Seule une télématique adaptée garantit l’efficacité de vos machines
L’UTILISATION DES BIG DATA POUR UNE FLOTTE DE MACHINES INTELLIGENTES
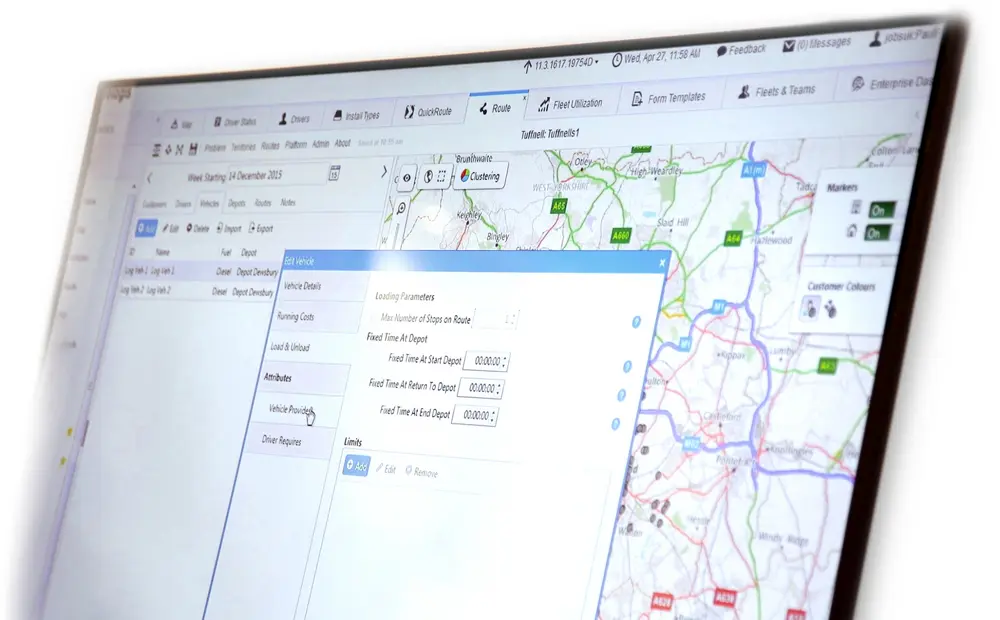
Nos machines sont de plus en plus intelligentes grâce aux avancées dans le domaine de la télématique. Au sein des entreprises, ces innovations doivent être utilisées dans le but d’exploiter au maximum leur valeur ajoutée. Les nouveautés se succèdent à un tel rythme qu’il est difficile de savoir exactement ce qu’il est possible de faire aujourd’hui. Voici donc un aperçu.
Chaque arrêt coûte très cher
Pendant des années, nous avons utilisé nos machines de façon relativement simple. Tant qu’elles fonctionnait, il n’y avait pas de problème. Le fonctionnement était garanti par un entretien périodique, et la sécurité par une certification obligatoire. En soi, cette méthode de travail ne pose pas de problème, mais les ennuis surviennent subitement dès qu’une panne inattendue se produit. En général, au moment où l’on s’y attendait le moins. Le coût d’un arrêt imprévu peut rapidement prendre une ampleur importante. Non seulement la personne se retrouve en chômage technique, mais le chantier prend aussi du retard à mesure qu’il faut attendre l’intervention d’un technicien externe. De plus, il faut y ajouter le coût d’un entretien de plus, celui d’une machine de location éventuellement prise en remplacement, sans oublier qu’il faut parfois attendre longtemps avant d’obtenir la pièce de rechange, qui souvent coûte elle aussi trop cher. Ajoutez à cela le coût incalculable imputé à votre perte de crédibilité. Rien de bon pour les nerfs de vos clients, et encore moins pour votre portefeuille. Et c’est bien dommage, car une étude a récemment montré que 80% des arrêts imprévus auraient pu être évités grâce à un plan de maintenance plus dynamique, adapté aux besoins réels du véhicule.
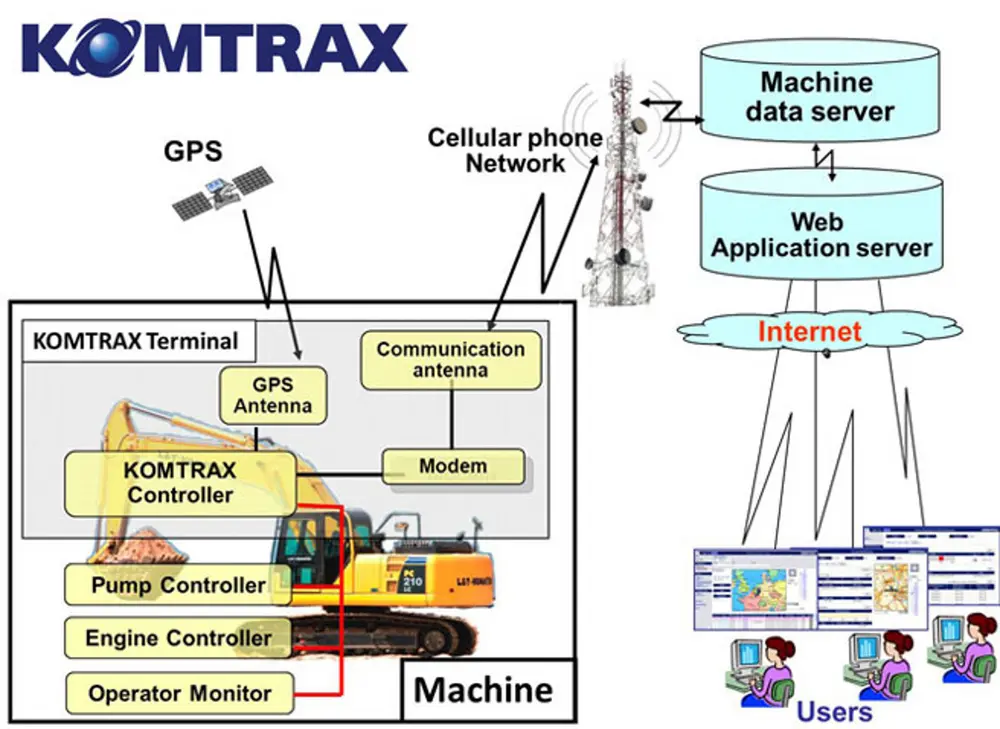
La télématique est synonyme de nouvelles possibilités
Les fabricants réagissent en développant de nouveaux concepts pour le suivi des machines. Et dans ce sens, ils suivent de près les avancées dans les autres secteurs également. L’industrie de la manufacture, par exemple, où une ligne de production entière peut être arrêtée suite à une panne d’un seul moteur. Le secteur militaire aussi est un bon exemple, puisqu’il s’agit là d’installations qui ne peuvent jamais tomber en panne. Rien de surprenant donc à ce que des concepts tels que la maintenance prédictive et la maintenance de condition aient d’abord été développés dans le secteur de l’aéronautique. Bref: le suivi des éléments principaux des composants critiques permet de prévoir les besoins réels de maintenance d’une pièce spécifique. En analysant la température et la qualité de l’huile régulièrement, p.ex., on peut allonger considérablement la durée de vie des roulements. L’électricité dégagée par un moteur peut être mesurée afin de déceler une tendance négative. Les maintenances sont alors plus efficaces, mais cela permet aussi d’éviter des interventions supplémentaires. Tout spécialiste en maintenance vous le dira d’ailleurs: des interventions de maintenance trop régulières peuvent faire plus de mal que de bien.
SUIVI A DISTANCE

Les mesures de toutes sortes de données, c’est une chose, après il faut encore trouver le moyen de les communiquer et de les traiter. Cette partie est souvent nettement simplifiée par la télématique, que nous connaissons surtout avec les systèmes de tracking qui nous permettent de savoir où se trouvent nos véhicules à n’importe quel moment. De plus en plus, cette fonction est étendue à de nouvelles fonctionnalités, que l’on regroupe aussi sous l’appellation ‘télématique’. Un terme adapté, puisqu’il s’agit d’une contraction de télécommunication et d’informatique, ce qui couvre de manière assez complète le nouveau champ d’application.
LES ‘BIG DATA’ ET L’INTELLIGENCE ARTIFICIELLE: ENCORE UN PAS DE PLUS
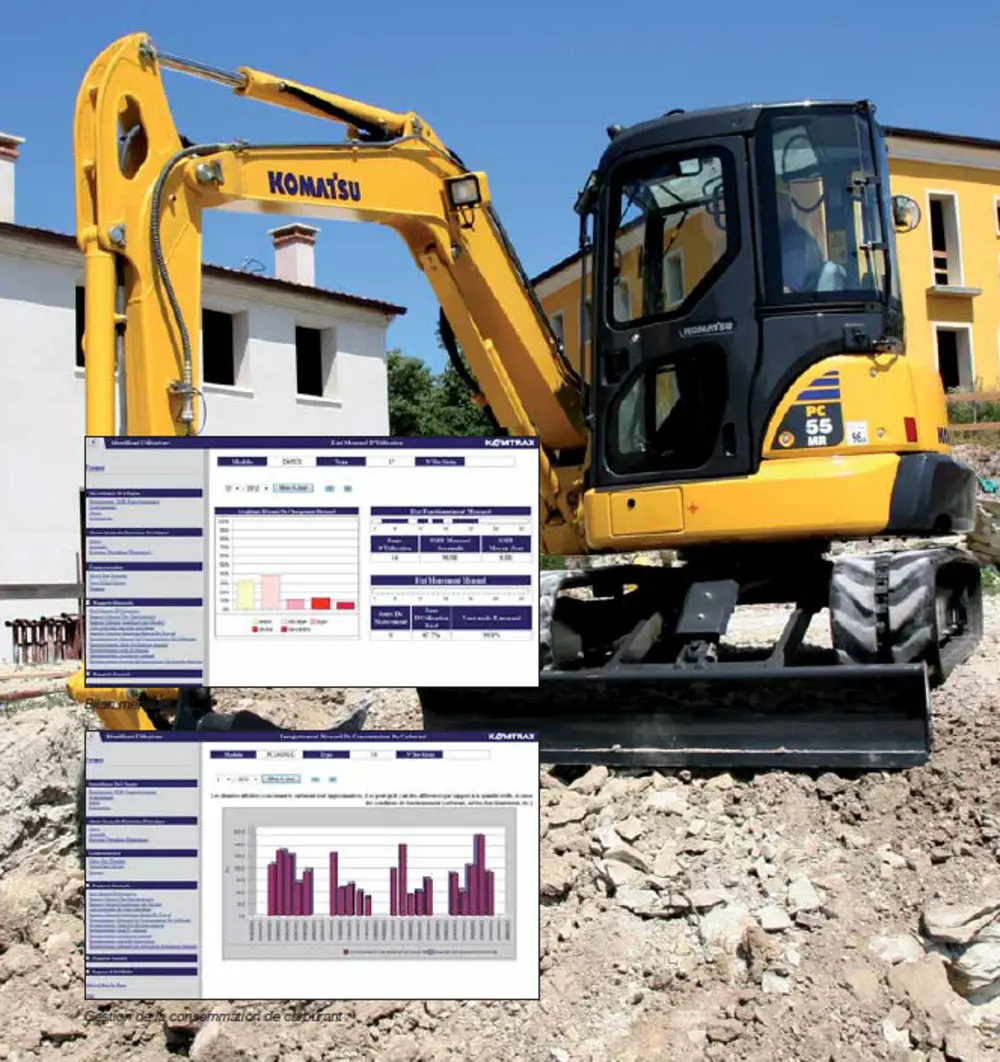
L’analyse des données est au cœur de l’actualité, car ces données permettent de faire des prévisions. Mais reste encore à réussir à les interpréter. Par exemple, une température d’huile en hausse indique un problème, c’est très parlant. La cause du problème peut être la qualité détériorée du lubrifiant, mais aussi à cause d’une trop chaude journée d’été, ou d’une journée de travail trop longue et trop dense, ou encore d’une tâche trop lourde, ou d’un problème avec le système de refroidissement ...
Tellement de facteurs peuvent entraîner un problème. Ces facteurs peuvent être analysés par informatique pour des prévisions plus précises. Le réglage et la programmation de ces algorithmes qui ‘captent’ les relations entre ces facteurs, sont un travail de spécialiste. Outre les données mesurées par les capteurs, ils utilisent aussi d’autres sources de données comme des tableaux d’ouvrages de référence, des données historiques et des informations externes comme la météo. L’objectif final? Regrouper toutes les informations dans un algorithme pour permettre une prévision précise sur l’état des machines.
Si ces algorithmes peuvent s’autogénérer, grâce au feed-back de décisions et d’analyses antérieures, vous obtenez à terme un système ultraperformant et autocorrecteur.
Une anecdote dans le secteur des grues permet de savoir où l’on se situe en matière d’intelligence artificielle. Pour les clients d’un fabricant de broyeurs pour machines dans l’industrie de la gestion forestière, il est important pour le uptime de remplacer les lames à temps.
Si l’on attend trop longtemps, la machine sera moins performante et les travaux risquent de prendre du retard suite à l’usure des dents. Si l’on attend encore plus longtemps, les lames risquent même de casser, avec toutes les conséquences que cela implique pour la sécurité des opérateurs et des pièces de la machine.
Il fallait donc trouver un système de détection capable de prédire l’usure des lames. La solution a finalement été trouvée avec l’installation d’un capteur sonore, basé sur la capacité d’un opérateur expérimenté à reconnaître le bruit émis par des lames usées. Des chercheurs ont réussi à détecter ce bruit et à le combiner à d’autres informations dans le cadre de cette application: température ambiante, niveau de charge, essences de bois, …
Un algorithme a pu être développé pour prédire avec exactitude le moment idéal de remplacement des lames. Le système est actuellement en phase de test, mais les résultats sont très prometteurs. Les capteurs parviennent même à détecter les prémices du problèmes avant les opérateurs.
Méthode de travail
La méthode exacte varie en fonction du fabricant de la machine. Les différences se situent surtout dans la communication entre la machine et le système de traitement des données, ainsi que dans l’affichage des résultats.
Communication entre la machine et l’utilisateur
La collecte de données de la machine se fait par le biais de capteurs – voir plus loin – qui envoient leurs informations à une unité de traitement centralisée. Cette unité compile l’ensemble des résultats et les envoie au fabricant ou à l’utilisateur. Cela se fait souvent par GPRS, donc le même principe que le trafic GSM. Des fabricants permettent aussi la communication par satellite. Ce qui est très pratique dans les régions reculées où l’on a besoin d’une infrastructure pour les réseaux mobiles. Le coût du transfert des données est calculé par abonnement. Les fabricants proposent pour la plupart des tarifs à l’année. La durée est en général au choix de l’utilisateur, la plupart du temps pour une période d’un an.
Rendu des résultats
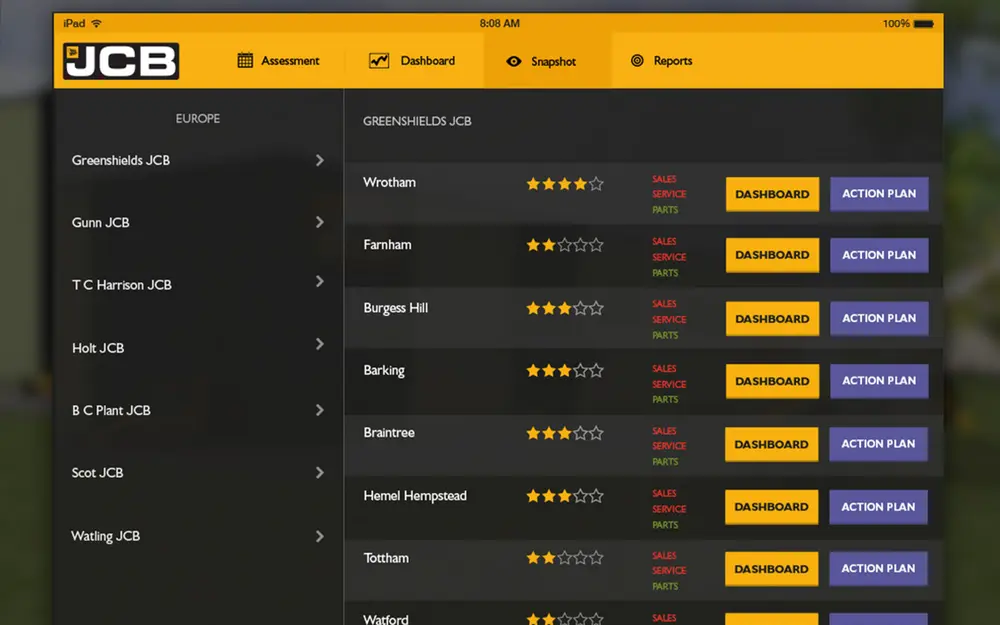
Le rendu des résultats est un facteur de choix important. Car collecter les données, c’est une chose, mais il faut ensuite que l’utilisateur puissent en comprendre les principales informations qu’il faut en retenir. Le programme du fabricant est important, mais aussi la visualisation ou l’interface aura un gros impact sur la facilité d’utilisation. Ainsi, certains fabricants préfèrent installer la machine eux-mêmes pour expliquer les éventuelles notifications d’erreur au propriétaire ou aux distributeurs afin de prévenir des problèmes. D’autres proposent de manière périodique (mois, semaine, trimestre, …) un aperçu de plusieurs éléments-clés des machines de leurs clients (nombre d’heures d’activité, temps de fonctionnement exact, etc.). Ainsi, vous disposez par machine des principaux indicateurs pour les comparer: consommation à l’heure, puissance du moteur, moyenne par rapport au parc de machines. Ces rapports permettent de mieux estimer le coût de projets futurs. L’accès aux données des machines se fait via GSM, tablette ou par ordinateur. En général, l’utilisateur doit s’enregistrer à l’aide d’un mot de passe et d’un nom d’utilisateur pour avoir accès à une plate-forme. La qualité de cette plate-forme est essentielle. Un rendu clair des chiffres, des tendances et la possibilité de régler des valeurs qui déclenchent une alarme, jouent clairement en faveur des programmes. Au fil des ans, les possibilités de la télématique ont énormément évolué, en qualité comme en quantité. Pour ceux qui hésitent encore quant à l’utilité de la télématique par rapport à son prix, voici un aperçu des possibilités, qui vont bien au-delà de la maintenance conditionnelle de votre parc de machines. La télématique contribue aussi à la sécurité et à l’optimisation de votre gestion d’entreprise.
Maintenance conditionnelle
Les facteurs pouvant être repris aujourd’hui dans un système de télématique pour le contrôle d’une machine sont très divers: alimentation moyenne et pics d’alimentation du moteur, puissance, tension, heures de fonctionnement, température du liquide de refroidissement, température du moteur, vitesse, température de l’huile, qualité de l’huile, pression de l’huile et consommation de carburant. Dans l’encadré – en page suivante – vous retrouverez les possibilités futures liées au suivi de ces données.
Sécurité
L’emplacement des machines peut être suivi avec précision grâce à la télématique, c’est d’ailleurs la première application qui a percé à grande échelle. Des alarmes peuvent être générées en cas de situations prédéfinies. Il est par exemple possible de faire fonctionner une machine dans un périmètre prédéfini, on parle alors de geofencing. Si la machine en sort, le propriétaire est notifié directement sur son téléphone, par courriel ou dans le portail web. Il est aussi possible de programmer des périodes pendant lesquelles la machine ne peut être actionnée. Si quelqu’un essaie, une alarme se déclenche et avertit le propriétaire. La télématique permet aussi de modifier les codes PIN à distance, une fonction surtout intéressante, lorsque le délai de location est passé et que la machine n’est pas ramenée de suite.

Optimisation
Les arrêts trop longs ou un déséquilibre entre les périodes stationnaires et les périodes de travail peuvent déclencher des alarmes. Les plus grandes entreprises au grand parc de machines peuvent ainsi contrôler et optimiser leurs machines. Une autre fonctionnalité intéressante consiste à suivre en temps réel la charge de la machine. L’opérateur est alors systématiquement averti, lorsque la charge est trop importante – ce qui est mauvais pour les pneus, la consommation et le moteur – ou trop faible – ce qui freine l’avancement des travaux. Mais vous pouvez aussi contrôler la consommation de carburant exactement au moment où le moteur développe telle ou telle puissance. Il peut être pratique de savoir si un utilisateur n’a pas tendance à consommer trop pour ensuite réagir en le formant de manière adéquate.
SUR QUELLES MACHINES?
L’installation de la télématique est aujourd’hui prévue de série sur la plupart des machines. Peu importe le type de machine: pelles hydrauliques, chargeuses sur pneus, tombereaux articulés, bouteurs, etc. Il est même possible d’équiper les anciennes machines d’une forme de télématique. Un fabricant propose même ce système pour pouvoir suivre des machines d’autres fabricants, pour répondre à la demande du terrain où les clients travaillent souvent avec des machines de marques différentes.