Cobot en industriële robot: geen concurrenten maar collega’s
TRADITIONELE ROBOT WINT NOG ALTIJD HET PLEIT
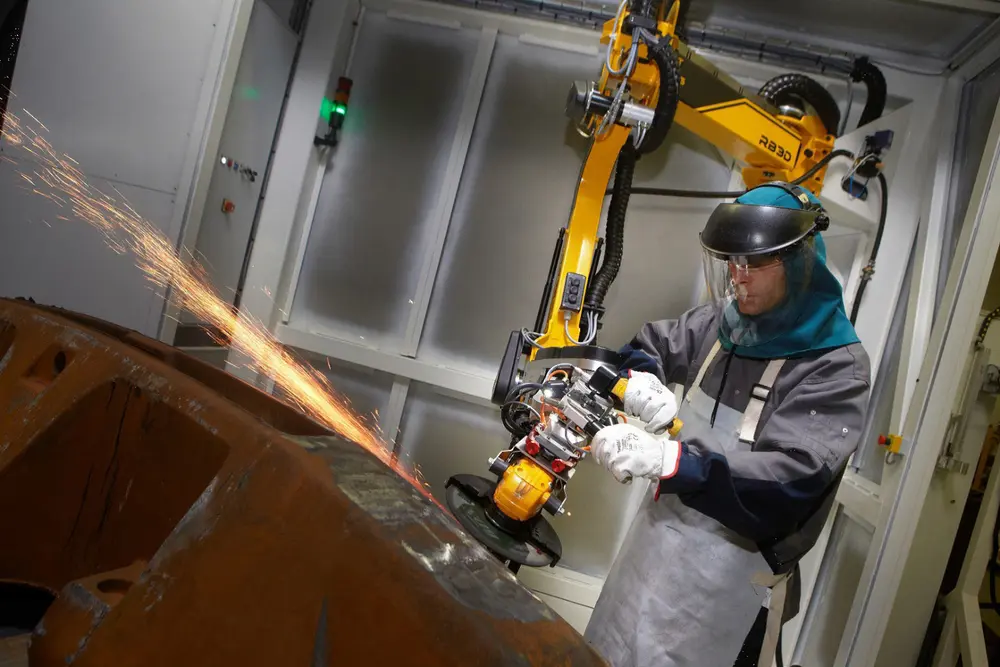
De opkomst van de cobot plaatst eindgebruikers voor een nieuwe keuze. Waar vroeger de keuze beperkt bleef tussen een traditionele machine en een industriële robot, wringt nu ook de samenwerkende robot zich tussen de mogelijkheden. Maar zijn de cobot en robot wel concurrenten? Een overzicht van de pro’s en contra’s van deze relatieve nieuweling.
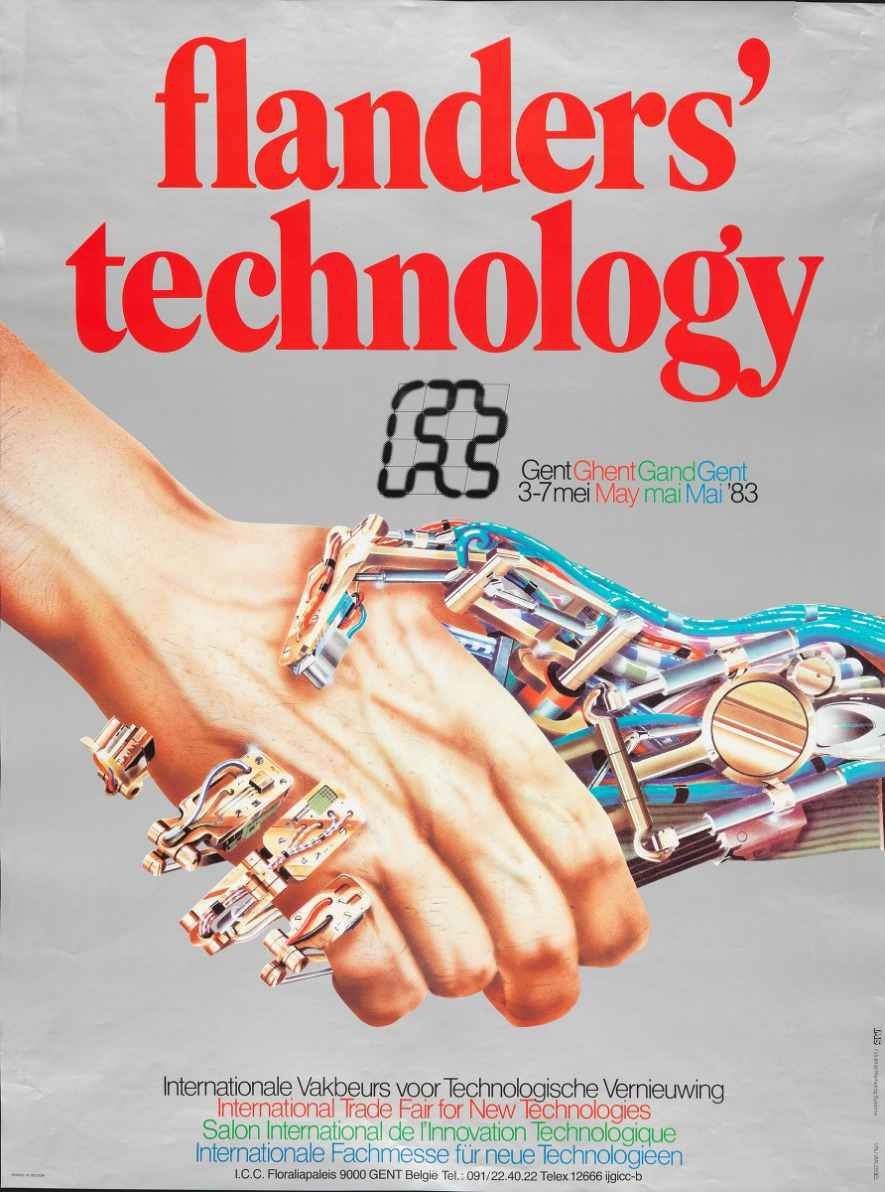
VEILIGHEID IS HÉT ISSUE
De traditionele industriële robot is ontworpen om zwaar en repetitief werk uit te voeren zonder al te veel stilstand. Dit type robots zit veelal gevangen achter stevig hekwerk, uiteraard vanwege de veiligheid van het personeel dat beschermd moet worden tegen aanvaringen met robotarmen of verwondingen door de last. Dat beperkt de robot enorm in zijn interactie met menselijke inbreng, die in feite gedegradeerd wordt tot een pure onderhouds- en reparatiefunctie. Assisteren bij de bewerking is onmogelijk en ook de toevoer wordt veelal machinaal gedaan via trilfeeders en transportbanden die via minieme openingen in het fysieke hekwerk de stukken aanvoeren. Hoogstens zien we eens een toepassing waarbij operatoren bakken met stukken manueel klaarzetten voor een verdere verwerking door de robot, maar dit is dan weer gebonden aan veiligheidsmaatregelen zoals lichtschermen of scanners die de beweging van de robot stilleggen. Als een bedrijf toch opteert voor een compleet hekloze uitvoering van de robotcel, dan is men gebonden aan veiligheidsscanners die de snelheid van de robot in gradaties verlagen tot deze nul is, waardoor ook de productiviteit meteen een ferme duik neemt. Een weinig efficiënte manier van werken dus. Bij een cobot ligt de veiligheid helemaal anders, want dit type robot is specifiek ontworpen met menselijke interactie in het achterhoofd. Daar waar de traditionele robot ervan uitgaat dat er geen menselijk contact is, zijn cobots ontwikkeld in de wetenschap dat ze voortdurend in aanraking zullen komen met operatoren. Dat wordt ook weerspiegeld in de veiligheidsnorm TS 15066, waarbij de pijn die mensen kunnen voelen, letterlijk de basis is voor de te volgen procedure. Voor meer informatie rond de TS 15066, zie het aparte kaderstuk rond dit thema.
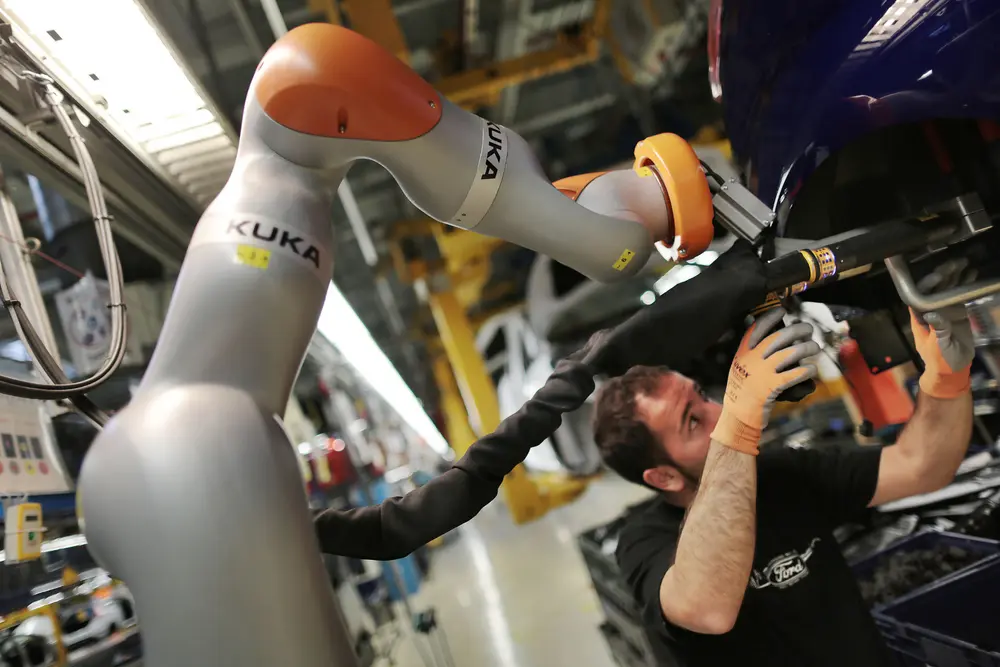
PAYLOAD
Het zware werk van industriële robots zorgt voor een breed scala aan uitvoeringen, voor elke applicatie is er een robot met een geschikte payload. Bij de meeste fabrikanten gaan die typisch richting een kleine 2.000 kg. Cobots hebben dan weer een beperkte payload (traditioneel ergens tussen de 5 en 35 kg). Maar hier moeten we al direct de kanttekening maken dat de cobottechnologie volop groeiende is. Zo zagen we al cobots verschijnen voor de automotive sector met een payload van 110 kg. Zoals bij elke innoverende markt geldt dus dat de stand van de technologie voortdurend verandert en dat het koffiedik kijken is wat de toekomst brengt.
COBOTICA REACH
De reach duidt de afstand aan tussen het centrum van de robot en het eindpunt van de robotarm als die volledig uitgestrekt is. Bij de traditionele industriële robots kan dit tot enkele meters lang zijn om zo een zeer flexibele opbouw van de productieruimte mogelijk te maken. Bij cobots is dat niet het geval, want die hebben zelden een reach die zich verder uitstrekt dan 1 meter. Uiteraard is de achterliggende reden hier dat cobots ontwikkeld zijn om de eenvoudige menselijke taken over te nemen.
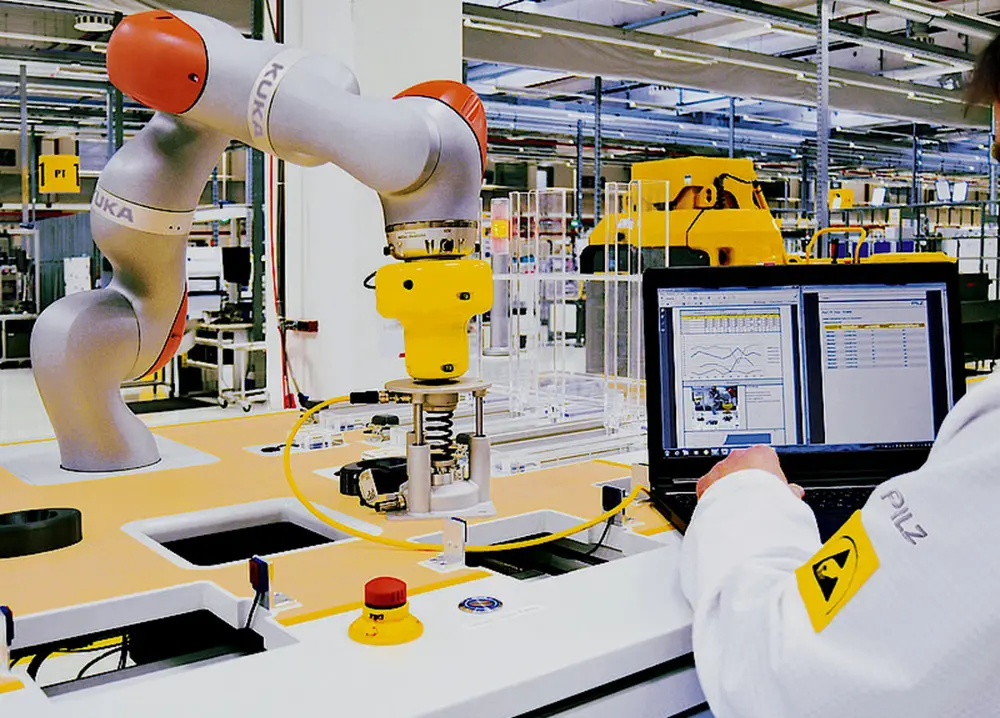
TS 15066
Sinds vorig jaar is de nieuwe veiligheidsnorm TS 15066 in voege getreden. Die is een aanvulling op de meer bekende normen voor industriële robots, de ISO 102181 en de 102182. De TS 15066 is ontwikkeld met de doorbraak van de cobot in het achterhoofd, omdat men merkte dat de vermelde ISO- normen tekortschoten bij dit soort robotsystemen. Van de 150 pagina’s in deze normen waren er welgeteld 8 pagina’s voorzien over collaboratieve taken. Let wel dat de TS 15066 geen norm is specifiek voor cobots, maar wel voor robotsystemen die collaboratieve taken uitvoeren. Wie zijn traditionele robot uit zijn hek wil bevrijden, moet dus ook met deze norm rekening houden. Er worden in de norm vier types van veiligheid bij een collaboratieve samenwerking beschreven:
- Safety-rated Monitored Stop: in deze veiligheidsfunctie stopt het robotsysteem als een operator zich in een afgebakende zone bevindt. Dit is handig bij installaties waarbij de samenwerking tussen mens en robot beperkt is tot momenten als het instellen en herpositioneren. Na het verlaten van de afgebakende zone gaat het robotsysteem automatisch weer aan de slag.
- Hand-guided: hierbij heeft de operator steeds de volledige controle over de beweging van het robotsysteem.
- Speed & Separation Monitoring: bij deze vorm wordt er gebruikgemaakt van veiligheidsscanners of visionsystemen die de zone rond het robotsysteem voortdurend monitoren. De snelheid van de robot wordt aangepast aan de afstand waarop de operator zich van de robot bevindt.
- Power and Force Limited (PFL) – De robotsnelheid en -beweging worden zo geconcipieerd dat een impact niet zal resulteren in pijn of verwondingen van de operator. Botsingen met mensen zijn onvermijdelijk, dat is de compleet andere benadering van veiligheid in deze laatste opmerkelijke veiligheidsfunctie. Niet het voorkomen van botsingen staat hier dus centraal, zoals in het traditionele veiligheidsdenken, maar wel het instellen van de maximumkracht van een impact en de snelheid van de impact. Dat gebeurde op basis van een onderzoek dat uitgevoerd is door de universiteit van Mainz bij honderd proefpersonen. Zij gingen voor hun onderzoek na wat de hoeveelheid pijn is die een mens voelt bij een zekere impact. Dat deden ze voor 29 lichaamszones. Zo formuleerden ze maximumwaardes voor elke lichaamszone. Uit de veiligheidsanalyse moet verder blijken welke lichaamsdelen in de applicatie een risico vormen. Vervolgens moet voor elk van die delen opgelijst worden welk type impact er is (door een aanvaring of klemming) en hoeveel de frequentie en de duur van het contact bedragen. Ongeacht welke van de vier methodes toegepast wordt, is ook steeds Pld cat.3 (volgens ISO 13849) of SIL2 met HFT1 volgens IEC62061 verplicht. Let er wel op dat de veiligheid van uw cobot – toch wat betreft het beantwoorden aan de specifieke veiligheidsnormen – voornamelijk de verantwoordelijkheid is van de robotproducent en de integrator.
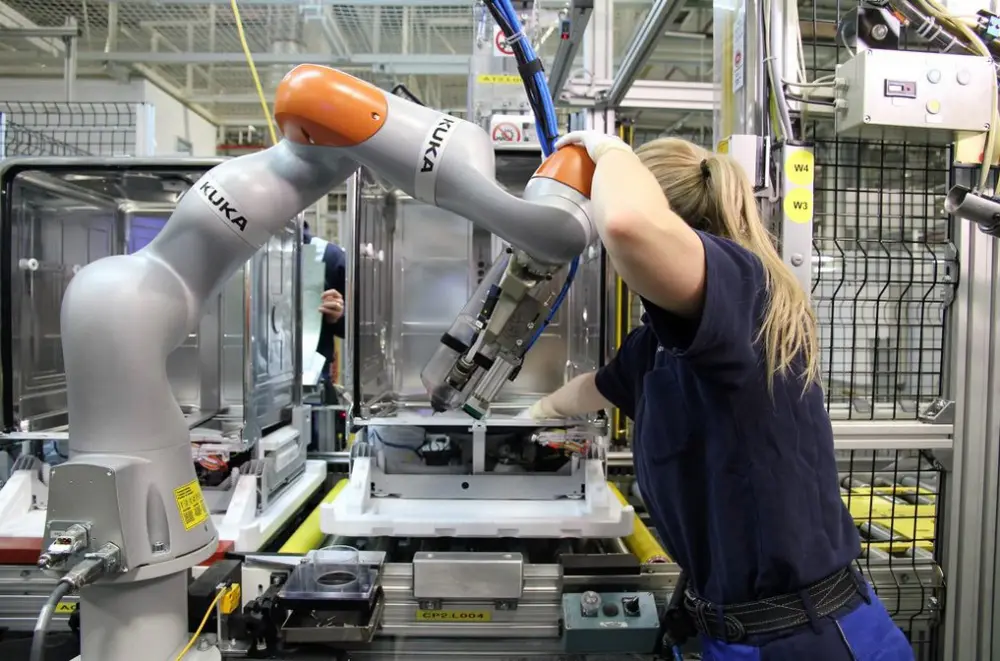
COBOTICA SNELHEID
Industriële robots zijn over het algemeen een stuk sneller, afhankelijk van het type. Bij deltarobots gaat dit makkelijk tot 10 m/s, de traditionele robot haalt makkelijk lineaire snelheden in de grootteorde van 3 m/s. Deze robots moeten zo snel mogelijk werken om een zo groot mogelijke output te genereren. Cobots daarentegen werken aan tragere snelheden, omdat de snelheid door hun collaboratieve aard ook minder belangrijk is: ze moeten zich aanpassen aan de taak van de medewerker. Bij het karakteristieke gebruik van cobots, waarbij de cobot een werkstuk aangeeft aan een medewerker die het vervolgens verder verwerkt, is het weinig zinvol dat de robot duizelingwekkende snelheden haalt. Bovendien betekenen grotere snelheden ook een grotere impact bij aanvaringen met operatoren.
PROGRAMMERING
Robotprogrammering is in vele gevallen werk voor de integrator. Afhankelijk van het product dat op dat moment gefabriceerd wordt, wordt het programma aangepast aan de nieuwe productiebatch. Robotproducenten leveren de laatste jaren evenwel grote inspanningen om een toegankelijke programmering toe te laten. Dat gebeurt op meerdere sporen zoals het werken met een visuele vorm of met een op PLC-taal gebaseerde programmeertaal. Een noodzakelijke evolutie, want vandaag worden productiebedrijven vaak geconfronteerd met kleine, maar gespecialiseerde series. Die vragen ook om een snel aanpasbare robot. Een cobot werkt volgens een ander programmeringsprincipe. De taak wordt in de meeste gevallen aangeleerd door de te maken beweging na te bootsen. Dit verloopt zeer intuïtief en vereist in principe weinig kennis van programmeren.
INPLANTING
Een industriële robot kan beschouwd worden als elke andere machine. Die neemt veel bedrijfsruimte in, moet afgeschermd worden, er is plaats nodig voor de voeding, voor de wisselstukken, meestal zijn er ingrijpende werken en veranderingen nodig voor de plaatsing … Een industriële robot is dus alomtegenwoordig in een productieruimte. Een cobot daarentegen laat zich makkelijk integreren, neemt weinig plaats in en is een stuk goedkoper dan een industriële robot. Hij is over het algemeen kleiner en ook de secundaire kosten (plaatsing, programmeren …) zijn beperkt. Maar beide vergelijken is eigenlijk onzin, gezien de grote verschillen in snelheid en payload. Er komt stilaan meer interesse in collaboratieve robots, maar omdat deze technologie eigenlijk haaks staat op de veiligheidsfilosofie die ons al jaren ingepeperd wordt (afschermen!), is er een zekere terughoudendheid. Ook de workflow is vaak al jaren min of meer dezelfde, waardoor men niet goed inziet waar een cobot precies van nut zou kunnen zijn. Soms is er dan ook een complete herwerking nodig van die productieflow, wat uiteraard op weerstand stuit. En dan hebben we het nog niet gehad over de veiligheidsanalyse, die in bepaalde gevallen zelfs kan oordelen dat een hek rond de cobot nodig is, hoe contradictorisch dit ook klinkt.