extension de la capacité dans une usine en activité
Hyline fournit à FrieslandCampina une nouvelle tuyauterie utilitaire
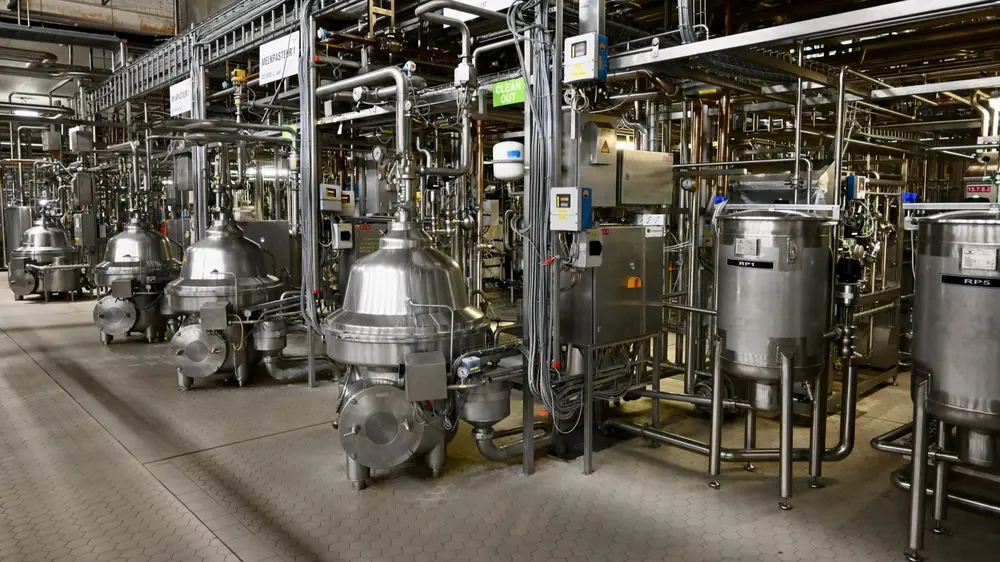
Pour doubler la quantité de lait que FrieslandCampina peut recevoir quotidiennement sur le site d'Aalter, les lignes de pasteurisation existantes ont été modernisées étape par étape. Pour ce faire, Hyline a été engagée pour renouveler une partie de la tuyauterie utilitaire. Une tâche complexe, parce que la production ne s'est jamais complètement arrêtée pendant les travaux. Cependant, grâce à une bonne communication entre toutes les parties concernées, le projet a pu être mené à bien.
Modernisation des installations existantes
Aujourd'hui, sur le site d'Aalter, FrieslandCampina produit du lait et des produits laitiers sous un certain nombre de marques de consommation bien connues, telles que Campina, Joyvalle, Cécémel et Fristi. Par ailleurs, elle fournit également des ingrédients aux clients industriels et au marché de la restauration.
Lignes de Pasteurisation
"Après la réception du lait, la première étape de notre processus de production est la pasteurisation. Pour ce faire, nous disposons ici de cinq lignes parallèles. Nous voulions doubler leur capacité, avec une ligne entièrement nouvelle et un renouvellement des équipements mécaniques et électriques sur quatre lignes existantes. À cette fin, nous avons investi notamment dans de nouvelles machines à plaques, des cuves à crème et l'automatisation correspondante pour contrôler et surveiller le tout", explique Didier Hooreweghe, chef de projet.
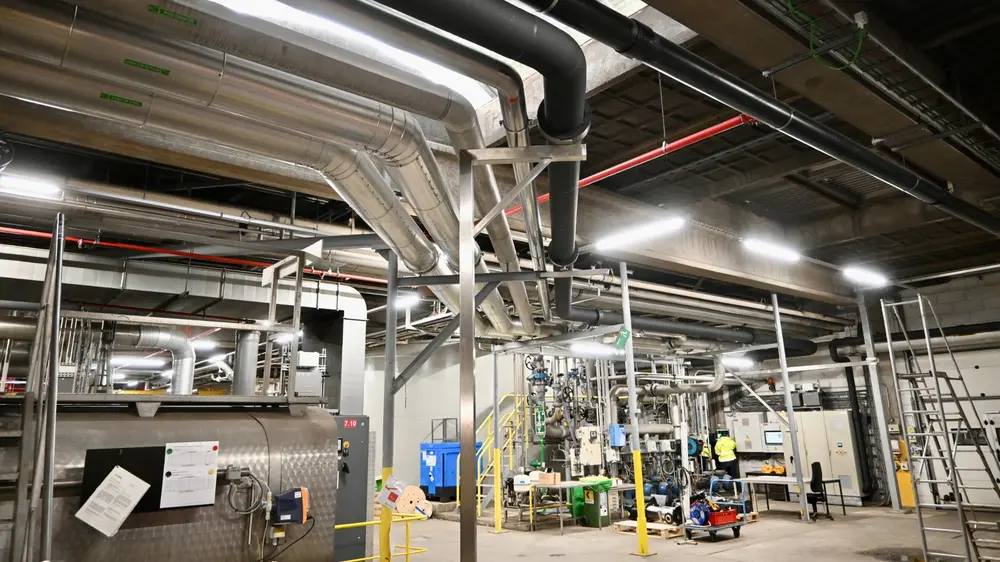
Nouvelles canalisations
Hyline a été désignée pour fournir de nouvelles canalisations utilitaires et renouveler la tuyauterie existante dans le rack à tuyaux. Tous les utilitaires – de la vapeur à l'air comprimé, en passant par l'eau glacée, l'eau de la tour de refroidissement et l'eau de traitement – passent par ces boucles. Concrètement, ces spécialistes de la tuyauterie étaient chargés de concevoir l'acheminement et d'effectuer les travaux de soudage, conformément au cahier des charges prédéfini. Par ailleurs, ils se sont également chargés de l'isolation de certaines conduites afin de conserver la chaleur ou le froid dans les canalisations.
Les travaux réalisés par Hyline ont débuté en octobre 2022, l'objectif étant de pouvoir fonctionner avec une usine entièrement modernisée et à pleine capacité dès l'été 2023.
"Impact sur la facilité de travail et la sécurité"
Fiable et flexible
"Hyline nous était déjà familière. En effet, ils interviennent régulièrement pour des travaux de maintenance ici. Ils ont donc déjà prouvé qu'ils étaient un partenaire fiable et flexible. En effet, ils peuvent déployer suffisamment de collaborateurs compétents pour répondre à la qualité requise et, en outre, ils peuvent respecter les délais fixés", explique Hooreweghe pour justifier le choix de cet entrepreneur.
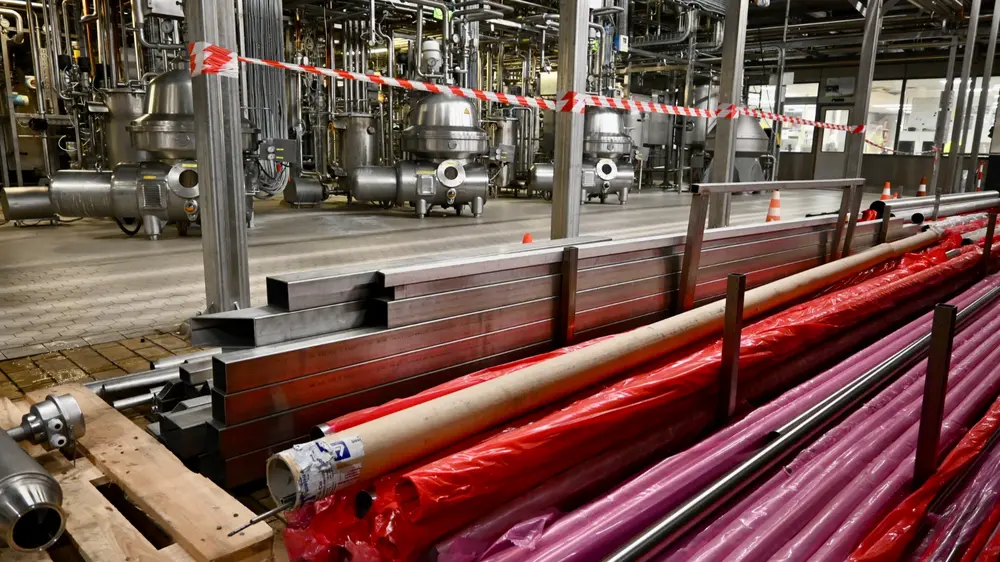
Cette qualité est attestée par les nombreux tests effectués par Hyline elle-même, FrieslandCampina ou un organisme de contrôle externe. "Il s'agit de contrôles visuels, de radiographies ou de tests de pression. La responsabilité de ces exigences de qualité, tout comme le respect de nos réglementations et des règles de sécurité (alimentaire), leur incombe. Nous avons constaté un suivi correct et méticuleux, ce qui a permis de respecter le calendrier et de confirmer notre confiance en eux", déclare le chef de projet.
les Défis
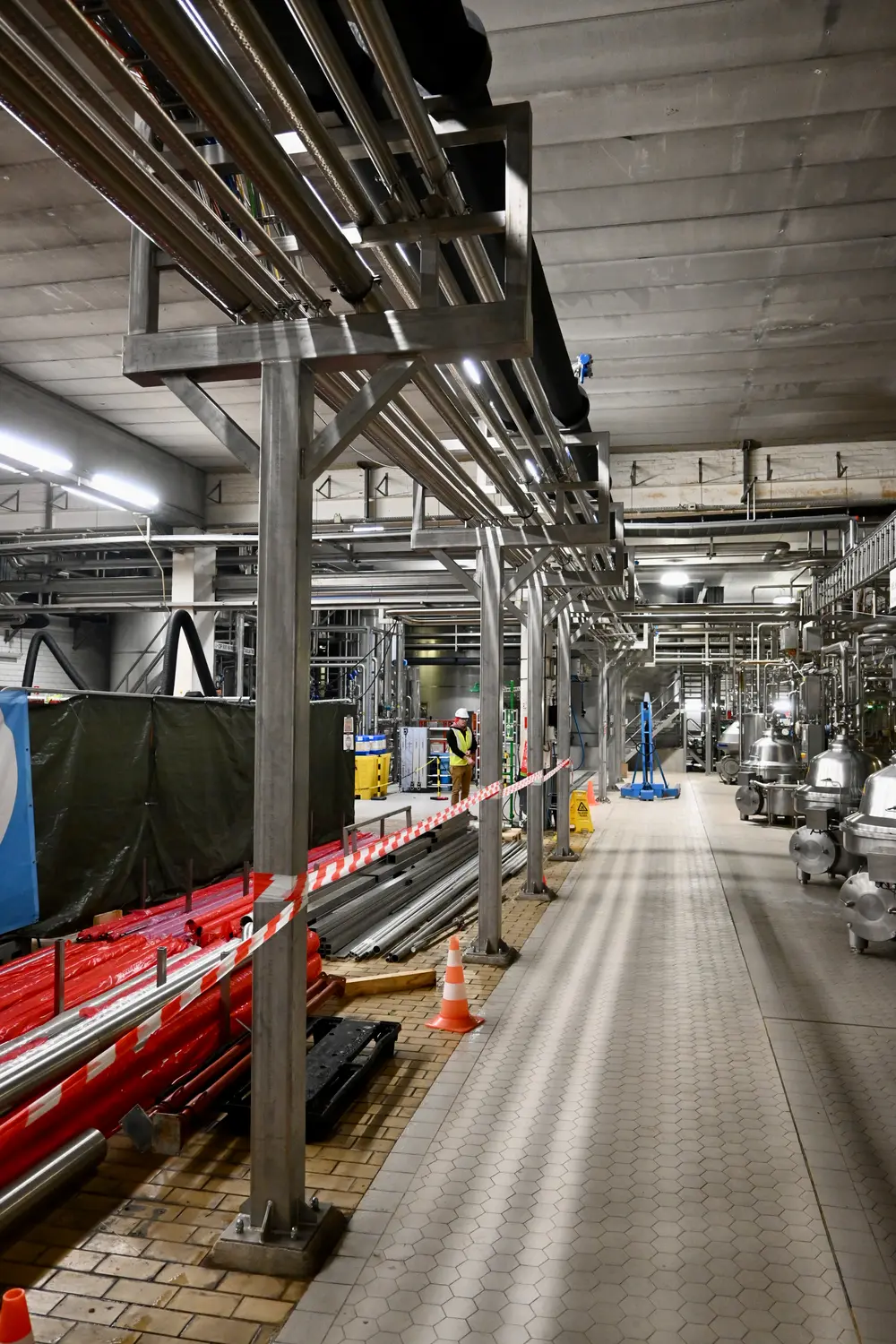
Le défi majeur de ce projet était qu'il s'agissait d'une opération dite "brown field", avec des collaborateurs de différentes entreprises partageant le même atelier en même temps, et avec une production qui n'était jamais complètement arrêtée. En d'autres termes, il s'agissait de travailler entre des conduites chaudes et des installations sous tension. Cette situation a naturellement eu des répercussions sur la facilité de travail et la sécurité, et a donc nécessité des efforts dans ces domaines.
Pas à pas
"Après l'installation de tous les nouveaux raccords, nous avons procédé à une conversion pasteurisateur par pasteurisateur. Le support du rack de conduites existante a également dû être remplacé pilier par pilier par des supports plus robustes. Alors que les installations sont restées en service", précise Hooreweghe pour décrire la complexité de l'opération.
"À cette fin, en concertation avec toutes les parties concernées, nous avons élaboré une procédure pour le premier support. Après sa mise en œuvre réussie, nous avons pu répéter ce plan d'action pour les supports suivants. La communication a été la clé du succès. En effet, nous avons prévu des réunions matinales quotidiennes et des moments de concertation hebdomadaires entre les responsables, qui ont à leur tour informé leur base", ajoute le chef de projet.