Pass-through distillation
for concurrent alcohol recovery and fermentation
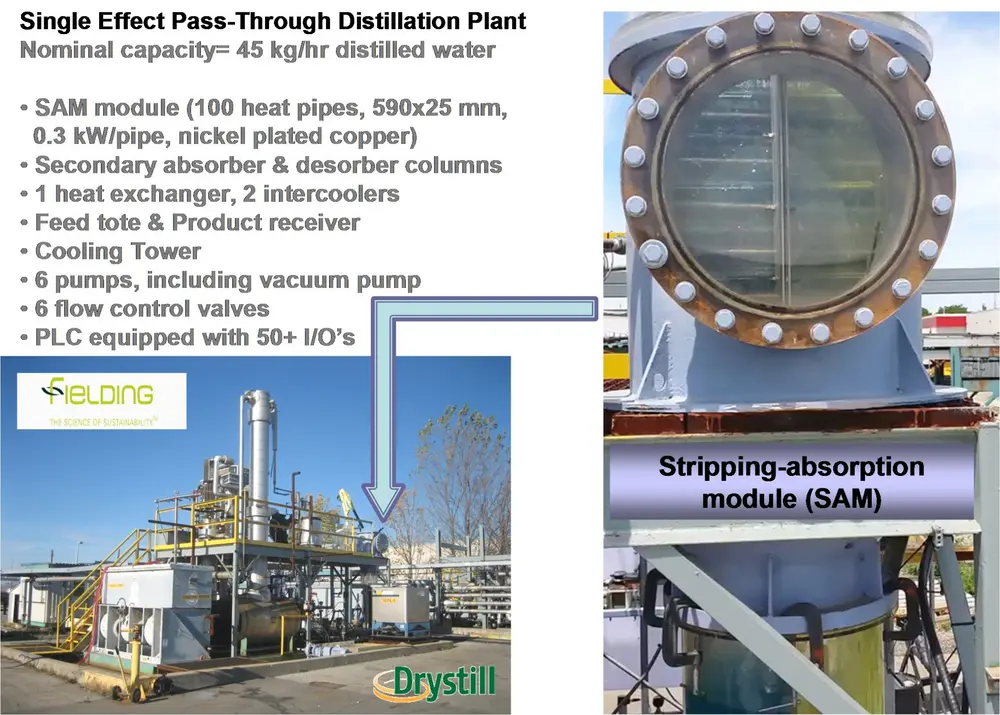
Pass-through distillation (PTD) is an emerging hybrid separation technology that can effectively address challenges associated with employing vacuum distillation in bio-based processes (where temperature limit for evaporation may require expensive refrigeration for condensation). PTD decouples the evaporation and condensation steps by inserting an absorption-desorption loop with an electrolyte absorption fluid. Consequently, these steps can be performed under different operating pressures allowing usage of cheaper utilities. Even though PTD per se is not less energy demanding compared to conventional distillation, coupling it with heat pump systems or multi-effect distillation results in significant energy savings. Process design for large-scale bioethanol recovery after fermentation using PTD showcases the applicability of this technology at an industrial level.
This is one of the most effective ways to transfer heat from the absorption to the evaporation part
Problem statement
Concurrent alcohol recovery and fermentation (CARAF) can overcome end-product toxicity, which is a major problem for bioethanol production. Vacuum distillation can be applied to continuously remove bioethanol from the broth while keeping the microorganisms viable for recycling to the fermenter. This approach in bioethanol recovery can address biomass removal issues after fermentation, such as regrowing separated wet cells, decrease in product yield relative to the substrate, loss of product with wet cells, additional washing of cells that would result in further dilution, etc.
However, in conventional vacuum distillation, the selection of the operating pressure determines both the reboiler and condenser temperatures. Consequently, the temperature limit for the evaporation might cause problems related to a very low condensation temperature and need to use expensive refrigeration instead of inexpensive cooling water.
Pass-through distillation (PTD) can effectively address the limitations of applying vacuum distillation to biobased systems by allowing evaporation and condensation steps to be performed at different pressures. It has already been proven effective on lab and pilot scale by Drystill (see Figure 1) [1], while rigorous process simulations confirm its competitiveness for a large-scale (100 ktonne/y) bioethanol plant.
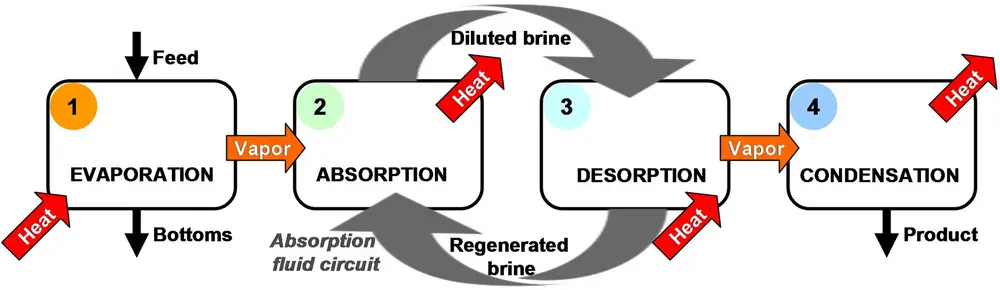
Working principle
The working principle of PTD is presented in Figure 2. Initially, the bioethanol product, with some water, is evaporated from the fermentation broth. The resulting vapor is subsequently absorbed by electrolyte absorbent fluid, commonly concentrated lithium-bromide (LiBr) brine. This exothermic absorption process releases heat that can be efficiently transferred to the evaporation part (see Figure 3) by heat pipes in an integrated process equipment unit known as a stripping-absorption module (SAM) (see Figure 4) patented by Drystill [2].
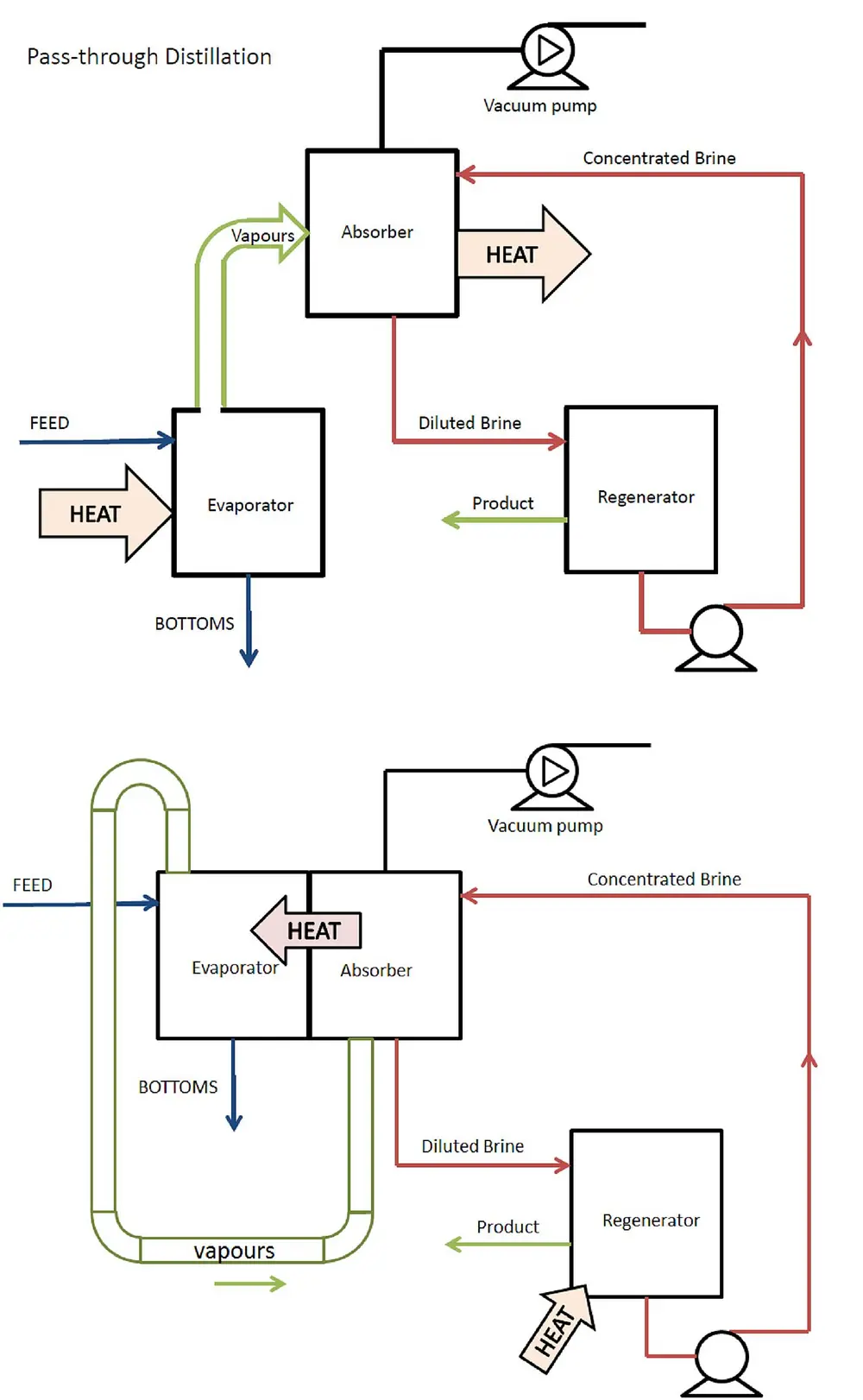
Even though PTD does not require SAM to work, this is one of the most effective ways to transfer heat from the absorption to evaporation part. The next steps are desorption and condensation of ethanol and water from dilute brine, whereby recovered concentrated brine can be reused in the absorption step.
Thus, a key advantage of the described process over conventional distillation is decoupling the evaporation and condensation steps. As a result, the evaporation (and absorption) can operate at a lower pressure and temperature that does not exceed the defined limit, while the condensation (and desorption) can operate at a higher pressure and temperature that allows using cheap cooling water.
Even though the heat needed for the initial evaporation of products from the fermentation broth can be completely provided from the absorption step, following desorption of products from dilute brine requires external heating. However, significant energy savings can be obtained by enhancing this step with heat pump systems (HP) or multi-effect distillation (MED), which are discussed in the next sections.
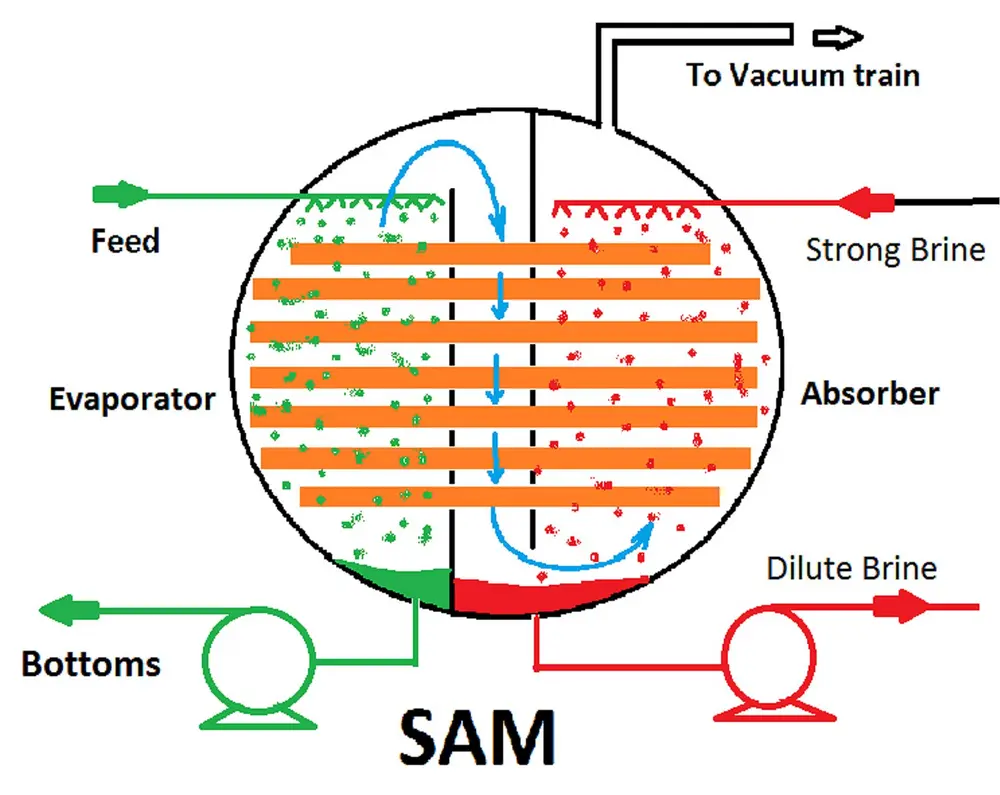
Bioethanol recovery process design
A rigorous process design for a large-scale (~100 ktonne/y) bioethanol plant using PTD was developed in Aspen Plus, as described in detail in reference [3] (see Figure 5 and Figure 6). Due to product toxicity to cells, a common fermentation broth is very dilute containing only about ~5 wt% ethanol. Additionally, some microorganisms, CO2 and non-volatile inert components are also present. The presence of living biomass limits the operating temperature for the initial separation steps. Simple flashing in a degasser unit can be applied to remove over 50% of the initially present CO2. Ethanol separated with CO2 can be recovered by absorption with water. After this initial degassing step, the fermentation broth is sent to the SAM unit, which operates under reduced pressure to allow evaporation of fermentation products from the broth while maintaining a moderate temperature appropriate for the microorganisms. The remaining broth after the evaporation contains microorganisms with most of the water and may be recycled to the fermentation to avoid loss of biomass, reduce fresh water requirements and increase fermentation yield [4].
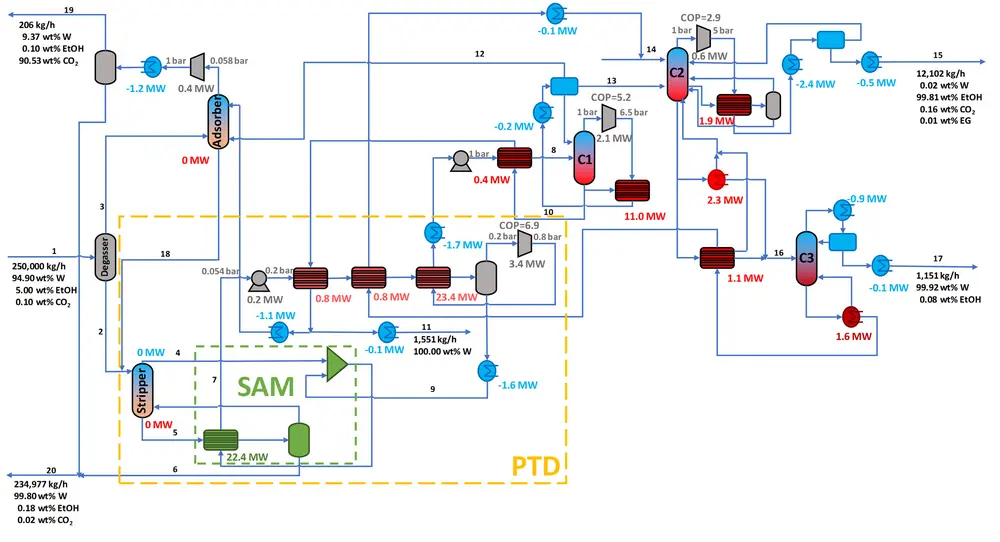
The flowrate of concentrated LiBr brine in the absorption step should provide sufficient heat release to cover heating requirements for the evaporation step. Ethanol recovery and concentration in the vapor formed after the evaporation step can be maximized by including a stripping column before the SAM unit. Furthermore, efficient recovery of absorbed ethanol and water is needed to ensure reusage of LiBr brine in the SAM unit. Since this desorption step can be very energy intensive, various energy saving opportunities can be considered.
Firstly, a heat pump system (HP) based on vapor recompression (VRC) can be used to enhance the desorption step (see Figure 5). In this design, desorbed ethanol–water vapor is compressed and used to heat the dilute brine. With the proper choice of operating pressure, the need for external heating for the desorption step can be completely avoided while allowing the following vapor condensation using cheap cooling utilities.
Alternatively, the desorption and condensation steps can be replaced with multi-effect distillation (MED) to reduce the external heating requirements (see Figure 6). This design implies splitting dilute brine in several streams of different pressures, whereby higher-pressure streams are used to provide heat to lower-pressure streams. The split ratio between streams of different pressures should be chosen to minimize total PTD energy requirements. After the PTD part of the recovery process, ethanol concentration can be increased from an initial 5 wt% to over 30 wt% with about 94% recovery.
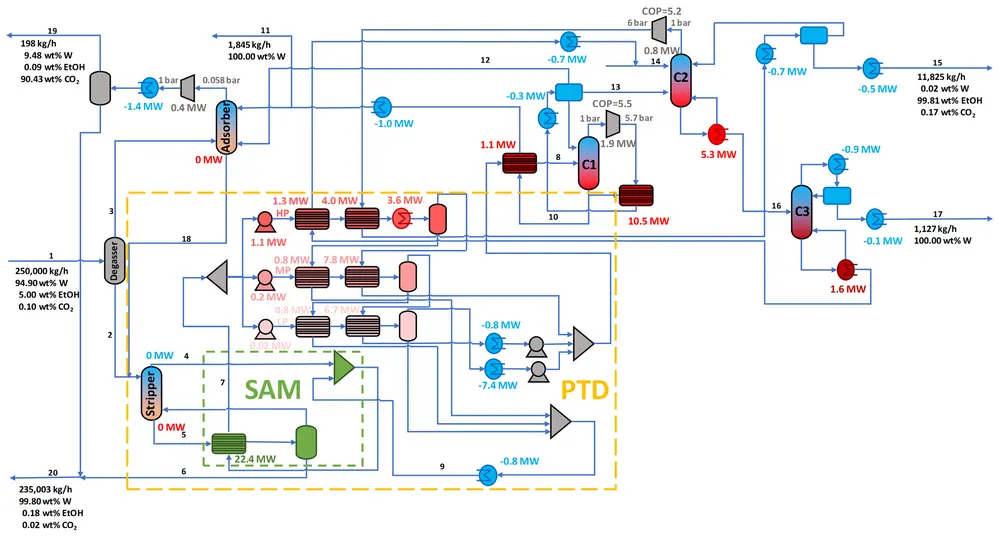
However, additional purification is needed to obtain high-purity bioethanol product. Due to the formation of ethanol–water azeotrope (95.57 wt% ethanol), several steps are required. Firstly, the recovered ethanol–water mixture after PTD should be preconcentrated to obtain 91 wt% of ethanol in the distillate since this concentration ensures minimal energy requirements for the overall recovery process [5]. The Vapor Recompression (VRC) heat pump system [6] can be implemented to the preconcentration distillation column to significantly reduce energy requirements for this step (5.6 – 6.4 times). Further treatment of the preconcentrated ethanol solution by extractive distillation with ethylene glycol is the best one for industrial scale in terms of both investment and operating costs [7].
After separating pure ethanol product (>99.8 wt%), ethylene glycol can be recovered from the mixture with water and reused. Furthermore, separated water streams can be cooled and recycled to the fermentation to further reduce water requirements. Additional heat integration opportunities (e.g. side reboiler on extractive distillation column, using recovered ethylene glycol to partially evaporate bottom liquid from extractive distillation column, etc.) should be considered to minimize total energy requirements for the overall recovery process.
PTD is a highly competitive technology that can be used in large-scale concurred alcohol recovery and fermentation
Concluding remarks
The PTD technology was proven to effectively recover more than 94% of ethanol from the fermentation broth while increasing its concentration from 5 wt% to over 30 wt% and providing full recycle of biomass. The flexibility of the PTD application was broadened by enhancing it with heat pump (vapor recompression) assisted desorber or multi-effect distillation. Following the PTD, pre-concentration and dehydration steps can be used to obtain high-purity (>99.8 wt%) bioethanol product.
Analysis of the economic and environmental impacts of this novel process proved that PTD is a highly competitive technology that can be used in large-scale concurred alcohol recovery and fermentation: 0.122 – 0.131 $/kgEtOH (with 10 years payback period) and 1.723 – 1.834 kWthh/kgEtOH (see Figure 7 and Figure 8). Additionally, besides increasing fermentation yield by removing inhibitory product from the broth, PTD enables recycling the separated microorganisms with most of the water to the fermentation process to avoid loss of biomass and reduce water requirements.
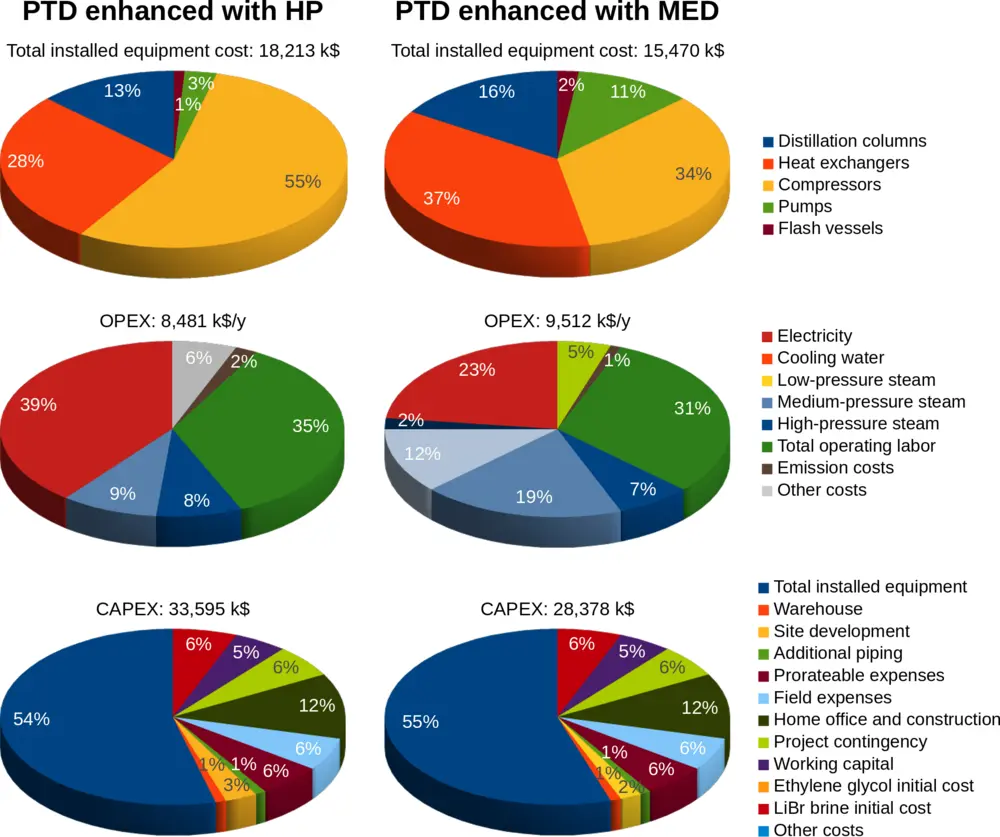
PTD technology perspectives for industrial application
As PTD has already been proven efficient on bench- and pilot-scale levels by Drystill, our original work offers insights into the application of this novel technology on an industrial level. For more details about process design please see [3].
Since PTD is proven to be highly competitive and effective, hence it should be added to the separation methods toolbox. Some of the benefits of PTD over conventional vacuum distillation are: applicability to heat-sensitive systems, avoiding the need for expensive refrigeration, reduced equipment size, etc.
Additionally, the application of PTD may be particularly advantageous in the case of more volatile products than ethanol, as it could prevent even lower condensation temperatures in the initial separation step. Further research is needed to determine alternative combinations of volatile components and absorbent fluids, especially for species that require refrigeration for condensation and thermally unstable components.
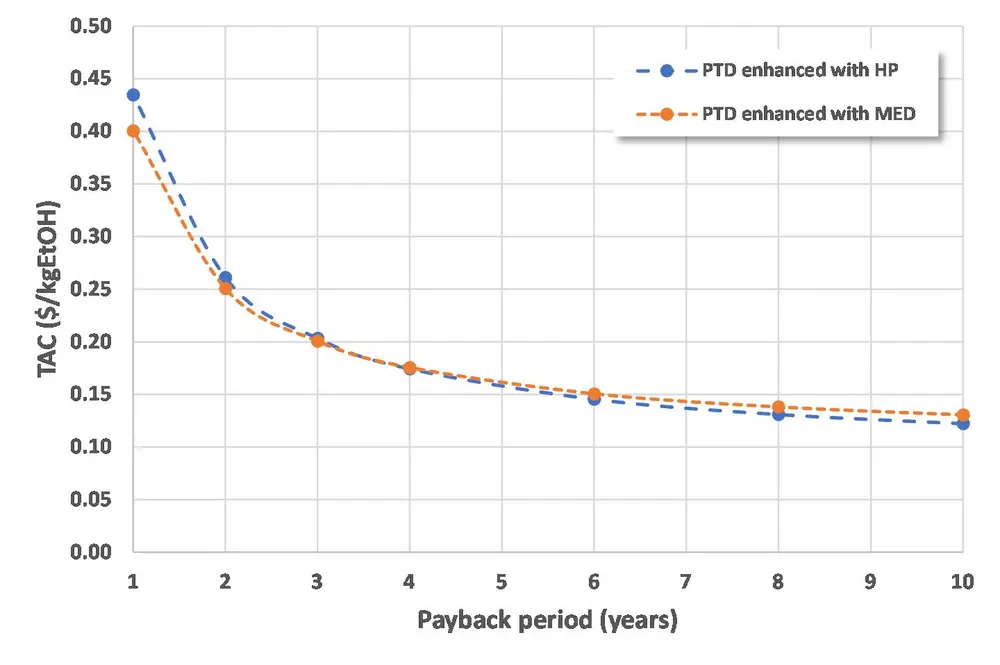
References
[1] A.A. Kiss, I.R. McGregor, S. Furlong, Pass-through distillation - A new player in separation technology, (December) (2014).
[2] I.R. McGregor, C.H. Belchers, Stripping absorption module, US 8,757,599 B2, 2014.
[3] T. Janković, A.J.J. Straathof, I.R. McGregor, A.A. Kiss, Bioethanol separation by a new pass-through distillation process, Sep. Purif. Technol. 336 (January) (2024) 126292. https://doi.org/https://doi.org/10.1016/j.seppur.2024.126292.
[4] J. Daniell, M. Köpke, S.D. Simpson, Commercial Biomass Syngas Fermentation, Energies. 5 (2012) 5372–5417. https://doi.org/10.3390/en5125372.
[5] A.A. Kiss, R.M. Ignat, Optimal Economic Design of an Extractive Distillation Process for Bioethanol Dehydration, Energy Technol. 1 (2013) 166–170. https://doi.org/10.1002/ente.201200053.
[6] A.A. Kiss, C.A. Infante Ferreira, Mechanically Driven Heat Pumps, in: Heat Pumps Chem. Process Ind., CRC Press, Boca Raton, 2016: pp. 189–251. https://doi.org/10.1201/9781315371030.
[7] P.A. Bastidas, I.D. Gil, G. Rodriguez, Comparison of the main ethanol dehydration technologies through process simulation, in: 20th Eur. Symp. Comput. Aided Process Eng. – ESCAPE20, 2010.
Corresponding author: tonykiss@gmail.com, A.A.Kiss@tudelft.nl