Stikstofproductie steeds vaker on site
Zelf controle over hoeveelheid, zuiverheid en beschikbare druk
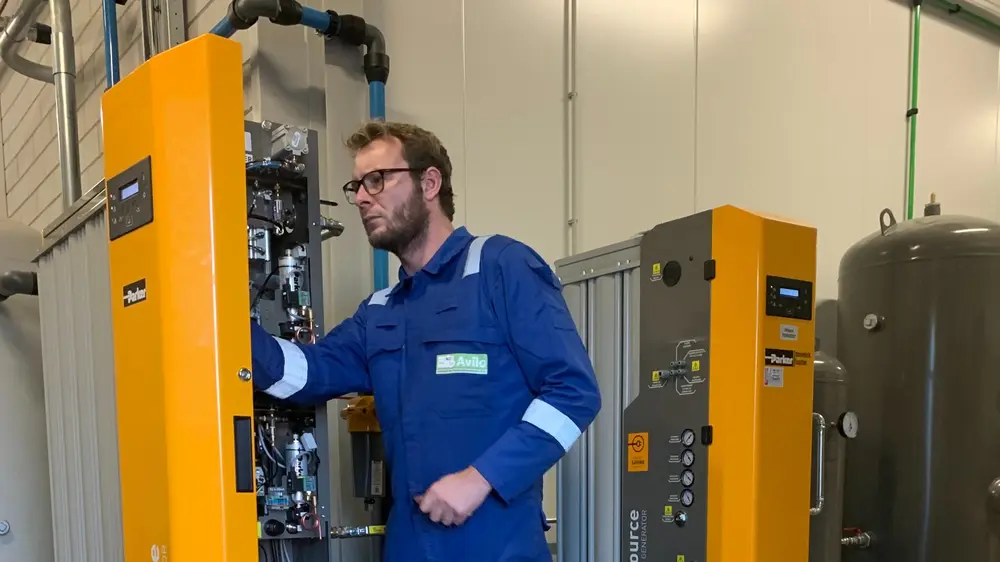
Stikstof wordt binnen de industrie op grote schaal en in sterk uiteenlopende sectoren toegepast. Dat varieert van de voedings-, metaal- en elektronica-industrie tot de chemische en farmaceutische industrie. In veel sectoren stapt men in toenemende mate over op het zelf genereren van stikstof met behulp van een stikstofgenerator. Twee technieken lenen zich daarvoor bij uitstek: membraantechnologie en de PSA-technologie.
Inert
Stikstof is onder normale omstandigheden een inert, reuk- en kleurloos gas, dat onschadelijk is voor mens en milieu. Het element kent toepassingen in uiteenlopende takken van industrie.
Stikstofgas (N2) wordt onder meer gebruikt als antioxidant voor het verlengen van de houdbaarheid van producten, als beschermgas bij het verpakken onder beschermende atmosfeer, voor inertisering en bij brandpreventie door het creëren van een zuurstofarme atmosfeer. Ook is het een belangrijk bestanddeel bij de bereiding van kunstmest, het uitlogen van goud en de productie van explosieven.
Vloeibaar stikstof wordt onder meer gebruikt in de voedingsindustrie om producten in te vriezen, in kerncentrales als blusmateriaal indien de reactor te heet wordt, in diverse industrietakken om bepaalde stoffen makkelijk(er) te kunnen verpulveren en bijvoorbeeld ook als koude mantel in de cryostaat van supergeleidende magneten, om warmte-instraling van het zich binnenin bevindende bad met vloeibaar helium te verminderen.
Opties
Er zijn in principe drie manieren om kwalitatief hoogwaardig stikstofgas te verkrijgen.
geleasede on-site stikstofgastank
Hierbij wordt gebruikgemaakt van een tank met vloeibare stikstof waarvan de inhoud wanneer nodig via bulktransport wordt aangevuld vanuit een centrale productielocatie. Ter plaatse wordt daar vloeibaar gemaakte, gecomprimeerde lucht gedestilleerd en gesplitst in verschillende gassen, waarbij stikstof de hoofdmoot vormt. Deze stikstof, die nagenoeg altijd over dezelfde hoge zuiverheid beschikt, wordt bij de gebruiker weer in de gasfase gebracht door verdamping. Dit is een proces dat veel warmte vergt.
aankoop van hogedrukflessen met stikstofgas
Dit ‘flessengas’ – een bijproduct van de hierboven beschreven productiemethode – is ook standaard op een en dezelfde (hoge) zuiverheid beschikbaar. Het gebruik van flessengas is evenwel geen optie wanneer er sprake is van een hoog stikstofgasverbruik.
zelf genereren met perslucht
Bedrijven kiezen in toenemende mate voor productie on site; hiervoor zijn verder geen aparte vergunningen noodzakelijk. De voordelen daarvan zijn evident: zo heeft men de hoeveelheid stikstof, de zuiverheid ervan en de druk waarmee wordt gewerkt zelf in de hand. Bijkomende voordelen zijn onder meer de logistieke controle, geen problemen met de cryogene opslag, geen afval door boil-offverliezen (verlies van koud product) en al naargelang ook een financieel voordeel en prijsstabiliteit.
Stikstof wordt in dat geval verkregen door gebruik te maken van stikstofgeneratoren, meestal in combinatie met een reeds operationele persluchtinstallatie. On-siteproductie werkt het best wanneer de kwaliteit aan de gewenste zuiverheid wordt aangepast; in principe kan elke gewenste zuiverheid daarbij worden verkregen. Voor een doeltreffende stikstofproductie is het dus van belang om per proces inzicht te verkrijgen in de benodigde zuiverheidsgraad.
Membraantechnologie
Het hart van membraanstikstofgeneratoren bestaat uit een membraanmodule (diameter circa 10 cm) die met kleine, holle polymeervezels is gevuld. De eerste processtap is permeatie, waarbij droge, schone perslucht in de generator wordt geleid. Dankzij de vezelstructuur stroomt een deel van de binnentredende perslucht naar de buitenkant van de vezels. Door de relatief hoge doordringsnelheid van water en zuurstof verlaten die de module al vrij snel via de zogeheten permeaatuitgang. Aangezien de doordringsnelheid van stikstof merkelijk lager ligt, blijft dit gas in het membraan achter.
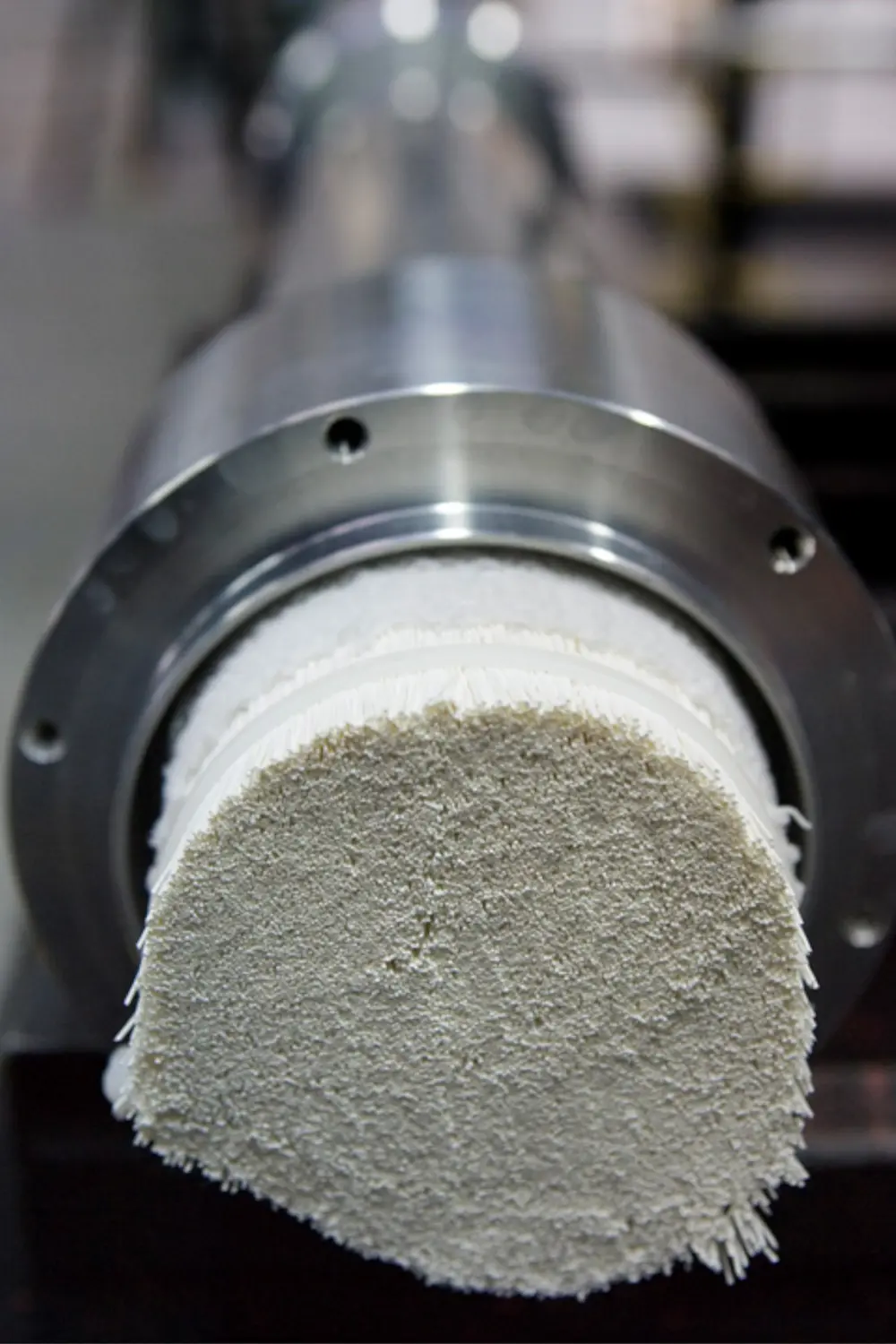
Stikstofgeneratoren met hollevezelmembraanmodules stoten zuurstof en andere gassen uiteindelijk weer uit, richting de omgevingslucht. De membraanmodules hebben een theoretische levensduur van 10 jaar, wat wordt ingekort door zaken als vervuiling door een slechte kwaliteit van perslucht, aantasting door eventuele dampen van oplosmiddelen en/of ozon die in de perslucht is terechtgekomen.
Door nu een aantal membraanmodules met elkaar te schakelen, kan een stikstofzuiverheid worden bereikt variërend van 95% (parallelle schakeling) tot 99,9% (serieschakeling). Membraangeneratoren met een zuiverheid tot 99,5% worden gebruikt voor kleine volumes; voor oplopende volumes begint dit bij 99%.
Een doeltreffende stikstofproductie hangt samen met de benodigde zuiverheidsgraad
Pressure Swing Adsorption
Bij deze techniek vindt scheiding van stikstof en zuurstof plaats door de binding van de zuurstofmoleculen aan een moleculaire koolstofzeef, de Carbon Molecular Sieve (CMS). Dat gebeurt alternerend in twee met CMS gevulde drukvaten: één vat is actief terwijl het andere regenereert ter voorbereiding op de volgende adsorptiefase.
Wanneer de perslucht het eerste drukvat binnenstroomt, zullen de zuurstofmoleculen de poriën van de koolstofzeef binnengaan; de stikstofmoleculen zijn daarvoor te groot en passeren de koolstofzeef ‘ongehinderd’. Na het verlaten van het systeem is deze stikstof direct geschikt voor gebruik. Een klein deel van de geproduceerde stikstof wordt naar het tweede drukvat geleid ten behoeve van de regeneratie ervan. Door daar de druk op te heffen, verliest de CSM het vermogen de zuurstofmoleculen aan zich te binden. Ze komen los en worden meegevoerd met de kleine stikstofstroom uit het eerste drukvat.
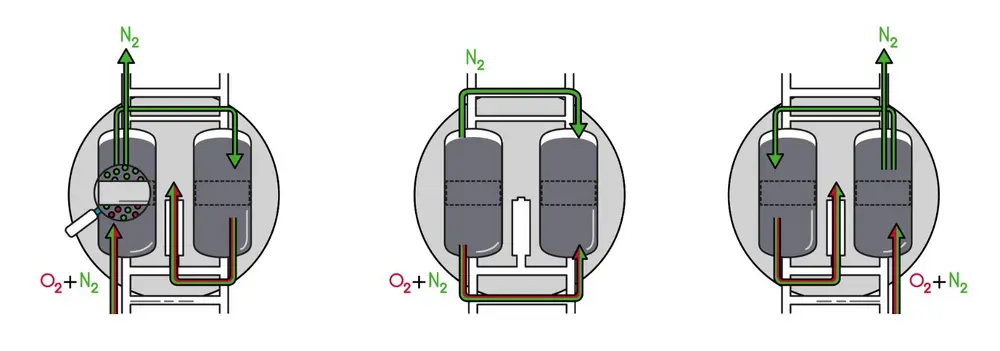
Voorafgaand aan de ‘omschakeling’ – vandaar de naam 'pressure swing adsorption' – wordt de druk in de beide vaten geëgaliseerd. De CMS in het eerste drukvat raakt verzadigd, terwijl het tweede drukvat wordt geregenereerd. Op het einde van de cyclus wordt de druk in de beide vaten geëgaliseerd, waarna de rol van de beide vaten wisselt. De zuiverheid van het geproduceerde stikstofgas ligt gemiddeld tussen 95 en 99,999%, maar onder bepaalde omstandigheden zijn zelfs nog hogere zuiverheden haalbaar.
Het grote voordeel van deze techniek ten opzichte van de membraantechnologie is het feit dat voor eenzelfde resultaat de benodigde hoeveelheid perslucht ingeval van hogere zuiverheden soms tot wel 40% lager ligt, op voorwaarde dat de capaciteit van de PSA voor de volle honderd procent wordt benut. Met de PSA-technologie kan ook een hogere zuiverheid worden behaald. Daartegenover staat dan weer dat het wijzigen van de ingestelde zuiverheid bij PSA aanzienlijk complexer is dan bij de membraantechnologie.
Veilig werken met stikstof
Blootstelling aan een teveel aan stikstof brengt gezondheidsrisico’s met zich mee. Het stikstofgas verdringt de voor de ademhaling noodzakelijke zuurstof. Stikstof die vrijkomt in de open lucht of in een goed geventileerde ruimte vormt geen gevaar; vloeibaar stikstof verdampt (1 l vloeibare stikstof vormt 600 l gasvormige stikstof). Vloeibare stikstof (-196 °C) kan bij contact met een onbeschermd huidoppervlak leiden tot (ernstige) brandwonden.
Naast de standaard-PBM’s zijn bij werkzaamheden met stikstof aanvullende maatregelen nodig om inademing van lucht met daarin te weinig zuurstof en huidcontact (vloeibare stikstof) te voorkomen. Bij het werken met stikstofgas zijn dat een persoonlijke zuurstofmeter en onafhankelijke ademluchtvoorziening. Bij werkzaamheden met vloeibaar stikstof: een persoonlijke zuurstofmeter, gesloten werkkleding, (vol)gelaatsscherm, cryogene handschoenen en een cryogeen zuurschort.
Procesvereisten
Een eerste vereiste is dat de perslucht schoon en droog is. Dit bevordert de stikstofkwaliteit en voorkomt dat het aanwezige vocht beschadigingen veroorzaakt aan de mebraammodules of de koolstofzeven. Een droger is dan ook een vereiste. Wordt de toegevoerde perslucht door een oliegesmeerde compressor geleid, dan dienen eveneens een oliecoalescerend filter en een koolstoffilter te worden geïnstalleerd om onzuiverheden uit de perslucht te verwijderen.
Hoe lager de gewenste zuiverheid, des te meer stikstof er uit de lucht wordt gehaald en des te minder perslucht er nodig is. Dit betekent dat het energieverbruik van de compressorinstallatie lager ligt; zie ook de tabellen. De zuiverheid van de geproduceerde stikstof kan – zeker wanneer deze is opgewekt met diep gedroogde perslucht (-40 °C drukdauwpunt) – ook in negatieve zin worden beïnvloed door lekkages in het leidingsysteem. Gedroogd gas werkt hygroscopisch en trekt vocht uit de omgeving aan, ondanks het feit dat de druk ter plaatse hoger is dan daar waar het vocht vandaan komt. Ook stikstoflekkage komt voor, met als gevolg dat het zuurstofgehalte in de betreffende ruimte daalt, met alle gevolgen van dien. Het is dan ook zaak de stikstofinstallatie met enige regelmaat te (laten) controleren op lekdichtheid.
Met medewerking van Atlas Copco, Avilo, Geveke en Presscon