MACHINEVEILIGHEID IS EEN CONTINU PROCES
Risicobeoordeling is geen nattevingerwerk
Werknemers beschermen behoort in onze bedrijven terecht tot de topprioriteiten. Een correcte beoordeling van de risico's helpt om alle mogelijke gevaren van een machine in kaart te brengen. Niet alleen uw personeel geniet zo van een veiliger werkomgeving, ook uw bedrijf loopt minder risico om aansprakelijk gesteld te worden bij een ongeval.
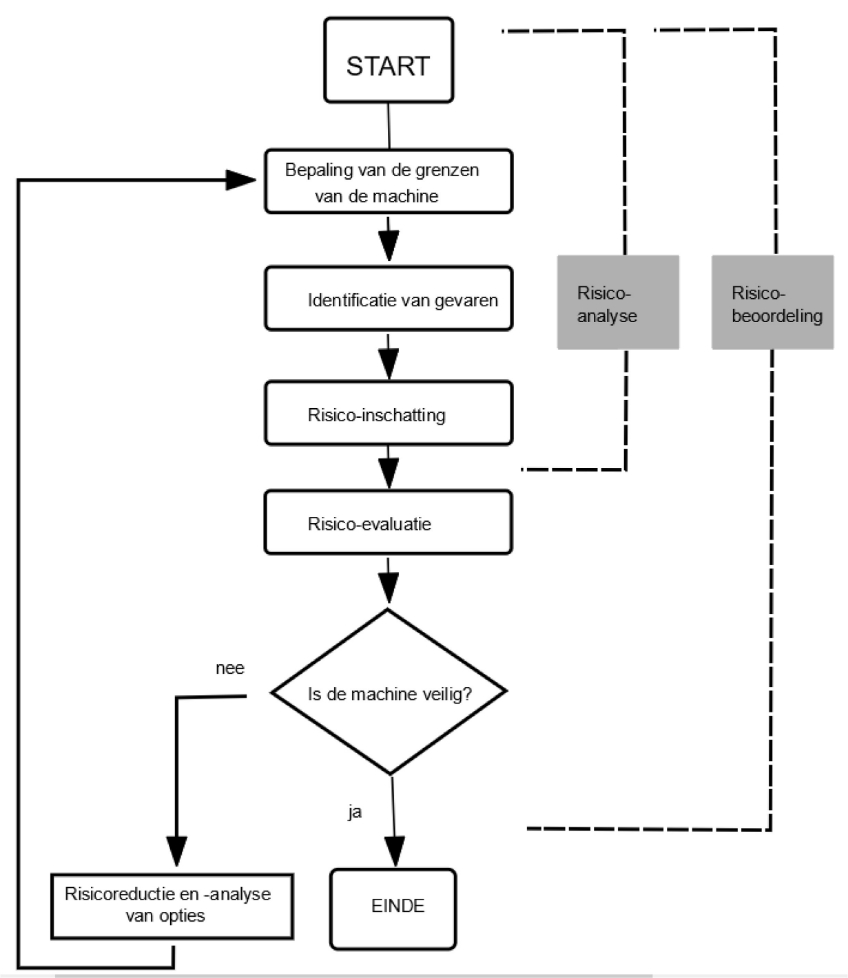
VERSCHIL RISICOANALYSE EN RISICOBEOORDELING
Alhoewel beide termen frequent door elkaar gebruikt worden, is er een wezenlijk verschil tussen beide. De risicoanalyse bestaat uit drie delen: de afbakening van de grenzen van de machine, de identificatie van de gevaren en de risico-inschatting.
Een risicobeoordeling gaat een stuk verder en bevat, naast die eerste drie stappen, ook de maatregelen om de veiligheidsrisico's weg te nemen, waarna de impact op de veiligheid wordt geherevalueerd. Een risicoanalyse stopt bij de inschatting van de risico's en is in feite een onderdeel van een risicobeoordeling. Belangrijk om te weten is dat een risicobeoordeling een continu proces is. Elke wezenlijke verandering aan de machine of haar omgeving kan een nieuwe risicobeoordeling of een update van de bestaande noodzakelijk maken.
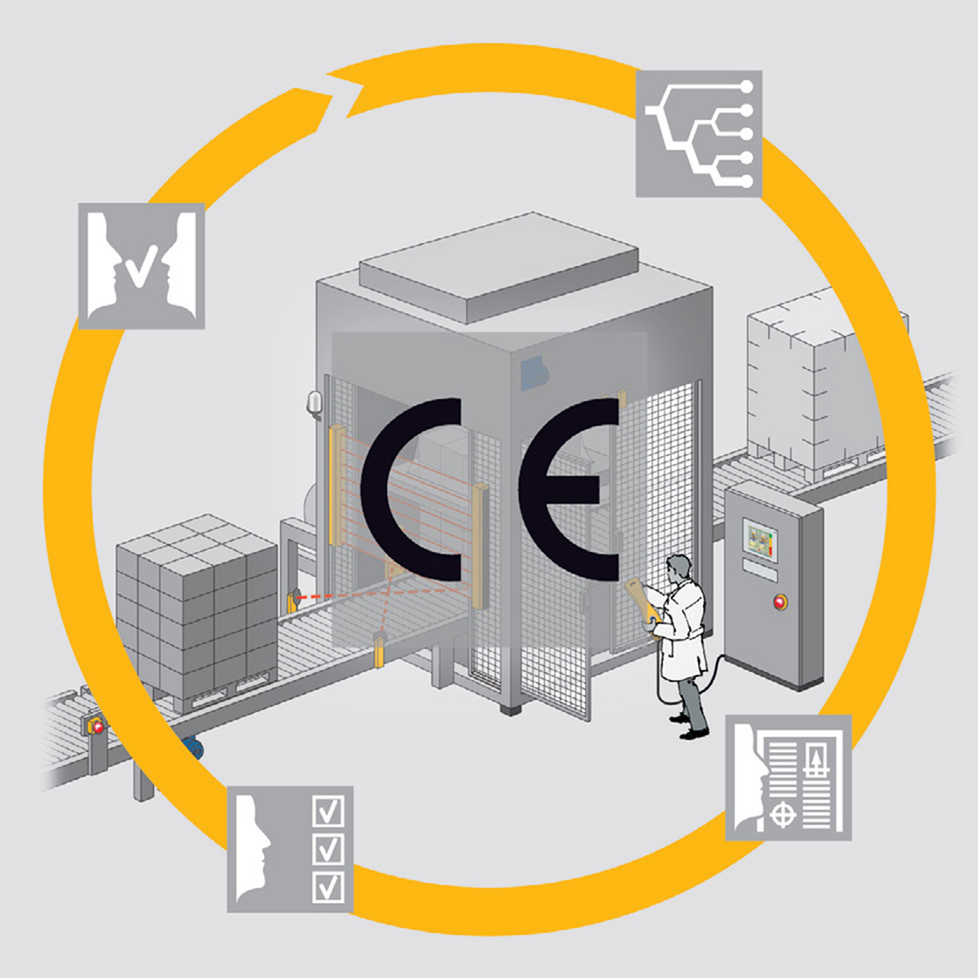
tot conformiteitsverklaring
CE-CERTIFICAAT BIEDT WEINIG GARANTIE
Bij een ongeval kan zowel de machinegebruiker als de machinebouwer aansprakelijk gesteld worden. Een eerste zaak die bekeken zal worden, is of de machine over een CE-attest beschikt. Als dat het geval is, moet de machinefabrikant ook een technisch constructiedossier hebben. De autoriteiten zullen dan bekijken in hoeverre de machine correct en veilig opgeleverd werd. Als de machinebouwer hiermee in orde is, wordt bekeken of de eindklant wel een indienststellingsverslag met bijbehorende risicobeoordeling heeft laten uitvoeren bij het in dienst nemen van de machine. In dit opzicht is de handleiding ook in vele gevallen bepalend. Een voorbeeld illustreert dat: een machinebouwer brengt een CE-gekeurde machine op de markt waarbij hij vermeldt dat de machine niet gebruikt mag worden zonder afscherming. Als de eindgebruiker dan zijn machine toch gebruikt zonder afscherming, is die persoon zelf aansprakelijk, want hij heeft de handleiding niet goed gevolgd. Hier telt de verantwoordelijkheid van de preventie-adviseur om een machine in dienst te nemen. Hij of zij moest in dit geval ervoor zorgen dat de handleiding gelezen werd. Verder is het een misvatting dat een CE‑certificaat sowieso betekent dat de machine veilig is. Wie een machine met CE‑certificaat wil afleveren, moet als een eerste stap een risicobeoordeling uitvoeren, waarna hij tien jaar lang de documenten hierover moet bijhouden. Na die periode kan hij wel nog aansprakelijk gesteld worden, maar heeft hij geen verplichting meer om aan te tonen dat er effectief een risicobeoordeling heeft plaatsgevonden. Het gebeurt wel eens dat machinebouwers het erop wagen om geen risicobeoordeling uit te voeren, maar toch het CE-plaatje aanbrengen. Zij hopen dan natuurlijk dat er tien jaar lang niks verkeerd loopt. Als eindklant is het belangrijk om zelf zo veel mogelijk veiligheidseisen te stellen aan de fabrikant. De enige verplichting van de machinebouwer naar de klant toe is het meegeven van een CE-certificaat en een handleiding. Het doorgeven van de risicobeoordeling, mechanische berekeningen en validatietesten is geen verplichting, want dat zou de eindklant zoveel info geven dat deze de machine zou kunnen nabouwen.
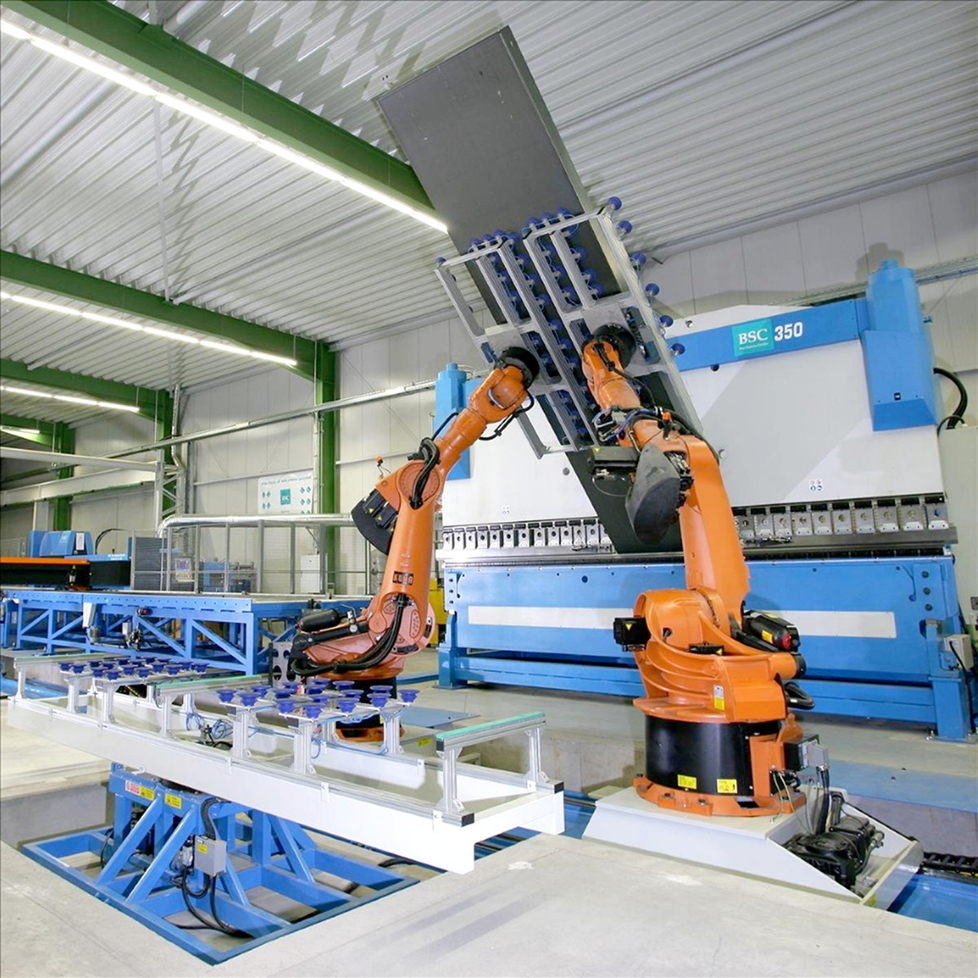
SAMENBOUW
Let wel, de opdeling tussen machinebouwer en eindklant is niet zo afgelijnd als de termen die we in de praktijk gebruiken. Een bedrijf dat twee machines aankoopt en die in één installatie samenbouwt, wordt ook beschouwd als een machinebouwer. Een voorbeeld hiervan is een robot en een CNC-machine, waarbij de robot de stukken van een transportband opneemt en in de CNC-machine brengt. Beide machines apart zouden elk perfect kunnen beantwoorden aan de veiligheidseisen, maar er rijst wel een probleem als ze samen gebruikt worden. Een noodstop op de robot resulteert niet in een reactie van de CNC-machine en vice versa, met alle risico's van dien. Als beide machines een gemeenschappelijk doel hebben én er is sprake van een gekoppeld besturingssysteem, dan worden ze beschouwd als één machine en in dat geval heeft de betrokkene dezelfde verplichtingen als een machinebouwer.
DE HIERARCHIE VAN A-, B-, C-NORMEN
Wie begint aan een veiligheidsproject, kan al snel verstrikt raken in het kluwen aan veiligheidsnormen. Voor robots is bijvoorbeeld de ISO 10218-1 in voege, maar evengoed is de basisnorm voor machineveiligheid EN 12100 van kracht voor deze machines, terwijl ook de ISO 13849 van toepassing is. De verhouding tussen deze normen is als volgt: er zijn drie niveaus; de A-, B- en C-normen. De norm voor specifieke machines (een robot, een draaibank, een pers …) is de C-norm. Wie een risicobeoordeling wil maken, start vanaf die norm (indien aanwezig). Vanuit de C-norm gaat het dan richting de B-normen. De B1-norm betreft veiligheidsvoorzieningen zoals noodstoppen (ISO 13850) en lichtschermen, de B2-normen veiligheidsaspecten zoals de PL-bepaling (ISO 13849‑1). De A-norm (de ISO 12100) geldt voor alle machines. Is er geen specifieke C-norm voor de applicatie (bijvoorbeeld mengers), dan moet men aan de A- en B‑normen voldoen.
METHODES
Een risicobeoordeling kan via meerdere methodes verlopen. Enkele voorbeelden uit de machinebouw zijn de risicograaf, een risicomatrix, de Kinney & Fine-methode en de numerieke methode.
De methodekeuze is vrij te bepalen en elke werkwijze heeft voor- en nadelen. Een voorwaarde is wel dat de gekozen methode in elk geval wel objectief moet verlopen om valabel te zijn.
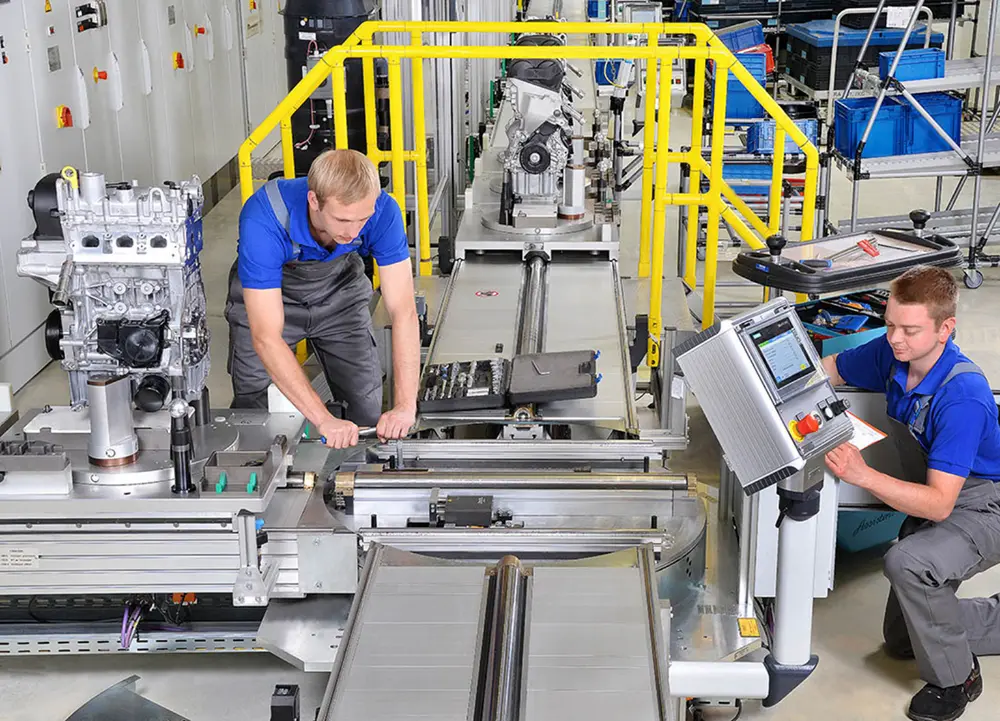
DE PRAKTIJK
Zodra de methode bepaald is, kan er van start gegaan worden met de praktijk. Als voorbeeld nemen we een numerieke methode. Er kan daarbij als volgt te werk gegaan worden:
- op basis van interviews met alle actoren die in contact komen met de machine, wordt er informatie verkregen over de risico's. De invulling van 'actoren' kan hierbij het best breed gehouden worden. Operatoren kunnen heel waardevolle informatie leveren, maar ook onderhoudsdiensten kunnen vanuit hun ervaring een eigen inbreng hebben, want zij voeren soms taken uit die operatoren niet uitvoeren. Hetzelfde geldt voor reinigingsploegen.
- Op basis van deze interviews wordt er van start gegaan met de risicobeoordeling. De machine zelf wordt eerst afgebakend (waar begint de machine precies en waar eindigt ze), het exacte doel en taken van de machine worden beschreven (wat produceert ze, hoe snel draait ze …) en de aanwezige technieken aangeduid (elektriciteit, perslucht, hydraulica …).
Naast de pure machineveiligheid moeten ook andere factoren tegen het licht gehouden worden: geluidsoverlast rond de machine, de verlichting rond de machines, aanwezigheid van heftrucks, de netheid van de omgeving, de ergonomie en het onderhoud. Ook die risico's moeten voorwerp uitmaken van de risicobeoordeling.
Vervolgens worden alle risico's ingeschat volgens de gekozen analysemethode. Bij de numerieke methode zal elk risico een quotering krijgen op basis van een aantal factoren. Vervolgens zullen er maatregelen voorgesteld worden om de situatie veiliger te maken en krijgt de gebruiker een indruk van de impact op de quotering (in het voorbeeld van een numerieke methode). Zo kan er ook een prioriteitenlijst geformuleerd worden met alle risico's, de betrokken veiligheidsnorm en de te nemen maatregelen.
Als de risicoreducerende maatregelen vastliggen, kan er dan een inschatting gebeuren naar de kostprijs toe. Het is dan aan de eindgebruiker om te beslissen welke maatregelen hij eerst wil invoeren.
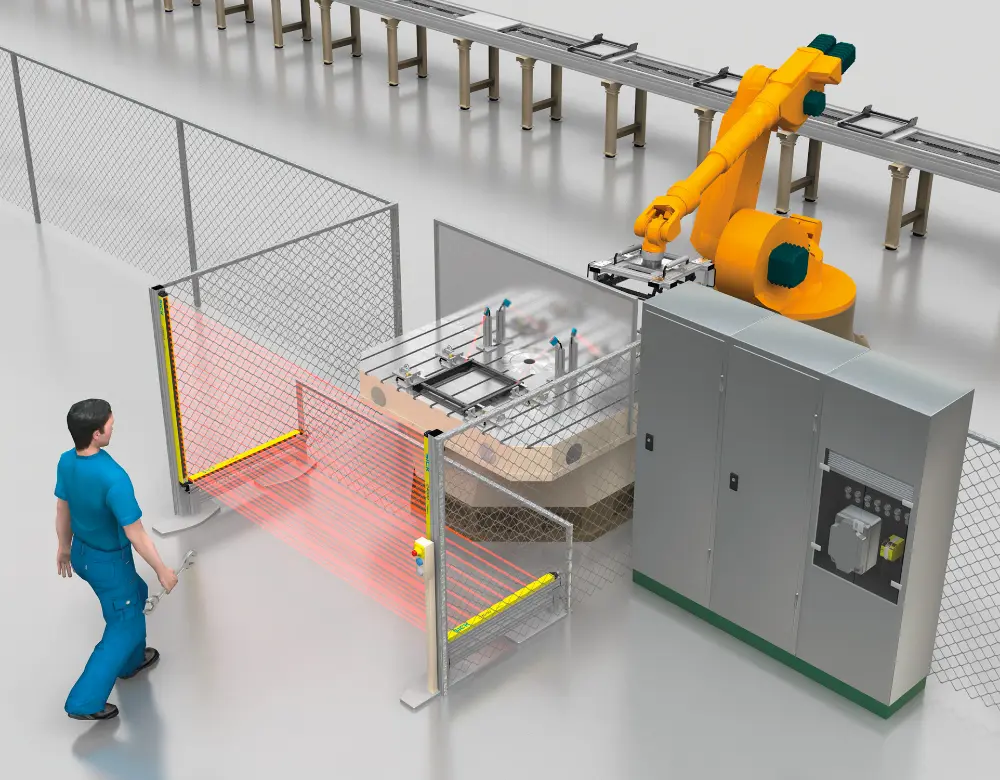
FREQUENT GEMAAKTE FOUTEN
Een risicobeoordeling uitvoeren vereist een inzicht in de machines en veiligheidstechnieken. Een onderschatting van de veiligheidsrisico's, in combinatie met te weinig technische kennis van veiligheidsinrichtingen, leidt in vele gevallen tot fouten in de beoordeling. Een prima voorbeeld daarvan situeert zich in de omgeving van veiligheidslichtschermen. Het testen van zo'n installatie is minder voor de hand liggend dan velen denken. Het volstaat niet om gewoon even met de hand de infraroodstralen van het lichtscherm te onderbreken om te testen of de machine stilvalt. Zo kan het risico immers onderschat worden.
Er bestaan meerdere types van lichtschermen, gaande van type 2 tot 4. Elk kan een verschillend Performance Level (PL) halen. Bovendien bestaat ook nog het onderscheid tussen lichaams-, hand- en vingerbeschermende installaties. Voor het beschermen van vingers en handen gebruikt men veiligheidslichtgordijnen, waarbij de infraroodstralen dichter opeenzitten om te voorkomen dat die lichaamsdelen ongedetecteerd door het detectieveld kunnen reiken. Ook moet de uitschakeling van de machine verlopen volgens de regels. Een ander voorbeeld is dat men een hekwerk plaatst, maar de deur gewoon openlaat zonder een deursensor te plaatsen. Operatoren kunnen zo ongehinderd binnenwandelen. Een ander mogelijk probleem is dat men te weinig achtergrondkennis heeft over cilinders, bijvoorbeeld dat men niet weet dat ze bij het ontluchten kunnen vallen. Er bestaan nog tal van andere specifieke voorbeelden, maar alle zijn uiteindelijk terug te brengen tot een gebrek aan inzicht in de werking van veiligheidsinrichtingen.
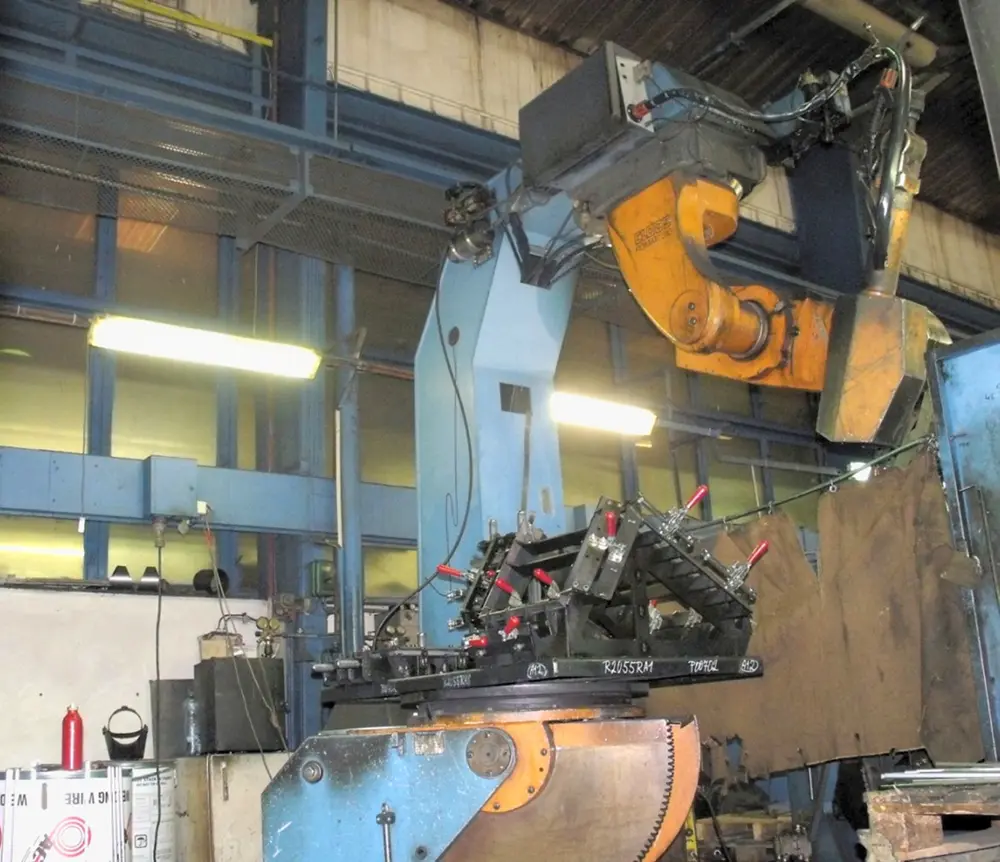
in regel niet nodig om daarvoor een CE-certificering te voorzien
IN WELKE GEVALLEN MOETEN OUDERE MACHINES CE-GECERTIFICEERD WORDEN?
Als we het hebben over oude machines is 1995 het breukjaar. Toen trad de CE-certificering in voege. Zolang er niks gewijzigd wordt aan de machine, is het in de regel niet nodig om daarvoor een CE-certificering te voorzien. Wanneer moet dat wel?
Er wordt een extra risico gecreëerd
Beschouw de robot op de afbeelding. Stel dat de stukken manueel aangevoerd worden maar dat men dit wijzigt naar een stootcilinder die het stuk in de machine brengt. In dat geval wordt een risico bijgecreëerd en is wel degelijk een CE‑certificering nodig.
Een bestaand risico verergert
Als men de snelheid van de machine vergroot van pakweg 10 m/minuut naar 15 m/minuut en operatoren daardoor minder tijd hebben om hun hand terug te trekken uit een gevaarlijke zone, creëert men een bijkomend risico. Ook in dat dient een CE-markering te worden aangebracht.
Het is echter niet zo dat een snelheidsverhoging an sich synoniem is voor een risicovergroting. Er moet echt sprake zijn van een groter gevaar. Bij machines gebouwd na 1995 moet de bestaande CE aangepast worden aan de nieuwe situatie als er een risico gecreëerd of verhoogd worden, waarbij de wijzigingen in de veiligheidsinrichtingen (een bijgeplaatste sensor, een wijziging in plc programma,…) goed moeten gedocumenteerd worden. Voor alle machines geldt bovendien ook dat vernieuwingen volgens de huidige stand van de technologie en normering moeten verlopen. Bijvoorbeeld: bij een machine gebouwd in 2000, een tijdperk waarin de Performance Level nog niet van toepassing was, moet vandaag bij het vervangen van een sensor gebruik gemaakt worden van een uitvoering die wel voldoet aan de vereiste PL.