process systems engineering: a friendly symbiosis, Computers & Chemical Engineering, 32, 3-11, 2008
4. Avraamidou S., Baratsas S. G., Tian Y., Pistikopoulos E. N., Circular Economy - A challenge and an opportunity for Process Systems Engineering, Computers & Chemical Engineering, 133, 106629, 2020.
5. Pistikopoulos E.N., Barbosa-Povoa A., Lee J.H., Misener R., Mitsos A., Reklaitis G.V., Venkatasubramanian V., You F., Gani R., Process Systems Engineering – The generation next?, Computers & Chemical Engineering, 147, 107252, 2021.