L'automatisation durable va bien au-delà de l'achat d'une machine éco-énergétique
Les entreprises qui cherchent à automatiser de manière durable se concentrent généralement sur les composants individuels. Par exemple, elles achètent un moteur qui consomme moins. Cette solution est assez simple et abordable, mais une optimisation approfondie de l'ensemble du système peut permettre de réaliser des gains d'efficacité bien plus importants. Comment peut-on automatiser de manière plus durable et économiser de l'énergie en recueillant des données et en considérant le système de manière globale?
Qu'est-ce que l'automatisation durable?
Le remplacement d'une machine par une autre plus économique est bien sûr le moyen le plus évident de réduire la consommation d'énergie. Aujourd'hui, de nombreuses entreprises ont déjà franchi cette étape relativement simple. Pour les autres gros consommateurs, soit la consommation actuelle est inconnue, soit les coûts d'investissement sont trop élevés, soit la différence d'efficacité est trop faible.
Ce que l'on sait moins, c'est qu'il y a souvent beaucoup plus de gains à réaliser au niveau du système qu'au niveau des composants individuels. Cette vision globale au niveau du système s'appelle l'automatisation durable - un concept à la fois beau et vaste. En général, la combinaison de trois éléments est importante:
- Quelle est l'efficacité du fonctionnement de la machine? Cela concerne l'utilisation des sources d'énergie, telles que le gaz, l'eau, l'air comprimé et la vapeur.
- Quelle est l'efficacité de l'utilisation de la machine par l'entreprise? Assurez-vous que la machine fonctionne de manière optimale, car une machine à l'arrêt n'apporte rien au processus de production.
- La machine est-elle utilisée de manière fonctionnelle? Une machine peut soulager les employés d'un travail lourd, dangereux ou répétitif, à condition qu'elle soit utilisée correctement, c'est-à-dire de manière fluide et sûre.
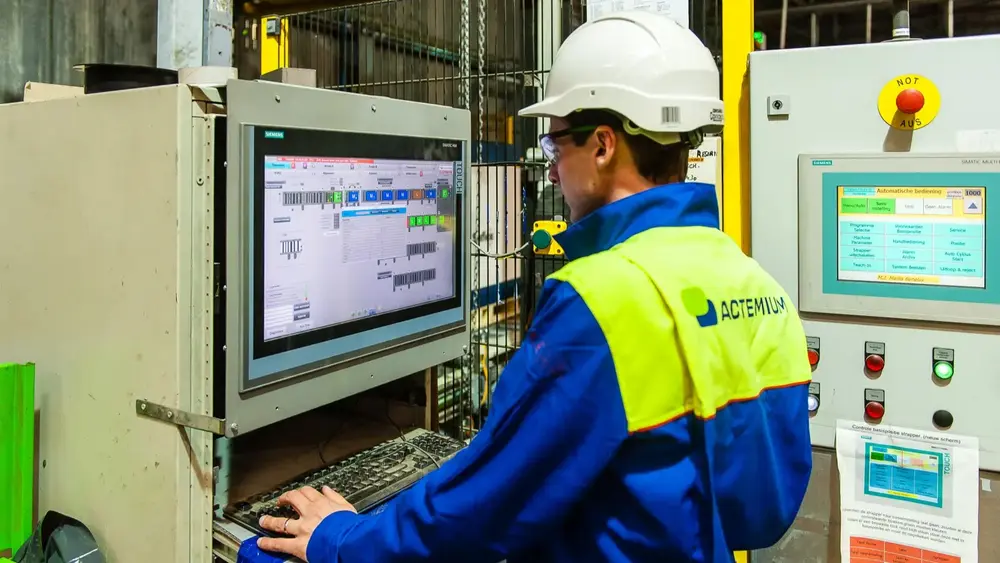
Approche numérique
L'automatisation durable ne se limite donc pas à remplacer les appareils inefficaces par des équivalents plus performants. Un contrôle et une surveillance plus efficaces peuvent avoir beaucoup plus d'impact que de continuer à faire la même chose avec de meilleurs composants.
Pensez à la commande par fréquence au lieu de la commande par vanne dans le cas d'une pompe, à la réduction de la vitesse d'un convoyeur lorsque le débit demandé est plus faible, ou à l'arrêt des appareils lorsqu'ils ne sont pas nécessaires.
La mise en œuvre de ces modifications est souvent déjà possible avec l'automatisation classique. Pour savoir quels systèmes peuvent être optimisés, de quelle manière et quels sont les gains, il faut souvent une approche numérique (avec données ou simulation).
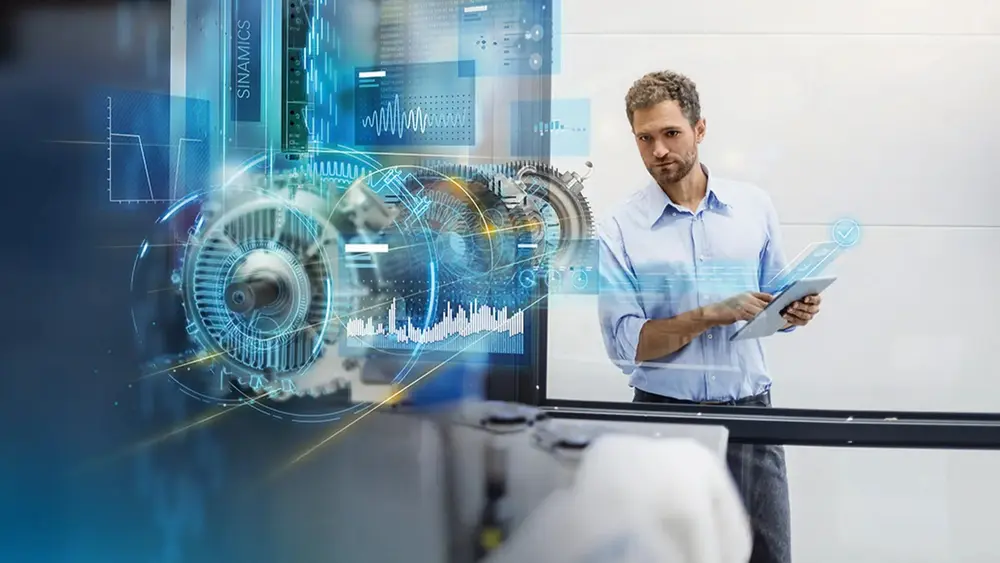
Exemples d'optimisation
Réutilisation
Le remplacement d'un composant par un autre plus performant présente logiquement un inconvénient: une unité qui fonctionne encore est mise hors service, tandis qu'une nouvelle unité génère à son tour des émissions. En termes de décarbonisation, la réduction des émissions lors de la production doit tenir compte des émissions supplémentaires du nouvel appareil. La réutilisation de l'appareil comme pièce de rechange en stock ou l'utilisation de pièces remises à neuf peut minimiser l'impact du nouvel appareil.
Une alternative durable à l'achat d'une nouvelle machine consiste à réviser ou à moderniser l'équipement existant. Le remplacement des pièces obsolètes et l'ajout de certains capteurs peuvent permettre à une machine de fonctionner sans problème pendant 20 ans. En retour, ces capteurs fournissent davantage d'informations à l'utilisateur, qui peut ainsi accroître l'efficacité et donc la durabilité.
Un timing idéal
Un autre exemple est l'utilisation de la maintenance prédictive pour prolonger la durée de vie des composants. Aujourd'hui, de nombreux composants (moteurs, réducteurs et vannes, par exemple) sont remplacés préventivement tout au long de leur vie, même s'ils sont encore en parfait état de fonctionnement. La maintenance prédictive permet au service de maintenance de remplacer les composants exactement au bon moment. Cela permet de maximiser la durée de vie et de réduire le risque de temps d'arrêt imprévus. A cet effet, on utilise l'intelligence artificielle.
La maintenance prédictive permet au service de maintenance de remplacer les composants au bon moment
Économies
Des études montrent que réduire la pression de service d'un système d'air comprimé peut permettre d'économiser 14% d'énergie. Une installation dotée d'un compresseur d'une puissance d'environ 90 kW peut donc facilement économiser 270.000 kWh par an. C'est l'équivalent de près de 80 ménages. Des économies peuvent également être réalisées dans le domaine du vide, qui est largement utilisé lors de la collecte des produits. En appliquant des plans d'économie, il est possible d'économiser jusqu'à 80% de vide. Pour un générateur de vide moyen, cela représente plus de 600 kg de CO2 par an.
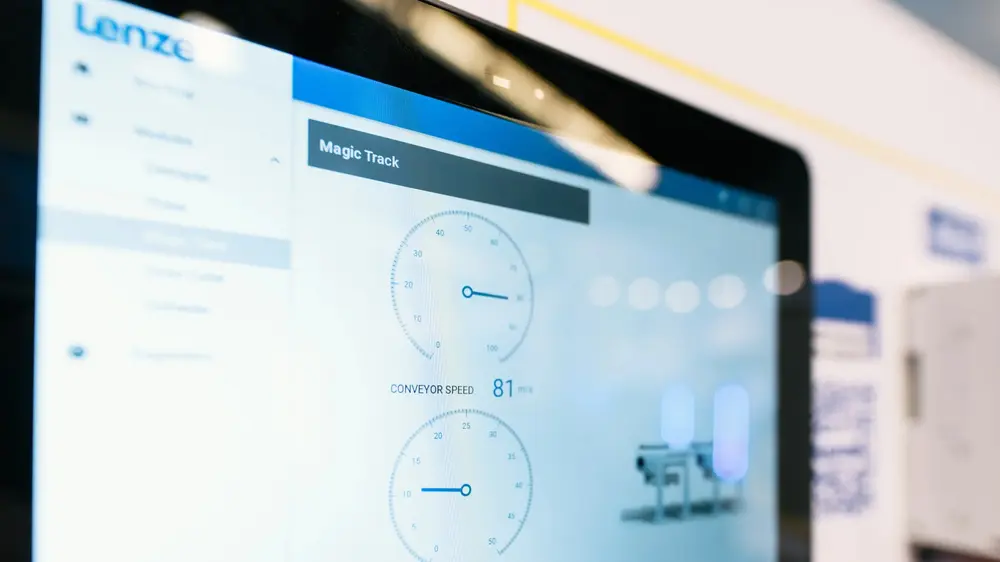
Un changement important est que les entreprises sont désormais beaucoup plus enclines à utiliser la bonne source d'énergie en fonction de l'application. Par exemple, les servomoteurs sont souvent plus économiques que l'air comprimé, mais pas dans tous les cas. Il ne faut donc pas choisir l'un ou l'autre, mais se demander quelle source est la plus adaptée à chaque fonction.
Les défis de l'optimisation
Découvrir où on peut réaliser des bénéfices et combien: c'est l'un des principaux défis de l'automatisation durable. Les données et la simulation sont deux outils utiles, mais également difficiles, que les entreprises peuvent utiliser à cet effet.
Données
Grâce aux données, les entreprises peuvent savoir quelle quantité d'énergie est consommée par quels consommateurs et à quel moment . Toutefois, dans de nombreux environnements de production, ces données ne sont pas centralisées, de sorte que les entreprises ne savent pas d'où provient leur consommation d'énergie. C'est là qu'un système de surveillance de l'énergie peut s'avérer utile. À l'aide de ce système, on examine comment les compteurs existants (séparés ou intégrés dans des variateurs de fréquence, par exemple) peuvent communiquer vers un endroit central (cloud, Edge ou serveur existant).
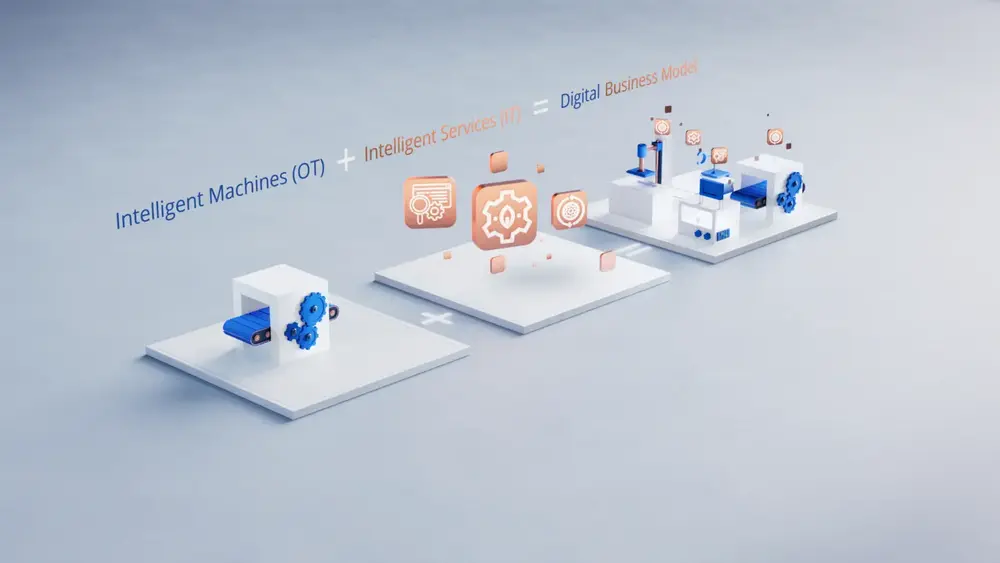
Simulation
Pour les nouvelles lignes de production, la simulation est la première étape. En incluant l'énergie comme indicateur clé de performance dans la conception numérique d'une ligne de production, il est plus facile d'optimiser la conception en termes de consommation d'énergie. En outre, la simulation présente des avantages secondaires en termes de durabilité. Par exemple, un meilleur dimensionnement des composants permet un fonctionnement plus efficace et réduit les risques de dommages lors du démarrage.
La simulation est également utile pour les lignes existantes: elle peut être utilisée pour tester des scénarios hypothétiques. L'ajustement des commandes a souvent une incidence sur la consommation d'énergie et la qualité du produit. Tester d'abord dans un environnement virtuel permet de déceler les effets imprévus et de réduire le risque d'erreurs.
En incluant l'énergie comme indicateur clé de performance dans la conception numérique d'une ligne de production, il est plus facile d'optimiser la conception en termes de consommation d'énergie
Etat d'esprit
Souvent, les constructeurs de machines ne sont pas suffisamment incités à produire de manière aussi efficace que possible sur le plan énergétique, car cette manière de travailler augmente le coût de production. En conséquence, les utilisateurs finaux sont moins enclins à acheter la machine. Un état d'esprit différent et global permet d'éviter que le prix de revient ne soit le principal critère d'achat d'une machine et garantit que les utilisateurs finaux prennent en compte des aspects tels que le rendement, la consommation d'énergie et l'entretien, dans une mesure au moins égale.
Par exemple, une unité qui arrête automatiquement une machine inutilisée est relativement coûteuse en soi. Mais l'effet positif peut permettre d'amortir cet investissement en quelques années seulement, alors que la durée de vie de la machine atteint souvent 20 à 30 ans.
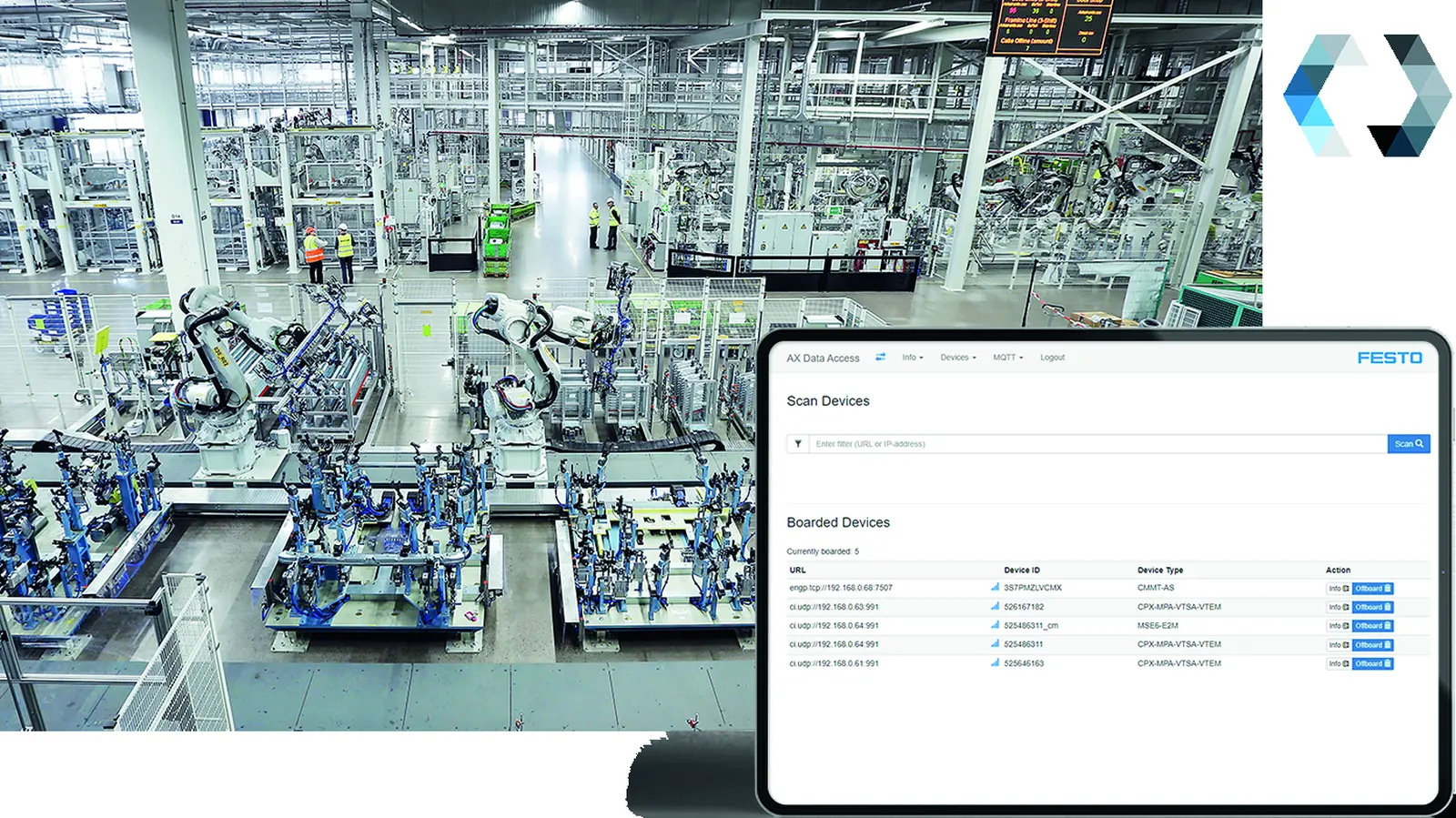
À l'avenir, l'interaction entre les systèmes deviendra plus intelligente. Un système de surveillance de l'énergie combiné à des données de production détectera lui-même les écarts et proposera des suggestions d'optimisation. Le système sous-jacent testera d'abord la suggestion sur un jumeau numérique pour s'assurer qu'il n'y a pas d'impact négatif sur la production et procédera automatiquement aux modifications nécessaires dans l'automate.
L'IA facilitera l'interprétation des données. Elle permet, sans connaissance de la programmation, de récupérer et de comparer les informations nécessaires. Cela permet aux personnes ayant des connaissances en production, mais moins en informatique, d'optimiser plus rapidement. L'IA permet également aux systèmes de contrôle de l'énergie de faire de meilleures suggestions.
En collaboration avec Actemium, Beckhoff Automation, Festo, Lenze et Siemens