MES-systemen moeten tot efficiënter machinegebruik leiden
Realtime productieaansturing en -optimalisatie dankzij data
Industrie 4.0 draait onder meer om de koppeling en communicatie tussen machines en diverse andere softwaresystemen in de onderneming. Manufacturing Execution Systems (MES) spelen hierin een belangrijke rol, omdat ze de verbinding vormen tussen de harde realiteit van machines en de administratieve kant van een bedrijf. Zo kan procesoptimalisatie gebeuren op basis van realistische gegevens en wordt de productie realtime aangestuurd vanuit het ERP-systeem.

Traceerbaarheid in de maakindustrie
Enkele jaren geleden waren MES-systemen enkel voor grote bedrijven. Hetzelfde kan eigenlijk gezegd worden van een ERP-pakket. Aanvankelijk zag je deze systemen vooral in sectoren die met een hoge mate van traceerbaarheid te maken hebben, zoals de lucht- en ruimtevaartindustrie, de levensmiddelenindustrie en de farmaceutische sector.
De laatste jaren hebben MES-systemen echter ook hun weg gevonden naar de maakindustrie. Zowel ERP- als MES-systemen hebben een democratiseringsslag gemaakt en zijn nu ook voor de kmo’s in de maakindustrie beschikbaar.
Deze trend is aan de ene kant gedreven door wet- en regelgeving die om meer traceability vraagt en anderzijds door de ontwikkelingen aan de softwarekant. Low-code programmering, meer universele interfaces om data uit te wisselen en machine learning-technieken jagen deze versnelling aan. Dat trekt ook nieuwe spelers naar de MES-markt, spelers die soms al actief zijn op de productievloer, maar daarover later meer.
De verwachting is dat strengere milieuregels, onder andere rond CO2-emissies, deze groei verder zullen versterken als OEM’s van de supply chain meer details gaan vragen over de CO2-emissie van de productie van componenten.
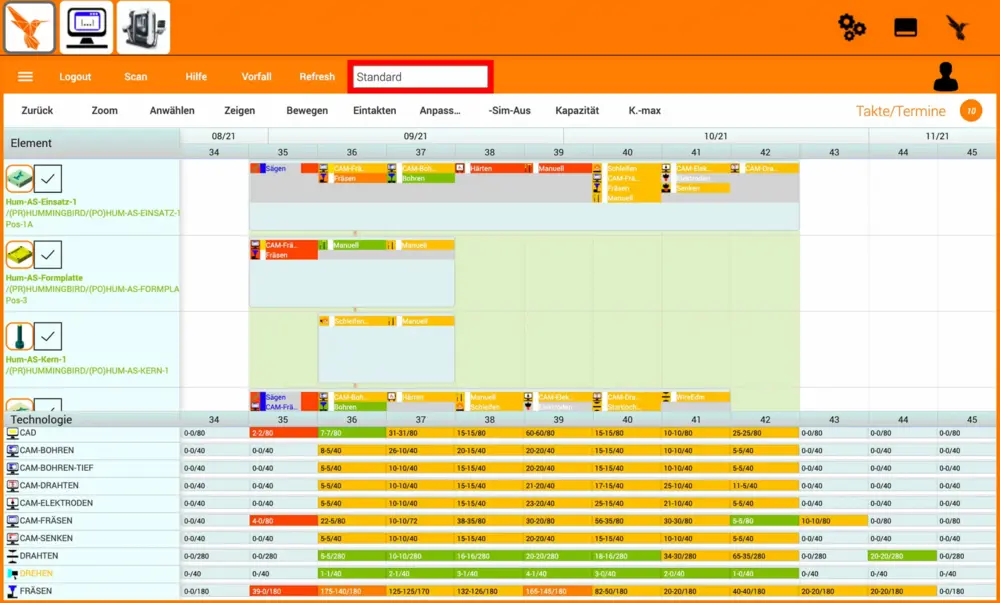
MES-systeem als tussenlaag
In de al meer dan 25 jaar oude ISA-95-norm wordt een MES-systeem gedefinieerd als 'een systeem om de productie te beheren'. Het zit daarmee tussen het ERP-systeem (planning en logistiek, niveau 4) en de procesbesturing (de lagere niveaus) in.
In het ERP-systeem liggen data vast zoals de orders van klanten, offertes, levertijden, beschikbaarheid van materialen en gereedschappen ... Het MES-systeem laadt deze gegevens in en gaat aan de slag om de productieplanning te maken én – nog belangrijker – blijft de productie monitoren en koppelt deze data terug naar het ERP-systeem. Zo krijgt men realtime-inzicht in hoe de realisatie van de productie zich verhoudt tot de afgesproken leverdata.
Op die manier kan men vroegtijdig knelpunten signaleren, bijvoorbeeld door onverwachte machinestilstand of het ontbreken van gereedschappen, en dan gepast actie ondernemen. Deze actie kan inhouden dat men automatisch gereedschappen of materialen gaat bestellen, de productie verplaatst naar andere machines of dat men met klanten al in een vroeg stadium aan de slag gaat om planningen bij te stellen.
Industrie 4.0 leidt tot decentralisatie; kennis in de vorm van digitale oplossingen is op een lager niveau beschikbaar. MES-systemen zijn een 'enabler' voor decentrale productie
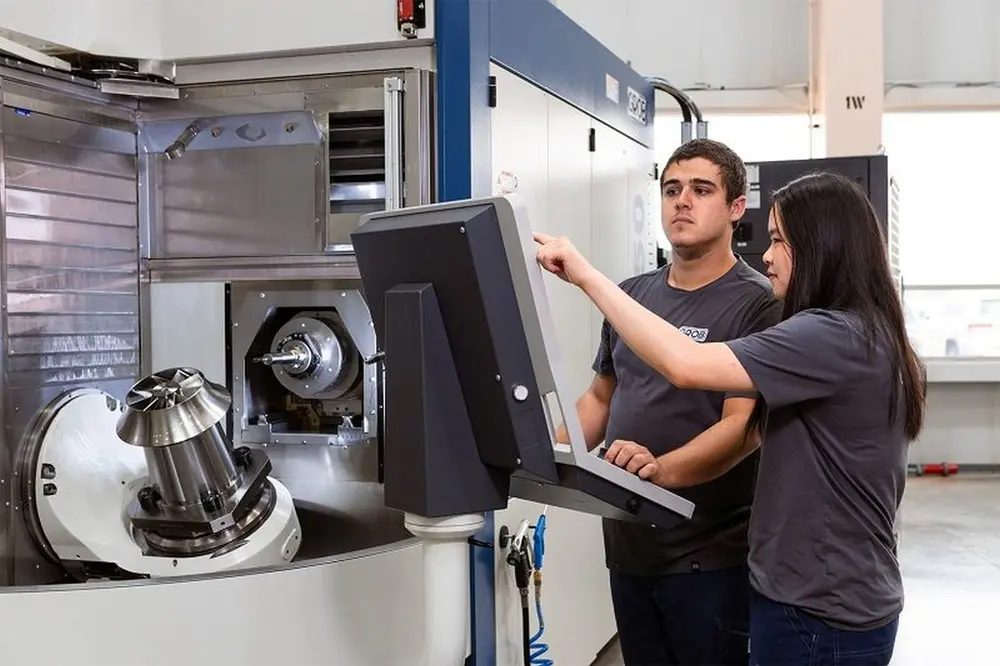
Via modules kan men inzicht krijgen in hoe het machinepark draait. Het systeem kan gereedschapsdata automatisch overdragen van voorinstelsystemen naar CNC-machines en vice versa, maar het kan ook de koppeling maken naar het ERP-systeem.
Inmiddels zijn er ook modules om data te analyseren met behulp van Machine Learning. Zo registreren sensoren in de spindel automatisch trillingen en temperatuurschommelingen en gaan na of de data correleren met de gemeten nauwkeurigheden.
Het systeem geeft dan aan of, en hoe, het proces kan verbeteren
Belang van interfaces
Dat MES-systemen pas in een later stadium tot ontwikkeling zijn gekomen dan ERP-systemen heeft een duidelijke reden: slimme fabrieken staan of vallen met data uit de machines. Dat kan informatie zijn die direct uit de machinebesturing wordt uitgelezen; het kunnen ook gegevens zijn van zogenaamde IIoT-sensoren (Industrial Internet of Things).
Een MES-systeem wordt gevoed met enerzijds data uit het ERP- (of PLM-)systeem, en anderzijds met data uit de productie. Dit laatste heeft lange tijd een doorbraak van MES-systemen richting de maakindustrie in de weg gestaan. Pas met de komst van nieuwe interfaces, zoals de Amerikaanse MTConnect en van recentere data de Duitse/Europese umati, wordt het gemakkelijker om data uit de hardware te halen en te gebruiken. Deze stap was nodig om MES-systemen beter toepasbaar te maken in kmo’s.
Bij een simpele toepassing worden deze data teruggekoppeld naar het ERP-systeem en gebruikt om de productie bij te sturen. Dergelijke informatie biedt echter ook inzicht in het effectieve gebruik van de machines. Het MES-systeem verzamelt de gegevens over of de spindel van een 5-assig bewerkingscentrum draait of niet, registreert de tijd die een CNC-operator bezig is met het instellen van de machine voor een nieuwe job en registreert machinestoringen. Al deze gegevens worden in overzichtelijke dashboards zichtbaar gemaakt.
Zo'n dashboard – of steeds vaker een app – biedt de werkplaatsverantwoordelijke inzicht in hoe de productie op dat moment verloopt en toont waar de verbeterpunten liggen met het grootste potentieel. Of hoe bijvoorbeeld insteltijden zich verhouden tot de gecalculeerde tijden. Of wat de meest voorkomende oorzaken van machinestoringen zijn. Door beslissingen te nemen op basis van deze data, verbetert uiteindelijk de bezettingsgraad van de machines.
Een ander voordeel is dat men voorraden kan reduceren doordat de planning gebruikmaakt van de ERP-data. Eén van de uitdagingen voor MES-ontwikkelaars is hoe ze hele waardeketens kunnen ontsluiten; niet alleen binnen een onderneming, maar ook de data van externe partners in de keten. De data van verschillende ketenpartners moeten daarmee transparanter worden voor alle betrokken partijen. In deze horizontale integratie zal cloudcomputing een wezenlijke rol spelen.
Eén van de uitdagingen voor MES-ontwikkelaars is hoe ze hele waardeketens kunnen ontsluiten; niet alleen binnen een onderneming, maar ook data van externe partners in de keten
Artificiële Intelligentie
Momenteel zorgt de opkomst van Machine Learning (ML) en – in de komende jaren – Artificiële Intelligentie (AI) ervoor dat het gebruik van MES-systemen verder vereenvoudigd wordt en dat het makkelijker wordt om alle data te analyseren en hier beslissingen op te baseren. Dit komt met name voort uit de snelle ontwikkeling van zogenaamde Large Language Models (LLM). Zoals je nu al informatie vraagt door een prompt in te typen in ChatGPT, zo zou men in de nabije toekomst Artificiële Intelligentie kunnen programmeren door simpelweg in bewoordingen aan te geven wat men wil.
Sommigen beweren dat taal de belangrijkste software interface zal worden in de toekomst. Je hebt dan geen AI-expert meer nodig om een bepaalde applicatie te bouwen of aan te passen. Vooral bij de kmo's zal dit ervoor zorgen dat veel meer monitoring en analysetools bereikbaar worden, niet alleen qua investering maar vooral wat betreft het gebruik ervan. Een MES-systeem zorgt voor overzicht van deze data én leidt ze terug naar een hoger niveau voor analyses.
Onderzoekers van de Hongaarse universiteit van Pannonia onderscheiden in een recente studie zes stadia van Industrie 4.0. In de eerste twee stadia gaat het om computerisatie en connectiviteit op het niveau van de individuele machine. Hier speelt MES nog geen rol. In het derde stadium gaat het om het zichtbaar maken van wat er gebeurt in de productie om vervolgens via de vierde stap volledige transparantie te creëren. Vanaf de derde fase komt MES in beeld.
Dan bereikt men de laatste twee fasen waarin verbetering centraal staat. Eerst predictive maintenance en dan als laatste stap in Industrie 4.0 het adaptieve vermogen van de productie om zich direct aan te passen aan de wisselende omstandigheden. Dat is de fase waarin een MES-systeem volledig kan worden benut.
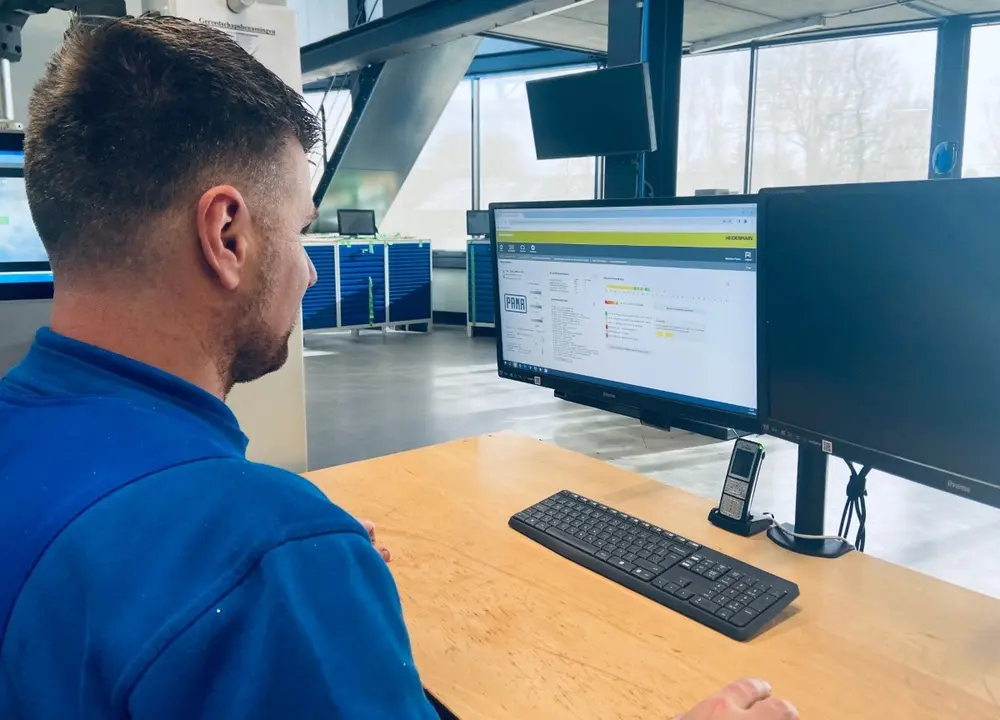
Nieuwe aanbieders van MES-systemen
Als je naar de aanbieders van MES-systemen kijkt, is er een interessante ontwikkeling gaande. Waren het vroeger met name gespecialiseerde softwareontwikkelaars die MES-systemen aanboden, zijn de laatste jaren onder andere machinebouwers en CAM-ontwikkelaars ook op deze markt gesprongen. Zij zien de vraag groeien; ze zien het gebruik gemakkelijker worden door de interfaces tussen de machines en software én ze hebben vaak al een ingang bij de eindgebruiker, in dit geval het metaalbedrijf. Sommigen brengen de MES-activiteiten onder in een apart bedrijf, terwijl anderen het integreren in bestaande oplossingen.
Een relatief jonge ontwikkeling is dat monitoringsystemen voor CNC-machines opschuiven in de richting van MES-systemen. Aanvankelijk waren de eerste systemen bedoeld om inzicht te krijgen in de effectieve inzet van een machine. Stilaan integreren de machinefabrikanten echter nieuwe functionaliteiten in hun monitoringsystemen die ook een planning mogelijk maken en zelfs een directe koppeling naar bijvoorbeeld een ERP-systeem. Ze doen dus meer dan enkel op individueel niveau de effectiviteit van een machine uitlezen.
Niet alleen machinefabrikanten werken aan deze ontwikkeling, er komen ook aanbieders van oplossingen die zich profileren als een machine-onafhankelijke oplossing. Dat is echter een punt dat inmiddels achterhaald is, omdat de machinefabrikanten zijn gaan inzien dat een oplossing specifiek voor hun machines geen werkbare oplossing in de praktijk zal zijn. Weinig metaalbedrijven zullen slechts één machinemerk in hun productie hebben.
Het ultieme doel van dit alles is om te komen tot een continu verbeterproces.
Het ultieme doel van dit alles is om te komen tot een continu verbeterproces