De friche industrielle à site de production de VE high-tech
Avec le Flamand Vic Daenen aux commandes
Nous sommes au berceau des modèles électriques Explorer et Capri de Ford. Plus précisément, au Ford Cologne Electric Vehicle Center, situé dans l'ancienne usine où Ford construit des voitures depuis 1930. Une partie de ce site a depuis été transformée en une installation de production ultramoderne capable d'assembler 250.000 voitures électriques par an. C'est le Flamand Vic Daenen qui nous fait visiter les lieux tout en nous fournissant des informations. Il fut le dernier directeur de l'usine Ford à Genk et il est aux commandes à Cologne depuis dix ans. Cet éloquent Limbourgeois était donc à la barre lorsque cette usine historique de Ford a dû être transformée en quelques mois à peine en un site de production de véhicules électriques high-tech.
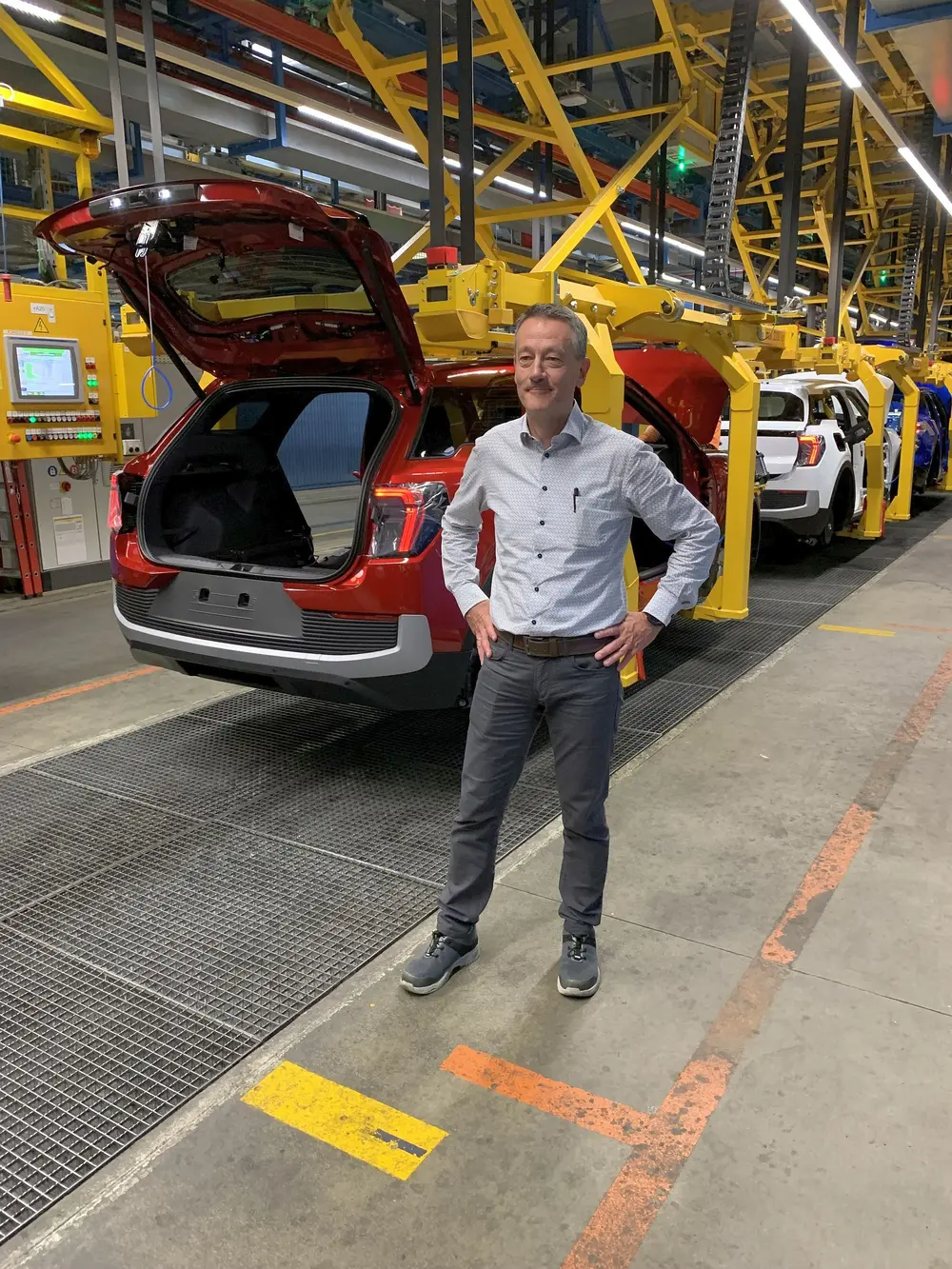
Le Ford Cologne Electric Vehicle Center représente le dernier chapitre de l'histoire d'un site Ford où l'on produisait depuis 1930 le modèle A, la Taunus, la Capri, la Granada et (jusqu'en juin 2023) la Fiesta, entre autres. C'est après l'arrêt de la production de la Fiesta - et dans la perspective de la production prochaine du Ford e-Explorer et du Ford e-Capri - que les usines Ford de Cologne ont dû subir une véritable métamorphose.
Une toute nouvelle ligne de production
La transformation de l'ancien assemblage ICE (modèles à moteur à combustion) en production BEV (modèles à batterie) dans les bâtiments existants de l'usine à l'abandon a nécessité un investissement de 2 milliards d'euros dans ce site de 125 hectares. Cela s'est traduit, entre autres, par une ligne de production entièrement nouvelle et efficacement approvisionnée, un assemblage de batteries, un outillage de pointe et (surtout) une automatisation encore plus poussée. Ford Cologne - désormais appelé Ford Cologne Electric Vehicle Center - est ainsi le premier site de production de véhicules électriques de Ford en Europe. Il a une capacité de production annuelle de 250.000 voitures électriques.
Alliances stratégiques
Ford peut désormais élargir sa gamme mondiale de modèles de VE - en plus de la Mustang Mach-E, de l'E-Transit et du F-150 Lightning - avec deux nouveaux venus construits à Cologne - et non des moindres - pour le marché européen: l'Explorer électrique, un SUV de taille moyenne, et un crossover sportif basé sur ce dernier, nommé d'après la légendaire Ford Capri des années 60 et 70.
Important à savoir: à l'instar de son alliance stratégique avec Volkswagen pour le développement de véhicules utilitaires efficaces en coût, Ford a conclu un partenariat avec VW pour la production de l'Explorer/Capri. Comme nous l'avons écrit précédemment, Ford a acquis la licence de la plateforme MEB de Volkswagen à partir du VW ID.4 pour l'Explorer et le Capri assemblés à Cologne.
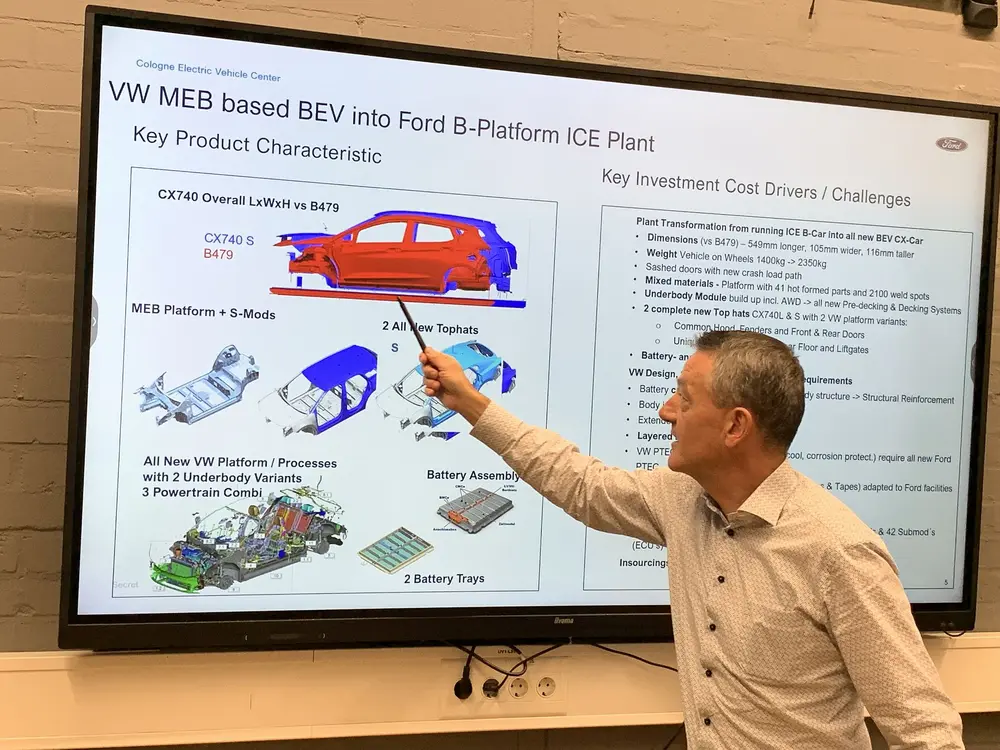
Ingénierie de production et communication numérique homme-machine
Cependant, les activités du Ford Cologne Electric Vehicle Center ne se limitent pas à la production de l'Explorer et du Capri. En effet, c'est à Cologne - qui, soit dit en passant, accueille le siège de Ford Europe depuis 1998 - que se trouve le centre Ford EV pour les développements numériques. C'est là qu'ont lieu la recherche et développement sur la communication numérique entre l'homme et la machine. Et il ne s'agit pas seulement d'une communication entre le conducteur et le véhicule. Mais aussi - et c'est important pour l'ingénierie de production - de la manière dont l'homme (le travailleur) peut être efficacement connecté aux machines (de production).
C'est à Cologne - qui, soit dit en passant, accueille le siège de Ford Europe depuis 1998 - que se trouve le centre Ford EV pour les développements numériques
Au Ford Cologne Electric Vehicle Center, on assiste à une forte implémentation de machines auto-apprenantes et de systèmes de transport autonomes. La gestion complète des données en temps réel est devenue un 'outil de travail' intégral pour rendre les différents processus de production encore plus efficaces. Pour l'assemblage de l'Explorer et du Capri électriques, l'ingénierie de production de Ford a installé de nouveaux robots cognitifs et collaboratifs et a conçu de nouvelles applications de réalité augmentée pour aider les travailleurs. En d'autres termes, l'efficacité du partage des données est renforcée par le partage structurel des expériences de production en temps réel.
Écran tactile géant
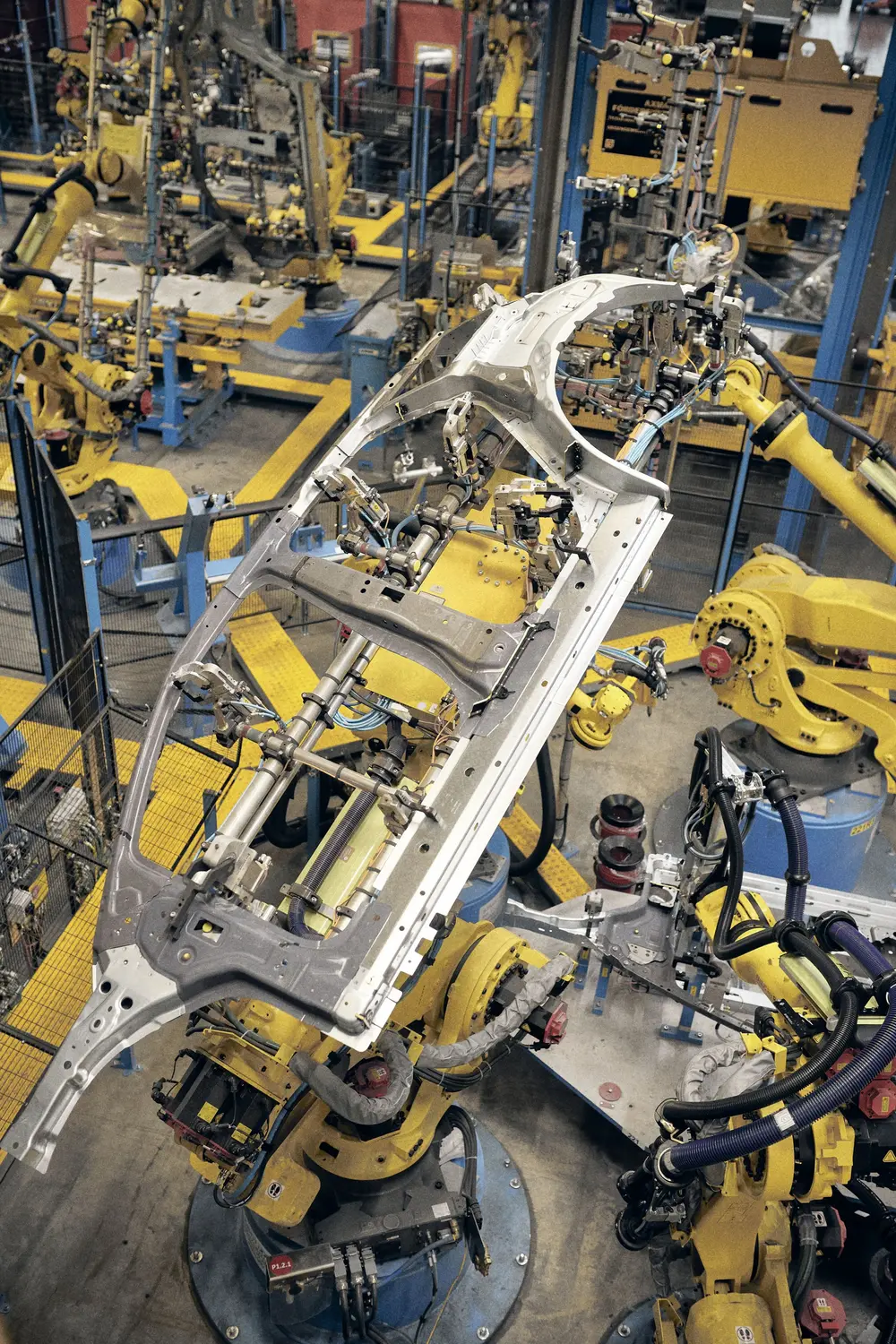
À cet égard, Vic Daenen montre sur un gigantesque écran tactile la rigueur avec laquelle l'ensemble du processus de production est contrôlé et coordonné dans le nouveau centre de contrôle. L'ensemble du processus d'assemblage est affiché en temps réel. Avec une vision claire des quantités de chaque pièce et de chaque écrou à chaque poste de travail. Avec des informations sur les outils, l'approvisionnement en matériaux et en pièces pour tous les postes de travail. En contrôlant également la sécurité du travail. Une partie de l'information provient donc des employés qui peuvent transmettre l'état de leur poste de travail à la chaîne de montage. Comme chaque étape du processus de production est ainsi visualisée numériquement - et peut être contrôlée - nous avons augmenté le niveau de qualité, explique Daenen.
Capacité de production actuelle: 630 voitures par jour
Lorsque la Ford Fiesta sortait de la chaîne de montage de Cologne, 4.500 personnes y travaillaient. Aujourd'hui, la production est assurée par 2.600 personnes. Réparties en deux équipes, elles peuvent construire 250.000 voitures par an. Ainsi, la capacité de production de Ford Cologne a chuté de 450.000 à 250.000 voitures par an.
Le système actuel à deux équipes permet de construire jusqu'à 630 voitures par jour, dont 200 Capri pour l'instant. Selon Daenen, il est possible d'augmenter la capacité de production quotidienne à 700 unités dans ce système à deux équipes. Et si ces 700 unités ne suffisent pas à répondre à la demande du marché, nous pouvons - a ajouté Daenen - augmenter la capacité de production à 1.250 voitures par jour sur la ligne d'assemblage actuelle. À condition de disposer d'une main-d'œuvre supplémentaire et de mettre en place un système à trois équipes.
Transformation de l'ICE en BEV dans une usine désaffectée
Pendant plus de 40 ans, la Fiesta a été fabriquée sur une double chaîne de montage à Cologne, en tant que modèle à moteur à combustion interne pour le segment B du marché. Il s'agissait d'un modèle 100% conçu par Ford. La simplification de l'assemblage et la réduction de l'intensité de la main-d'œuvre ont également été prises en compte lors du développement. La dernière Fiesta a quitté la chaîne de montage en juillet 2023. Pour construire l'Explorer et le Capri électriques, cette usine désaffectée a dû être transformée en peu de temps en une installation moderne de production de véhicules électriques.
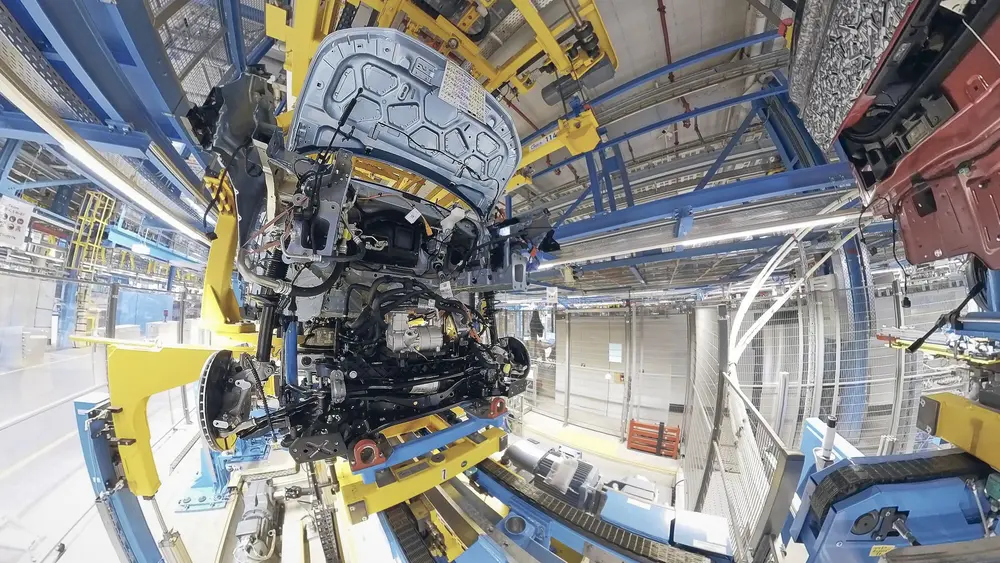
"Normalement, nous aurions pu construire nos premiers Explorers six mois plus tôt", explique Daenen. "Mais ce n'est qu'en juin dernier que nous avons pu lancer officiellement la production de l'Explorer, suivie quelques semaines plus tard par celle des premiers modèles Capri."
Daenen explique à quel point il est complexe de passer de la production de moteurs à combustion interne à celle de BEV dans une usine existante en friche. "Tout d'abord, la Fiesta était une voiture du segment B. L'Explorer et le Capri BEV que nous construisons aujourd'hui sont des voitures du segment C aux dimensions plus généreuses. En outre, nous sommes passés d'une double chaîne d'assemblage (Fiesta) à une chaîne d'assemblage unique pour l'Explorer et le Capri. Nous n'avions plus affaire à l'assemblage Fiesta simple et nécessitant moins de main-d'oeuvre, que nous avions développé nous-mêmes. En effet, l'Explorer et le Capri sont construits sur la plateforme MEB de VW, ce qui nous a confrontés à un assemblage plus difficile et à plus forte intensité de main-d'œuvre en raison de l'approche clairement centrée sur la plateforme de VW.
Un logiciel complexe et deux cultures
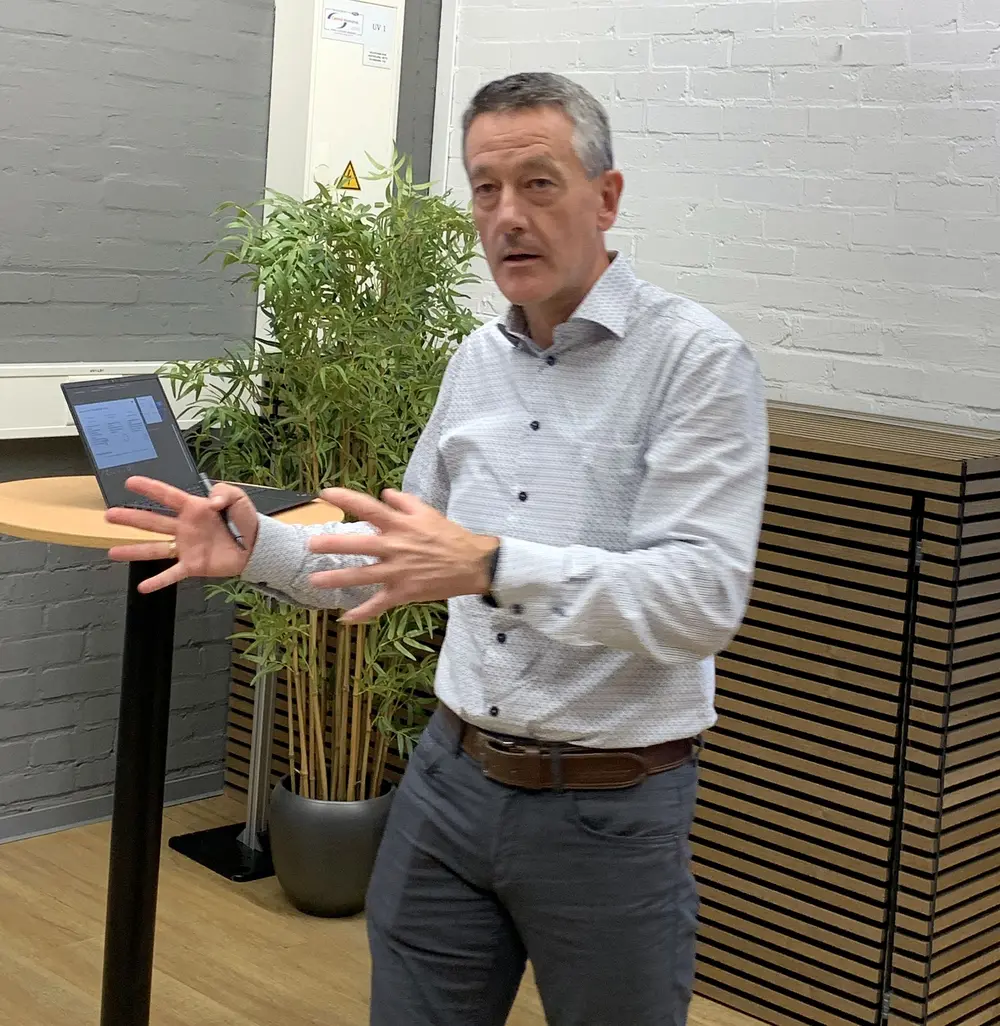
"Nous étions donc confrontés à deux cultures qui devaient fusionner", poursuit Daenen. "Chez Ford, nous avons une culture axée sur les coûts de production. À cela s'oppose la culture de plateforme de VW, qui vise à réaliser des économies d'échelle. Nous assemblons la Fiesta compacte ici depuis des décennies. Et ce, dans une Europe où les coûts élevés de la main-d'œuvre constituaient, pour ainsi dire, la pierre d'achoppement de la construction de voitures compactes abordables. Notre efficacité axée sur le coût du produit a prouvé le contraire".
"Par ailleurs, lors du lancement de la production de l'Explorer et du Capri, ainsi que de l'implémentation de la plateforme MEB de VW, nous avons été confrontés - outre à un assemblage plus compliqué (que celui de la Fiesta) et à forte intensité de main-d'œuvre - au logiciel beaucoup plus complexe utilisé chez Volkswagen", poursuit Danen. "Chez VW, il y a d'ailleurs 54 processeurs au sein de cette donnée de plateforme. Chez Ford, nous avons adopté une approche simplifiée, avec deux unités centrales principales et 42 sous-groupes. Les modifications logicielles nécessaires pour ces applications ont été compliquées, mais elles ont finalement été couronnées de succès.
Intelligence artificielle et nouveaux robots
Pour garantir la qualité de la production de l'Explorer et du Capri dans l'Electric Vehicle Center, on recourt à une intelligence artificielle avancée. En outre, des centaines de robots chorégraphiés (auto-apprenants) ont été installés. Au final, la production est donc soutenue par des machines auto-apprenantes et un total de plus de 600 nouveaux robots effectuant des tâches de soudage, de découpe, de dépoussiérage, de peinture et de fusion.
Pour la composition de la sous-structure (85 pièces par structure), Cologne utilise 126 robots de soudage, 143 robots de manutention, 10 robots de collage ou d'adhésion, 13 robots de soudage par points et 4 robots de mesure. La composition de cette sous-structure nécessite 1.938 soudures par points, 127 boulons, 35 mètres de colle ou de matériaux d'adhésion et 24 écrous à souder. Dans l'atelier de carrosserie, il y a 112 robots qui soudent, 62 robots de manutention, 20 robots de collage ou d'adhésion, 2 robots de soudage par points, 8 robots de mesure, 8 robots de soudage au laser et 10 robots de nettoyage...
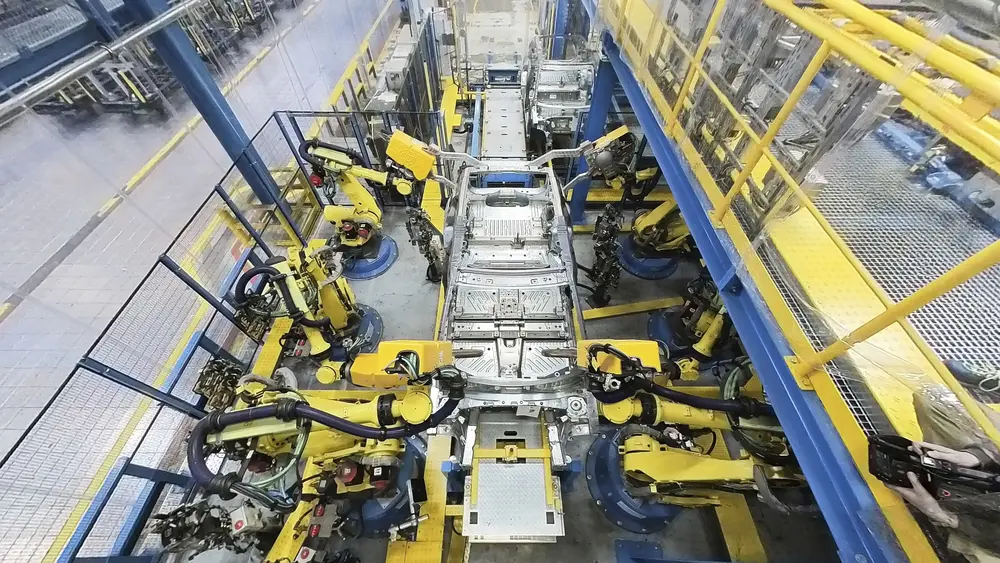
La Chine est la référence en matière de véhicules électriques
Tandis que Vic Daenen nous explique avec expertise les tenants et les aboutissants du site de production qu'il dirige depuis dix ans, une question revient sans cesse dans notre esprit: l'industrie automobile européenne souffre en ce moment en raison de la faiblesse des ventes de VE, les usines menacent de fermer... Dans ce climat économique, Ford investit de manière extraordinaire dans une nouvelle ligne de production pour lancer deux nouveaux VE sur un marché difficile. Deux SUV de taille moyenne qui appartiennent également à un segment de marché dans lequel - même dans la section BEV - l'offre est déjà énorme. Pourquoi Ford n'a-t-il pas choisi de construire ici à Cologne des modèles plus compacts (selon les normes de la Fiesta) et moins chers (que l'Explorer et le Capri)?
Daenen: "Avec des voitures électriques construites en Europe et coûtant moins de 35.000 euros, il est impossible de concurrencer les constructeurs chinois"
Daenen: "Parce qu'avec des voitures électriques construites en Europe et coûtant moins de 35.000 euros, il est impossible de concurrencer les constructeurs chinois. Pour les voitures un peu plus chères et plus spacieuses comme l'Explorer et le Capri, c'est un peu plus facile.... (silence) ou plutôt moins difficile. Avec des modèles mieux positionnés sur le marché en Europe comme l'Explorer et le Capri et 'aidés' par notre assemblage axé sur les coûts de production, je pense que nous pouvons rattraper un peu de notre retard sur les constructeurs chinois dans le segment de marché Explorer/Capri. Car, ne nous voilons pas la face, la Chine est la référence en matière de VE."
"Elle dispose des matières premières, contrôle la quasi-totalité de la chaîne d'approvisionnement des VE, bénéficie du soutien du gouvernement et n'est pas (ou beaucoup moins que l'Europe) entravée par les réglementations en matière de CO2. En outre, les Chinois travaillent sur l'électrification des voitures depuis plus longtemps que nous. Cela leur a donné une avance considérable en matière d'ingénierie électrique. Il suffit de regarder leur technologie des batteries, qui leur a donné une avance sensible sur les constructeurs européens. Et en ce qui concerne cette avance de la Chine, je ne mentionne même pas le nombre moyen d'heures de travail beaucoup plus élevé et les coûts salariaux inférieurs des travailleurs chinois. Ou encore les coûts énergétiques en Chine, qui sont bien inférieurs à ceux de l'Europe", conclut Daenen.